How much does it cost to start a woodworking business? Starting a woodworking business requires careful consideration of the initial investment needed to establish a successful venture.
From creating a comprehensive business plan to budgeting for equipment, workshop space, materials, and marketing expenses, understanding the costs involved is crucial in ensuring a profitable and sustainable woodworking business. In this article, we will explore the key components and financial considerations of starting a woodworking business, providing valuable insights into the initial investment required for aspiring entrepreneurs in the woodworking industry.
When embarking on the journey of starting a woodworking business, it is essential to create a detailed business plan that outlines all the necessary components and associated costs. This includes evaluating the expenses for equipment and tools, workshop space, material sourcing, marketing and branding, as well as identifying any unforeseen expenses that may arise during the startup phase.
By gaining an understanding of these financial requirements upfront, individuals can effectively plan and budget for the initial investment needed to launch their woodworking business successfully.
In addition to outlining the fundamental costs involved in setting up a woodworking business, we will also delve into budgeting and financial considerations. Managing startup costs effectively is paramount in ensuring long-term success, and our article will provide valuable tips for entrepreneurs on how to budget strategically and make informed financial decisions when starting a woodworking business.
Whether you are an experienced woodworker looking to transition into entrepreneurship or someone passionate about woodworking with dreams of starting your own business, understanding the initial investment required is key to realizing your aspirations in the woodworking industry.
Creating a Business Plan
When starting a woodworking business, it is essential to create a comprehensive business plan that outlines all the key components and costs involved. This will serve as a roadmap for the venture and provide a clear understanding of the financial requirements. Here are some key components and costs to consider when developing a business plan for your woodworking business:
- Equipment and tools: One of the primary expenses when setting up a woodworking business is the cost of purchasing essential equipment and tools. This can include table saws, power drills, sanders, clamps, routers, and other woodworking machinery.
- Workshop space: Whether you choose to rent or purchase a workshop space, this will be a significant cost to factor into your business plan. Consider the size of the space needed, location, and any necessary renovations or modifications.
- Material costs: Wood and other materials for your projects will also contribute to the startup costs. Researching suppliers and estimating the ongoing material expenses is crucial for an accurate business plan.
In addition to these major expenses, it’s important to also consider marketing and branding expenses in your business plan. Allocating funds for advertising, website development, logo creation, and other promotional activities will help establish a strong brand presence in the market.
Lastly, identifying additional costs such as permits, licenses, insurance, and professional fees is essential for a complete overview of the startup investment required. These extra expenses may vary based on local regulations and should not be overlooked when creating your woodworking business plan.
By thoroughly identifying all components and costs involved in setting up a woodworking business in your business plan, you will have a clearer understanding of how much does it cost to start a woodworking business. This comprehensive approach will help you effectively manage your budget and financial considerations for a successful launch of your venture.
Costs of Equipment and Tools
When starting a woodworking business, one of the most significant initial investments you will need to make is in equipment and tools. The cost of these essentials can vary depending on the type of woodworking projects you plan to undertake, the scale of your business, and the quality of tools you choose to invest in. It’s important to carefully consider what tools are essential for your specific woodworking niche and budget accordingly.
One of the basic necessities for any woodworking business is a set of high-quality hand tools such as chisels, planes, saws, hammers, and clamps. These tools are indispensable for precision work and can range in price depending on their quality and brand. Investing in durable hand tools is crucial as they will be the backbone of your craftsmanship.
In addition to hand tools, power tools are also essential for efficiently completing woodworking projects. Items such as a table saw, miter saw, router, drill press, and sander are commonly used in woodworking shops. When considering these larger purchases, it’s important to weigh the cost against the benefits each tool will bring to your business. Quality power tools can be a significant upfront expense but are crucial for producing high-quality products efficiently.
It’s important not only to budget for purchasing equipment and tools but also to set aside funds for maintenance and potential repairs down the line. Establishing a solid foundation with reliable equipment is essential for launching a successful woodworking business. By understanding how much does it cost to start a woodworking business when it comes to equipment and tools, you can effectively plan and allocate your startup budget.
Renting or Purchasing a Workshop
When starting a woodworking business, one of the crucial decisions to make is whether to rent a workshop space or purchase one. Each option comes with its own set of pros and cons, as well as associated costs that need to be carefully considered.
Renting a workshop space offers flexibility in terms of location and size, allowing businesses to easily move or expand as needed. However, the monthly rent can add up over time and may not be a cost-effective long-term solution.
On the other hand, purchasing a workshop provides stability and the opportunity to build equity in a property. It also allows for customization and investment in a space that meets the specific needs of the woodworking business. However, the upfront costs of purchasing a workshop can be substantial, including down payments, mortgage payments, property taxes, maintenance, and potential renovation expenses.
Associated costs for renting a workshop space include monthly lease or rent payments, security deposits, utilities, insurance for rented premises, and any additional fees charged by the landlord. On the other hand, purchasing a workshop involves expenses such as down payment (if financing), mortgage payments or property taxes if paid outright, insurance for owned premises, maintenance/repairs costs, renovation expenses to customize the space if necessary.
Ultimately, whether to rent or purchase a workshop depends on various factors such as available capital, long-term business plans and goals, location preferences, and overall financial strategy. Regardless of which decision is made it’s important to carefully factor these associated costs into the overall budget when considering how much does it cost to start a woodworking business.
Material Costs
Starting a woodworking business comes with its own set of challenges and costs, particularly when it comes to sourcing wood and other materials for your projects. The cost of materials is a significant aspect that needs careful consideration in your overall business plan.
First and foremost, the type of woodworking projects you intend to take on will heavily influence the material costs. For example, if you plan on creating high-end furniture using exotic woods, your material expenses will be higher compared to crafting smaller items from more affordable wood varieties. It’s crucial to have a clear understanding of the specific materials required for your projects and their respective costs.
In addition to wood, there are other materials such as adhesives, finishes, hardware (e.g. hinges, knobs), and protective equipment that need to be factored into your budget. These items are essential for woodworking tasks and should not be overlooked when estimating your startup expenses.
To effectively manage material costs, consider establishing relationships with reliable suppliers who can offer competitive prices for bulk purchases. Additionally, exploring alternative sources such as reclaimed wood or recycled materials can help minimize expenses while adding an eco-friendly dimension to your woodworking business.
Wood Type | Cost Per Board Foot |
---|---|
Oak | $5 – $10 |
Maple | $4 – $8 |
Walnut | $7 – $13 |
Marketing and Branding Expenses
When starting a woodworking business, it’s essential to allocate funds for marketing and branding expenses in order to promote the business and establish a strong brand presence. This section will outline the key components and costs involved in marketing and branding for a woodworking business.
Digital Marketing Strategy
In today’s digital age, having a strong online presence is crucial for any business. This includes creating a professional website, setting up social media profiles, and engaging in email marketing campaigns. Budgeting for web development, social media management tools, and email marketing services is important to consider when determining the startup costs for your woodworking business.
Print Marketing Materials
Despite the prominence of digital marketing, print materials such as business cards, brochures, and flyers are still valuable tools for promoting a woodworking business. Factor in the cost of designing and printing these materials when budgeting for marketing expenses.
Branding Initiatives
Building a strong brand identity is vital for standing out in the market. Allocating funds for logo design, packaging materials, and signage will contribute to establishing a memorable brand image for your woodworking business.
Networking Events and Trade Shows
Participating in networking events and trade shows within the woodworking industry can be an effective way to promote your business. Consider budgeting for event registration fees, booth setup costs, and promotional giveaways to maximize exposure at these events.
By carefully considering these marketing and branding expenses when calculating the startup costs for your woodworking business, you can effectively allocate funds to promote your business and establish a strong brand presence in the market.
Identifying Additional Costs
When starting a woodworking business, it’s essential to consider the additional costs that may not be immediately obvious but are crucial for ensuring a smooth and legally compliant operation. These unforeseen expenses include permits, licenses, insurance, and professional fees that should be factored into the overall startup cost. Failing to account for these costs can lead to financial challenges and potential legal issues down the line.
Permits and Licenses
Depending on the location of your woodworking business, you may need to obtain various permits and licenses to operate legally. This could include a general business license, a specific woodworking or construction-related license, health permits if you plan on selling finished products, and zoning permits if you’ll be operating from a designated commercial space. The cost of these permits and licenses can vary widely based on your location and the specific requirements set by local authorities.
Insurance
Acquiring insurance is an essential part of running any business, including a woodworking venture. General liability insurance, property insurance for equipment and inventory, and workers’ compensation insurance (if hiring employees) are all important considerations. The cost of insurance will depend on factors such as coverage limits, the size of your operation, and the level of risk associated with your woodworking activities.
Professional Fees
Seeking professional assistance from lawyers, accountants, or business consultants may also incur costs that need to be included in your startup budget. Legal advice for setting up contracts or navigating regulations, accounting services for managing finances and taxes, or consulting fees for crafting a solid business strategy are all valuable investments in ensuring the long-term success of your woodworking business.
By taking into account these additional costs when calculating the total investment required to start a woodworking business, entrepreneurs can better prepare for a financially sound launch. Proper budgeting and financial planning are crucial for avoiding unexpected financial strain in the early stages of operations.
Budgeting and Financial Considerations
In conclusion, understanding the initial investment required to start a woodworking business is crucial for aspiring entrepreneurs in this field. The costs involved in setting up a woodworking business can vary widely depending on factors such as equipment and tools, workshop space, material expenses, marketing, branding, and additional unforeseen costs. Creating a detailed business plan that outlines these key components and costs is essential for effectively managing the startup costs and ensuring a successful launch of the woodworking business.
One of the major expenses that aspiring woodworking business owners need to consider is the cost of equipment and tools. From basic hand tools to power tools and machinery, investing in high-quality equipment is vital for producing exceptional wood products. Additionally, deciding whether to rent or purchase a workshop space also requires careful consideration due to its associated costs. While renting may provide flexibility, purchasing a workspace can be a long-term investment.
In addition to budgeting for equipment and workshop space, allocating funds for sourcing materials, marketing and branding efforts, as well as accounting for unforeseen expenses such as permits, licenses, insurance, and professional fees are all critical aspects of managing the startup costs effectively. By carefully considering these financial considerations and implementing sound budgeting practices, individuals looking to start a woodworking business can position themselves for success in this industry.
Therefore, aspiring entrepreneurs should conduct thorough research and seek guidance from industry professionals to gain insights on how much it truly costs to start a woodworking business and manage their finances effectively for a successful launch.
Frequently Asked Questions
Is Woodworking a Profitable Business?
Woodworking can be a profitable business for those who are skilled and passionate about creating high-quality, unique wooden products. With the right marketing, pricing, and customer base, a woodworking business can generate a steady income.
However, it is important to consider the initial investment in tools, materials, and workspace, as well as the time required to build a solid reputation and client base.
Is It Expensive to Start Woodworking?
The cost of starting a woodworking business can vary depending on the scale and scope of the operation. While it is possible to start small with basic hand tools and gradually invest in more advanced equipment as profits grow, purchasing quality machinery such as saws, planers, and sanders can be expensive.
Additionally, setting up a workshop or dedicated workspace will also incur costs. It’s important to carefully budget and make informed decisions about equipment purchases.
What Do I Need to Start a Woodworking Business?
To start a woodworking business, you will need essential tools such as saws, chisels, drills, measuring devices, and safety equipment. Access to high-quality wood materials is crucial for producing attractive products. A dedicated workspace with proper ventilation and lighting is also necessary for cutting and assembling wood safely.
In addition to physical resources, having the skills to design and create appealing wood products is essential. Finally, developing a strong online or offline presence through branding efforts and marketing strategies will help attract customers and promote your woodworking business effectively.
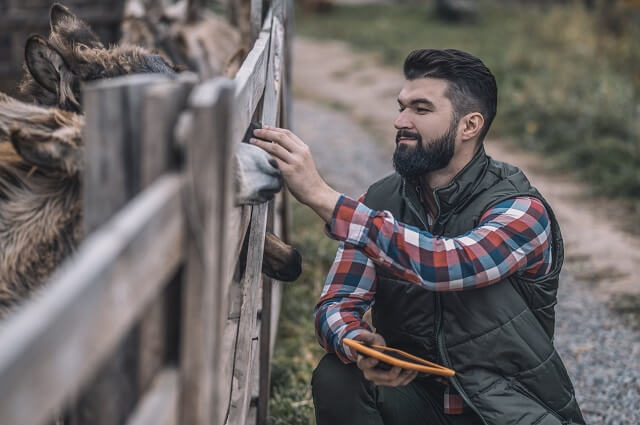
Hi everyone! I’m a woodworker and blogger, and this is my woodworking blog. In my blog, I share tips and tricks for woodworkers of all skill levels, as well as project ideas that you can try yourself.