Can a subpanel handle a woodworking shop? This question is of utmost importance for those who are keen on setting up their own woodworking shop. A woodworking shop requires a proper electrical setup to ensure safety and efficiency. In this article, we will explore the significance of having a dedicated subpanel for improved safety in woodworking shops and discuss the potential risks of overloading the main panel.
When it comes to woodworking shops, having a dedicated subpanel is crucial for maintaining electrical safety. Woodworking tools, such as table saws, planers, and jointers, require substantial amounts of power to operate effectively. By having a separate subpanel, you can distribute the electrical load more efficiently and reduce the risk of overloading your main panel. This not only ensures safety but also allows for better power management in your woodworking shop.
Overloading the main panel can lead to various issues, including tripped breakers or even electrical fires. A main panel may not have sufficient capacity to handle all the power demands of your woodworking tools and equipment. By connecting your woodworking shop to its own subpanel, you can mitigate these risks and create a safer environment for your projects.
In the next sections of this article, we will dive deeper into understanding what exactly a subpanel is and how it differs from a main panel. We will also discuss how to assess the electrical needs of your woodworking shop and choose the appropriate subpanel. Additionally, we will provide step-by-step guidance on wiring the subpanel, calculating its load capacity, ensuring safety considerations, troubleshooting common issues that may arise with subpanels, and more.
So if you’re wondering whether or not a subpanel can handle your woodworking shop’s electrical needs, read on as we explore the ins and outs of proper electrical setup for woodworking shops.
Understanding the Basics
A subpanel, also known as a subdistribution panel or a subsidiary panel, is an independent electrical panel that branches off from the main electrical panel in a building. It serves as a distribution point for electricity to specific areas or circuits within a woodworking shop. While the main panel is responsible for delivering power to the entire building, including other rooms and appliances, the subpanel focuses solely on the electrical needs of the woodworking shop.
Definition and Purpose of a Subpanel
A subpanel is essentially a smaller version of the main electrical panel that is designed to handle the specific power demands of a dedicated space. It acts as an intermediary between the main panel and various woodworking tools and machines in a shop. The purpose of having a subpanel is to ensure efficient power distribution and mitigate potential risks associated with overloading the main electrical system.
Difference Between Subpanels and Main Panels
Subpanels differ from main panels in several ways. While both panels have circuit breakers for protection against overloads, only the main panel has its own disconnect switch or breaker, which shuts off power to the entire building if necessary. Subpanels do not require their own disconnects because they can be fully powered down by shutting off power at the main panel.
Another notable difference is that while main panels are typically located close to where electricity enters a building (e.g., near the electric meter), subpanels can be placed anywhere inside a building as long as proper wiring is established. This flexibility allows woodworkers to strategically position their subpanel closer to their equipment, reducing any potential voltage drop issues due to long wiring runs.
Electrical Load Distribution
The primary function of both main panels and subpanels is load distribution. Electrical load refers to the amount of power required by various devices connected to an electrical system at any given time. Distributing this load properly across multiple circuits ensures that no single circuit is overloaded, which could lead to tripped breakers or even electrical fires.
With a subpanel, the load distribution within the woodworking shop can be fine-tuned and optimized. By connecting tools and machines to different circuits within the subpanel, woodworkers can spread the electrical load evenly across multiple branch circuits, reducing the chances of overloading any single circuit. This allows for a more balanced power distribution, improved operating efficiency of equipment, and enhanced safety within the woodworking shop..
Determining Power Requirements
When setting up a woodworking shop, it is crucial to assess the electrical needs of the space. The power demand of different tools used in woodworking, such as table saws, planers, and jointers, can vary significantly. Properly assessing these needs will ensure that the subpanel can handle the workload and prevent any potential electrical issues.
To determine the power requirements for a woodworking shop, several factors need to be considered. Firstly, you need to calculate the power demand of each individual tool based on its wattage or amperage rating. This information is usually found in the manufacturer’s specifications or on the tool itself.
Along with individual tool demands, you should also consider other factors that may affect power requirements in your shop. For example, if multiple tools are likely to be used simultaneously or if there are any other high-power equipment (such as dust collectors) that will be connected to the subpanel. It is important to account for these factors when calculating the overall power requirements.
Another important consideration is scalability. As your woodworking business grows or if you plan on adding new tools or expanding your operations in the future, it’s essential to estimate future power needs when deciding on a subpanel capacity. Investing in a subpanel with higher amperage than currently required can save you from having to upgrade again later.
Once you have determined your power requirements, you can begin selecting an appropriate subpanel that meets those needs. In the next section, we will discuss how to choose the right subpanel for your woodworking shop based on capacity specifications and other factors to consider.
– List of considerations when determining power requirements:
- Calculate individual tool power demands.
- Consider simultaneous use and additional high-power equipment.
- Estimate future power needs for scalability.
– Benefits of accurately assessing power requirements:
- Prevents overloading and electrical issues.
- Ensures efficient power distribution.
- Allows for future expansion.
– Importance of consulting an electrician:
- Professional guidance in determining power requirements.
- Ensures compliance with electrical codes and regulations.
- Expert knowledge in selecting appropriate subpanel capacity.
Selecting the Right Subpanel
Selecting the Right Subpanel: Choosing the Appropriate Subpanel for a Woodworking Shop
When it comes to setting up a woodworking shop, one crucial aspect is selecting the right subpanel. A subpanel serves as an electrical distribution point separate from the main panel, providing power to various circuits within the workshop. Choosing the appropriate subpanel is essential for meeting the electrical needs of your woodworking equipment and ensuring safety.
Capacity specifications and amperage ratings are important factors to consider when selecting a subpanel for your woodworking shop. The capacity of a subpanel indicates how much power it can handle, typically measured in amps. It is crucial to match the capacity of the subpanel with the total amperage demand of your woodworking tools to prevent overloading.
Additionally, space and future expansion should be taken into account when choosing a subpanel. Consider not only your current power requirements but also potential future needs as you add or upgrade tools in your workshop. Opting for a larger or expandable subpanel can save you from having to replace it down the line.
Two common types of subpanels available in the market are main lug panels and main breaker panels. Main lug panels do not have built-in circuit breakers and require an external disconnect switch, making them more economical but less convenient in terms of circuit protection. On the other hand, main breaker panels come with built-in breakers for each circuit and offer better protection against overloads.
It is advisable to consult with an electrician or qualified professional when choosing a subpanel for your woodworking shop. They can assess your specific requirements and recommend options that meet local codes and regulations while taking into consideration factors such as workspace layout, budget constraints, and any special needs unique to your operation.
Finding Space
Before installing a subpanel, consider where it will be located within your woodworking shop. The size of the panel itself will determine how much space you need. Ensure that there is enough room to accommodate the panel and provide easy access for maintenance or future expansion.
Future Expansion
When selecting a subpanel, it’s important to consider the potential for future expansion of your woodworking shop. If you foresee adding more tools or increasing power needs in the future, it may be wise to choose a larger capacity subpanel than what is currently required. This will save you from having to replace or upgrade the panel later on, resulting in cost savings and minimizing disruption to your workshop.
Wiring the Subpanel
Properly wiring a subpanel is crucial for ensuring the safety and functionality of your woodworking shop. Follow this step-by-step guide to ensure a proper installation:
- Gather necessary materials and tools: Before starting the installation, gather all the materials and tools you will need. This includes a subpanel with the appropriate capacity and amperage rating, electrical cables, wire connectors, circuit breakers, wire strippers, screwdrivers, and pliers.
- Determine the appropriate wire gauge: The size of the electrical cables you will need depends on the amperage of your subpanel and the distance between the main panel and the subpanel. Use a wire gauge chart or consult with an electrician to determine the correct wire gauge for your specific requirements.
- Safety precautions: Prioritize safety during the installation process. Make sure to turn off power at the main breaker before starting any work. Use personal protective equipment (PPE) such as insulated gloves and eyewear when handling electrical components.
- Install grounding and bonding: It is essential to properly ground and bond your subpanel to ensure safety. Connect a grounding electrode conductor from the grounding bar in your main panel to a grounding rod outside of your woodworking shop. Inside the subpanel, connect the bare copper wires from each circuit’s ground wire to the grounding bar.
- Connect hot wires: Strip back about ¾ inch of insulation from each hot wire in your electrical cable using wire strippers. Connect each hot wire to its corresponding bus bar in the subpanel using appropriate wire connectors or screws.
- Connect neutral wires: Similar to connecting hot wires, strip back insulation from each neutral wire in your electrical cable and connect them to their corresponding bus bar in the subpanel.
- Install circuit breakers: Based on your woodworking shop’s power requirements, install circuit breakers in the subpanel. Each circuit breaker should correspond to a specific tool or electrical load in your shop. Make sure to follow the manufacturer’s instructions for installation.
- Double-check connections and tighten all screws: Once all the wiring is complete, double-check all connections to ensure they are secure and tight. Loose connections can lead to fires or electrical problems.
Following these steps will help ensure a proper and safe wiring installation for your subpanel in your woodworking shop. However, if you are unsure about any part of the process, it is always recommended to seek professional guidance from a licensed electrician. They can provide expert advice and assistance to ensure that your subpanel is installed correctly and meets all safety requirements.
Sizing and Calculating Load
A crucial step in setting up a subpanel for a woodworking shop is ensuring that it can handle the workload. Properly sizing and calculating the load demands will help prevent overloading and ensure the efficient operation of your woodworking tools. This section will guide you through the process of determining the load requirements for your subpanel.
Woodworking Tool | Power Demand (Amps) |
---|---|
Table Saw | 15-20 Amps |
Planer | 12-15 Amps |
Jointer | 10-12 Amps |
When calculating power requirements, consider both the continuous load and the intermittent peak loads that each tool may generate. It’s important to note that most circuits in a woodworking shop are considered continuous loads, meaning they operate at their maximum capacity for three hours or more.
Apart from individual tool demand, other factors must be considered when determining power requirements. These include voltage drop considerations, available electrical service capacity, and any potential future expansion plans for your woodworking shop.
It’s crucial to estimate future needs when sizing your subpanel as well. You should consider any plans of adding new equipment or increasing usage in the foreseeable future. By accounting for scalability, you can avoid having to upgrade your subpanel sooner than necessary.
Calculating and sizing your load according to code standards, such as the National Electric Code (NEC), is essential. The NEC provides guidelines for load calculation methods and demand factors, which can help ensure that your subpanel can handle the anticipated workload without any issues.
To properly calculate the load, it’s recommended to consult a qualified electrician or refer to code resources for detailed instructions and examples. They will be able to guide you through the process and ensure that your calculations are done accurately and in compliance with electrical safety standards.
Safety Considerations
Woodworking shops can be potentially dangerous due to the use of heavy machinery and power tools. It is crucial to prioritize safety when setting up an electrical system in these environments. In this section, we will discuss the safety considerations that need to be taken into account when installing a subpanel for a woodworking shop.
One important aspect of safety is grounding and bonding requirements. Proper grounding helps prevent electrical shock by providing a safe path for electricity to flow in case of a fault. It is essential to ensure that the subpanel is properly grounded, along with all the equipment and machinery in the workshop. Additionally, bonding involves connecting metal parts together to create an equipotential plane, reducing the risk of electrical shock or other hazardous conditions.
Another safety measure that should not be overlooked is the installation of Ground Fault Circuit Interrupter (GFCI) protection. GFCIs are designed to quickly detect any imbalance in current flow and shut off power in order to prevent electric shocks. Installing GFCIs on circuits used for woodworking machines can significantly reduce the risk of accidents and injuries.
Furthermore, fire safety measures are crucial in woodworking shops where flammable materials may be present. It is important to have proper fire suppression systems, such as fire extinguishers or sprinkler systems, installed and easily accessible in case of emergencies. Implementing good housekeeping practices by keeping the work area clean and free from sawdust buildup can also minimize fire hazards.
Grounding and Bonding Requirements | GFCI Protection | Fire Safety Measures |
---|---|---|
Properly ground subpanel and equipment | Install GFCIs on circuits used for woodworking machines | Have fire suppression systems and extinguishers in place |
Ensure bonding of metal parts for equipotential plane | Reduce the risk of electric shock | Maintain good housekeeping practices to minimize fire hazards |
Troubleshooting and Common Issues
Once a subpanel is installed in a woodworking shop, it is important to be aware of potential issues that may arise. Being able to identify and resolve subpanel-related problems can help ensure the smooth operation of your woodworking equipment and promote a safe working environment. This section will address some common issues that may occur with subpanels and provide troubleshooting techniques to resolve these problems.
One common issue that woodworkers may encounter is circuit overload. This can happen when the electrical demand exceeds the capacity of the subpanel or specific circuits within it. An overloaded circuit can lead to tripped breakers, loss of power, or even electrical fires.
To troubleshoot an overloaded circuit, you should first identify which tools or equipment are causing the overload by disconnecting them one at a time. Once the culprit is identified, you can redistribute the load by connecting the equipment to different circuits or reducing the overall power demand by using more energy-efficient tools.
Another issue that may arise with subpanels is tripped breakers. A breaker trip occurs when there is a fault or excessive current flow in a circuit, causing the breaker to automatically disconnect and interrupt power supply. If a breaker trips frequently, it could indicate an underlying problem such as a short circuit, ground fault, or overloading.
To troubleshoot this issue, start by identifying which specific breaker is tripping and then inspecting the corresponding circuit for any signs of damage or faulty wiring. It may also be necessary to unplug any connected equipment to determine if they are causing the problem.
If you are unsure about how to troubleshoot or resolve subpanel-related problems on your own, it is recommended to seek professional help from a licensed electrician. They have the knowledge and expertise to diagnose complex issues and ensure that your electrical setup is safe and compliant with local regulations.
Additionally, they can provide guidance on preventive measures such as periodic maintenance and inspections to mitigate future problems. Remember, safety should always be the priority when it comes to electrical systems in a woodworking shop.
Conclusion
In conclusion, a dedicated subpanel is an essential component for a safe and well-functioning woodworking shop. By having a separate subpanel, woodworkers can ensure that their electrical setup is capable of handling the unique power demands of their tools and equipment. It also minimizes the risk of overloading the main panel, which can lead to electrical hazards and potentially even fires.
Throughout this article, we have discussed the basics of subpanels, including their purpose and how they differ from main panels. We have also covered important considerations such as determining power requirements, selecting the right subpanel, proper installation, sizing and calculating load demands, safety considerations, and troubleshooting common issues. Each step highlights the importance of a thorough understanding and adherence to proper electrical practices.
By carefully assessing power needs and selecting the appropriate subpanel with sufficient capacity and amperage ratings, woodworkers can ensure that their electrical system will meet current demands while allowing room for future expansion. Proper wiring, grounding, bonding, GFCI protection, and fire safety measures are also crucial aspects to be considered in order to provide a safe working environment.
However, it’s important to note that while this article provides valuable information on using a subpanel for a woodworking shop, it is not intended as a comprehensive guide. If you are unsure about any aspect of installing or maintaining your subpanel, it is strongly recommended to seek professional guidance. Electricians who specialize in woodworking shop setups will have the expertise necessary to ensure that your electrical system meets all safety standards and regulations.
Overall, by investing in a dedicated subpanel and following proper installation guidelines outlined in this article or with professional assistance when needed, woodworkers can enjoy peace of mind knowing that their electrical setup will support their woodworking operations safely and effectively.
Frequently Asked Questions
How many amps does a shop subpanel use?
The number of amps that a shop subpanel uses can vary depending on the specific needs and electrical demands of the workshop. Generally, a typical shop subpanel may range from 60 to 100 amps.
However, it is essential to consider the specific equipment and machinery present in the shop and calculate their respective power requirements to determine the appropriate ampacity for the subpanel.
What size electrical panel do I need for my shop?
The size of the electrical panel needed for a shop depends on various factors, such as the size of the workshop space, the type of machinery and equipment being used, and future expansion plans. A general guideline is to have a panel with a capacity ranging from 100 to 200 amps for an average-sized shop.
However, it is crucial to consult with a qualified electrician who can assess your specific needs and provide expert advice on determining the appropriate panel size for your shop.
How many amps does a small workshop use?
The amp usage of a small workshop can vary based on its activities and equipment. A small workshop typically utilizes around 30-50 amps or even less if it primarily consists of light-duty tools like hand tools or small woodworking equipment.
However, if heavy machinery or power-intensive tools are involved, it may require additional amperage capacity. It is always recommended to consult an electrician who can assess your specific equipment needs and ensure that your electrical system is adequately designed to handle your workshop’s power requirements.
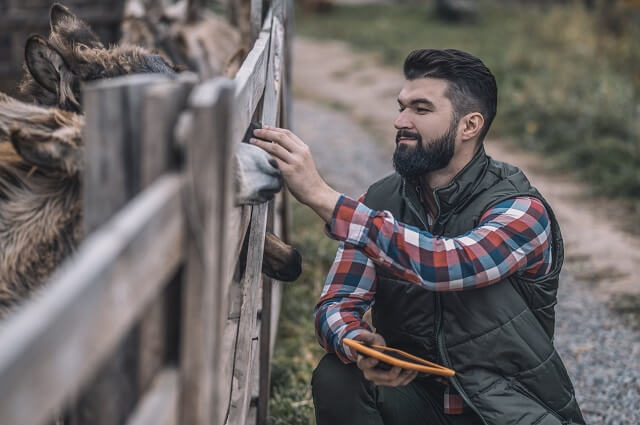
Hi everyone! I’m a woodworker and blogger, and this is my woodworking blog. In my blog, I share tips and tricks for woodworkers of all skill levels, as well as project ideas that you can try yourself.