Woodworking is a craft that requires precision and attention to detail. Whether it’s creating furniture, constructing cabinets, or carving intricate designs, woodworkers understand the value of achieving smooth and flawless finishes. However, friction can often impede their progress and affect the overall quality of their work. In this blog post, we will delve into the world of woodworking and explore the various techniques and tools that woodworkers use to make wood have less friction.
Friction plays a significant role in woodworking, and understanding its effect is crucial for any woodworker. Friction occurs when two surfaces rub against each other, resulting in resistance and heat generation. In woodworking processes such as planing, sanding, or using hand tools, excessive friction can lead to issues like rough surfaces, inaccurate cuts, or even damage to the tools themselves.
Woodworkers face common challenges due to friction that can jeopardize the outcome of their projects. Precision suffers as inaccuracies in measurements occur when moving parts encounter resistance from friction. Efficiency is reduced as laborious effort is required to overcome resistive forces while working with wood. Moreover, safety concerns arise when friction causes tools to stick or kickback unexpectedly during use.
Over time, traditional solutions have been developed by experienced woodworkers to reduce friction in their craft. Techniques such as waxing, oiling, and polishing have proved effective in providing smoother surfaces and minimizing frictional resistance. These age-old methods continue to be employed by many woodworkers today.
However, with advancements in technology and materials science, modern tools and techniques are now available that offer more precise and efficient ways of reducing friction in woodworking. Specialized coatings designed explicitly for low-friction applications have entered the market alongside lubricants tailored for woodworking purposes. Woodworkers now have access to a range of options that optimize performance while minimizing frictional constraints.
In this blog post series on “What Do Woodworkers Use to Make Wood Have Less Friction,” we will dive into various methods, tools, and techniques that woodworkers utilize to overcome the challenges presented by friction. From exploring the use of natural beeswax to discussing the significance of sanding and smoothing techniques, this blog post aims to empower woodworkers with knowledge and practical advice for achieving optimal friction reduction in their woodworking projects.
Understanding Friction in Woodworking
Friction is a fundamental concept in woodworking that plays a crucial role in the overall quality and outcome of the project. By understanding friction and its implications, woodworkers can make informed decisions on how to effectively reduce it. In woodworking, friction refers to the force that acts against the motion of two surfaces in contact, resulting in resistance and heat generation.
Friction affects various woodworking processes, such as cutting, sanding, planing, and joinery. When there is excessive friction between woodworking tools and the wood surface being worked on, it can lead to several issues. Firstly, high friction can cause tools to seize or get stuck, leading to inefficiency and potential damage to both the tool and the wood.
Secondly, friction can generate heat that may cause burn marks or scorching on the wood surface. Additionally, excessive friction can negatively impact precision by causing inaccuracies in measurements and cuts.
To address these challenges posed by friction in woodworking, woodworkers have developed traditional solutions over time. One common method used for centuries is waxing. Woodworkers often apply beeswax or specialized blends of waxes onto their tools or work surfaces. The waxes provide a lubricating effect that minimizes friction when working with wood. Another traditional technique is oiling, where oils are applied to maintain smoothness during cutting or shaping processes.
In recent years, advancements in technology have led to innovative tools and techniques specifically designed for reducing friction in woodworking projects. For instance, low-friction coatings have become increasingly popular among woodworkers. These coatings are typically made from materials like polytetrafluoroethylene (PTFE) or nylon and are applied onto tool surfaces or workpieces to create a protective barrier against excessive friction.
Woodworking professionals now have access to an array of products specifically engineered for reducing friction levels. Non-stick glides are one example of such products; they can be attached to machinery parts or jigs, allowing smoother movement and reducing friction. Teflon-based coatings are another modern solution that can be applied onto tool surfaces to minimize friction levels. Furthermore, self-lubricating materials have been developed to provide a built-in lubricating effect.
By understanding the impact of friction in woodworking processes and having knowledge of both traditional and modern solutions for friction reduction, woodworkers can make more informed decisions. Whether it’s utilizing traditional techniques like waxing and oiling, or embracing innovative tools and products, woodworkers can effectively reduce friction to enhance their woodworking experience and achieve higher quality results.
Common Challenges Faced by Woodworkers Due to Friction
Woodworking is a craft that requires precision, accuracy, and attention to detail. However, friction can often pose significant challenges for woodworkers, affecting the quality of their work and overall efficiency. In this section, we will explore some common challenges faced by woodworkers due to friction and how it impacts their craftsmanship.
Precision
Friction can have a detrimental impact on the precision of woodworking projects. As wood slides against tools or other surfaces, the resistance caused by friction can lead to inaccuracies in measurements and cuts. This can result in misaligned joints, uneven surfaces, or improperly fitted parts. The lack of precision not only affects the aesthetic appeal of the final product but also compromises its functionality and structural integrity.
Efficiency
Friction also affects the efficiency of woodworking processes. When working with high-friction surfaces or materials, woodworkers may have to exert more force or effort when using tools such as saws, planes, or sanders. This not only slows down their workflow but also increases physical fatigue and the risk of injury. Additionally, excessive friction can cause tools to heat up quickly and potentially damage both the tool and the workpiece.
Safety
Friction poses safety risks for woodworkers as well. When surfaces are not adequately lubricated or treated to reduce friction, there is an increased likelihood of kickbacks from power tools such as table saws or routers. Kickbacks occur when a workpiece is forcefully thrown back towards the operator due to sudden release of built-up tension caused by frictional forces. These incidents can result in serious injuries if proper safety precautions are not followed.
It is crucial for woodworkers to understand these common challenges associated with friction in order to effectively address them and achieve optimal results in their projects. In the next section, we will delve into traditional solutions that woodworkers have used throughout history to reduce friction and improve their craftsmanship.
Traditional Solutions for Reducing Friction
Woodworkers have been dealing with friction in their craft for centuries, and over time, they have developed various traditional solutions to reduce it. These age-old methods not only help in achieving smoother wood surfaces but also contribute to the overall quality and durability of the final product.
Waxing
One of the most common techniques used by woodworkers to reduce friction is waxing. By applying wax onto wooden surfaces, they create a thin protective layer that minimizes resistance during movement and contact. Beeswax has been a popular choice due to its natural properties and easy availability.
Woodworkers typically rub a block of beeswax onto their tools or furniture pieces, ensuring even coverage on all exposed wooden areas. The heat generated from the friction between the wood and the block melts the wax, allowing it to seep into the pores of the wood, forming a smooth surface. In addition to decreasing friction, waxing also serves as a protective barrier against moisture and contaminants.
Oiling
Another traditional method employed by woodworkers is oiling. Various oils can be used for this purpose, such as linseed oil, tung oil, or mineral oil. Oiling helps hydrate and lubricate the wooden surface, reducing friction between moving parts or when working with hand tools. Woodworkers often use oils on cutting boards, workbenches, or any wooden components that require frequent handling or movement. Oils penetrate deep into the wood fibers, enhancing their natural beauty while also providing protection against moisture damage.
Polishing
Achieving a polished finish not only adds aesthetic appeal but also contributes to reducing friction in woodworking projects. Woodworkers employ various methods of polishing based on their desired outcome and individual preferences. Sandpaper with progressively finer grits is commonly used for initial sanding and leveling rough surfaces before polishing begins.
Natural abrasive compounds such as pumice or rottenstone, along with oil or water, are used to create a slurry that polishes the wood surface. Additionally, polishing compounds like Tripoli or jewelers’ rouge can be utilized to buff and bring out the natural luster of the wood. Polishing not only reduces friction but also enhances the overall appearance of the final woodworking project.
While traditional methods are effective in reducing friction in woodworking, advancements in technology have introduced modern tools and techniques that further enhance this aspect. These will be explored in subsequent sections of this blog post.
Modern Tools and Techniques for Friction Reduction
Friction is a common challenge faced by woodworkers that can affect the quality, precision, and efficiency of their projects. Fortunately, advancements in woodworking technology have introduced modern tools and techniques specifically designed to reduce friction and enhance the woodworking experience.
One tool that has gained popularity among woodworkers is low-friction coatings. These coatings are applied to woodworking tools such as saw blades, drill bits, and router bits to minimize friction and promote smoother cutting. Low-friction coatings typically consist of a thin layer of specialized materials such as PTFE (polytetrafluoroethylene) or DLC (diamond-like carbon), which reduce surface-to-surface contact with the wood and prevent heat buildup during operation.
In addition to low-friction coatings, woodworkers also utilize lubricants for friction reduction. Lubricants like silicone spray or dry lubricants are applied to the workpiece or tools to create a slippery barrier between surfaces, minimizing friction and allowing for easier movement or manipulation. These lubricants not only reduce friction but also help in preventing binding or sticking of moving parts in cutting or shaping processes.
Another modern technique for reducing friction in woodworking is the use of ball bearing guides or linear motion systems. These mechanical systems provide smooth movement along a predetermined path, eliminating any unnecessary resistance caused by friction. For example, when using a sliding table saw with ball bearing guides, there is less opportunity for the workpiece to stick or bind against the table surface due to minimized friction.
Woodworking has always required precision and attention to detail, and reducing friction plays a significant role in achieving those standards. With the advent of modern tools and techniques focused on friction reduction, woodworkers now have more options at their disposal to enhance their projects’ quality and efficiency.
Examples of Modern Tools for Friction Reduction
- Low-friction coatings
- Lubricants (e.g., silicone spray, dry lubricants)
- Ball bearing guides
- Linear motion systems
By incorporating these modern tools and techniques into their woodworking practices, woodworkers can significantly improve the overall experience, making their projects smoother, more precise, and safer.
The Popular Use of Beeswax in Friction Reduction
Beeswax is a popular and eco-friendly solution used by woodworkers to reduce friction in woodworking projects. Known for its natural properties, beeswax has been utilized for centuries as a lubricant and protective coating for various materials, including wood.
One of the key reasons why beeswax is favored is its ability to provide a smooth and slippery surface on wood, resulting in reduced friction. The high melting point of beeswax allows it to form a thin layer that can resist heat generated during woodworking processes, further enhancing its effectiveness in reducing friction.
To apply beeswax for friction reduction, woodworkers typically rub or melt the wax onto the wood surface. This creates a protective barrier that not only minimizes friction but also adds a level of moisture resistance to the wood. By preventing excess moisture from being absorbed into the wood fibers, beeswax can help maintain the dimensional stability of the wood and prevent warping or cracking over time.
In addition to reducing friction, beeswax also enhances the appearance of woodworking projects by adding a subtle shine and richness to the wood’s natural color. Unlike some synthetic coatings or lubricants, beeswax does not leave behind a sticky residue or emit harmful chemicals into the environment.
Overall, the use of beeswax as a natural and eco-friendly solution for friction reduction in woodworking showcases how traditional techniques continue to hold value in modern practices. Woodworkers can rely on this tried-and-true method to achieve smoother surfaces, increase precision in their work, improve efficiency, and enhance safety throughout their projects.
The Role of Sanding and Smoothing in Friction Reduction
Sanding and smoothing play a crucial role in reducing friction in woodworking projects. When woodworkers aim to achieve smooth surfaces on their creations, they are simultaneously working towards minimizing friction. By understanding the significance of proper sanding techniques, woodworkers can effectively reduce friction and enhance the overall quality of their work.
One of the key benefits of sanding is that it helps create an even surface by removing imperfections such as rough spots, splinters, or uneven edges. These irregularities can cause increased friction when two pieces of wood rub against each other. Sanding smooths these surfaces, making the contact between the wood pieces much smoother and reducing friction.
There are different methods and tools used by woodworkers to achieve optimal sanding results. One common technique is hand sanding using sandpaper sheets or blocks. This method allows for precise control over the amount of pressure applied to different areas, ensuring a consistent level of smoothness throughout the project. Electric sanders, such as palm sanders or belt sanders, provide efficiency and speed when working on larger surfaces or bulkier materials.
To further enhance the reduction of friction through sanding, woodworkers may utilize various grits of sandpaper depending on their specific needs. Coarse-grit papers (around 40-60 grit) are typically used for initial material removal or leveling uneven surfaces. As the process continues, finer-grit papers (around 120-220 grit) help achieve a smoother finish by progressively removing smaller imperfections left behind by coarser sands.
By incorporating proper sanding techniques into their woodworking practices, craftsmen not only improve the aesthetic appeal of their projects but also ensure reduced friction for better functionality and longevity of wooden pieces. Sanding should be considered an integral part of any woodworking process aiming to achieve low-friction surfaces that will enhance both user experience and product lifespan.
- Hand sanding using sandpaper sheets or blocks
- Electric sanders like palm sanders or belt sanders
- Using different grits of sandpaper (coarse to fine)
Specialized Products for Friction Reduction in Woodworking
Woodworkers are constantly seeking ways to minimize friction in their projects, and there are several specialized products designed specifically for this purpose. These innovative solutions offer effective friction reduction, allowing woodworkers to achieve better results in terms of precision, efficiency, and safety.
One popular option among woodworkers is the use of non-stick glides. These glides are typically applied to tools and equipment such as saw blades, router bits, and planer blades. The non-stick coating reduces friction between the tool and the wood surface, resulting in smoother cuts and less heat generated during the woodworking process. This not only improves the quality of the final product but also prolongs the lifespan of the tools by reducing wear and tear.
Another common product used for friction reduction is Teflon-based coatings. Teflon is known for its low coefficient of friction, making it an ideal choice for woodworkers looking to minimize resistance during their work. Teflon coatings can be applied to various surfaces, including jigs, guides, and fences, allowing wood to slide smoothly across these surfaces without sticking or catching. This ensures that woodworkers can work with greater ease and accuracy.
In addition to non-stick glides and Teflon coatings, there are also self-lubricating materials available for reducing friction in woodworking projects. These materials have built-in lubrication properties that eliminate the need for applying additional lubricants or oils. Self-lubricating materials can be used as bearings or bushings in machines or as components in sliding mechanisms like drawer slides. They provide a smooth motion and reduce wear on moving parts, improving both performance and longevity.
These specialized products offer a range of options for woodworkers looking to minimize friction in their projects. By incorporating non-stick glides, Teflon-based coatings, or self-lubricating materials into their woodworking processes, they can enhance their overall experience while achieving better results. It is important for woodworkers to explore and experiment with these products to find the ones that work best for their specific needs and preferences, ultimately enhancing their woodworking craft.
Best Practices and Tips for Achieving Optimal Friction Reduction
Woodworking requires a significant amount of skill and attention to detail, and one important aspect that woodworkers need to consider is friction reduction. Minimizing friction can improve the efficiency, safety, and overall quality of woodworking projects. In this section, we will explore some best practices and tips for achieving optimal friction reduction in woodworking.
One essential practice is proper tool maintenance and sharpening. Dull tools create more friction as they interact with the wood, leading to less precise cuts and an increased risk of accidents. Regularly sharpening blades and maintaining tools in good condition not only reduces friction but also enhances the overall woodworking experience.
Another important tip is using the right lubricants or coatings to minimize friction between wood surfaces and moving parts. For example, applying beeswax onto machine surfaces or drawer slides can significantly reduce the resistance encountered during operation. Beeswax has natural low-friction properties and is environmentally friendly compared to synthetic alternatives.
Additionally, temperature control and humidity management play a vital role in achieving optimal friction reduction in woodworking. Wood expands when exposed to heat or moisture, which can increase friction between components. Controlling the environment by ensuring a stable temperature and humidity level helps to minimize unwanted expansion or contraction of wood, thus reducing friction.
Overall, achieving optimal friction reduction in woodworking requires attention to detail, proper tool maintenance, the use of lubricants or coatings, and controlling environmental factors like temperature and humidity. By incorporating these best practices into their woodworking routine, craftsmen can enjoy improved efficiency, safety, and a higher quality finished product.
Best Practices for Achieving Optimal Friction Reduction | Tips for Implementing Friction Reduction Techniques |
---|---|
Proper tool maintenance | Regularly sharpen blades for clean cuts – Use lubricants specific to woodworking tools |
Utilize appropriate lubricants or coatings | Apply beeswax to machine surfaces and drawer slides – Consider natural and environmentally friendly options |
Control temperature and humidity levels | Maintain a stable environment – Minimize wood expansion/contraction due to heat or moisture |
Conclusion
In conclusion, it is evident that friction reduction plays a critical role in woodworking. The quality of the final product heavily relies on minimizing friction during the various woodworking processes. Throughout this blog post, we have explored different methods, tools, and techniques that woodworkers use to achieve smoother wood surfaces and enhance their overall woodworking experience.
From traditional solutions such as waxing, oiling, and polishing to modern advancements in woodworking technology like low-friction coatings and lubricants, there are numerous options available for woodworkers to reduce friction. We have also delved into the popular use of beeswax as a natural and eco-friendly solution for friction reduction in woodworking projects.
Moreover, proper sanding techniques have been highlighted as a significant factor in achieving optimal friction reduction. Woodworkers should pay attention to using the right sanding methods and tools to attain smoother wood surfaces.
Lastly, specialized products designed explicitly for reducing friction in woodworking were showcased. These innovative solutions include non-stick glides, Teflon-based coatings, and self-lubricating materials.
By empowering woodworkers with knowledge about friction reduction techniques and practices discussed throughout this blog post, they are encouraged to experiment and incorporate these methods into their woodworking projects. With a deeper understanding of how to minimize friction effectively, woodworkers can enhance precision, efficiency, and safety while achieving higher-quality results.
Frequently Asked Questions
What wax reduces friction on wood?
One commonly used wax to reduce friction on wood is a lubricating wax. This type of wax contains ingredients that help to minimize the friction between the wood and other surfaces.
It is typically applied as a thin layer onto the wood, forming a protective barrier that allows for smoother movement without causing damage or wear to the wood surface. Lubricating waxes are often utilized in various woodworking applications, such as on plane soles, saw blades, or any other areas where reduced friction is desired.
How do you reduce friction between two pieces of wood?
There are several methods to reduce friction between two pieces of wood. One approach is to apply a lubricant between the surfaces of the wood. This could be done using different substances like beeswax, paraffin wax, or even specialized lubricants designed specifically for woodworking purposes.
By introducing these lubricants at the contact points of the woods, they create a slippery layer that effectively reduces friction upon movement. Another option is to incorporate components such as ball bearings or sliding mechanisms into the wooden structure itself, which can offer smooth motion and prevent direct contact between the wooden surfaces.
How do you reduce friction on wood drawers?
To reduce friction on wood drawers, there are a few measures that can be taken. One common method is utilizing drawer slides or runners made from low-friction materials such as nylon or Teflon. These materials have excellent self-lubrication properties and allow for easy sliding of the drawer without causing excessive friction or wear on its tracks.
Additionally, applying a thin layer of wax on the wooden drawer edges and runners can further aid in reducing friction by providing a smooth surface for gliding. Regular maintenance and cleaning of both the drawers and their corresponding tracks also contribute to minimizing friction over time, ensuring continued ease of use for the drawers while keeping them in good condition.
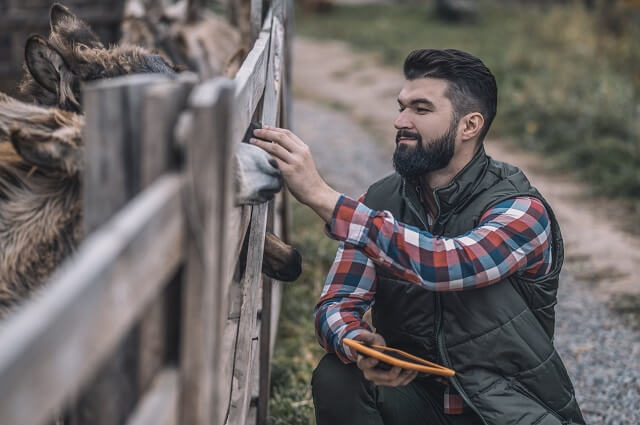
Hi everyone! I’m a woodworker and blogger, and this is my woodworking blog. In my blog, I share tips and tricks for woodworkers of all skill levels, as well as project ideas that you can try yourself.