Properly maintaining woodwork machines is crucial for ensuring their longevity, efficiency, and safety. Woodwork machines are essential tools in woodworking industries and workshops, and they require regular care and maintenance to perform at their best. Neglecting maintenance can result in decreased performance, increased risk of accidents, and costly repairs. This article provides a comprehensive guide on how to maintain woodwork machines effectively.
Woodwork machines come in various types, including table saws, planers, jointers, routers, and more. Each machine has specific maintenance requirements that need to be understood and followed. By properly maintaining these machines, you can maximize their lifespan and ensure optimal performance in your woodworking projects.
However, before embarking on the maintenance process, it is important to take essential safety measures. Woodworking machines can be dangerous if not used or maintained with caution. This includes wearing protective gear such as goggles and gloves and ensuring the machines are powered off and unplugged before performing any maintenance tasks.
Regular inspections are the first step towards effective machine maintenance. By inspecting your woodwork machines regularly, you can identify any potential issues or wear and tear that may affect their performance.
Regular inspections also allow you to spot safety concerns that need immediate attention. In the following sections of this article, we will delve deeper into best practices for cleaning and lubrication of woodwork machines, replacing worn-out parts, calibration and alignment techniques, proper storage methods, troubleshooting common issues, as well as when professional maintenance services may be necessary.
Understanding the Different Types of Woodwork Machines
Woodworking machines play a crucial role in the woodworking industry, helping professionals and hobbyists create intricate pieces of furniture and other wooden objects. However, before diving into the maintenance aspect, it is essential to have a basic understanding of the different types of woodworking machines available. This overview will provide a brief explanation of some common types of machines frequently used in woodworking.
Table Saw
The table saw is one of the most commonly used woodworking machines. It consists of a circular blade mounted onto an arbor driven by an electric motor. The blade protrudes through the surface of a table and can be adjusted in height or tilted at various angles, allowing for accurate cuts in different shapes and sizes.
Jointer
A jointer is used to create flat surfaces along the edges or faces of wooden boards. It consists of an infeed table, an adjustable fence, and rotating knives that remove material as it passes over them. Jointers are particularly useful when preparing lumber for glue-ups or when creating precise edges for joinery work.
Planer
A planer is used to create parallel and flat surfaces on wooden boards with uniform thickness. The machine has two parallel tables on top and bottom, between which the board is fed. The planer removes material from the top surface until it reaches the desired thickness, resulting in smooth and consistent boards.
Router
Routers are versatile woodworking machines that use different types of cutters for shaping wood. They can be handheld or mounted onto routers tables and are commonly used for decorative edges, cutting grooves or dados, making mortises, or creating intricate patterns on wood surfaces.
Bandsaw
Bandsaws consist of a continuous band with teeth stretched between two wheels that rotate in one direction. It is primarily used for making curved cuts due to its narrow blade size and ability to maneuver easily. Bandsaws are proficient at resawing thick stock into thinner pieces, creating decorative scrollwork, or producing smooth cuts in irregular shapes.
While this overview provides a glimpse into the different types of woodworking machines, it is important to note that there are numerous other specialized machines available for specific woodworking tasks. Familiarizing yourself with these machines and understanding their functionalities will not only enhance your maintenance practices but also help you make informed decisions when performing repairs or troubleshooting issues.
Essential Safety Measures
Performing maintenance on woodwork machines can be a potentially dangerous task if proper safety measures are not taken. Before starting any maintenance procedures, it is crucial to prioritize safety to prevent accidents and injuries. Here are some essential safety measures that should be followed before performing maintenance on woodwork machines:
Read the User Manual
Familiarize yourself with the specific safety guidelines and instructions provided by the manufacturer in the user manual for each machine you plan to maintain. The user manual will outline any unique safety considerations or precautions specific to that machine.
Wear Protective Gear
Always wear appropriate personal protective equipment (PPE) when working with woodwork machines. This may include safety glasses, ear protection, gloves, and a dust mask or respirator, depending on the type of machine and the nature of your maintenance tasks.
Inspect the Machine
Before beginning any maintenance work, inspect the machine thoroughly for any signs of damage or wear that could pose a risk during maintenance. Check for loose or damaged parts, frayed cords or hoses, and any other visible abnormalities. If you notice any issues, address them before proceeding.
Disconnect Power Supply
To ensure your own safety while performing maintenance tasks, always disconnect the power supply or unplug the machine from its power source before starting any work on electrical components or moving parts.
Lockout/Tagout Procedures
If your maintenance work involves accessing internal components or machinery under power, it is important to implement lockout/tagout procedures. This ensures that no one can accidentally turn on the machine while you are working on it.
By following these essential safety measures, you can minimize the risks associated with maintaining woodwork machines and create a safer environment for yourself and those around you. It is crucial to prioritize safety and take the necessary precautions to prevent accidents or injuries during maintenance tasks.
Regular Inspections
Regular inspections are a crucial part of maintaining woodwork machines and ensuring their optimal performance. By conducting regular inspections, woodworkers can identify any potential issues or defects before they become major problems. This not only helps to prevent costly repairs or replacements but also extends the lifespan of the machines.
When performing regular inspections on woodwork machines, it is important to pay attention to several key areas. First, check the overall condition of the machine’s structure and components. Look for any signs of wear and tear, such as loose or damaged parts, frayed cables, or rusted surfaces. These issues should be addressed promptly to prevent further damage or safety hazards.
In addition to inspecting the physical condition of the machine, it is important to assess its functionality. Test all controls and mechanisms to ensure they are working properly. Pay attention to any unusual noises, vibrations, or irregular movements that could indicate underlying issues. It is also recommended to check the accuracy and precision of measurements and adjustments by performing test cuts or tasks.
To make the inspection process more efficient and organized, create a checklist of items to inspect for each machine. This can include specific parts, components, or functions that need regular attention based on the manufacturer’s recommendations. By following a checklist during inspections, woodworkers can ensure that no important aspect is overlooked.
- Check the overall condition of the machine’s structure
- Inspect for any signs of wear and tear
- Assess the functionality of controls and mechanisms
- Pay attention to unusual noises, vibrations, or irregular movements
- Check the accuracy and precision of measurements and adjustments
- Create a checklist for efficient and comprehensive inspections
By incorporating regular inspections into their maintenance routine, woodworkers can catch potential issues early on and address them promptly. This proactive approach helps reduce downtime due to unexpected breakdowns and ensures that woodwork machines are always operating at their best.
Cleaning and Lubrication
Woodwork machines are complex tools that require regular cleaning and lubrication to ensure they run smoothly and efficiently. Proper maintenance of these machines is important to extend their lifespan, prevent costly repairs, and maintain the quality of the woodwork produced. In this section, we will discuss the best practices for cleaning and lubricating woodwork machines.
Cleaning
- Regular dusting: Dust buildup can cause malfunctions and affect the accuracy of woodwork machines. Use a soft brush or vacuum cleaner with a brush attachment to remove dust from all areas of the machine, including hard-to-reach places.
- Cleaning agents: Depending on the type of woodwork machine, certain cleaning agents may be necessary for effective cleaning. Always refer to the manufacturer’s guidelines for recommended products that are safe to use on your specific machine.
- Cleaning surfaces: Pay particular attention to the surfaces that come into contact with wood or other materials during operation. Use a mild solvent or cleaner to remove any residue or build-up that may affect the smooth movement of parts.
- Removing debris: Regularly check for and remove any chips, sawdust, or other debris that may accumulate in or around the machine. This debris can interfere with proper operation and even pose safety hazards.
Lubrication
- Appropriate lubricants: Refer to your machine’s manual for recommendations on suitable lubricants for each part. It’s important not to use excessive amounts of lubricant as it can attract more dust and debris which could lead to issues in the long run.
- Lubrication points: Identify all moving parts that require lubrication, such as gears, bearings, chains, pulleys, etc., and make sure they receive adequate lubrication according to the manufacturer’s guidelines.
- Frequent application: The frequency of lubrication depends on various factors such as usage frequency and operating conditions. However, as a general guideline, it is recommended to lubricate woodwork machines at least once a month.
- Wipe off excess lubricant: After applying lubricant, wipe off any excess to prevent it from attracting dust and debris that could interfere with the machine’s performance.
By following these best practices for cleaning and lubrication, woodwork machines will continue to operate smoothly and efficiently, ensuring high-quality woodworking results. Regular maintenance in this area will prolong the lifespan of your machine and minimize the risk of breakdowns or costly repairs.
Replacing Worn Out Parts
Replacing worn out parts is an essential aspect of maintaining woodwork machines in order to ensure optimal performance. Over time, certain components of the machine may become worn or damaged, which can negatively impact its efficiency and functionality. This section will discuss the importance of identifying these worn out parts and provide guidelines on how to replace them effectively.
To begin with, it is crucial for woodworkers to be able to identify the specific components that are affecting the machine’s performance. Commonly affected parts include blades, belts, bearings, and cutting tools. Signs of wear and tear can manifest in various ways such as inaccurate cuts, excessive vibration, or unusual noises produced by the machine during operation.
Once the worn out parts have been identified, it is important to source replacement components that are compatible with the specific make and model of the woodwork machine. It is recommended to refer to the manufacturer’s guidelines or consult with a professional if unsure about choosing the right replacement parts.
Replacing these worn out parts should be done with caution and in accordance with proper safety measures. It is advisable to turn off the machine and disconnect it from any power source before starting the replacement process. Additionally, using the appropriate tools and following manufacturer instructions will help ensure a successful replacement.
Regularly replacing worn out parts not only improves a woodwork machine’s performance but also extends its lifespan. By properly maintaining these key components, woodworkers can enjoy consistent accuracy, efficiency, and safety during their woodworking projects.
Common Worn Out Parts | Replacement Guidelines | Safety Measures |
---|---|---|
Blades | Refer to manufacturer guidelines or consult professionals for sourcing replacement blades | Turn off machine and disconnect from power source before replacing blades; Use appropriate tools |
Belts | Refer to manufacturer guidelines or consult professionals for sourcing replacement belts | Turn off machine and disconnect from power source before replacing belts; Use appropriate tools |
Bearings | Refer to manufacturer guidelines or consult professionals for sourcing replacement bearings | Turn off machine and disconnect from power source before replacing bearings; Use appropriate tools |
Cutting Tools | Refer to manufacturer guidelines or consult professionals for sourcing replacement cutting tools | Turn off machine and disconnect from power source before replacing cutting tools; Use appropriate tools |
Calibration and Alignment
Calibration and alignment are crucial aspects of maintaining woodwork machines to ensure accuracy and precision in their performance. When a machine is properly calibrated and aligned, it can produce high-quality and consistent results, reducing the chances of errors or faulty work. This section will discuss the importance of calibration and alignment in woodwork machines and provide best practices for achieving optimal results.
Woodwork machines, such as table saws, jointers, planers, and routers, rely on precise measurements to create accurate cuts and smooth surfaces. Over time, these machines can experience wear and tear that may affect their alignment or calibration. Factors such as vibrations, improper use, or accidental impacts can cause misalignment or throw off the accuracy of measurements.
Best Practices for Calibration and Alignment: |
---|
1. Use manufacturer’s guidelines: Refer to the machine’s user manual for specific instructions on calibration and alignment procedures. |
2. Check parallelism: Ensuring that the tabletop or fence is parallel to the blade or cutting tool is essential for accurate cuts. |
3. Measure with precision tools: Utilize precision measuring tools like dial indicators or laser guides to assess alignment. |
Regular maintenance tasks such as lubrication should also be carried out after calibration and alignment to enhance the overall performance of woodwork machines. By prioritizing calibration and alignment in your maintenance routine, you can maintain consistent accuracy in your woodwork projects.
Storage and Environmental Factors
Woodwork machines are valuable tools that require proper care and maintenance, even when not in use. In this section, we will discuss the importance of storage and environmental factors in protecting woodwork machines from damage. By implementing the recommended practices, you can extend the lifespan of your machines and ensure they remain in optimal condition for longer periods of time.
Choosing an Appropriate Storage Location
When it comes to storing woodwork machines, choosing the right location is crucial. Machines should be stored in a clean, dry, and well-ventilated area to prevent moisture buildup and rust formation. Avoid places that are prone to temperature fluctuations or high humidity levels, as these conditions can accelerate wear and tear on machine components.
Additionally, consider the security aspect of storage as well. Woodwork machines can be targets for theft or vandalism if left unattended in an insecure area. Ensure that the storage location has appropriate locking mechanisms or invest in additional security measures such as alarms or surveillance cameras if needed.
Proper Machine Covering and Protection
Covering your woodwork machines when they are not in use is another essential measure to protect them from dust, debris, and other contaminants that can cause damage. Use fitted covers specifically designed for your machine models whenever possible. These covers help to keep unwanted particles out while allowing airflow to prevent moisture buildup.
When covering your machines, make sure they have completely cooled down after use. This helps prevent condensation from forming on their surfaces and causing corrosion over time. Remember to remove any loose accessories or attachments before covering the machines as well.
The Role of Climate Control
Extreme temperatures can significantly impact the performance and longevity of woodwork machines. If possible, store them in a controlled climate environment where temperature and humidity levels remain consistent year-round. Consider investing in heating or cooling systems for your storage area if necessary.
In regions with high humidity or areas prone to seasonal changes, using dehumidifiers or humidifiers can help regulate moisture levels and prevent damage to the machines. Regularly monitor and adjust the climate control settings as needed to ensure optimal conditions for your woodwork machines.
By implementing proper storage practices and taking into consideration environmental factors, you can protect your woodwork machines from unnecessary damage and extend their lifespan significantly. This will not only save you money on repairs or replacements but also ensure that your machines maintain their performance and accuracy over time.
Troubleshooting Common Issues
Woodwork machines are highly reliable tools that help craftsmen create beautiful pieces of furniture and other wooden objects. However, like any mechanical equipment, they can sometimes encounter issues that affect their performance. In this section, we will explore some common problems that woodwork machines may face and provide tips on how to identify and resolve them.
One common issue that many woodwork machines experience is a decrease in cutting or drilling power. This can be caused by various factors such as a dull blade or drill bit, improper tensioning of the belts or chains, or motor wear and tear. To determine the cause of the problem, it is important to first conduct a thorough inspection of the machine and its components.
If the issue is due to a dull blade or drill bit, it is recommended to replace them with new ones. Dull blades not only reduce cutting efficiency but also increase the risk of accidents. Proper tensioning of belts or chains is crucial for maintaining optimal performance. Loose belts or chains can result in slippage which leads to reduced power transmission. Tightening or replacing them if necessary can solve this problem.
Another common problem that woodwork machines may encounter is inaccurate cutting or drilling. This can be frustrating as it affects the quality and precision of the final product. Misaligned fences, tables, or guides are often the culprits behind this issue. Regular calibration and alignment should be performed to ensure accuracy and precision in woodwork machines.
Issue | Possible Cause | Solution |
---|---|---|
Decreased cutting/drilling power | Dull blade/drill bit; loose belts/chains; motor wear | Replace blades/drill bits; tighten or replace belts/chains; check motor |
Inaccurate cutting/drilling | Misaligned fences/tables/guides | Calibrate and align machine components regularly |
In addition to the problems mentioned above, other common issues in woodwork machines include excessive vibration, difficulty in adjusting settings, and sudden motor stalling. These problems can often be resolved by conducting regular inspections, cleaning and lubricating the machine parts, and replacing worn-out components. In some cases, seeking professional maintenance services may be necessary to address more complex issues.
By troubleshooting common issues promptly and effectively, woodworkers can ensure that their woodwork machines operate at their full potential, resulting in better quality products and a smoother working experience.
Sources:
- Reference 1.
- Reference 2.
Professional Maintenance Services
Woodwork machines are complex pieces of equipment that require regular maintenance to ensure optimal performance and longevity. While many routine maintenance tasks can be carried out by the machine operators themselves, there are instances where it is necessary to seek professional maintenance services. In this section, we will discuss when and why it is important to turn to experts for assistance in maintaining woodwork machines.
When to Seek Professional Maintenance Services
There are several situations in which it is advisable to consult professionals for the maintenance of woodwork machines. First and foremost, if you are not confident in your own ability to carry out complex repairs or adjustments, it is best to leave the task in the hands of experienced technicians. This can help prevent further damage or potential safety hazards.
Additionally, certain maintenance tasks may require specialized knowledge or equipment that you may not have access to. For example, if your machine requires electrical repairs or calibration, it is crucial to enlist the expertise of a qualified electrician or technician who has experience working with woodwork machinery.
Lastly, scheduling regular professional inspections and servicing can help identify potential issues before they escalate into major problems. By conducting preventative maintenance on a regular basis, you can avoid costly breakdowns and downtime that could negatively impact your woodworking business.
The Benefits of Professional Maintenance Services
Seeking expert assistance for maintaining woodwork machines offers a range of benefits. Firstly, experienced technicians have an in-depth understanding of these machines and their components, allowing them to diagnose problems accurately and efficiently. They also possess the knowledge required to implement appropriate solutions and make adjustments that enhance performance.
Furthermore, professional maintenance services often come with warranties or guarantees on the work carried out. This provides peace of mind knowing that any issues arising from the maintenance work will be promptly addressed at no additional cost. Additionally, these warranties may cover specific parts or labor costs for a certain period of time, further reducing potential expenses.
Lastly, engaging professional maintenance services allows machine operators and business owners to focus on their core responsibilities without being burdened by complicated repair or maintenance tasks. This not only saves time but also ensures that the woodwork machines are in the hands of experts who can handle any problems effectively.
Conclusion
In conclusion, the proper maintenance of woodwork machines is crucial for ensuring their longevity and optimal performance. By following the recommended guidelines and precautions outlined in this article, woodworkers can extend the lifespan of their machines and minimize the risk of accidents or injuries.
Regular inspections are the first step in machine maintenance. By conducting routine checks, woodworkers can identify any issues or signs of wear and tear before they develop into major problems. This allows for timely repairs or replacements, thereby preventing unnecessary downtime and costly repairs in the future.
Cleaning and lubrication are also essential practices for keeping woodwork machines running smoothly. Regularly removing dust, debris, and rust from the surfaces helps to maintain their efficiency and prevent clogs or jams. Applying appropriate lubricants to moving parts reduces friction, minimizes wear and tear, and enhances overall machine performance.
Replacing worn-out parts is another important aspect of machine maintenance. As components age or become damaged, they can affect the machine’s functionality and accuracy. Identifying these parts early on through regular inspections allows for timely replacements, improving both productivity and safety.
Calibration and alignment should also be a part of regular maintenance routines. Ensuring that woodwork machines are properly calibrated enhances their precision and accuracy. Correct alignment minimizes errors during cutting or shaping processes, resulting in high-quality outputs.
Furthermore, storing machines correctly when not in use is crucial for protecting them from damage caused by environmental factors such as moisture or extreme temperatures. Proper storage can significantly increase the lifespan of woodwork machines.
In some cases, despite all efforts put into regular maintenance, issues may still arise. Troubleshooting common problems requires proper knowledge and experience. Seeking expert assistance from professional maintenance services can help diagnose and resolve complex issues effectively.
Frequently Asked Questions
What are the ways of maintaining machines?
There are several ways to maintain machines in order to ensure their proper function and longevity. Firstly, regular cleaning is essential to remove any dirt, dust, or debris that may accumulate and affect the machine’s performance. This can include wiping down surfaces, clearing out ventilation areas, and ensuring all moving parts are free from obstructions. Additionally, lubrication is crucial to reduce friction between components and prevent wear and tear.
This involves applying appropriate lubricants to specific areas as recommended by the manufacturer. Another important aspect of machine maintenance is conducting routine inspections and checks to identify any signs of damage or malfunctioning parts. By catching any issues early on, repairs can be made promptly before they worsen and potentially cause more extensive damage.
What is maintenance of woodwork tools?
Maintenance of woodwork tools is necessary to keep them in optimal working condition and extend their lifespan. Regular upkeep involves various practices such as cleaning, sharpening, and adjusting the tools when needed. Cleaning involves removing sawdust or other debris from the tool’s surface using a brush or cloth, while also ensuring that no moisture is left behind to prevent rusting.
Sharpening tools such as chisels or plane blades ensures that they remain effective for cutting through wood smoothly without excessive effort. This can be done using sharpening stones or honing guides depending on the specific tool being maintained. Adjustments may also be required for certain tools such as planes to ensure their settings are suitable for different woodworking tasks.
What is maintenance in woodwork technology?
Maintenance in woodwork technology refers to the systematic processes carried out with the aim of keeping woodworking equipment and machinery in optimal working condition. It involves a combination of preventative measures along with regular checks and servicing procedures designed to minimize breakdowns and maximize efficiency in woodwork operations.
These maintenance tasks typically encompass various aspects including cleaning, lubricating moving parts, replacing worn-out components like belts or blades, checking electrical connections for faults, calibrating machinery settings for accuracy, and conducting overall inspections to identify potential issues. Regular maintenance is crucial for both the safety of workers and the quality of output produced by woodwork technology, ensuring that the machinery operates smoothly and efficiently at all times.
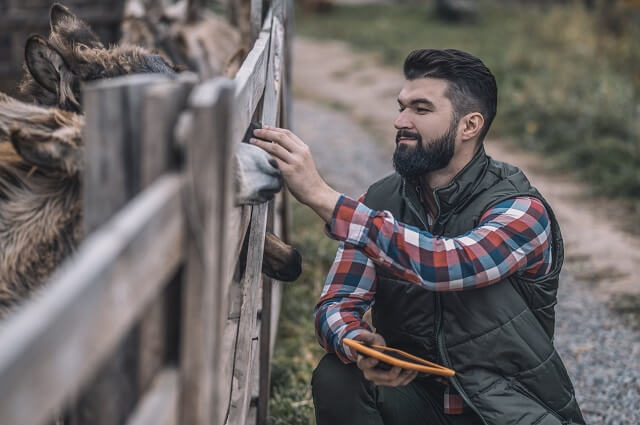
Hi everyone! I’m a woodworker and blogger, and this is my woodworking blog. In my blog, I share tips and tricks for woodworkers of all skill levels, as well as project ideas that you can try yourself.