Have you ever wondered what is HMR in woodworking? In this article, we will delve into the world of High Moisture Resistance (HMR) materials and explore its significance in the woodworking industry. HMR materials are specially designed to withstand high levels of moisture and humidity, making them ideal for various woodworking applications.
HMR materials have been a game-changer in the woodworking industry due to their unique properties and versatility. From kitchen cabinets to bathroom vanities, HMR materials are revolutionizing the way woodworkers approach projects that are exposed to moisture. Understanding the history, advantages, disadvantages, types, and applications of HMR materials is essential for any woodworker looking to expand their knowledge and skillset.
In this article, we will discuss the history of HMR in woodworking, the advantages and disadvantages of using HMR materials in projects, different types of HMR materials commonly used by woodworking professionals, as well as tips for working with HMR effectively. Whether you are a seasoned woodworker or just starting out, gaining insights into HMR can enhance your understanding of this innovative material and its future in the woodworking industry.
History of HMR in Woodworking
Woodworking has evolved over the years, and one significant development in the industry is the introduction of high moisture resistance (HMR) materials. The history of HMR in woodworking dates back to the 1980s when manufacturers began experimenting with new materials that offered improved durability and resistance to moisture. This led to the development of engineered wood products that provided a viable alternative to traditional solid wood.
The use of HMR materials in woodworking gained momentum in the 1990s as advancements in technology and manufacturing processes made these materials more accessible and affordable. Manufacturers started producing a wide range of HMR products, including plywood, particleboard, and medium-density fiberboard (MDF), which soon became popular among woodworkers for various applications.
As demand for durable and moisture-resistant materials grew, HMR became increasingly integrated into woodworking projects, especially for applications that required enhanced durability and water resistance. Today, HMR has become an essential component in modern woodworking, revolutionizing the way woodworkers approach their projects and providing solutions for challenging environmental conditions.
Year | Development |
---|---|
1980s | Experimentation with new materials for improved durability and moisture resistance |
1990s | Advancements in technology lead to mass production of HMR materials such as plywood, particleboard, and MDF |
Advantages of Using HMR in Woodworking Projects
HMR, or High Moisture Resistance, is a type of engineered wood product that is commonly used in woodworking projects. HMR is made by compressing and bonding together wood fibers using resin adhesives under high heat and pressure. This results in a strong and durable material that is highly resistant to moisture and humidity. In this section, we will discuss the advantages of using HMR in woodworking projects.
1. Moisture Resistance: One of the primary advantages of HMR in woodworking is its exceptional resistance to moisture. This makes it an ideal choice for applications in areas with high humidity or potential exposure to moisture, such as kitchens, bathrooms, and outdoor furniture.
2. Stability: HMR panels are known for their stability and ability to maintain their shape and structure even when exposed to fluctuating environmental conditions. This characteristic makes them suitable for applications where dimensional stability is crucial, such as cabinet making and furniture construction.
3. Smooth Surface Finish: HMR panels have a smooth surface finish that allows for easy painting, laminating, or veneering. Woodworkers can achieve a high-quality finish on HMR panels without the need for extensive surface preparation, saving time and effort during the woodworking process.
Overall, the use of HMR in woodworking projects offers several advantages that make it a popular choice among woodworkers for various applications requiring moisture resistance and stability.
Disadvantages of HMR in Woodworking
When it comes to working with High Moisture Resistance (HMR) materials in woodworking, there are certainly some drawbacks to consider. While HMR has many advantages, it is important to be aware of the potential disadvantages as well. Understanding these disadvantages can help woodworkers make informed decisions when selecting materials for their projects.
Cost
One of the main disadvantages of using HMR in woodworking is the cost. HMR materials tend to be more expensive than traditional wood or other composite materials. This can significantly impact the overall cost of a woodworking project, especially if a large amount of HMR material is required.
Limited Design Options
Another disadvantage of HMR in woodworking is the limited design options available. Unlike natural wood, which can be easily shaped and customized, HMR materials are often pre-fabricated and do not offer as much flexibility in terms of design. This can restrict the creative possibilities for woodworkers who prefer more intricate and unique designs in their projects.
Environmental Impact
Lastly, the environmental impact of HMR materials is an important consideration. Many HMR materials are not biodegradable and may contribute to environmental issues such as waste accumulation and pollution. Additionally, the manufacturing process for these materials may also have negative implications for the environment.
While HMR has its disadvantages, it is important to weigh these against the benefits it offers in order to determine if it is the right choice for a particular woodworking project. Understanding both the pros and cons of HMR materials can ultimately lead to better decision-making in woodworking endeavors.
Different Types of HMR Materials Used in Woodworking
When it comes to woodworking, choosing the right materials is crucial to the success of any project. High Moisture Resistance (HMR) materials are increasingly gaining popularity in the woodworking industry due to their durability and versatility. There are several types of HMR materials commonly used in woodworking, each with their own unique characteristics and applications.
Melamine Faced Panels
One of the most widely used HMR materials in woodworking is melamine faced panels. These panels consist of a particleboard or MDF core that is coated with a melamine-impregnated paper overlay. The result is a smooth, durable, and moisture-resistant surface that is ideal for cabinet making, furniture construction, and interior design projects.
Phenolic Resin Coated Plywood
Another common type of HMR material used in woodworking is phenolic resin coated plywood. This material is made by impregnating layers of wood veneer with phenolic resin, which creates a strong and water-resistant plywood panel. It is often used in outdoor applications such as building construction, boat building, and outdoor furniture due to its exceptional resistance to moisture and weathering.
Thermally Fused Laminate (TFL)
Thermally fused laminate, or TFL, is another popular choice for HMR materials in woodworking. TFL panels are created by fusing multiple layers of decorative paper and resin together under high heat and pressure. The resulting material is highly durable, scratch-resistant, and moisture-resistant, making it suitable for a wide range of applications including kitchen cabinets, store fixtures, and architectural millwork.
Understanding the different types of HMR materials available in woodworking allows craftsmen to choose the best material for their specific project needs. Whether it’s melamine faced panels for indoor furniture or phenolic resin coated plywood for outdoor structures, HMR materials offer a reliable solution for creating long-lasting and resilient wood products.
Common Applications of HMR in Woodworking
HMR, or High Moisture Resistance, is a type of engineered wood product that is commonly used in woodworking projects due to its durability and resistance to moisture. This material has a wide range of applications in the woodworking industry, making it an essential component for various projects. Here are some common applications of HMR in woodworking:
1. Cabinet Making: HMR is often used in the construction of kitchen and bathroom cabinets due to its ability to withstand high levels of moisture and humidity. The use of HMR in cabinet making ensures that the cabinets will not warp or deteriorate over time, making them a long-lasting investment for homeowners.
2. Furniture Construction: Many furniture makers utilize HMR as a core material for building pieces such as desks, tables, and chairs. The high moisture resistance properties of HMR make it ideal for furniture that may be exposed to changing environmental conditions.
3. Outdoor Projects: HMR is also suitable for outdoor woodworking projects such as building outdoor furniture, decking, and fencing. Its resistance to moisture makes it a reliable material for withstanding the elements.
The versatility and durability of HMR make it a popular choice for many woodworking applications, especially those that require long-term stability and resistance to environmental factors.
Overall, these are just a few examples of how HMR is commonly used in the woodworking industry. Its ability to resist moisture makes it an appealing choice for many applications, ensuring that woodworkers can create durable and long-lasting products for their clients. Whether it’s used in cabinets, furniture, or outdoor projects, HMR continues to be a valuable material in the field of woodworking.
Tips for Working With HMR in Woodworking Projects
Woodworking projects often involve the use of HMR, or High Moisture Resistance, materials. HMR in woodworking refers to engineered wood products that are specially designed to withstand high levels of moisture and humidity without warping, swelling, or deteriorating. This section will provide valuable tips for working with HMR in woodworking projects to ensure successful and long-lasting results.
When working with HMR materials in woodworking projects, it is important to use the right tools and techniques. HMR materials can be more dense and heavy than traditional wood, so it is essential to have sharp cutting tools and a sturdy work surface. Additionally, using high-quality adhesives that are specifically formulated for HMR materials will help ensure strong and durable bonds.
Another important tip for working with HMR in woodworking projects is to properly seal and finish the material. While HMR materials are designed to resist moisture, proper sealing and finishing will provide an extra layer of protection against environmental factors. This can include using waterproof sealants or paints that are suitable for use on HMR surfaces.
It is also crucial to consider the specific application of the HMR material when working on a woodworking project. Whether it is for kitchen cabinets, bathroom vanities, or outdoor furniture, understanding the intended use of the finished product will help determine the best practices for working with HMR materials.
Tip | Description |
---|---|
Use sharp cutting tools | Ensure clean cuts in dense HMR materials |
Use high-quality adhesives | Ensure strong and durable bonds between HMR pieces |
Properly seal and finish | Add an extra layer of protection against moisture by using suitable sealants or paints |
Conclusion
In conclusion, HMR, or High Moisture Resistance, has become an integral part of the woodworking industry due to its durability and versatility. As technology in the manufacturing of HMR materials continues to advance, we can expect to see even more innovative and sustainable options for woodworking projects. The use of HMR in woodworking has evolved over time, from its introduction as a moisture-resistant alternative to traditional wood products to its wide range of applications in modern construction and design.
Despite some disadvantages such as limited finish options and higher cost compared to traditional wood materials, the advantages of using HMR in woodworking projects outweigh the drawbacks. Its resistance to moisture, mold, and wear make it an attractive option for outdoor furniture, kitchen cabinets, and bathroom vanities. This longevity contributes to sustainability in construction while reducing maintenance costs long-term.
As the demand for environmentally friendly building materials grows, we can anticipate the continued development of eco-friendly HMR options that offer the same resilience as traditional materials. With ongoing research into sustainable practices and materials, HMR is poised to play a significant role in shaping the future of woodworking by providing durable and environmentally friendly solutions for a variety of project needs.
Frequently Asked Questions
Is HMR Particle Board Better Than MDF?
HMR particle board and MDF are both engineered wood products, but they have different characteristics. HMR is known for its higher moisture resistance compared to MDF, making it a better choice for areas with high humidity or moisture.
What Is HMR Board Used For?
HMR board, also known as High Moisture Resistant board, is commonly used in areas where moisture resistance is important, such as kitchen cabinets, bathroom vanities, and furniture that may be exposed to higher levels of humidity. It is also used in interior decorative applications.
What Is the Difference Between HDF and HMR?
HDF (High Density Fiberboard) is a type of fiberboard made from highly compressed wood fibers, while HMR board is specifically designed to resist moisture. The difference lies in their intended use – HDF is more suitable for applications where high density and strength are required, while HMR board excels in areas with higher moisture levels.
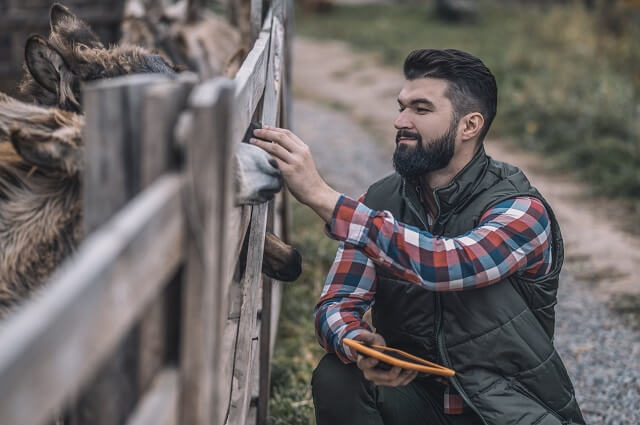
Hi everyone! I’m a woodworker and blogger, and this is my woodworking blog. In my blog, I share tips and tricks for woodworkers of all skill levels, as well as project ideas that you can try yourself.