Woodworking patterns serve as the backbone of successful woodworking projects, providing a blueprint for precision and accuracy. In this article, we will explore the basics of woodworking patterns and their significance in creating beautiful and functional pieces. We will discuss the tools and materials required for creating woodworking patterns, as well as the process of choosing the right design for your project.
Additionally, we will provide step-by-step instructions for planning, sketching, transferring, cutting, shaping, refining, and completing your woodworking project based on the pattern. Throughout this journey, we will emphasize the importance of patience and practice in mastering woodworking patterns. So let’s dive in and discover how to make woodworking patterns that will elevate your craftsmanship to new levels.
Woodworking patterns are vital in ensuring precise and accurate results in any woodworking venture. They act as a guide for determining dimensions, measurements, and cuts necessary to bring a design to life. By following a carefully crafted pattern, woodworkers can save valuable time, effort, and materials by avoiding mistakes or inaccuracies that could result in costly errors. Whether you are a beginner or an experienced woodworker looking to enhance your skills, understanding how to create effective woodworking patterns is essential.
In this comprehensive guide on how to make woodworking patterns, we will cover everything you need to know about this critical aspect of woodworking projects. From the basic definition of what constitutes a woodworking pattern to understanding its role as a blueprint for success, we’ll delve into each step involved in creating precision designs.
By following these steps diligently and applying best practices along the way, you’ll gain confidence in crafting beautiful wooden pieces that meet your desired specifications.
Throughout this article series dedicated to making woodworking patterns accessible to all skill levels, we’ll share expert insights on selecting suitable designs for your projects, exploring various tools needed for pattern creation or transferal onto workpieces effectively. Additionally discussing techniques essential for cutting or shaping based on established patterns while maintaining safety standards. Alongside this, we will provide guidance on refinements, such as sanding or detailing wood to match specific pattern specifications.
Lastly, we’ll address the importance of patience and practice, highlighting the rewarding benefits of mastering woodworking patterns while encouraging readers to showcase their craftsmanship and share their journey with others. So whether you’re just starting out or looking to refine your woodworking skills, let’s begin this woodworking pattern-making adventure together.
Understanding the Basics of Woodworking Patterns
Woodworking patterns are an essential tool for any woodworking project, as they provide the necessary blueprint for precision and accuracy. Without a pattern, it can be difficult to achieve the desired outcome and measurements in a woodworking project. In this section, we will define woodworking patterns and explore their significance in woodworking.
Defining Woodworking Patterns
Woodworking patterns are templates or guides that outline the dimensions and shapes needed to create a specific piece of woodwork. These patterns serve as a reference point for accurate cutting, shaping, and assembling of the wood. They can range from basic shapes to intricate designs, depending on the complexity of the project.
The purpose of a woodworking pattern is to assist woodworkers in achieving consistency and precision in their work. By following a pattern, woodworkers can ensure that each component fits together seamlessly and that the overall design is executed with accuracy.
The Significance of Woodworking Patterns
Woodworking patterns play a crucial role in saving time, effort, and materials during a woodworking project. By having a clear plan and guidelines through a pattern, woodworkers can minimize errors such as misalignment or incorrect measurements. This not only reduces wasted materials but also prevents unnecessary rework or adjustments.
Using woodworking patterns also allows woodworkers to replicate successful projects or designs. Once a pattern has been created for a specific piece, it can easily be used multiple times to recreate identical or similar pieces with consistency. This becomes particularly useful for those who engage in production woodworking or make custom orders.
Furthermore, woodworking patterns enable woodworkers to customize their projects based on their preferences or client requirements. By having a clear visual representation of the final product through the pattern, they can make necessary modifications or additions before starting the construction process.
In summary, understanding and utilizing woodworking patterns are vital skills for any woodworker aiming to create quality projects with precision and accuracy. These patterns not only serve as blueprints for construction but also save time, effort, and materials while providing the opportunity for customization.
Tools and Materials Required for Creating Woodworking Patterns
When it comes to creating woodworking patterns, having the right tools and materials is essential. These tools not only help you accurately translate your design onto paper but also ensure precision when transferring the pattern onto your workpiece. Here are the necessary tools and materials you’ll need for creating woodworking patterns.
Firstly, you’ll need some basic drafting tools like a drafting compass, rulers, and pencils. These tools will allow you to measure and draw precise lines, angles, and curves on your drafting paper or template material. A good quality compass is especially important for drawing circles or arcs of various sizes.
In terms of materials for pattern templates, plywood or cardboard are readily available options. Plywood is durable and can be easily cut into specific shapes using a jigsaw or scroll saw if needed. On the other hand, cardboard is more affordable and offers flexibility for creating intricate patterns.
For those who prefer digital pattern creation, there are optional tools and software available. Computer-aided design (CAD) software allows you to create complex woodworking patterns digitally. This can be useful if you plan on replicating your designs multiple times or if you want to experiment with different variations before finalizing your pattern.
Having the right tools and materials not only makes the process of creating woodworking patterns easier but also ensures accuracy in translating the design onto the workpiece. By investing in these basic items, you’ll set yourself up for success in woodworking projects.
Choosing the Right Design for Your Woodworking Project
When embarking on a woodworking project, one of the crucial steps is selecting the right design for your woodworking pattern. The design serves as the foundation and guide for your entire project, so it’s important to consider several factors before making your final decision.
Firstly, it is important to assess the complexity of the design and ensure that it aligns with your skill level. If you are a beginner or have limited experience in woodworking, opting for a simpler design can help build confidence and prevent frustration. On the other hand, if you are more experienced and looking for a challenge, a complex design can provide an opportunity to test your skills and push boundaries.
Another factor to consider is functionality. What will be the purpose of your woodworking project? Is it meant to be purely decorative or does it need to serve a practical function? Understanding the intended use of the finished piece will inform your choice of design, as certain styles may be better suited for specific purposes.
In addition to complexity and functionality, finding inspiration from various sources can help expand your creativity and refine your personal style. Magazines dedicated to woodworking often feature a wide range of designs that cater to different tastes and preferences. Online platforms such as Pinterest or woodworking forums are also excellent resources for discovering unique designs shared by fellow woodworkers. Finally, don’t hesitate to let your own imagination do the work – sometimes the best designs come from within.
By carefully considering these factors – complexity, skill level, functionality, and inspiration – you can confidently select a design that not only complements your skills but also brings your vision to life.
Factors to Consider when Choosing a Design
Factor | Description |
---|---|
Complexity | Assessing the level of complexity and ensuring it aligns with your skills |
Functionality | Determining if the design meets the intended use of the finished piece |
Inspiration | Finding ideas from magazines, online platforms, or one’s own creativity |
Planning and Sketching the Woodworking Pattern
When it comes to creating woodworking patterns, proper planning and sketching are essential steps in the process. This section will guide you through the necessary steps to effectively plan and sketch your woodworking pattern.
Step 1: Planning the Dimensions and Measurements
Before you start sketching your woodworking pattern, it’s important to plan out the dimensions and measurements of your project. Consider the size of the final piece, as well as any specific measurements required for different components or joints. Using a measuring tape or ruler, accurately measure all relevant dimensions and jot them down for reference.
Step 2: Translating Your Design Sketch into a Comprehensive Woodworking Pattern
Once you have a clear idea of the dimensions, it’s time to translate your design sketch into a comprehensive woodworking pattern. Start by drawing a rough outline of your project on drafting paper. Use straightedges or rulers to ensure precision in your lines.
Next, add in all necessary details such as joints, curves, and angles. Take your time in this step to ensure accuracy in translating your design onto paper. If there are any complex sections in your design, consider breaking them down into smaller parts for easier visualization.
Step 3: Utilizing Scaling Techniques and Measuring Tools
To ensure that your woodworking pattern accurately represents the size and proportions of your desired project, it’s important to utilize scaling techniques and measuring tools. One common technique is using a scaling factor where each inch on paper represents a certain measurement on the actual project.
Consider using a drafting compass to draw circles or curves with precision. Rulers with detailed markings can help you measure distances accurately while drafting pencils are recommended for their fine lines that allow for better resolution when transferring patterns onto workpieces.
Remember to double-check all measurements before moving forward with your woodworking pattern to avoid errors that may lead to misaligned pieces or ill-fitting joints.
By following these steps for planning and sketching your woodworking pattern, you can lay a solid foundation for the success of your project. Stay patient and take your time in this phase, as it will greatly impact the accuracy and quality of your final piece.
Transferring the Woodworking Pattern onto Your Workpiece
Once you have created your woodworking pattern, the next step is to transfer it onto your chosen workpiece. This is a crucial step in ensuring accuracy and precision in your woodworking project. There are several techniques that you can use to transfer the pattern onto the wood, depending on your preference and the tools available to you.
One common method for transferring woodworking patterns is by using carbon paper. Start by placing the carbon paper, dark side down, on top of your workpiece. Then, place the woodworking pattern on top of the carbon paper, making sure it is aligned correctly. Using a pencil or a stylus, trace over the lines of the pattern with firm pressure. The carbon paper will leave an impression on the wood, allowing you to accurately recreate the design.
Another option is to use transfer paper. This method involves placing a sheet of transfer paper between your woodworking pattern and workpiece. With a pencil or stylus, trace over the lines of the pattern with consistent pressure. The pressure will cause the transfer paper to leave marks on both the wood and pattern template.
If you don’t have access to carbon or transfer paper, you can also use tracing methods. Simply place your woodworking pattern on top of your workpiece and secure it in place using tape or clamps. With a pencil or pen, carefully trace over all lines of the pattern, applying enough pressure so that it transfers onto the wood surface.
Regardless of which method you choose, it’s important to align and secure your woodworking pattern properly before transferring it onto the workpiece. Any misalignment at this stage can result in inaccurate cuts or shapes later on in your project.
Cutting and Shaping Wood Based on the Woodworking Pattern
Once you have created a woodworking pattern, the next step is to cut and shape the wood based on the pattern. This crucial phase ensures that your project takes its desired form and brings your design to life. In this section, we will provide step-by-step instructions on cutting and shaping techniques based on the woodworking pattern.
To begin, gather the necessary tools for cutting and shaping wood, such as saws, chisels, routers, and jigsaws. Each tool serves a specific purpose in achieving different cuts and shapes. For example, a saw is ideal for straight cuts, while a router can create intricate designs and contours. It’s important to select the right tool for each task to achieve the desired results.
Before starting, it is essential to prioritize safety by wearing appropriate protective gear such as goggles or safety glasses, gloves, and a dust mask. Familiarize yourself with each tool’s operation manual and follow all safety precautions.
Once you have selected the appropriate tool for each cutting or shaping task based on your woodworking pattern, carefully approach the woodwork. Follow your pattern as closely as possible while making precise cuts or creating intricate shapes. Take your time to ensure accuracy and avoid rushing through the process.
Throughout this stage, it is beneficial to periodically check your progress against the woodworking pattern to ensure you are staying true to its specifications. Remember that mistakes can happen; however, they can often be rectified during subsequent refinements or adjustments.
By effectively cutting and shaping wood based on your woodworking pattern, you are using your skills and techniques to bring your design vision into reality. With patience and precision, take pride in each step of this process as it contributes significantly to the final outcome of your woodworking project.
Refining and Fine-tuning the Woodworking Pattern
Once you have created your woodworking pattern, it is important to refine and fine-tune it during the project to ensure the best possible outcome. This section will provide strategies and techniques for refining and adjusting your woodworking pattern as needed.
One common issue that may arise is misalignment or inaccurate measurements in your woodworking pattern. To troubleshoot this problem, double-check all measurements and dimensions against your design sketch. Use measuring tools such as a tape measure or calipers to verify accuracy. If you discover any discrepancies, make appropriate adjustments on your pattern before proceeding.
In addition to measurements, ensure that the various parts of your woodworking project align properly with the pattern. Use a straightedge or a level to check for alignment along edges or joints. If there are any misalignments, adjust your pattern accordingly by redrawing or modifying specific sections.
Sanding, shaping, and detailing the wood are also crucial steps in fine-tuning the woodworking pattern. After cutting and shaping the wood based on your pattern, use sandpaper or sanding blocks to smooth out any rough edges or surfaces. Pay attention to areas where two pieces of wood join together; these should be sanded flush for a seamless finish. In addition, use carving tools or chisels to add intricate details if desired.
Remember that refining and fine-tuning are ongoing processes throughout the woodworking project. As you progress with construction, reassess your pattern periodically to make sure it aligns with the workpiece seamlessly and accurately.
By taking the time to refine and fine-tune your woodworking pattern, you set yourself up for success in creating a high-quality finished project that meets your expectations. A well-refined pattern ensures precision in cutting, shaping, and assembling wood pieces according to plan.
In conclusion (excluding HTML):
- Double-check all measurements and dimensions against design sketch.
- Verify alignment of parts using straightedge or level.
- Use sandpaper, sanding blocks, carving tools, and chisels to refine the wood.
Remember that patience and practice are key in mastering woodworking patterns. The more you work with patterns and refine your skills, the better you will become at creating precise and accurate woodworking projects. Don’t be discouraged by mistakes or setbacks along the way – they are valuable learning experiences that will ultimately contribute to your growth as a woodworker.
Embrace experimentation and enjoy the creative process of woodworking patterns. By sharing your journey with others, you can inspire and be inspired by fellow woodworking enthusiasts.
Finishing and Completing the Woodworking Project
Finishing and completing a woodworking project is the final step in creating a beautiful and functional piece. This section will provide ideas, tips, and steps to ensure that your project is finished with care and attention to detail.
Ideas for Applying Finishes
One of the most important aspects of finishing a woodworking project is applying the right finishes to enhance its appearance and protect the wood. Here are some ideas for applying finishes:
- Stains: Choose a stain color that complements the wood species and desired aesthetic. Apply the stain evenly using a brush or cloth, following the manufacturer’s instructions.
- Varnishes: Apply varnish coats to protect the wood from moisture, scratches, and UV rays. Opt for a gloss, semi-gloss, or satin finish depending on your preference.
- Paints: If you prefer a painted finish, select high-quality wood paint suitable for your project. Sand and prime the surface before applying several coats of paint.
- Oil Finishes: Natural oil finishes provide a warm and rich look to wooden surfaces. Apply linseed oil or tung oil using a clean cloth, following the manufacturer’s guidelines.
Tips for Assembly and Joinery
Proper assembly and joinery techniques are vital to ensure that your woodworking project is sturdy and durable. Consider these tips:
- Choose appropriate joinery methods based on your project design, such as butt joints, mortise and tenon joints, dovetail joints, or pocket hole joinery.
- Pre-drill holes before driving screws or nails to prevent splitting or cracking of wood components.
- Apply glue generously between mating surfaces for added strength in joint connections.
- Clamp assembled pieces securely until the glue dries completely.
- Sand any visible joinery edges to ensure a seamless and professional finish.
Final Steps for Sanding, Polishing, and Inspection
After assembly and applying finishes, it’s important to pay attention to the final details of your woodworking project. Follow these steps for a polished final result:
- Sanding: Use progressively finer grit sandpaper to smooth any rough surfaces or imperfections. Sand in the direction of the wood grain to avoid scratches.
- Polishing: Apply wax or polish with a clean cloth to add a lustrous shine to your project.
- Inspection: Carefully inspect the completed project for quality assurance. Check for any loose joints, rough spots, or inconsistencies in the finish. Make any necessary touch-ups or adjustments before declaring your project complete.
By following these finishing steps with care and attention, you can elevate the overall look of your woodworking project and create a piece that will be admired for years to come. Remember that practice makes perfect, so don’t be discouraged if your first attempt doesn’t turn out as expected. With patience and persistence, you can refine your skills in woodworking patterns and create truly remarkable projects.
Conclusion
In conclusion, mastering the art of creating woodworking patterns requires a combination of patience and practice. Throughout this article, we have explored the significance of woodworking patterns in successful projects and discussed the step-by-step process of creating and implementing these patterns.
By understanding the basics, acquiring the necessary tools and materials, choosing the right design, planning and sketching the pattern, transferring it onto the workpiece, cutting and shaping wood based on the pattern, refining it as needed, and finally completing the project, one can create impressive woodworking pieces.
It is important to emphasize the role of patience in this craft. Woodworking patterns require precision and accuracy, which can be achieved through careful planning and execution. Rushing through any step can lead to mistakes or inaccuracies that may affect the final outcome. Therefore, taking one’s time throughout each stage of creating a woodworking pattern is crucial for achieving desired results.
Additionally, practice plays a significant role in mastering woodworking patterns. Each project presents an opportunity to learn and improve upon previous techniques. Woodworking often involves trial-and-error processes; mistakes will happen along the way. It is through these mistakes that valuable lessons are learned, leading to growth as a woodworker.
Lastly, it is important to share your journey with others. Woodworking is not just about creating beautiful pieces but also about being part of a community where knowledge is shared and inspiration thrives. By showcasing finished projects and sharing experiences with fellow woodworkers, you contribute towards fostering creativity and innovation within this craft.
In summary, by embracing patience, practicing consistently, and sharing your progress with others, you can excel in creating impressive woodworking patterns. Don’t be afraid to experiment or make mistakes along the way – these experiences will only enhance your skills. So go forth with confidence into the world of woodworking patterns, and let your creativity shine through in every piece you create.
Frequently Asked Questions
What is the best material to make woodworking templates?
The best material to make woodworking templates is typically a strong and durable material that can withstand repeated use. Many woodworkers prefer to use medium-density fiberboard (MDF) for making templates. MDF is smooth, dense, and stable, allowing for precise measurements and cuts.
It also doesn’t expand or contract with changes in humidity, ensuring accuracy over time. Other suitable materials for templates include plywood, acrylic sheets, or even high-quality cardboard if the template is not expected to be used extensively.
What can I make woodworking templates out of?
Woodworking templates can be made out of various materials depending on their purpose and durability requirements. In addition to MDF, plywood is commonly used as it provides stability and can withstand moderate usage.
Acrylic sheets are another option as they offer the advantage of being transparent, allowing for better visibility during the layout process. Metal can also be utilized in some cases for more heavy-duty applications where long-lasting durability is necessary, though it may require specialized tools and techniques.
How do you make a woodwork template?
Making a woodworking template involves several steps to ensure accuracy and precision. First, you need to determine the exact dimensions and shape desired for your template.
This can be done by sketching it out on paper or using computer-aided design (CAD) software if you prefer a digital approach. Once you have the design finalized, transfer it onto your chosen material using a pencil or marker.
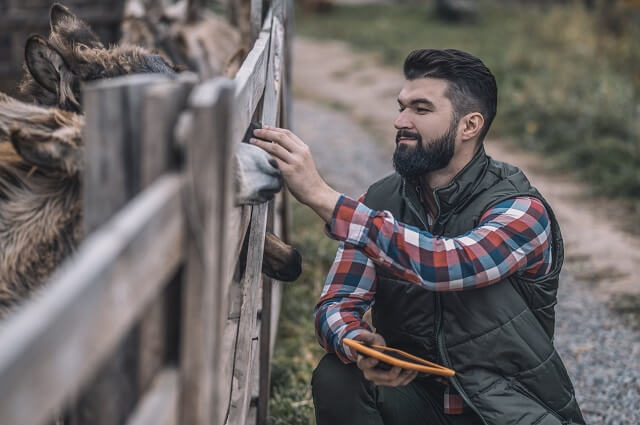
Hi everyone! I’m a woodworker and blogger, and this is my woodworking blog. In my blog, I share tips and tricks for woodworkers of all skill levels, as well as project ideas that you can try yourself.