Introduction
Air compressor woodworking is a rewarding yet challenging endeavor. It requires patience and careful planning prior to the execution of any project. The use of a reliable air compressor coupled with the right tools, is essential for any successful project. Understanding how an air compressor works, the key components required, selecting suitable materials and estimating time and energy needed to complete a project are some of the fundamentals that an avid woodworker should be familiar with.
When using an air compressor for woodworking, it is important to understand its basic components such as the motor, tank, pressure regulator and safety valve. Compressors vary in size depending on their power source (electric or petrol) and capacity of the tank in terms of CFM (Cubic Feet per Minute). Knowing what type of compressor is suitable will depend on the task at hand and its frequency of use.
The selection of materials is also essential when it comes to woodworking with an air compressor. Choosing appropriate timber can reduce sanding time as different types react differently when subjected to heat from tools like orbital sanders or polishers that require airflow from the compressor. Estimating the amount of material needed for a specific task can cut down construction waste which would result in cost savings over time.
Finally, it is necessary to make accurate estimates when calculating total completion times for projects along with factorizing energy expenses with realistic figures based on purchase prices and running costs associated with an air compressors’ motor type, size etc. That being said, proper preplanning will greatly assist in producing satisfactory results while working with tools powered by compressed air.
Key Benefits of Woodworking with an Air Compressor
Air compressors are great for powering the tools of woodworking. An air compressor is used to convert power into potential energy stored in pressurized air, which can provide a constant and powerful source of energy to use with a wide range of tools. Compressed air is cleaner than electricity, so it is much safer than using electrical tools. This makes them ideal for use in public or workshop areas, ensuring both safety and reliability. Furthermore, compressed air tools offer greater precision when working with wood; allowing for more accurate and controlled cuts and finishes. Air compressors also require minimal maintenance since they do not rely on switching components or having high voltage electrical current flow through them like electric motors do, making them ideal if you need reliable performance over long time periods. Finally, they produce far less noise and vibration than electric motors and are have a much lower cost in operation than electric hand tools due to their highly efficient nature. With all these advantages, it is no wonder that air compressors have become so popularly used in woodworking projects.
Essential Tools and Accessories for Air Compressor Woodworking
The most important tool for air compressor woodworking is an air compressor. Without this, you will be unable to power any of the tools needed for the job. A good-sized compressor with sufficient pressure and tank capacity should be the first purchase.
In addition to the air compressor, essential tools and accessories include various types of nail guns, a drill, impact wrenches, sanders and grinders, spray guns and saws. Air tools are typically more powerful than conventional counterparts and their use can help cut down on fatigue from manual labor. Having an air regulator that allows precise control of the air pressure is also necessary for many jobs. Specialized attachments such as nozzles and hoses must also be purchased depending on need.
Safety gear should not be overlooked either; wearing protective goggles and using special earplugs are all essential items when working with loud machinery like compressors sent at high pressures among other power tools. It may also prove beneficial to have some sort of dust mask due to particles created by sanding or grinding projects inside or outdoors. Lastly, having a variety of clamp sets will help hold workpieces in place while they are being routed or nailed together.
Techniques for Sanding and Finishing Wood with an Air Compressor
Using an air compressor while woodworking has become popular due to its many advantages. Air compressors offer more power and portability than electric motors, and they can also be used for intricate detailing. As a woodworker, you can use an air compressor to assist in sanding and finishing wooden pieces. Here are some of the techniques for getting the most out of your air compressor for sanding and finishing wood:
1. Use an adjustable speed sander attachment with your air compressor so you have more control over the pressure of sanding. This allows you to produce smooth surfaces quickly as well as create intricate detail work with ease.
2. If a specific area needs extra attention, use a die grinder attachment on the air compressor to achieve more precision when taking off small amounts of wood and providing clean edges.
3. Use a contour sander attachment to take off just enough material from curves or corners without severely damaging the surface of the wood piece you are working on.
4. Use a rotary scraper attachment to remove what is left after rough-sanding these areas with a belt/disc sander ” this will ensure that all surfaces are even before staining or painting them with any sealants available at hardware stores and DIY shops.
5. When it comes to finishing, using an airbrush along with an air compressor can help achieve flawless results in less time than traditional brush applications would take while still giving you the same great look quality finish desired on any project!
Tips for Choosing the Right Air Compressor for Woodworking
When choosing the right air compressor for woodworking, it is important to consider a few factors. The horsepower (hp) and capabilities of the compressor will determine how powerful a tool it can power. If you are using pneumatic tools such as a drill or sander, then you will need to ensure that your compressor has enough power to provide adequate airflow. You should also consider the capacity of your compressor’s tank – larger tanks can allow you to use more powerful tools without running out of air pressure during operation. Additionally, noise is an important factor to take into consideration when shopping for an air compressor. Air compressors with rubber mounts often reduce vibration and thus decrease noise levels, making for a more comfortable workspace. Finally, make sure you choose an air regulator that has adjustable settings; this will allow you to adjust airflow speed and pressure based on whichever projects you may be working on at the time. With these tips in mind, you should be able to find an air compressor that is suitable for all of your woodworking needs.
Common Risks and Safety Measures for Air Compressor Woodworking
Air compressor woodworking is an extremely popular form of construction and carpentry as it can reduce labor costs and provide greater accuracy. However, it also poses certain inherent safety dangers due to the pressure and force that comes from using compressed air tools. Therefore, any individual engaging in this type of work must be aware of the possible risks they may face and take steps to ensure their safety.
One of the primary risks associated with air compressor woodworking is exposure to loud noise levels, which can lead to potential hearing damage if proper hearing protection isn’t used. Compressed air tools can emit sound levels as high as 100 decibels or higher, so it’s essential to wear ear protection while operating them. Additionally, flying debris like sawdust and wood chips can pose a risk of eye injuries unless proper face protection is worn.
Other potential dangers include strain on the body due to vibration or fatigue from overexertion related to carrying heavy equipment or working for long periods of time with limited breaks. It’s important for individuals to pay attention to signs of fatigue such as aches, pains, lightheadedness, headaches and dizziness and stop work if these occur or take regular breaks throughout their day.
Finally, improper use or maintenance of compressed air tools can lead to serious injury from flying pieces of metal or plastic being ejected at high speed. This highlights the importance for users to fully understand how a tool should be used before starting a job as well as ensuring that all components are checked regularly for any wear and tear that could affect safe operation.
Common Beginner Mistakes to Avoid in Air Compressor Woodworking
1. Not having enough air storage capacity: Air storage capacity is important when it comes to air compressor woodworking as the right amount can be the difference between success and failure. A large tank with a larger capacity will provide more adequate power for your woodworking tasks like cutting, sanding, and spraying. Having too little air storage can cause there to not be enough compressed air for all of your needs.
2. Using the wrong sized compressor: When selecting an air compressor for woodworking, it’s important to get one that is appropriate in size for the job. A small compressor with inadequate power won’t get the job done effectively, while an over-sized unit will cost significantly more yet not produce satisfactory results either.
3. Incorrectly set pressure regulator: Ensuring that your pressure regulator is properly set is important when working with any type of air tools or machinery. The recommended pressure setting can be found in the instruction manual and should never exceed what’s outlined in the guide; over-pressurizing could prove to be dangerous or damaging to your active equipment.
4. Not checking filters and lubricants regularly: Check the filter regularly on your particular model when doing maintenance or else you risk contaminants ending up inside the tank which can lead to a whole host of problems including clogging and decreased performance of your machine due to poor airflow or lack of lubrication within internal components. Proper lubrication across parts is also necessary so make sure this doesn’t slip by without attention!
Conclusion
Using an air compressor as a tool for woodworking opens up new possibilities for unique designs and precision work. Craftsmen can use air tools to create intricate detailing and achieve smoother, more consistent results when creating cutting boards, furniture pieces and other items. Air compressors allow for greater control and accuracy when using drill bits for drilling, router bits for edging, and sanders for finishing surfaces. Additionally, by adding various nozzles and attachments to the end of the air hose craftsmen can customize the amount of airflow needed depending on the task being completed. By having access to this abundance of tools which an air compressor provides, craftsmen are able to improve their quality of work while also having fun trying out creative projects – all with the same machine.
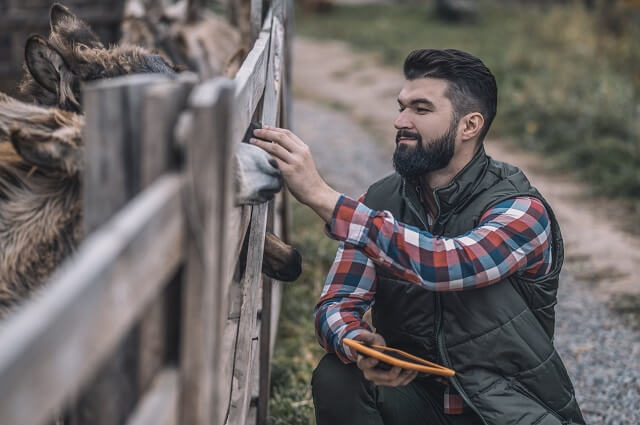
Hi everyone! I’m a woodworker and blogger, and this is my woodworking blog. In my blog, I share tips and tricks for woodworkers of all skill levels, as well as project ideas that you can try yourself.