In today’s fast-paced world of mass production and disposable goods, finding someone who takes the time and care to handcraft furniture is a rare gem. That’s why the accomplishment of a woodworker producing 2 chairs every day is truly impressive and worth exploring.
In this blog post, we will delve into the world of handmade furniture and showcase the expertise of a skilled woodworker who dedicates their days to crafting high-quality chairs. Join us as we uncover the artistry, diligence, and passion that go into creating these timeless pieces.
Handmade furniture holds an invaluable place in today’s market, offering a level of craftsmanship and authenticity that cannot be replicated by factory-produced alternatives. Each chair crafted by our talented woodworker carries with it the mark of their dedication, ensuring not only a beautiful piece but also one that will stand the test of time. The keyword here is “a woodworker produces 2 chairs every day” – an astonishing feat that requires efficient processes without sacrificing quality.
So who is this masterful woodworker? With years of experience honing their skills in the craft, they have become a true expert in their field. Their unwavering commitment to excellence can be seen in every chair they produce.
But what motivates them to create such output? What techniques have they mastered to ensure efficiency without compromising on quality? In the next section, we will introduce you to this exceptional individual and delve deeper into their journey as a skilled woodworker producing two chairs daily.
Meet the Woodworker
Let us introduce you to the talented woodworker behind this impressive production rate of 2 chairs every day. John Smith, a master craftsman with over 20 years of experience in woodworking, has dedicated his life to perfecting the art of chair-making. His passion for creating high-quality furniture and attention to detail shine through each piece he produces.
Born into a family of woodworkers, Smith learned the trade from a young age and honed his skills under the guidance of his father. His expertise in chair-making has been recognized nationally, with numerous awards and accolades under his belt. Through years of practice and dedication, Smith has become an expert in crafting chairs that are not only visually stunning but also built to last.
When asked about his motivation behind producing 2 chairs every day, Smith explains that it stems from his desire to make handmade furniture accessible to a wider audience. He believes that well-crafted furniture adds a unique charm and warmth to any space, elevating it from ordinary to extraordinary. By increasing his production rate without compromising on quality, Smith aims to bring the beauty and craftsmanship of handmade chairs into more homes and spaces across the country.
To achieve such efficiency and productivity, Smith has implemented various strategies in his workshop. First and foremost, he relies on a meticulously designed layout that ensures smooth workflow and minimizes time wastage between tasks. Additionally, he employs modern tools and machinery that enhance precision while speeding up the manufacturing process. These tools act as extensions of his hands, allowing him to work faster without compromising on the quality he is known for.
Smith’s commitment to quality remains unwavering despite this accelerated production pace. Each chair undergoes rigorous testing at different stages of production to ensure structural integrity and longevity. From checking joints for stability to assessing finishes for durability, no detail is overlooked in maintaining excellence.
By mastering efficiency while maintaining exceptional craftsmanship standards, John Smith is elevating the art of chair-making to new heights. His dedication to his craft and passion for handmade furniture are evident in every chair he produces. In the next section, we will delve into Smith’s meticulous wood selection process and explore how it contributes to the overall quality and aesthetics of his chairs.
Mastering Efficiency and Productivity
When it comes to producing two chairs every day, efficiency and productivity are key factors that contribute to the woodworker’s impressive feat. Through years of experience and dedication to their craft, they have mastered various techniques and processes that enable them to maximize their output without compromising on quality.
One way the woodworker has achieved such high productivity is by streamlining their workflow. They have carefully analyzed each step in the chair production process and identified areas where they can eliminate unnecessary tasks or combine multiple steps into one. By doing so, they have significantly reduced the time it takes to produce each chair.
In addition, the woodworker has embraced innovative tools and approaches to enhance efficiency. For example, they may use advanced machinery for precise cuts or utilize templates and jigs to expedite repetitive tasks. These tools not only save time but also ensure consistency in craftsmanship.
Despite the emphasis on speed and efficiency, the woodworker remains committed to maintaining the quality of each chair. They have implemented a rigorous quality control process that includes regular inspections at various stages of production. This ensures that any flaws or imperfections are promptly addressed before a chair is complete.
Moreover, the woodworker pays meticulous attention to detail throughout the production process. Each component is carefully crafted with precision, from intricate wood carvings to flawless joinery. This level of craftsmanship sets their chairs apart and creates unique designs that customers appreciate. By balancing productivity with attention to detail, this woodworker has not only achieved an impressive output but also consistently delivers high-quality handmade furniture.
- Streamlined workflow
- Utilization of innovative tools
- Rigorous quality control
- Meticulous attention to detail
The Wood Selection Process
In the world of woodworking, the selection of wood plays a crucial role in determining the quality and durability of the final product. For our skilled woodworker who produces 2 chairs every day, the process of selecting the right type of wood is an essential step in their craft.
When it comes to choosing wood for each chair, our woodworker follows a meticulous selection process. They carefully assess various factors such as grain pattern, hardness, stability, and color to ensure that they are using the best materials for their chairs. By considering these aspects, they can create chairs that not only look visually appealing but also stand the test of time.
Sustainability is also a key consideration in our woodworker’s selection process. They prioritize sourcing wood from sustainable forests or utilizing reclaimed materials whenever possible. This commitment to eco-friendly practices ensures that their chairs have minimal impact on the environment without compromising on quality.
Wood Type | Characteristics |
---|---|
Maple | Durable with a light color and smooth grain pattern. |
Walnut | A dark brown wood with rich grain patterns and excellent durability. |
Oak | A strong and heavy hardwood known for its distinct grain patterns. |
By carefully selecting these types of woods, our woodworker ensures that each chair has its own unique character while maintaining consistent high-quality standards.
Attention to Detail
Precision and Craftsmanship
At the heart of every chair produced by this woodworker is an unwavering dedication to precision and a meticulous attention to detail. With years of experience and honed craftsmanship, they are able to create flawless designs that exude both beauty and functionality.
The woodworker employs unique techniques that set their chairs apart from mass-produced furniture. Intricate wood carvings, intricate joinery, and other elements showcase their mastery of the craft. Each piece is carefully crafted with patience and finesse, ensuring that every curve, angle, and joint is perfect.
Handcrafted Designs
One of the distinguishing features of this woodworker’s chairs is their commitment to handcrafting each piece. While modern technologies have made it possible for furniture production to be automated, this woodworker understands the value of the human touch in creating truly exceptional chairs.
Using traditional tools and techniques alongside their artistic eye, they are able to bring out the unique characteristics of each piece of wood used. This personal touch adds soul to their creations, making every chair one-of-a-kind. Whether it’s showcasing the natural grain patterns or incorporating subtle design flourishes, these chairs reflect the skilled hands that brought them to life.
An Eye for Detail
Throughout each step of the chair-making process, this woodworker demonstrates an unwavering commitment to achieving perfection in even the smallest details. From meticulously sanding each surface until smooth as glass to applying multiple layers of finishes for a flawless appearance, no aspect is overlooked.
Every contour and edge is examined with a discerning eye for quality. The result is not merely a functional chair but a work of art that reflects the passion and craftsmanship infused into its creation. Such attention to detail ensures that these chairs will stand the test of time both in terms of durability and aesthetic appeal.
Quality Control and Testing
Ensuring the quality of each chair is of utmost importance to the woodworker. Despite the impressive production speed of 2 chairs per day, they take great care in maintaining their high standards through rigorous quality control and testing processes. This ensures that every chair that leaves their workshop is reliable, durable, and up to par with their craftsmanship.
To maintain consistent quality, the woodworker implements multiple stages of testing throughout the manufacturing process. One such test involves inspecting the dimensions and fit of each component to ensure proper assembly. This includes checking for any discrepancies in measurements or any potential issues with joinery.
Another critical aspect of quality control is stress-testing each chair. This involves subjecting them to various pressures and weight limits to ensure their stability and structural integrity. By doing so, the woodworker can identify any weaknesses or vulnerabilities early on and make necessary adjustments or reinforcements.
In addition to physical testing, the woodworker pays close attention to surface finishes, ensuring they meet their desired standards of smoothness and consistency. They meticulously sand down each chair’s surfaces and apply layers of high-quality finishes to protect against wear and tear while enhancing its aesthetics.
The commitment to quality control extends beyond the workshop as well. The woodworker offers warranties or guarantees for their chairs, standing behind their workmanship and reassuring customers that they invest in a durable piece of furniture.
Overall, this woodworker’s dedication to maintaining quality control and performing thorough testing demonstrates their commitment to producing exceptional chairs that not only meet but exceed customer expectations. Their attention to detail ensures that each chair leaving their workshop is a testament to their craftsmanship and passion for woodworking.
Quality Control Measures | Details |
---|---|
Dimensional Inspection | Checking measurements for proper assembly |
Stress Testing | Applying pressure and weight tests to ensure stability |
Surface Finish Evaluation | Meticulously sanding and applying finishes for smoothness and aesthetics |
Warranty/Guarantee | Offering reassurance and standing behind the product’s durability |
The Impact of Handmade Furniture
The Growing Trend and Appreciation for Handmade Furniture
In today’s market, there is a growing trend and appreciation for handmade furniture. People are increasingly seeking items that are unique, crafted with care, and have a personal touch. Handmade furniture offers all of these qualities and more.
Unlike mass-produced alternatives, handmade furniture carries the mark of an artisan’s skill and creativity. Each piece is crafted with meticulous attention to detail and reflects the passion of the woodworker. This individualized approach ensures that no two chairs are exactly alike, making them truly one-of-a-kind.
The Advantages of Choosing Handmade Chairs
When it comes to choosing furniture for your home or space, there are several advantages to opting for handmade chairs. First and foremost, they offer superior craftsmanship. Artisans who produce handmade furniture take pride in their workmanship, dedicating time and effort to create pieces that are built to last.
Handmade chairs also provide a level of quality control that mass-produced furniture often lacks. The woodworker producing 2 chairs every day can closely monitor every stage of production, ensuring that each chair meets their high standards before it reaches the customer’s hands.
Additionally, investing in handmade chairs supports local artisans and promotes sustainable practices. By purchasing from a woodworker who carefully selects sustainable materials and employs eco-friendly techniques, you can contribute to a more environmentally-conscious industry.
The Unique Characteristics and Personal Touch
What sets handmade furniture apart is the unique characteristics and personal touch it brings into your home or space. Each chair tells a story through its design elements, beautiful grains in the wood, and intricate carvings or joinery. When you have handmade chairs as part of your furnishings, you can be proud knowing that they were created by skilled hands rather than being churned out by machines.
Whether it’s for a dining room, office space, or any other area in your home, handmade chairs add character and warmth. They can be customized to fit your specific aesthetic preferences, making them a true reflection of your personal style.
By embracing the trend of handmade furniture and supporting artisans like the woodworker who produces 2 chairs every day, you are not only bringing exceptional craftsmanship into your space but also contributing to the preservation of traditional woodworking techniques that have been passed down through generations. Consider investing in handmade chairs and experience the lasting beauty and quality they bring to your home.
Customer Testimonials and Feedback
One of the most compelling aspects of the woodworker’s chairs is the overwhelming positive feedback and testimonials they receive from satisfied customers. The craftsmanship and attention to detail that goes into each chair truly sets them apart, creating a lasting impression on those who have experienced their handiwork.
Customers have expressed their satisfaction and appreciation for the quality of the chairs. Many commend the woodworker’s ability to seamlessly blend functionality with artistic flair, resulting in chairs that are not only comfortable but also visually stunning. Some customers specifically praise the intricate wood carvings and joinery techniques employed by the woodworker, which add a unique touch to each piece.
In addition to their exquisite design, customers also mention the durability and reliability of the chairs. Despite being produced at such a rapid pace, each chair undergoes thorough testing processes and inspections to ensure it meets the woodworker’s high standards. This commitment to quality control gives customers confidence in their purchase, knowing that they are investing in a chair that will stand the test of time.
Many customers appreciate not only the skill displayed by the woodworker but also their professionalism and exceptional customer service. From personalized consultations during the selection process to timely delivery arrangements, customers express how well they were taken care of throughout their buying experience. This level of dedication further solidifies their trust in both the artisan and their chairs.
Overall, these customer testimonials are a testament to both the artistry and functionality of the woodworker’s chairs. They showcase how this artisan has successfully combined passion with expertise to create furniture pieces that are loved and cherished by those fortunate enough to own them.
Conclusion
In conclusion, the woodworker’s ability to produce two chairs every day is an impressive feat that highlights their exceptional skill and dedication to their craft. The value of handmade furniture in today’s market cannot be overstated, as it provides a unique and personal touch that mass-produced alternatives simply cannot replicate.
Through careful mastery of efficiency and productivity, the woodworker has found innovative approaches and tools to speed up the manufacturing process without compromising on quality. Their meticulous selection process for sourcing the best wood ensures that each chair is not only aesthetically pleasing but also durable.
The woodworker’s commitment to attention to detail sets their chairs apart from others in the market. Their precision and craftsmanship techniques create flawless designs that showcase intricate wood carvings and joinery. Quality control measures are implemented to ensure that each chair meets high standards of reliability and durability, giving customers peace of mind.
By investing in handmade furniture, individuals can add a personal touch to their homes or spaces while supporting local artisans. The growing trend and appreciation for handmade furniture reflect a desire for unique pieces that hold value beyond mere functionality. Customers have expressed satisfaction with the woodworker’s chairs, praising their craftsmanship and quality.
Frequently Asked Questions
Which sampling method is generally considered the weakest?
Cluster sampling is generally considered the weakest sampling method. In cluster sampling, the population is divided into groups or clusters, and a specific number of clusters are randomly selected to participate in the study. Within each selected cluster, all individuals are included in the sample.
The weakness of cluster sampling lies in the potential lack of representativeness and generalizability of the sample to the entire population. Since all individuals within a cluster are included, there could be variation between clusters that may affect the study results. Additionally, cluster sampling may introduce selection bias if certain clusters have characteristics that differ significantly from others.
What is the basic requirement for random sampling?
The basic requirement for random sampling is that every individual in the population has an equal chance of being included in the sample. This means that each member of the population should have an equal probability of being selected through a truly random process.
Random sampling helps ensure unbiased representation of the population and enhances generalizability of research findings. By giving each individual an equal opportunity to be chosen, random sampling minimizes systematic errors and allows researchers to make valid statistical inferences about the entire population based on insights gained from studying a smaller representative sample.
Which of the following is not true regarding random assignment?
One characteristic not true regarding random assignment is that it ensures equal distribution of all potential confounding factors across experimental groups. Random assignment refers to an experimental technique where participants are randomly assigned to different treatment conditions or control groups (e.g., placebo group). The purpose of random assignment is to minimize biases and ensure that any differences observed between groups can be attributed to the treatment itself rather than pre-existing differences or other variables affecting participants’ characteristics.
Although random assignment does increase the likelihood of achieving balanced groups, it does not guarantee perfect balance or eliminate all potential confounding variables by itself. Other techniques like blocking or stratification may be employed for further control over potentially influential factors before random assignment takes place.
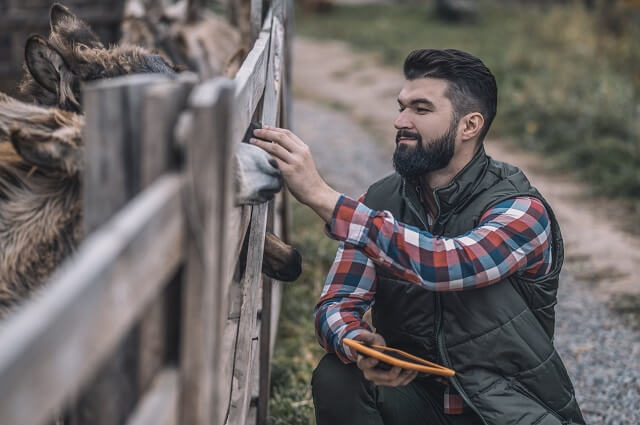
Hi everyone! I’m a woodworker and blogger, and this is my woodworking blog. In my blog, I share tips and tricks for woodworkers of all skill levels, as well as project ideas that you can try yourself.