Adding a section on costs and budgeting
Woodworking dust collection systems are an important safety measure for a woodshop, helping to keep fine dust particles off surfaces, out of the air and ultimately away from the lungs of those working in the space. Dust collection systems are available in a range of sizes and capabilities, designed to suit a variety of different budgets and needs.
When shopping for dust collection systems, it is important to consider the cost of the system versus its power and capacity. Many cheaper systems can effectively collect larger particles, but are not as powerful at collecting finer dusts that need more specialized filtration. More expensive units might last longer or include more powerful motors. When trying to stay within a budget it is important to carefully consider both current and future requirements when choosing your system as compromises made now may end up costing you more down the road if upgrading is needed.
The initial cost of purchasing a dust collection system is only part of the equation – running costs such as energy use and filter replacements should also be taken into account when budgeting for these systems. However, long term savings can be achieved by investing indust collection systems that are properly sized for the job on hand so that you don’t have excessive energy wastage due to oversized units running more than needed. Installing these systems ultimately reduces cleaning time and labor costs; plus there may be various discounts or tax breaks depending on where you live – making them even more cost effective in some cases.
Adding a section on environmental considerations
The use of woodworking dust collection systems is not just a way to keep your workspace clean, but also beneficial in regards to environmental considerations. To ensure the best results, woodworkers should consider using the most environmentally-friendly systems available. In addition to improve air quality, these systems also help reduce air pollution by collecting particulate matter from the surrounding environment.
Dust collection systems are effective in trapping particles and other pollutants that are released during sanding, grinding, sawing and other similar processes. This helps decrease air pollution as well as indoor air quality since the dust and particulates emitted during these activities can contribute to pollen allergies, respiratory illnesses and asthma attacks. Additionally, some studies have shown that increased dust count pollution can contribute to serious lung illnesses such as interstitial lung disease that can be prolonged over long periods of time.
To ensure a safe working environment and protect human health as much as possible, it’s important to invest in a highly efficient woodworker dust collection system with sufficient suction power. When compared with traditional methods of dust containment such as vacuuming or manual sweeping, these systems have been found to be far more cost-effective at capturing large quantities of dust particles without frequent need for maintenance or replacement parts.
Adding a section on “troubleshooting”
Troubleshooting: Dust collection systems, while designed to facilitate the efficient and safe removal of wood particles from a shop floor or other working space, can suffer from problems. Common problems include fan clogs, impeller issues, improper ducting setup, leaks in fittings and poor fitment of aspiration points. Other potential complications could be electrical overheating or incorrect connections leading to stoppages in production. A solution to many of these issues is regular maintenance and servicing. It may also be necessary to replace filters and hoses which have become clogged with fine particulate matter over time.
Smart dust collection systems: The recent emergence of smart dust collection technology adds a new layer of sophistication to traditional dust collection systems for woodworking applications. Smart dust collection systems are specifically designed to integrate with other machines such as CNC routers, edge banders and saws. These systems have the ability to monitor volumes produced and needs for changeover times throughout a production process, allowing for optimal implementation across multiple processes . Such linkage can improve efficiency and reduce unnecessary stops when dealing with floating particles caused by heavy machinery operation. In addition, automated settings allow for greater consistency regarding airflow rates which is essential for maintaining safety levels in industrial environments as well as optimising filter sizes for large scale operations.
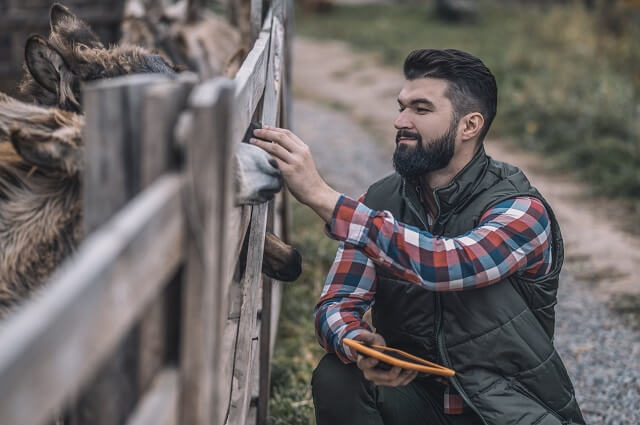
Hi everyone! I’m a woodworker and blogger, and this is my woodworking blog. In my blog, I share tips and tricks for woodworkers of all skill levels, as well as project ideas that you can try yourself.