Woodworking is a craft that dates back centuries, with artisans carving and shaping wood into beautiful and functional pieces. While safety is a crucial aspect of any trade or profession, it may come as a surprise to many that woodworkers often choose not to wear welding gear. In this article, we will delve into the reasons behind this decision, exploring the unique risks associated with woodworking and the historical context that has shaped safety practices in the field.
Safety should always be the top priority in any woodworking project. Protective equipment, such as welding gear, plays a vital role in ensuring the well-being of woodworkers. However, it is perplexing to discover that many woodworkers opt not to utilize this essential protective gear. To comprehend this practice better, we must first understand the reasons behind it.
As we examine the reasons why woodworkers forgo wearing welding gear, it is essential to explore the distinctive risks associated with woodworking itself. Woodworking presents its own set of hazards, including sharp tools, flying particles, toxic fumes from certain woods, and potential injuries from machinery accidents. These risks are inherent in the craft and require careful consideration when it comes to maintaining worker safety.
In summary, understanding the reasons why woodworkers do not wear welding gear is crucial for comprehending their choices and evaluating their impact on safety in woodworking. From exploring the unique risks associated with woodworking to considering historical practices and cultural influences on safety practices, we will delve into various factors contributing to this dilemma. By doing so, we can identify potential solutions and work towards finding a balance between tradition, practicality, and safety in woodworking.
Safety First
Woodworking is a rewarding and fulfilling hobby, but it also comes with its fair share of risks. From flying wood chips and sawdust to the potential for injury from sharp tools, safety should always be a top priority for woodworkers. One crucial aspect of safety in woodworking is the use of protective equipment, including but not limited to eyewear, gloves, and respiratory protection.
When it comes to exploring the unique risks associated with woodworking, it becomes apparent why protective equipment is essential. Woodworking often involves using power tools such as saws and routers, which can generate high speeds and forces that can lead to accidents. Additionally, the cutting of wood produces fine dust particles that can pose health risks if inhaled.
Protective gear such as goggles or safety glasses help prevent eye injuries caused by flying wood chips or sawdust. Gloves provide protection against cuts and splinters while also improving grip on hand-held tools.
It is worth noting that the historical context of woodworking has shaped safety practices today. In traditional wooden boatbuilding or carpentry work, heavy-duty gloves were not commonly used due to their bulkiness hindering intricate handwork. However, as technology advanced and more precise tools became available, the need for protective gloves became evident. Understanding these historical practices can help shed light on why some woodworkers may resist wearing welding gear today.
Protective Equipment | Purpose |
---|---|
Eyewear (goggles or safety glasses) | Prevent eye injuries from flying wood chips or sawdust |
Gloves | Protect hands against cuts and splinters |
Respiratory protection (masks) | Prevent inhalation of fine dust particles |
As woodworkers consider the importance of safety gear, it is not uncommon for various misconceptions to arise. One common misconception is that woodworking does not require the same level of protection as other industries, such as metalworking or construction. However, the risks associated with woodworking should not be underestimated. While woodworking may have different hazards, they are no less dangerous and should be taken seriously.
Exploring the Unique Risks Associated with Woodworking
Woodworking is a craft that has been practiced for centuries and has evolved significantly over time. However, with every woodworking project comes unique risks and hazards that woodworkers must be aware of to ensure their safety. In this section, we will explore the specific risks associated with woodworking and why it is important for woodworkers to understand and address these risks.
Wood Dust: A Silent Threat
One of the most significant risks in woodworking is the production of wood dust. When working with wood, especially during cutting or sanding processes, small particles of dust are released into the air. These fine particles can easily be inhaled and can pose serious health risks over time. Prolonged exposure to wood dust is known to cause respiratory problems, such as allergies, asthma, and even more severe conditions like chronic obstructive pulmonary disease (COPD) or cancer.
To mitigate the risks associated with wood dust, woodworkers should always wear proper respiratory protection such as N95 masks or respirators equipped with high-efficiency particulate air (HEPA) filters. Additionally, it is crucial to maintain proper ventilation in the workspace by using dust extraction systems or wearing a personal dust collection device that captures airborne particles directly at the source.
Sharp Tools and Machinery
Woodworking involves working with sharp tools and machinery that can cause injuries if not handled properly. Accidental slips or mishandling of tools can lead to deep cuts, amputations, or other serious wounds. Power tools such as table saws, band saws, routers, and power drills should always be used with caution while following all safety guidelines provided by manufacturers.
Woodworkers should wear appropriate personal protective equipment (PPE) like gloves and safety glasses to protect themselves from potential accidents caused by sharp tools. It is also essential to maintain a clean and organized workspace free from clutter that may contribute to accidents or tripping hazards.
Chemical Hazards
In certain woodworking processes, the use of chemicals like varnishes, stains, glues, and solvents is common. While these substances can enhance the aesthetic appeal and functionality of wood projects, they can also pose health risks if not handled properly. Exposure to harmful chemicals can result in skin irritation, respiratory issues, or even long-term health effects.
To minimize the risks associated with chemical hazards, woodworkers should always read and follow the instructions provided by manufacturers when using any chemical products. It is also crucial to work in a well-ventilated area with proper personal protective equipment such as gloves and goggles.
By understanding and addressing these unique risks associated with woodworking, woodworkers can ensure their safety and protect themselves from potential harm. Taking necessary precautions, wearing appropriate protective gear, and following best practices will contribute to a safe and enjoyable woodworking experience.
Historical Context
Woodworking has a rich history that dates back centuries, and this historical context has shaped the safety practices in the craft. Throughout history, woodworking traditions have played a significant role in influencing the use of safety equipment such as welding gear.
In the early days of woodworking, when tools were simpler and less sophisticated, woodworkers often did not have access to or utilize protective equipment like welding gear. This lack of safety practices was due to several factors. Firstly, there was limited knowledge about the potential hazards associated with woodworking, as scientific understanding of these risks was still developing. Additionally, traditional woodworking methods focused more on efficiency and craftsmanship rather than prioritizing worker safety.
Traditional woodworking techniques often involved hand tools and manual labor, which did not create the same risks as modern woodworking machinery does today. Woodworkers primarily relied on hand saws, chisels, and planes to shape wood. The level of physical exertion required by these tools was high compared to automated machinery commonly used today. Therefore, protective equipment like welding gear was not deemed necessary for those working with traditional hand tools.
Another factor that contributed to the lack of safety practices in woodworking was societal norms and cultural values associated with craftsmanship. Woodworking has long been considered an art form deeply rooted in tradition and heritage. The focus was on preserving techniques passed down through generations rather than adhering to modern workplace safety standards.
Despite these historical factors shaping woodworking traditions and safety practices over time, it is essential to recognize that advancements have been made in recent years towards promoting safer working conditions. Occupational health and safety regulations have been implemented in many countries around the world, highlighting the importance of using personal protective equipment (PPE) such as welding gear.
Overall, understanding the historical context of woodworking helps shed light on why woodworkers traditionally did not wear welding gear or other protective equipment. While past practices were rooted in cultural traditions and limited awareness of risks, it is crucial for woodworkers today to prioritize safety and make use of modern safety equipment to prevent accidents and protect their well-being.
Common Misconceptions Surrounding Welding Gear in Woodworking
As with any industry or craft, there are several common misconceptions surrounding the use of welding gear in woodworking. These misconceptions often contribute to woodworkers not wearing adequate protective equipment while engaging in their craft. It is important to address and debunk these misconceptions in order to promote a safer working environment for woodworkers.
One common misconception is that welding gear is uncomfortable and restricts movement, making it difficult to work efficiently. However, advancements in technology have led to the development of more ergonomic and lightweight protective equipment specifically designed for woodworkers. For example, specialized gloves and aprons made from materials such as Kevlar provide both protection and flexibility. Additionally, modern welding helmets are lighter and more adjustable, allowing woodworkers to have enhanced visibility without compromising safety.
Another misconception is that woodworking does not pose the same risks as other industries that require welding gear. While it may be true that woodworking does not involve the same level of heat exposure or sparks as metalworking, there are still serious hazards involved. Wood dust, for instance, can ignite easily and lead to fires or explosions if proper precautions are not taken.
In addition, woodworkers are exposed to harmful fumes from certain types of wood finishes or adhesives used in their projects. Protective equipment such as respirators and safety goggles should be worn to minimize these health risks.
Lastly, some woodworkers may believe that their experience and skill level make them immune to accidents or injuries, rendering protective gear unnecessary. However, accidents can happen even to the most experienced individuals. Woodworking tools are sharp and accidents involving cuts or splinters can occur at any time. Welding gear provides an extra layer of protection against these risks and can significantly reduce the severity of injuries.
To address these misconceptions effectively, it is crucial for educational institutions and industry organizations to provide comprehensive training on woodworking safety practices. By emphasizing the importance of wearing welding gear and debunking the misconceptions surrounding its use, woodworkers can make more informed decisions about their personal safety.
Misconception | Debunking |
---|---|
Welding gear is uncomfortable and restricts movement. | Advancements in technology have led to the development of more ergonomic and lightweight protective equipment specifically designed for woodworkers. |
Woodworking does not pose significant risks that require welding gear. | Wood dust can ignite easily, and woodworkers are exposed to harmful fumes from finishes or adhesives. Protective equipment should be worn to minimize these risks. |
Experienced woodworkers do not need welding gear as they are less prone to accidents. | Accidents can happen regardless of skill level. Welding gear provides an extra layer of protection against injuries from sharp tools or unexpected incidents. |
Cost vs. Benefit Analysis
The Expense of Welding Gear
One of the main reasons why woodworkers may choose not to wear welding gear is the cost associated with purchasing and maintaining the necessary equipment. Welding gear, such as helmets, gloves, and protective clothing, can be quite expensive, especially if high-quality gear is desired for maximum safety. For woodworkers who pursue woodworking as a hobby or side job, the investment required for welding gear may seem excessive and unnecessary.
Perceived Risk versus Actual Risk
Another factor that influences woodworker’s decision regarding welding gear is their perception of the risk involved in woodworking projects. Many woodworkers believe that they are at a lower risk of exposure to harmful fumes or sparks compared to those engaged in metalworking or industrial welding. This perception can lead woodworkers to underestimate the importance of wearing proper protective equipment.
However, it is essential to understand that woodworking still poses its own unique risks. Wood dust generated during cutting and sanding processes can contribute to respiratory issues over time. Additionally, there is always a risk of accidental fires or burns from interacting with power tools and hot surfaces. Neglecting proper protection puts woodworkers at higher risk of injury or long-term health complications.
Considering Long-Term Health Costs
While upfront costs may deter some woodworkers from investing in welding gear, it is crucial to consider the long-term impacts on their health and wellbeing. Exposure to harmful fumes and particles generated during woodworking projects can lead to respiratory problems like asthma, lung damage, and even cancer over time. These potential health risks should be weighed against the expense of purchasing protective equipment.
Furthermore, failing to protect oneself adequately from potential workplace accidents can result in increased medical costs due to injuries. Treating burns or other injuries resulting from accidents could be far more expensive than investing in proper safety gear initially. Woodworkers need to consider these long-term health costs when evaluating the economic factors influencing their choices regarding welding gear. Ultimately, the financial investment in protective equipment may prove to be more cost-effective in the long run.
Cultural Factors
Woodworking, like any other trade or craft, is influenced by cultural factors that shape the practices and choices of woodworkers. These social and professional influences play a significant role in whether or not woodworkers choose to wear welding gear. Understanding these cultural factors can provide valuable insights into the reasons behind their decisions.
Peer Pressure and Norms
One of the main cultural factors affecting woodworkers’ decision not to wear welding gear is peer pressure and the influence of norms within the woodworking community. In some woodworking circles, there may be a prevailing belief that wearing welding gear is unnecessary or even seen as a sign of weakness. Woodworkers who adhere to these norms may feel pressured to conform by not wearing protective equipment, even if they understand the importance of safety.
Breaking away from established norms can be challenging, especially when it comes to personal protective equipment. Woodworkers who choose to wear welding gear might feel isolated or judged by their peers, which further reinforces the cultural aversion towards using such equipment.
Traditional Craftsmanship
Woodworking has a rich historical context rooted in traditional craftsmanship. There is often a deep respect for tradition within woodworking communities, where skills are passed down through generations. This focus on tradition can lead some woodworkers to reject modern safety practices, including wearing welding gear.
Additionally, certain techniques in woodworking require close proximity to the materials being manipulated. Woodworkers who have honed their skills over many years may have developed alternative methods that they believe mitigate risks without relying on external protective equipment like welding gear. This emphasis on traditional craftsmanship can make it challenging for newer approaches that prioritize safety measures to gain acceptance within woodworking communities.
Cultural factors have a strong influence on the choices woodworkers make regarding wearing welding gear. Peer pressure and adherence to established norms within woodworking communities can discourage the use of protective equipment. Additionally, the emphasis on traditional craftsmanship can override modern safety practices in favor of alternative methods. Understanding these cultural factors is crucial in effectively addressing the challenges and finding solutions to improve woodworking safety.
Practical Alternatives
Woodworkers not wearing welding gear can be a concerning issue when it comes to their safety. However, there are practical alternatives that can help mitigate the risks associated with woodworking. These solutions provide a balance between tradition, practicality, and safety.
One possible solution is to use alternative forms of protective equipment that are more suitable for woodworking tasks. Traditional welding gear may not be designed specifically for woodworking activities and could hinder a woodworker’s mobility or dexterity. Instead, woodworkers can consider using specialized gear such as reinforced gloves, aprons made from flame-resistant materials, and protective eyewear specifically designed for woodworking tasks. These alternatives provide sufficient protection while allowing the woodworker to perform their tasks comfortably.
Another practical alternative is to implement safety procedures and practices that minimize the need for welding gear altogether. This includes adopting techniques or tools that eliminate or reduce the risk of sparks or fire during woodworking activities.
For example, woodworkers can explore options like using hand tools instead of power tools whenever possible, which reduces the likelihood of sparks being produced. Additionally, implementing a strict policy on keeping flammable materials away from work areas can significantly reduce the risk of fires.
Furthermore, creating awareness and education campaigns within the woodworking community can play a significant role in promoting safe practices without relying solely on welding gear. Sharing stories of accidents or near misses due to lack of protection can serve as a reminder for woodworkers to prioritize their safety. Offering training workshops or seminars on proper safety procedures specific to woodworking can also empower woodworkers with essential knowledge to make informed decisions regarding protective equipment.
By identifying these potential solutions and putting them into practice, woodworkers can address the welding gear dilemma effectively while still ensuring their safety. It is crucial for individuals in the woodworking community to collaborate and share insights on what works best for them in terms of protective measures. Striking a balance between tradition, practicality, and safety ultimately creates an environment where woodworkers feel comfortable while minimizing unnecessary risks.
Expert Advice
Woodworking is a craft that requires skill, precision, and attention to detail. It also comes with inherent risks, making safety a top priority for woodworkers. In this section, we will delve into the expert advice and insights from seasoned woodworkers and safety professionals who have firsthand experience in the field.
One key aspect that many experts emphasize is the importance of wearing proper protective equipment when working with wood. This includes not only safety goggles and gloves but also respiratory protection to prevent inhalation of wood dust particles. Woodworking can produce fine dust that can irritate the respiratory system or even lead to serious health issues such as asthma or lung disease. Therefore, using appropriate respiratory protection is crucial in safeguarding woodworkers’ long-term health.
Another piece of advice shared by experts is the need for training and education in safe woodworking practices. Seasoned woodworkers stress the importance of understanding how machinery works, as well as knowing how to properly handle hand tools. Safety professionals recommend attending workshops or classes to learn best practices for using tools and machinery safely. By doing so, woodworkers can reduce the risk of accidents caused by improper use or lack of knowledge.
It is worth noting that expert advice varies depending on the specific woodworking task at hand. For instance, when it comes to using power tools like table saws or routers, experts stress the importance of machine guards and push sticks to maintain a safe distance between hands and blades. On the other hand, when carving intricate designs using chisels or carving knives, experts advise woodworkers to use cut-resistant gloves to protect their hands from accidental slips.
Expert Advice | Insights |
---|---|
Wearing Proper Protective Equipment | Safety goggles, gloves, and respiratory protection are crucial in safeguarding woodworkers’ health. |
Training and Education | Understanding machinery and proper tool handling significantly reduces the risk of accidents. |
Task-specific Safety Measures | Varying advice depending on the woodworking task, such as using machine guards or cut-resistant gloves. |
The Future of Woodworking Safety
Woodworking has come a long way in terms of safety practices and technologies. As we look towards the future, it is important to explore how these advancements can further improve the safety of woodworkers. This section will discuss some of the evolving practices and technologies that are shaping the future of woodworking safety.
One area where technology has made significant progress is in the development of new types of protective equipment. Traditional welding gear may not have been suitable for woodworking due to its heavy-duty nature and limited mobility. However, manufacturers are now designing protective equipment specifically for woodworkers, taking into consideration their unique needs and requirements. These new types of gear offer improved comfort, breathability, and maneuverability without compromising on safety.
In addition to advancements in protective equipment, there are also emerging practices that aim to enhance woodworking safety. One such practice is implementing comprehensive safety training programs for woodworkers. These programs go beyond basic equipment usage and focus on hazard identification, risk assessment, and safe work practices specific to woodworking tasks. By equipping woodworkers with the knowledge and skills to identify potential risks and take appropriate precautions, these training programs play a crucial role in preventing accidents and injuries.
Another aspect of the future of woodworking safety lies in the integration of technology into woodworking tools and machinery. Advanced sensors can be installed in machines to detect anomalies or unsafe conditions, automatically stopping operations to prevent accidents. Additionally, digital tools such as virtual reality simulations can be used for training purposes, allowing woodworkers to practice various scenarios in a safe environment before executing them in real life.
As we look ahead, it is clear that the future of woodworking safety lies in an integration of evolving practices and technologies. By continuously improving protective equipment, implementing comprehensive training programs, and leveraging technological innovations, we can create safer working environments for woodworkers while preserving traditional craftsmanship. The next section will delve deeper into expert advice from seasoned woodworkers and safety professionals who have valuable insights on these evolving practices and technologies.
Conclusion
In conclusion, it is clear that the issue of woodworkers not wearing welding gear is a complex one that involves multiple factors. The importance of safety cannot be overstated in woodworking, as this craft presents unique risks and hazards. However, historical traditions and cultural influences have shaped the practices and mindset of woodworkers, sometimes leading to a lack of priority for protective equipment.
Throughout this article, we have explored the various reasons behind woodworkers not wearing welding gear, including common misconceptions, economic considerations, and social influences. It is important to address these factors in order to find a balance between tradition, practicality, and safety in woodworking.
One potential solution to the welding gear dilemma is through education and raising awareness. By providing woodworkers with accurate information about the risks they face and the benefits of using protective equipment, we can help change attitudes and behaviors. Additionally, promoting the development and use of innovative technologies can provide practical alternatives to traditional methods that may be more appealing to woodworkers while still ensuring their safety.
The future of woodworking safety lies in evolving practices and technologies. As our understanding of the risks improves and new solutions are developed, it is crucial for woodworkers, safety professionals, and industry leaders to work together towards creating a safer working environment. By finding a balance between tradition, practicality, and safety in woodworking, we can continue to preserve this timeless craft while prioritizing the well-being of those who practice it.
Frequently Asked Questions
Should carpenters wear wedding rings?
The decision of whether carpenters should wear wedding rings ultimately depends on personal preference and the nature of their work. While some carpenters may choose to wear wedding rings as a symbol of their commitment, others may opt not to wear them due to safety concerns or workplace regulations.
Carpenters often work with tools and machinery that can pose a risk of injury, such as getting caught in machinery or causing discomfort while handling tools. Therefore, some carpenters choose to remove their wedding rings while working in order to prioritize safety and minimize potential hazards.
Why do some married couples not wear their wedding rings?
There are various reasons why some married couples may choose not to wear their wedding rings. Firstly, practicality and comfort play a significant role for individuals who have jobs or hobbies that make wearing a ring inconvenient or potentially dangerous. This includes occupations such as construction work, healthcare professions, cooking, or sports activities where a ring could get caught on equipment or pose a risk during physical activity.
Additionally, personal preferences, cultural norms, and individual beliefs may also influence this decision. Some couples might find alternative ways to symbolize their commitment or simply feel that they do not need to display their marital status through jewelry.
Are silicone rings safe for carpenters?
Silicone rings have gained popularity as an alternative for traditional metal wedding bands in environments where safety is paramount, like for carpenters. These rings are made from silicone rubber material which is non-conductive and highly flexible, making them safe for individuals who work with electricity or hand tools regularly. Silicone rings are designed to break under sufficient force instead of causing severe injury if caught on machinery or equipment.
They are also heat-resistant and non-allergenic, making them suitable for carpenters who may encounter heat sources or have sensitivities to certain metals. However, it’s important for each carpenter to assess the specific risks involved in their work environment before deciding whether silicone rings are the best choice for them personally.
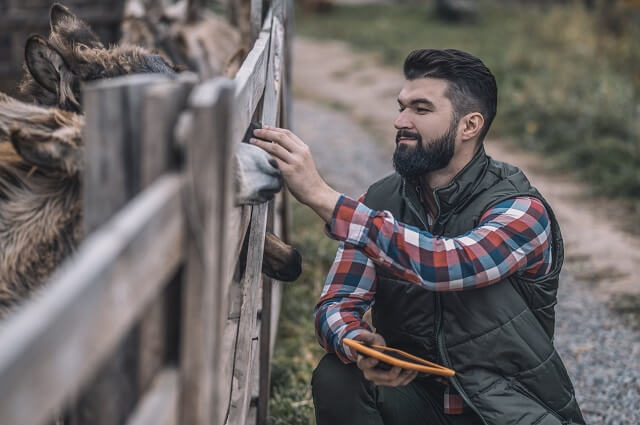
Hi everyone! I’m a woodworker and blogger, and this is my woodworking blog. In my blog, I share tips and tricks for woodworkers of all skill levels, as well as project ideas that you can try yourself.