Introduction to Automated Woodworking Machinery
Automated woodworking machinery is an important tool for those in the woodworking industry. It offers a number of advantages to professional wood workers, such as increased accuracy and consistency of cuts, increased productivity, decreased waste and faster production times. Automation also reduces the need for skilled labor and manual labor, minimizing costs. This makes it an attractive option for businesses that want to produce large volumes of wood components with minimal costs.
The range of automated woodworking machinery available today includes saws, routers, planers, moulders, jointers and lathes. These machines can be used for a variety of applications in the world of furniture making and carpentry. Saw machines are typically used for cutting shapes from stock material such as boards or plywood sheets and prepare joints like mortises. Routers are used to shape edges and form shapes by routing out shallow grooves known as dadoes or rabbets. Planers are used to plane surfaces and smooth them down flat. Moulders can create profiles on stock materials as well as curved or corrugated surfaces. Jointers let two pieces of once-improperly joined material fit together snugly while lathes are used to shape round objects like table legs or decorative jewelry boxes using a cutting tool in controlled rotary motion.
Other uses for automated woodworking machinery include aligning wood pieces precisely and creating complex miter joints which would otherwise be very difficult to cut by hand manually; milling curved parts; drilling holes; sanding parts; assembling projects like birdhouses or cabinets; finishing projects with paint; engraving; carving 3D structures; as well as pressing veneer onto flat surfaces like in all types of furniture construction.. Automation also allows project designers to quickly switch from one task to another without having to reset their tools each time. The use of automated machinery leads to repeatable results that finish not only faster but more precisely than can be achieved by hand tools allowing for easier assembly in subsequent operations when building furniture or cabinetry..
The History of Automated Woodworking Machinery
Automated woodworking machinery has become a mainstay in manufacturing and production. Prior to the industrial revolution, most woodworking was completed by hand at small shops scattered across the countryside. By the mid-1800s, as machine tools became more sophisticated, factories began using automated woodworking machinery for mass production. At first, these machines tackled only simple tasks such as drilling holes and cutting boards on a straight line. Often driven by human or animal power, these early machines still took much longer to complete complicated tasks than modern counterparts.
By the turn of the century, some of these automated machines had begun to perform more complex jobs. This increase in complexity gave manufacturers access to more production with less labor and paved the way for today’s computer-controlled CNC routers and other automated equipment used in furniture making, millwork fabrication and cabinetry construction. Today’s automated machinery is capable of executing highly detailed instructions quickly and accurately. Virtually every aspect of a project can be accomplished through automation including cutting, edge banding, mortising joints, sanding, drilling pilot holes and creating three-dimensional components that would be impossible to make by hand. The combination of speed and precision can result in significant cost savings through reduced labor costs and shorter lead times on projects so manufacturers are able execute work orders with greater efficiency than ever before.
Types and Performance of Automated Woodworking Machinery
Automated woodworking machinery is used in large production environments where efficiency and quality are of utmost importance. There are several types of automated machinery each with varying performance capabilities.
One type of automated woodworking machinery features CNC (Computer Numerical Control) routing machines which can be programmed to precisely shape wood pieces into a variety of custom shapes and sizes. These machines feature high velocity spindles for cutting, routing, and shaping the material, as well as multiple heads that can be used for more complex operations such as turning and profiling. Other specialized CNC machines include beam saws, which allow users to accurately cut large stock materials into multiple parts using just one machine, as well as panel sizing saws with electronic control systems which make repetitive cuts while still providing accurate results.
Another type of automated woodworking machinery is edgebanding machines capable of producing smooth firmly-adhered edges on boards without the use of glues or screws. Edgebanders feature a feeder system that moves the board along a track while it is sprayed with glue or heat activated adhesive tape at the same time that electrical motors drive rubber rollers applying pressure to the edging bands. The precision glue application ensures a consistent result every time.
Sanding machines also fall within this category and offer a range of features from simple belt sanders to computer-controlled sanders featuring multiple working units applied in succession for even more consistent results. These multi-head sanding systems allow operators to achieve higher levels of automation by reducing human labor input by automating work stages that previously required manual operation or additional floor space for accommodating large scale abrasive devices like orbital sanders or wide belt sanders.
Key Features of Automated Woodworking Machinery
Automated woodworking machinery is an essential tool for any modern woodworking or manufacturing facility. It offers a number of key features that give benefits when it comes to speed, accuracy, and consistency.
One key feature of automated woodworking machinery is its ability to cut with precision. Utilizing computer-controlled routers and lasers, these machines are designed to make precise cuts in a variety of materials with minimal waste, reducing labor costs associated with manual cutting methods. Automated routers also tend to provide more consistent results than hand routing tools, helping to lower scrap rates and create higher quality products.
Another great feature of automated woodworking machinery is the ability for users to customize the size and shape of the finished product on-the-fly. Operators can adjust settings on the machine without having to worry about setup procedures each time, saving valuable time during production runs. This feature also allows for greater flexibility when creating custom shapes and components, enabling increased product variety and merchandising options.
In addition to its cutting capabilities, automated woodworking machines also boast features like automatic tooling adjustments that help reduce setup time in between operations. This type of automation helps increase efficiency levels because it eliminates the need for manual intervention during operation changes or swap-outs, resulting in fewer downtime events caused by human error or operator fatigue.
Finally, most automated machines have integrated safety features like guards that enclose moving parts such as blades or side milling stages, providing a safer user experience while keeping man and machine separated at all times. Similarly they come equipped with fail-safe mechanisms that will halt production if an unexpected event occurs — protecting people as well as delicate materials from potential risk during operation.
Common Applications of Automated Woodworking Machinery
Automated woodworking machinery is commonly used for many tasks including milling, cutting, sanding, carving, and routing. Milling involves using a rotating tool to cut into and shape the workpiece. Cutting includes planing, band sawing, crosscutting, and rip sawing as well as grooving and chamfering with a router. Sanding involves using abrasive materials like sandpaper or drum sanders to prepare the surface of the wood. Carving can involve engraving intricate patterns into thin pieces of wood or shaping large surfaces. Finally, routing is a type of machining that uses cutters to shape the edges of a wood piece along predetermined line paths. Automated woodworking machinery also finds use in hardwood floor installation and furniture manufacturing operations.
Things to Consider Before Purchasing Automated Woodworking Machinery
1. Budget: Before purchasing any automated woodworking machinery, it is important to consider how much money you are willing to spend and what type of equipment you need. It is important to research different brands and models so that you can make an informed decision based on the features and cost. Additionally, it is also vital to understand what accessories will be required for operation such as tooling, blades and cutting speeds.
2. Features: There are a range of features available when selecting automated woodworking machinery such as cutting speed, accuracy, precision, efficiency and safety features. Understanding the functions of each feature will help you determine which model best suits your needs as well as your budget.
3. Maintenance Requirements: Automated woodworking machinery requires regular maintenance in order to keep it operating at peak performance for longer periods of time. Checking the manufacturer’s manual for the recommended maintenance schedule will help make sure the machine’s components last longer without needing costly repairs due to wear and tear from improper upkeep.
4. Operator Training: If the operators in your facility are not properly trained on how to safely use the machining equipment they may be put at risk of being injured while using the machines or causing damage to them due to misuse or inexperience with specific functions or procedures within automated woodworking machinery programming software/hardware systems. Therefore it is essential that thorough training is carried out before allowing any personnel use the machining equipment unsupervised which could result in significant financial losses if not followed correctly
Automated Woodworking Safety and Best Practices
When operating or working around automated woodworking machinery, it is important to follow basic safety procedures to help avoid injury and ensure optimal performance. To begin, workers should always wear protective clothing and equipment, including face masks, safety glasses, and hearing protection. Additionally, any loose jewelry or clothing should be removed so it does not get caught in the machine’s moving parts. Before starting the tools and machinery, workers can inspect the area to make sure all guards are installed properly and the workpiece is securely clamped. Machines should be turned off whenever one is adjusting or replacing parts such as saw blades. When turning on the machinery again, operators should wait at least 10 seconds after pushing the start button to allow enough time for all of its internal components to move into position before beginning operations. It’s also important that no operators stand in line with the cutting path of hand-fed machines. Lastly, workers need to be aware of their surroundings at all times when using woodworking machinery and take extra safety precautions when working near chemicals can cause a fire or other accident if mishandled or ignored.
Conclusion
Automated woodworking machinery offers an infinite range of possibilities when it comes to creating both functional and decorative objects. It is becoming increasingly popular among both professionals and serious do-it-yourselfers alike, as its capabilities save time, money, and effort throughout the entire crafting process. Whether you need to make precise cuts for furniture or intricate details for a wall decoration, automated woodworking machines can get the job done quickly and efficiently. Best of all, they open up the creative potential of anyone willing to explore its possibilities. With automation technology being constantly improved upon, woodworking has never been easier!
Automated woodworking machinery is an essential tool for any hobbyist that is looking to take their craftsmanship to the next level. When used correctly by someone who knows what they’re doing, this machine can produce results far more accurate than those achieved with traditional hand tools. Not only does it bring precision accuracy in cutting lines and angles, but it also speeds up the production rate significantly so you can get more projects done in less time. What’s even more appealing about these machines is that they require very little maintenance while still producing top-notch results every single time.
Finally, automated woodworking machinery brings a versatility like no other tool out there. You can use it to shape practically any type of material into anything you can imagine – from basic cabinetry to complicated carvings that would be impossible with traditional tools alone. As technology advances further, these machines will become even more powerful so there’s no telling what kind of new creations we’ll see popping up on our streets soon! The bottom line is that if you are looking for a way to expand your creativity through woodworking projects then this machine is an essential tool worth considering now and in the future.
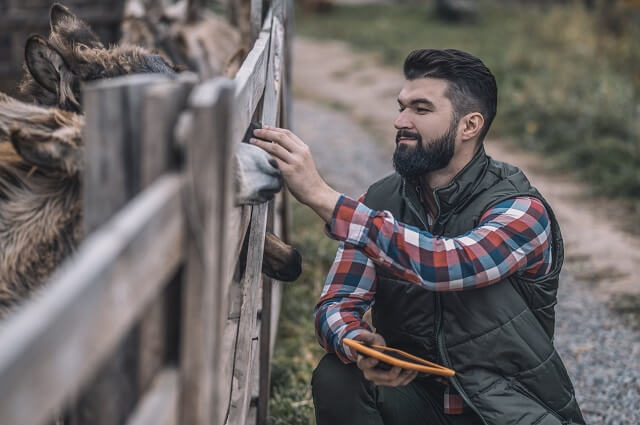
Hi everyone! I’m a woodworker and blogger, and this is my woodworking blog. In my blog, I share tips and tricks for woodworkers of all skill levels, as well as project ideas that you can try yourself.