Woodworking is a craft that requires precision, skill, and attention to detail. Every piece created has a unique beauty and character that adds value to both the artisan and the buyer. However, one aspect of woodworking that often goes unnoticed is CMF, which stands for Color, Material, and Finish. In this article, we will delve into the world of CMF in regard to woodworking and explore its significance in creating stunning pieces of art.
CMF refers to the deliberate choices made by woodworkers in selecting the color, material, and finish of their creations. These choices play an important role in determining the overall look and feel of a piece. Whether it’s a vibrant hue on a freshly lacquered tabletop or the smoothness of a well-polished chair leg, CMF adds depth and dimension to woodworking projects.
In this article, we will take an in-depth look at CMF in woodworking. We will begin by defining what CMF means in this specific context and explain its significance. We will then explore how CMF has evolved over time from traditional practices to modern-day techniques.
Additionally, we will examine the importance of color in CMF and how woodworkers utilize it to enhance aesthetics. The role of texture and finish in CMF will also be explored – understanding how surface characteristics can transform a plain slab of wood into a visually appealing piece of furniture.
By thoroughly examining these different aspects of CMF, readers will gain insight into the thought process behind creating wooden masterpieces. Through this article, woodworkers new and old can expand their knowledge base, refine their techniques, troubleshoot common challenges they may face when working with CMF, while also looking ahead towards future innovations and trends within this field.
What is CMF
CMF, in regard to woodworking, stands for Color, Material, and Finish. It is a term used to describe the combination of these three elements in the design and creation of wooden objects. This section will provide a definition and explanation of CMF, highlighting its importance and role in woodworking.
Color refers to the visual appearance of the wood and how it is enhanced or altered through the use of pigments or dyes. Woodworkers carefully select colors that complement the overall design and aesthetic they are trying to achieve. Different woods also naturally possess varying colors, such as the rich reddish tones of mahogany or the light blond hues of maple. By incorporating color into their creations, woodworkers can add depth, contrast, or even create unique patterns.
Material refers to the type of wood being used in a woodworking project. Different types of wood have distinct characteristics such as grain pattern, hardness, durability, and texture. Woodworkers choose materials based on their intended end-use and desired visual effect. For example, a piece of furniture requiring strength may be made from oak while a fine art sculpture may call for a more delicate wood like cherry.
Finish refers to surface treatments applied to protect and enhance the natural beauty of wood. It can include processes such as sanding, staining, varnishing, polishing or applying specialty coatings. Finishes allow woodworkers to manipulate the appearance and feel of the wood while providing protection against wear and tear over time.
By focusing on CMF in woodworking projects, craftsmen are able to create pieces that not only showcase their technical skills but also display an attention to detail and aesthetics. The combination of color choices with specific materials and finishes allows for endless possibilities in creating unique wooden objects that evoke different emotions or suit specific spaces.
Overall, understanding CMF is essential for any woodworker who wants to produce high-quality pieces that are visually appealing and durable. By carefully considering color choices in combination with suitable materials and finishes, woodworkers are able to achieve their desired results and bring their creative visions to life.
CMF Element | Role in Woodworking |
---|---|
Color | Enhances visual appearance, adds depth, contrast, or creates unique patterns |
Material | Determines the characteristics of the wood such as grain pattern, hardness, durability, and texture |
Finish | Surface treatments that protect and enhance the natural beauty of wood |
The Evolution of CMF in Woodworking
Woodworking has a long history that dates back to ancient civilizations, and over time, the techniques and practices used in this craft have evolved significantly. CMF, which stands for color, texture, and finish, plays a crucial role in woodworking as it enhances the aesthetics of different wood projects. In this section, we will explore the evolution of CMF in woodworking, tracing its journey from traditional practices to modern-day techniques.
In the past, woodworkers relied on natural materials and methods to achieve desired CMF effects. They used various organic substances such as dyes made from plants or animals to add color to their projects. Texture was influenced by the natural grain pattern of the wood itself or by carving intricate designs onto the surface. Finishes were often applied using oils or waxes derived from plants.
However, with advancements in technology and the availability of new materials, modern woodworkers now have a wide range of options when it comes to achieving CMF effects. Synthetic dyes and pigments offer a broader color palette and greater colorfastness compared to natural dyes. Different types of wood stains allow woodworkers to create varying shades and tones.
Surface textures can be altered through sanding techniques or by adding overlays such as veneers or laminates. Finishes have also evolved with the introduction of polyurethane coatings that provide durability and protection.
As woodworking continues to evolve, so does CMF. Woodworkers are constantly pushing boundaries with innovative techniques and materials. Laser engraving machines allow for precise detailing on wooden surfaces, creating unique textures and patterns. Epoxy resin is becoming popular for creating stunning finishes with vibrant colors and a glossy appearance. The use of digital technologies like computer-aided design (CAD) software has also opened up new possibilities for experimenting with CMF in woodworking.
Overall, the evolution of CMF in woodworking showcases the continuous exploration and experimentation in the field. From traditional practices that relied on natural materials to the use of modern-day techniques and materials, woodworkers have embraced innovation while still appreciating the beauty and craftsmanship of woodworking. This evolution has not only expanded the possibilities for creating visually appealing wood projects but also ensures that woodworking remains a dynamic and exciting craft in the present day.
Traditional CMF Techniques | Modern CMF Techniques |
---|---|
Natural dyes from plants or animals | Synthetic dyes and pigments with greater colorfastness |
Oils or waxes derived from plants as finishes | Polyurethane coatings for durability and protection |
Natural grain pattern or carving for texture | Sanding techniques or veneers/laminates for surface textures |
Importance of Color in CMF
Color is a crucial aspect of CMF (Color, Material, Finish) in woodworking as it plays a significant role in enhancing aesthetics. Woodworkers understand the importance of color selection and its impact on the overall appearance of their creations. The right choice of colors can transform a simple piece of wood into a visually stunning masterpiece.
Woodworkers utilize color in CMF to create various effects and convey different moods. Warm colors like red, orange, and yellow are often used to evoke feelings of energy and excitement. Cool colors such as blue, green, and purple are commonly employed to create a sense of calmness and tranquility. By strategically incorporating colors into their designs, woodworkers can evoke specific emotions in the viewers.
In addition to setting the mood, color can also be used to highlight certain features or elements within a woodworking project. For example, contrasting colors can draw attention to intricate details or bring focus to specific areas of a piece. Woodworkers often use this technique to showcase unique joinery, carvings, or other design elements that deserve special recognition.
Furthermore, color is essential for achieving harmony and balance in woodworking projects. Woodworkers carefully consider color schemes that complement each other and the surrounding environment. They may employ techniques like color mixing or layering different shades to achieve depth and dimension in their work. Through skillful use of color, woodworkers are able to create visually captivating pieces that leave a lasting impression.
Overall, understanding the importance of color in CMF is crucial for woodworkers looking to enhance the aesthetics of their creations. By selecting the right colors, highlighting key features, and achieving harmony within their designs, woodworkers can transform ordinary pieces into extraordinary works of art.
Texture and Finish in CMF
Texture and finish play a crucial role in the field of CMF (Color, Material, and Finish) in woodworking. Woodworkers understand that the overall appearance and feel of a finished piece depend not only on the color but also on the texture and finish of the wood surface. This section will explore the significance of texture and finish in CMF, discussing how they contribute to enhancing aesthetics in woodworking.
Understanding Texture in CMF
Texture refers to the tactile quality or surface characteristics of wood. It adds depth and personality to a piece, creating visual interest and inviting touch. Woodworkers achieve various textures through techniques such as sanding, distressing, brushing, carving, or applying different types of treatments. Each texture creates a unique visual effect that can transform a plain piece of wood into a work of art.
The Role of Finish in CMF
The finish is what protects the wood surface while also enhancing its natural beauty. It provides durability, resistance to moisture, dirt, and scratches while adding depth and richness to the color. Finishes can be classified into two main categories: penetrating finishes that soak into the wood pores (such as oils and stains) or film-forming finishes that create a protective layer on top (such as polyurethane or lacquer).
Woodworkers select finishes based on their desired aesthetic outcome, as different finishes can significantly alter the appearance of wood. A glossy finish will provide shine and reflectivity, highlighting intricate details. In contrast, a matte finish offers a more natural look with low reflection for those seeking a rustic or vintage appeal.
Combining Texture and Finish
Woodworkers often combine different textures with specific finishes to achieve desired effects in CMF projects. For example, rougher textures like distressing or wire brushing may pair well with matte finishes to create an aged or weathered appearance. On the other hand, smoother textures, such as a glass-like finish achieved through polishing or buffing, can enhance the natural beauty of wood and create a more modern or contemporary look.
Texture and finish in CMF are essential elements that woodworkers consider when designing and creating woodworking projects. By understanding how they work together, craftspeople can transform pieces of wood into visually stunning works of art that not only look good but also feel good to the touch.
Materials Used in CMF
The materials used in CMF (Color, Material, and Finish) in woodworking play a crucial role in achieving desired aesthetics and enhancing the overall appearance of the final product. From natural wood to specialty coatings, the choice of materials can greatly impact the CMF outcome.
One of the primary materials used in CMF is natural wood. Wood comes in a wide variety of species, each with its unique characteristics such as grain pattern, color, and texture. Woodworkers often select specific types of wood based on their desired CMF results. For example, maple may be chosen for its light tone and fine grain pattern, while oak may be preferred for its strong and prominent grain.
In addition to natural wood, specialty coatings are also commonly used in CMF applications. Specialty coatings provide an opportunity to enhance or alter the color or finish while adding protection to the wood surface. These coatings can include stains, dyes, paints, varnishes, lacquers, and oils. Each type of coating offers different properties and effects on wood surfaces. For instance, a stain can add depth and highlight the natural beauty of wood grains while preserving its texture.
Woodworkers carefully select these materials based on their understanding of how they will interact with one another during the CMF process. They consider factors such as compatibility between different materials and their impact on adhesion or durability. Additionally, they take into account environmental considerations like sustainability and health concerns when choosing materials for CMF practices.
CMF Techniques
When it comes to the field of woodworking, achieving the desired CMF (Color, Material, and Finish) effects requires a combination of skill, knowledge, and the use of specific tools and techniques. Woodworkers meticulously select and employ various methods to achieve their desired outcomes. In this section, we will explore some common CMF techniques used in woodworking, along with the tools that are often employed.
One widely used technique in CMF woodworking is staining. Stain is applied to wood surfaces to alter or enhance its color and create depth. Woodworkers can choose from a range of both oil-based and water-based stains. These stains come in a variety of hues, allowing for endless possibilities in achieving the desired color effect on different types of wood.
Another technique frequently used in CMF woodworking is distressing or antiquing. This method involves deliberately creating imperfections on the surface of the wood to give it an aged or weathered appearance. Common tools used for distressing include hammers, chains, chisels, wire brushes, and sandpaper. By carefully using these tools to dent, scrape, or sand away certain areas of the wood’s surface, woodworkers can create unique textures and patterns that add character and charm to their projects.
Additionally, woodworkers often use various application methods when working with specialty coatings such as lacquers or varnishes. Spraying is one popular technique that allows for an even distribution of coating materials onto the wood surface. This method usually requires specialized spray guns or airbrushes for optimal results.
Brushing is another commonly employed method where woodworkers use high-quality brushes to apply coatings by hand. This technique gives artisans greater control over coverage and allows them to create unique brush strokes for artistic effects.
In summary, achieving desirable CMF effects in woodworking involves employing a range of techniques and utilizing specific tools designed for each method. Woodworkers use staining to alter or enhance the color of wood, distressing to create texture and an aged appearance, and apply specialty coatings using application methods such as spraying or brushing. These techniques, combined with skill and creativity, result in visually stunning woodwork projects that showcase the beauty of color, materials, and finishes.
Common Applications of CMF in Woodworking
One of the most common applications of CMF in woodworking is in the creation of furniture. Woodworkers carefully consider color, texture, and finish when building furniture pieces to enhance their overall aesthetics. The use of different materials and techniques allows for endless possibilities in designing unique and visually appealing furniture.
In furniture making, woodworkers often utilize a variety of materials to achieve the desired CMF effects. Natural wood is a popular choice due to its inherent beauty and versatility. Different types of wood have distinct colors, grains, and textures that can be enhanced through finishing techniques such as sanding, staining, and varnishing.
Cabinetry is another area where CMF plays a vital role in woodworking. Cabinets not only serve functional purposes but also contribute to the overall design and ambiance of a space. Woodworkers carefully consider color schemes, texture patterns, and finishes to create cabinets that are visually cohesive with their surroundings. They may incorporate specialized coatings or overlays to achieve specific effects like high gloss or distressed finishes.
Beyond furniture and cabinetry, CMF is utilized in various other aspects of woodworking. Trim work, moldings, decorative panels, flooring, and even structural elements can all benefit from the careful consideration of color, texture, and finish. Woodworkers aim to create harmonious environments by incorporating CMF principles into every aspect of their projects.
In summary, the common applications of CMF in woodworking extend beyond just furniture and cabinetry. It encompasses a wide range of woodworking projects where careful consideration is given towards achieving the desired color palette, texture patterns, and finishes. By utilizing different materials and techniques, woodworkers are able to create visually stunning pieces that enhance both functionality and aesthetics in any space they are used in.
Troubleshooting CMF Challenges
When it comes to CMF in woodworking, there are often challenges that woodworkers face during the process. Understanding these challenges and having troubleshooting techniques can help ensure success in achieving the desired results. Here are some common CMF issues and tips for resolving them:
Inconsistent color
One of the most common challenges in CMF is achieving consistent color across a project. Woodworkers may face issues such as uneven stain application, color blotches, or variations in wood tones. To tackle this issue, it is important to prepare the wood adequately before applying any finishes.
This includes properly sanding the surface to create an even canvas for staining or coating. Additionally, using a pre-stain conditioner can help ensure an even absorption of color. It is also crucial to carefully follow manufacturer’s instructions when applying stains or dyes, and to test them on scrap pieces beforehand.
Poor adhesion of coatings
Another challenge in CMF can be poor adhesion of coatings such as paint, varnish, or lacquer. This can lead to bubbling, cracking, or peeling over time. To address this issue, proper surface preparation is key.
Woodworkers should ensure that the surface is clean and free from dust, grease, or any other contaminants before applying any coatings. Using a high-quality primer can also improve adhesion by creating a strong bond between the wood and the finish. Applying multiple thin coats rather than one thick coat can also help enhance adhesion and reduce the risk of peeling.
Achieving desired sheen
Woodworkers often strive to achieve a specific level of sheen when it comes to CMF projects. However, they may encounter difficulties in obtaining the desired result due to factors such as improper sanding techniques or inconsistent application of finishes.
To overcome this challenge, it is crucial to carefully sand the wood, paying attention to the direction of the grain and ensuring a smooth surface. Applying finishes with even strokes and following manufacturer’s recommendations for drying time can also aid in achieving the desired sheen.
By understanding these common CMF issues and implementing the corresponding tips and tricks, woodworkers can troubleshoot challenges they may encounter during the process. Whether it is addressing inconsistent color, improving adhesion of coatings, or achieving the desired sheen, these troubleshooting techniques are valuable tools for success in CMF woodworking projects.
The Future of CMF in Woodworking
In conclusion, the future of CMF in woodworking holds exciting possibilities as innovations and trends continue to emerge. As technology advances, woodworkers are finding new ways to incorporate CMF into their projects, pushing the boundaries of creativity and design.
One key innovation to watch out for is the use of digital tools and software in CMF. With computer-aided design (CAD) programs becoming more sophisticated, woodworkers are able to experiment with different color schemes, textures, and finishes before committing to a final product. This not only saves time and resources but also allows for greater precision and customization in CMF.
Another trend on the horizon is the integration of sustainable practices in CMF. As environmental awareness grows, woodworkers are seeking alternative materials that are eco-friendly without compromising on quality or aesthetics. From recycled wood to non-toxic coatings, there is a growing demand for CMF techniques that prioritize sustainability.
Furthermore, the future of CMF may see an increased collaboration between different industries. Woodworking has traditionally been viewed as a separate craft from fields such as interior design or architecture. However, as more professionals recognize the potential of combining disciplines, we can expect to see unique collaborations that push the boundaries of traditional woodworking and redefine what it means to incorporate CMF into various spaces.
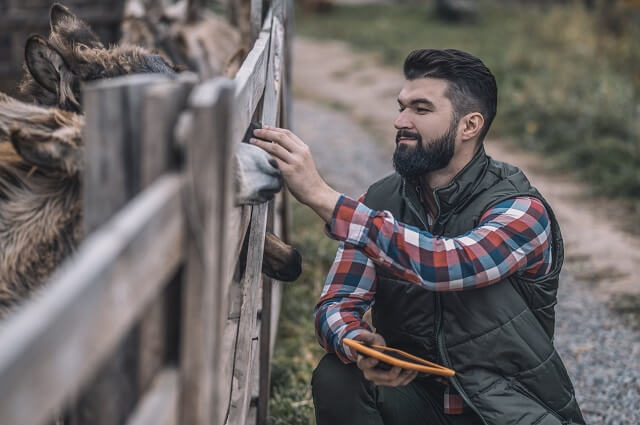
Hi everyone! I’m a woodworker and blogger, and this is my woodworking blog. In my blog, I share tips and tricks for woodworkers of all skill levels, as well as project ideas that you can try yourself.