A woodworking machine factory plays a crucial role in the woodworking industry, serving as the hub for manufacturing various types of machines essential for woodworking processes. These factories are responsible for producing a wide range of equipment such as saws, drills, sanders, and more that are used by craftsmen and industries alike. They are instrumental in ensuring the efficiency and accuracy of wood processing tasks, making them indispensable in the field.
The history of woodworking machine factories dates back to centuries ago when manual tools were replaced by mechanized ones to increase productivity and precision in woodworking. Over time, these factories have evolved significantly, incorporating advanced technologies and automation into their manufacturing processes. Their continuous evolution is a testament to their adaptability and commitment to meeting the ever-changing demands of the woodworking industry.
In today’s modern era, woodworking machine factories not only focus on producing high-quality equipment but also prioritize sustainability practices and innovation. By implementing stringent quality control measures, embracing new technologies, and adopting eco-friendly initiatives, these factories strive to reduce their environmental impact while staying at the forefront of technological advancements in the industry. This commitment to excellence ensures that woodworking machine factories remain key players in shaping the future of woodworking processes worldwide.
History of Woodworking Machine Factories
Woodworking machine factories have a rich history that dates back centuries, with the industrial revolution marking a significant point in the evolution of these facilities. Throughout history, woodworking machine factories have played a crucial role in revolutionizing the woodworking industry by introducing mechanized tools and equipment that increased efficiency and productivity. The early days of woodworking machine factories saw the emergence of basic cutting and shaping machines that laid the foundation for more sophisticated equipment in modern times.
Origins of Woodworking Machine Factories
The origins of woodworking machine factories can be traced back to the 18th century when the first automated woodworking tools were developed. These initial machines were rudimentary compared to today’s advanced technology but paved the way for further innovation in the industry. As demand for wooden products grew, so did the need for more efficient methods of production, leading to the establishment of specialized factories dedicated to manufacturing woodworking machines.
Evolution of Woodworking Machine Factories
Over time, woodworking machine factories evolved to meet the changing needs of customers and advancements in technology. From manual operation to computer-controlled systems, these facilities have adapted to incorporate new techniques and processes that improve precision and accuracy in wood processing. The evolution of woodworking machine factories has been driven by a combination of technological advancements, market demands, and consumer preferences, resulting in a diverse range of products that cater to various sectors within the woodworking industry.
Types of Woodworking Machines Manufactured
Woodworking machine factories are essential in the woodworking industry as they are responsible for manufacturing a wide range of machines that aid in the production process. These factories play a crucial role in providing woodworkers with the tools necessary to efficiently cut, shape, and finish wood products. Understanding the different types of woodworking machines manufactured in these factories is key to appreciating their importance and impact on the industry.
Here are some of the common types of woodworking machines produced in woodworking machine factories:
- Saws: Woodworking machine factories produce a variety of saws, such as table saws, band saws, and circular saws, which are used for cutting wood into various shapes and sizes.
- Drills: Another essential type of woodworking machine manufactured in these factories is drills, including bench drills, hand drills, and power drills, which are used for creating holes in wood for joinery purposes.
- Sanders: Woodworking machine factories also produce sanders like belt sanders, random orbital sanders, and disc sanders that help smooth and refine wooden surfaces by removing imperfections and enhancing overall finish.
These woodworking machines are instrumental in enhancing productivity and precision in woodworking projects. By understanding the different types available from woodworking machine factories, woodworkers can select the most appropriate tools based on their specific needs for crafting high-quality wood products.
The Manufacturing Process
Woodworking machine factories play a crucial role in the woodworking industry by producing a wide range of machines essential for wood processing. These factories are equipped with specialized tools, machinery, and skilled technicians to manufacture high-quality woodworking machines. The manufacturing process in a woodworking machine factory involves several steps that ensure the final products meet industry standards and requirements.
One of the initial steps in the manufacturing process of woodworking machines is the design phase. Engineers and designers work together to create detailed plans and specifications for each type of machine to be produced. This stage involves considering factors such as functionality, precision, safety, and efficiency. Once the design is finalized, it moves on to the fabrication phase where raw materials like metal, wood, and other components are sourced.
Following the fabrication stage, these raw materials undergo machining processes such as cutting, shaping, drilling, and welding to form the different parts of woodworking machines. Skilled machinists and technicians operate various equipment like lathes, milling machines, grinders, and CNC machines to transform raw materials into intricate components that will eventually make up a complete woodworking machine. The assembly phase then brings all these components together to build fully functional machines ready for quality testing before being released into the market.
Woodworking Machine Manufacturing Process | Description |
---|---|
Design Phase | Engineers create detailed plans and specifications for each machine. |
Fabrication Stage | Raw materials are sourced and processed through cutting, shaping, drilling, etc. |
Assembly Phase | All components are put together to build fully functional woodworking machines. |
Quality Control and Assurance
Woodworking machine factories prioritize quality control and assurance to ensure that their products meet industry standards and customer expectations. Here are some of the key measures taken by these factories to uphold the quality of their woodworking machines:
- Regular Inspections: Woodworking machine factories conduct routine inspections throughout the manufacturing process to identify any potential defects or issues. This helps in ensuring that each machine meets the desired specifications before being released to the market.
- Testing Procedures: Before finalizing a woodworking machine, factories subject them to rigorous testing procedures to evaluate their performance, durability, and safety. This includes running various tests to simulate real-world usage conditions and ensure that the machines meet all necessary requirements.
- Training and Certification: Employees working in woodworking machine factories receive specialized training in quality control processes and techniques. They are also required to obtain relevant certifications to demonstrate their proficiency in maintaining high-quality standards.
By implementing these measures, woodworking machine factories can guarantee that their products are reliable, efficient, and durable for users in the woodworking industry.
In addition to these measures, woodworking machine factories also prioritize continuous improvement and feedback mechanisms to enhance their quality control practices. By actively soliciting feedback from customers, conducting post-market analysis, and investing in research and development efforts, these factories strive to stay ahead of industry trends and consistently improve the quality of their products.
Innovation and Technology
Automation in Woodworking Machine Factories
One of the key advancements in woodworking machine factories is the integration of automation systems into their manufacturing processes. Automation allows for tasks such as cutting, shaping, and finishing to be carried out with minimal human intervention, leading to increased speed and consistency in production. By utilizing automated machinery and robotics, woodworking machine factories can optimize their operations, reduce labor costs, and improve overall product quality.
Digitalization and Smart Technologies
Digitalization has also played a significant role in transforming woodworking machine factories. Through the use of smart technologies such as sensors, data analytics, and IoT (Internet of Things) devices, factory operators can gather real-time insights into their production processes. This enables them to monitor equipment performance, track inventory levels, and identify potential maintenance issues proactively. Additionally, digitalization facilitates connectivity between different machines on the factory floor, creating a more streamlined and interconnected workflow.
Benefits of Innovation and Technology
Overall, the incorporation of innovation and technology in woodworking machine factories brings various benefits to both manufacturers and consumers. Manufacturers can achieve higher levels of efficiency, precision, and cost-effectiveness in their production processes. Consumers benefit from improved product quality, increased customization options, and faster turnaround times. As technology continues to advance at a rapid pace, we can expect even more groundbreaking developments in the woodworking machine factory industry that will shape its future trajectory.
Sustainability Practices
Woodworking machine factories play a significant role in the woodworking industry, manufacturing a wide range of machines such as saws, drills, and sanders that are essential for woodworking operations. These factories are vital for providing the necessary equipment to woodworkers, carpenters, and furniture makers to carry out their tasks efficiently. In addition to their importance in the industry, woodworking machine factories also have a responsibility to implement sustainable practices to reduce their environmental impact.
One of the key sustainability practices implemented by woodworking machine factories is the use of eco-friendly materials in the manufacturing process. This includes sourcing materials from renewable sources, using recyclable components where possible, and minimizing waste production during manufacturing. By incorporating these practices, woodworking machine factories can reduce their carbon footprint and contribute to environmental conservation efforts.
Moreover, woodworking machine factories are also exploring energy-efficient technologies to minimize electricity consumption and lower their overall energy use. This includes investing in energy-efficient machinery, optimizing production processes to reduce energy waste, and utilizing alternative energy sources such as solar or wind power. By adopting these energy-saving measures, woodworking machine factories can not only decrease their operational costs but also lessen their environmental impact significantly.
Sustainability Practices Implemented | Benefits |
---|---|
Use of eco-friendly materials | Reduces carbon footprint and waste production |
Exploring energy-efficient technologies | Minimizes electricity consumption and lowers energy use |
Future Outlook
Woodworking machine factories have been pivotal in revolutionizing the woodworking industry, providing essential tools and equipment for craftsmen and industrial operations alike. As we look towards the future of this industry, one can expect significant advancements driven by the integration of artificial intelligence (AI) and robotics. These technologies are poised to enhance efficiency, precision, and productivity in woodworking machine factories, marking a new era of innovation.
The incorporation of AI into woodworking machine factories can streamline processes such as design optimization, predictive maintenance, and production scheduling. By leveraging AI algorithms and machine learning capabilities, manufacturers can improve their decision-making processes and adapt quickly to changing demands. Additionally, robotics have the potential to automate repetitive tasks on the factory floor, freeing up human workers to focus on more complex or creative aspects of production.
In terms of product development, the integration of AI and robotics in woodworking machine factories may lead to the creation of smart machines capable of self-adjustment based on real-time data feedback. These intelligent systems could optimize performance parameters autonomously and even communicate with other machinery in a networked environment.
Overall, embracing these cutting-edge technologies will not only drive operational efficiencies within woodworking machine factories but also pave the way for new possibilities in creating innovative woodworking solutions for various industries. The future holds exciting prospects for the woodworking machine factory industry as it continues to evolve with technological advancements at its forefront.
Frequently Asked Questions
Who Makes the Best Industrial Woodworking Tools?
The best industrial woodworking tools are often considered to be those produced by companies with a long-standing reputation for quality and innovation. Names like Festool, SawStop, Powermatic, and Laguna Tools are frequently mentioned among professionals in the industry. These companies are known for producing high-performance tools that can withstand the demands of heavy-duty industrial use.
What Is the Most Popular Machine in a Woodworking Shop?
The most popular machine in a woodworking shop is typically the table saw. Table saws are versatile tools that can handle a variety of cutting tasks, making them essential in any woodworking shop. Whether it’s ripping boards to size or cutting precise joinery, a quality table saw is a cornerstone of most woodworking operations.
What Is the Oldest Woodworking Machine?
The oldest woodworking machine that is still in use today is believed to be the lathe. Lathes have been used for centuries to shape wood into various forms by rotating it along its axis while cutting tools are applied to the workpiece.
While modern lathes have advanced significantly in terms of technology and capabilities, they still utilize the same basic principles that were developed centuries ago.
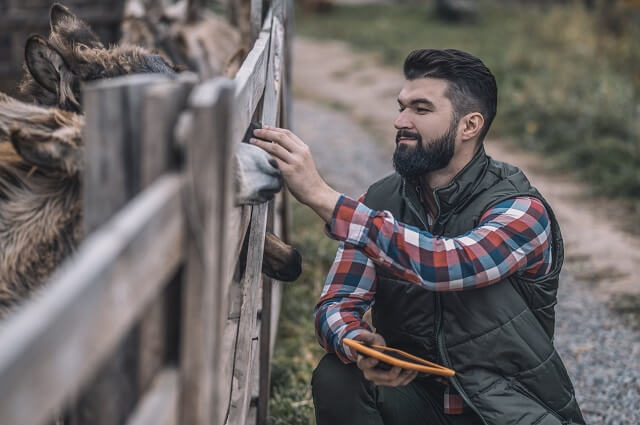
Hi everyone! I’m a woodworker and blogger, and this is my woodworking blog. In my blog, I share tips and tricks for woodworkers of all skill levels, as well as project ideas that you can try yourself.