Woodworking has evolved over the years, and one of the significant advancements is the integration of machines in woodwork. The use of machines has revolutionized the woodworking industry, allowing for increased precision, efficiency, and productivity. From traditional hand tools to modern machinery, the role of machines in woodwork continues to shape the future of this craft.
The history of machines in woodwork traces back to the use of hand-operated tools, which eventually paved the way for power tools and automated machinery. Today, woodworking machines such as table saws, bandsaws, planers, and more play a crucial role in shaping and creating wooden products with unparalleled accuracy.
This article aims to explore the different types of machines used in woodworking, their advantages, safety precautions when operating them, maintenance tips, and the impact of technology on woodworking machines. Additionally, it delves into future trends such as robotics and 3D printing that are set to further innovate the woodworking industry.
History of Machines in Woodwork
The evolution of machines in woodwork has been a significant factor in shaping the woodworking industry as we know it today. From the use of primitive hand tools to the introduction of modern machinery, the history of machines in woodwork showcases the progression and innovation within this field.
Early Beginnings: Hand Tools and Simple Machines
In the early days of woodworking, craftsmen relied on traditional hand tools such as chisels, saws, and planes to shape and manipulate wood. These tools required a great deal of skill and physical effort to use effectively. As time progressed, simple machines like pulleys and levers were incorporated to aid in lifting heavy materials and creating more precise cuts.
Industrial Revolution: Introduction of Power Tools
The Industrial Revolution brought about a monumental shift in woodworking with the advent of power tools. Steam-powered and later electrically powered machinery revolutionized production processes, allowing for increased efficiency and productivity. This period saw the introduction of machinery such as table saws, jointers, planers, and lathes, which became essential in mass-producing wood products.
Modern Era: Integration of Advanced Technology
In recent years, advancements in technology have further transformed the woodworking industry. Computer numerical control (CNC) machines have revolutionized woodworking by providing automated precision and intricate design capabilities. Additionally, innovations such as laser cutting machines and 3D printing have opened up new possibilities for creating intricate and complex woodwork designs.
Overall, the history of machines in woodwork reflects a journey from reliance on manual labor with hand tools to embracing advanced technology that has revolutionized the way woodworkers operate today.
Types of Machines Used in Woodworking
Woodworking has evolved significantly over the centuries, and one of the most impactful changes has been the introduction of machines in woodwork. These machines have revolutionized the industry, making it easier for craftsmen to create intricate and detailed pieces while also increasing efficiency and productivity. When it comes to woodworking machines, there are several types that are commonly used, each serving a specific purpose in the creation of wooden products.
One of the most essential woodworking machines is the table saw. This versatile tool is used for straight and angled cuts and is a staple in any woodworking shop. Another important machine is the bandsaw, which is ideal for cutting irregular shapes or resawing lumber into thinner pieces. Additionally, planers are crucial for creating smooth and flat surfaces on rough lumber, providing a seamless finish to woodworking projects.
These woodworking machines have transformed the way woodworkers approach their craft, allowing them to work with greater precision and efficiency. They have opened up new possibilities for creativity and design by enabling artisans to achieve intricate details that would be nearly impossible with traditional hand tools. As technology continues to advance, we can expect even more innovative machines in woodwork to further enhance the capabilities of craftsmen in the future.
Woodworking Machine | Primary Function |
---|---|
Table Saw | Straight and angled cuts |
Bandsaw | Cutting irregular shapes or resawing lumber |
Planer | Creating smooth and flat surfaces on rough lumber |
Advantages of Using Machines in Woodwork
The use of machines in woodwork has revolutionized the woodworking industry, providing a wide range of advantages that have significantly improved the precision, efficiency, and productivity of woodworkers. One of the main benefits of utilizing machines in woodwork is the enhanced level of precision they offer. Modern woodworking machines are equipped with advanced technologies that allow for accurate and consistent cuts, shaping, and joinery, resulting in high-quality finished products.
In addition to precision, machines in woodwork also bring about increased efficiency. With the ability to perform repetitive tasks at a much faster pace than traditional hand tools, woodworking machines enable craftsmen to complete projects in a shorter amount of time. This not only boosts productivity but also allows for higher output and fulfillment of larger orders.
Moreover, the utilization of woodworking machines contributes to enhanced productivity in the workshop. By streamlining processes and reducing manual labor, these machines enable woodworkers to focus their time and energy on other aspects of their craft, such as design and finishing work. This ultimately leads to greater overall productivity and a more efficient use of resources within the woodworking business.
Advantages | Impact |
---|---|
Increased Precision | High-quality finished products |
Efficiency | Faster completion of projects |
Productivity | Focus on design and finishing work |
Safety Precautions When Operating Woodworking Machines
When it comes to using machines in woodwork, safety should always be a top priority. Proper training and the use of protective gear are crucial to ensuring the well-being of woodworkers and anyone else nearby. The powerful nature of woodworking machines makes them potentially dangerous if not handled with care and knowledge. This section will delve into the essential safety precautions that should be taken when operating woodworking machines.
One of the most important aspects of safety when using machines in woodwork is receiving proper training. Whether it’s learning how to operate a table saw, bandsaw, planer, or any other type of woodworking machine, individuals should undergo comprehensive training on how to use the equipment safely and effectively. This will help prevent accidents and injuries caused by lack of knowledge or experience.
In addition to training, wearing appropriate protective gear is essential for safeguarding against potential hazards. Safety goggles, hearing protection, gloves, and respiratory masks are just a few examples of protective gear that should be worn when operating woodworking machines.
This gear can help protect against flying wood chips, loud noise, sharp tools, and fine dust particles that are common in woodwork settings. By following these safety precautions, woodworkers can minimize the risk of accidents and maintain a secure working environment while using machines in their craft.
Maintenance and Troubleshooting of Woodworking Machines
Woodworking machines are essential tools in any woodworking shop, allowing woodworkers to achieve precision and efficiency in their craft. To ensure the machines continue to operate effectively, regular maintenance and troubleshooting are crucial. Here are some tips for keeping woodworking equipment in top condition:
1. Regular Cleaning: Dust and debris can accumulate on woodworking machines, affecting their performance over time. It’s important to regularly clean the machines after use to prevent buildup. Use compressed air or a vacuum with a brush attachment to remove sawdust and particles from the machine’s surfaces, gears, and moving parts.
2. Lubrication: Proper lubrication of the moving parts of woodworking machines is essential for smooth operation. Check the manufacturer’s guidelines for recommended lubricants and schedules for applying them. Be sure to use the appropriate lubricants for each type of machine, such as oil-based or silicone-based lubricants.
3. Inspection and Adjustment: Regular inspection of woodworking machines is necessary to identify any signs of wear or damage. Check for loose belts, misaligned components, or worn-out parts that may need replacement. Make adjustments as needed, following the manufacturer’s instructions to maintain proper alignment and function.
4. Electrical Components: Woodworking machines often have electrical components that require careful attention. Inspect cords, switches, and plugs for any signs of wear or damage, and replace them if necessary. It’s also important to follow proper procedures for connecting and disconnecting power sources to prevent electrical hazards.
By following these maintenance tips, woodworkers can prolong the lifespan of their woodworking machines and ensure consistent performance in their woodworking projects.
Impact of Technology on Woodworking Machines
Woodworking machines have come a long way from traditional hand tools to modern, technologically advanced equipment. The integration of automation and digital controls has revolutionized the woodworking industry, offering a wide range of benefits and capabilities that were previously unimaginable. This section will delve into the impact of technology on woodworking machines, exploring how automation and digital controls have transformed the way woodworkers operate and produce their creations.
One of the most significant impacts of technology on woodworking machines is the level of precision and accuracy that can now be achieved. Automation allows for consistent and repeatable cuts, shaping, and carving, resulting in finely crafted pieces with minimal margin for error. Digital controls further enhance this precision by providing woodworkers with programmable settings and real-time monitoring of machine performance.
Additionally, the integration of automation and digital controls has greatly improved efficiency and productivity in woodshops. With automated processes and digital interfaces, tasks that once required manual labor can now be executed at a much faster pace. This not only saves time but also enables woodworkers to take on more complex projects and handle larger workloads.
Furthermore, technology has brought about a new level of versatility in woodworking machines. With digital controls, woodworkers can easily switch between different cutting patterns, adjust for various material thicknesses, or create intricate designs with just a few clicks. This flexibility opens up a world of creative possibilities, allowing artisans to push the boundaries of traditional woodworking techniques.
Future Trends in Woodworking Machines
The future of woodworking machines is an exciting landscape filled with innovative advancements that promise to revolutionize the industry. From robotics to 3D printing, these cutting-edge technologies are poised to reshape the way woodworkers approach their craft and produce their creations.
Robotics in Woodworking
One of the most significant trends in woodworking machines is the integration of robotics into the manufacturing process. Robotics have the potential to automate repetitive tasks, increase production efficiency, and improve overall precision in woodwork. With advancements in technology, robotic arms and automated systems are increasingly being used for tasks such as sanding, carving, and even assembly in woodworking processes.
3D Printing in Woodworking
Another innovative trend that is gaining traction in the woodworking industry is the use of 3D printing technology. While traditionally associated with plastics and metals, 3D printing has now found its way into the realm of woodworking. This technology allows for the creation of intricate and complex woodwork components with unparalleled precision, opening up new possibilities for design and customization in woodworking projects.
Other Innovative Advancements
In addition to robotics and 3D printing, there are a host of other innovative advancements on the horizon for woodworking machines. This includes improved digital controls for enhanced precision and accuracy, as well as advancements in material handling systems that aim to streamline the manufacturing process. Furthermore, developments in sustainable materials and eco-friendly practices are also playing a crucial role in shaping the future of woodworking machines.
As technology continues to evolve, it’s clear that the future of woodworking machines is bright with possibilities. Woodworkers stand to benefit from increased efficiency, precision, and creativity as they embrace these innovative advancements in their craft. As we look ahead, it’s clear that these trends will continue to shape and redefine the woodworking industry for years to come.
Conclusion
In conclusion, the use of machines in woodwork has significantly shaped the woodworking industry and will continue to play a crucial role in its future. From the early days of hand tools to the advanced machinery available today, technology has revolutionized the way woodwork is done. The introduction of table saws, bandsaws, planers, and other types of machines has brought about increased precision, efficiency, and productivity in woodworking projects.
Furthermore, as technology continues to evolve, we can expect to see even more integration of automation and digital controls in woodworking machines. The future of woodworking machines may also involve robotics, 3D printing, and other innovative advancements that will further streamline processes and expand possibilities for woodworkers.
Ultimately, it is important for woodworkers to embrace the advancements in technology and machinery while prioritizing safety precautions and proper training. By staying current with maintenance and troubleshooting tips for woodworking machines, individuals can ensure that their equipment remains in top condition for optimal performance. As we look ahead to the future of the woodworking industry, it is evident that embracing the role of machines will be essential for advancement and success within this field.
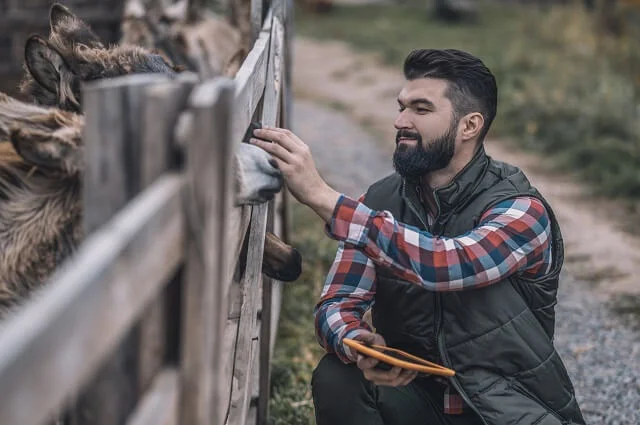
Hi everyone! I’m a woodworker and blogger, and this is my woodworking blog. In my blog, I share tips and tricks for woodworkers of all skill levels, as well as project ideas that you can try yourself.