Introduction
Woodworking is a craft and trade that involves the forming, cutting, shaping and treating of wood to make furniture, tools, art pieces and other items. Woodworking can be done by hand or with the help of machines. Woodworking machines are tools which are used to automate certain tasks involved in the woodworking process. These tasks can include shaping, drilling, boring, cutting and jointing.
Using machines in woodworking helps to improve accuracy in production of furniture or other items meant for sale. Furthermore, use of appropriate machines also increases productivity as it makes certain processes faster than performing them manually with hand tools. Additionally, powered machines reduce fatigue that is associated with doing manual work while still providing a high-quality finish to any piece being worked on. Moreover, the use of specialised power equipment lessens the time required for general wood preparation thereby making it easier for woodworkers to focus more on creative aspects rather than worry about perfecting details.
Handheld vs Machine
Handheld Woodworking Machines: Handheld woodworking machines have the advantage of being lightweight and portable. This allows you to move freely around your workspace and make smaller adjustments when creating intricate, detailed pieces of furniture. The downside is that you need to manually apply pressure in order to cut or shape material, which can increase fatigue and require more time than with a machine. Additionally, handheld tools may not be as precise in their measurements as those made with machines.
Machine Woodworking Machines: Machine woodworking machines offer increased precision and are generally much faster than handheld tools. This is especially beneficial for commercial grade projects where precision and speed are key elements for making sure deadlines are met. Unfortunately, machine woodworking machines also come at a higher cost due to their complex engineering which includes motors for power, advanced controls for accuracy and their own unique set of attachments or parts. Additionally, they require a large amount of space in the workspace due to their size which can limit mobility and access to tight spaces or corners.
Power Saws
Table saws are the most important woodworking machine for any woodworker. They can be used to make precise and straight cuts, as well as making angled cuts and creating unique designs with a variety of available blades. Table saws are especially useful for making miter, crosscut, rip cut, and rabbet cuts. The blades are either installed underneath the table or attached to an arm off the side of the base. Both types provide a great deal of power and accuracy but differ in design, portability, and capacity.
Band saws, like table saws, are used to make a variety of cuts depending on their design. These machines have one or two metal blades that rotate on a wheel or pulley system to create clean curves or angled edges into sheets of wood material. When using band saws with two blades you can also get interesting patterns which makes them perfect for cabinet-making and other intricate works.
Circular saws are powered electric tools used primarily for making more basic crosscuts and rip cuts without requiring an extensive setup like traditional table saws require. Their design is versatile enough that they can be mounted on an adjustable stand or set up onto a piece of support material while it spins around its blade at high speeds cutting through the chosen material in one quick action. Circular saws come in both corded (powered by electricity) and cordless (powered by battery) varieties so depending on your power supply needs one type may be more viable than another for your project needs!
Jointers and Planers
Jointers and planers are an essential tool for any woodworker. Jointers are used to create a flat surface on the edge of a board or panel by running it through a series of blades. Planers do the same but on the face of a workpiece.
The type of joiner or planer needed will depend on the woodworker’s needs and preferences. Generally, standard 6-inch jointers have enough power for most amateur woodworking projects and can be found at any hardware store. If more powerful jointers are needed, 8-inch models provide more power and come with additional features such as larger cutter heads, longer beds, adjustable fences and dust chutes. On the other hand, planers typically range in size from 12 to 48 inches depending on their application. Because they use greater force than jointers to plane the surfaces, they require more powerful motors; thus they come in various sizes to handle various weight capacities effectively. In addition to their size differences, planers also feature different tables, cutter heads and control systems depending on how advanced users want their planers to be. For instance, precision inserts can be replaced if desired to ensure accuracy when making certain cuts; higher end models offer digital readouts that display thicknesses before cutting; some planers have helical spiral cutters as discreet teeth configurations that offer superior finish/smoothness compared to traditional straight knives when cutting boards; and many electronic controls allow users flexibility in advance settings for degree control over tilt angles for added precision when profiles are designed into boards throughout their workshop tasks.
To help choose between these two popular woodworking machines, consider their intended purpose: if you need small workpieces thinned down or large panels flattened then choose a planer; but if you desire only slightly flatten surfaces along with small edgings then select a jointer as your go-to machine instead. Knowing this information helps shoppers pick which specific model make sense financially while addressing specific needs simultaneously whether being used within beginner or experienced workshops alike.
Drills
Impact drivers are a type of drill that is used for driving screws and fasteners. They use rapid, repetitive, hammer-like blows to drive them into materials with ease. Impact drivers are different than regular drills because they’re more powerful with greater torque. In order to generate higher torque in an impact driver, two sets of gears move inside the machine—one set moves very quickly and the other set moves very slowly. This rotating power creates a “hammering” action that drives screw or fastener into the material with great force.
Hammer drills, on the other hand, can cut through materials such as concrete and stone because they contain a special bit which forces the surface of the material into small fractures so it can be drilled through easily. Hammer drills also use rapid hammer-like blows and force the bit into the material in order to create pilot holes for screws or even larger holes for pipes, fixtures, or anchors in masonry walls and foundations. Unlike impact drivers, hammer drills have a strong rotation from its motor but no additional gearing mechanisms are applied so there is less torque available.
Routers and Lathes
Routers and lathes are two of the most commonly used woodworking machines. Routers are great for creating precise shapes and edges in wood, metal, plastic, and composite materials. They feature a powerful motor that drives a rotating bit or cutter that can be moved along the surface of the material to create unique textures, shapes, curves, holes, rabbets, recesses and intricate details. The cutting tool can be adjusted to create wider or narrower cuts depending on the desired result. Lathes are also very useful in woodworking projects as they make round objects from blocks of wood by spinning the block while a sharp cutting tool is moved slowly down its length to remove excess material. The speed at which it spins depends on the final item being crafted. Lathes offer immense control over detail when shaping such objects as table legs, chair spindles and baseball bats. When combined with other machines like band saws and drill presses, these two essential pieces of shop equipment can really help bring any project to life accurately and uniquely customized for any application.
Working With Composite Materials
When it comes to composite materials in woodworking, there is a variety of machines available to work with them. These include power saws, routers, planers and other furniture-making tools. The type of machine required for any given project will depend on the intended use of the material and its properties. A few examples of more common woodworking machines when working with composite materials are: table saws, miter saws, band saws, jointers, edge sanders and belt sanders. Table saws are commonly used to cut boards down to their desired dimension and make square edges; miter saws are used for making mitered pieces; band saws are best suited for cutting curves in thicker boards; jointers are utilized to flatten uneven edges or create flat joints in two pieces; edge sanders help maintain consistent thickness over the long length of a board; and finally belt sanders are used as a finishing tool to shape the surface texture into a smoother finish. Depending on the task in hand, one or several machines may be necessary. For example, if you’re creating an intricate chair frame from composite material such as carbon fiber reinforced plastic you would likely require multiple tools such as miter saws for cutting angles; grinding wheels for shaping curving surfaces; angle grinders for cutting paper-thin bars of fiberglass or Kevlar fabric; and various drill bits and chisels to further refine your project’s details. Each machine comes with its own learning curve but with practice they ensure that your pieces end up looking exactly how you imagined them!
Maintenance Tips
Regular maintenance is important to help ensure that your common woodworking machines perform optimally. To maximize performance and longevity, it is essential to follow a few simple maintenance tips:
-Keep machinery clean and free of dust, dirt, and debris. Cleaning should be done regularly using compressed air or soft brushes to gently brush away any buildup.
-Check the lubrication level in the bearings on all machines that utilize them. Add oil as needed to maintain proper lubrication levels so moving parts don’t suffer undue wear and tear over time. Always use the correct type of oil for your particular machine model.
-Monitor the tension levels on any belts or chains used by your woodworking machines. Make sure they are always at their recommended levels for optimal performance and wear.
-Inspect cutting tools for signs of dullness frequently. Change saw blades, drill bits, router bit shanks, etc., when necessary to maintain peak sharpness so you get the best cuts possible from each task.
-Maintain accurate alignment in all shafts and spindles within the machine itself. This can easily become misaligned due to vibration during operation or occasional bumps while handling or storing machinery components or accessories; make sure you check it regularly and realign if necessary before use every time.
Conclusion
In conclusion, when it comes to assigning the right woodworking machines to a particular job, it is important to first consider the type of project that needs to be done. From there, the amount of space available in the shop and the budget play an essential role in determining which machines may be best. Of course, safety should also not be overlooked—woodworking can sometimes involve a lot of power tools that need to be operated correctly for optimal protection. Taking all these pieces into consideration will ensure one gets maximum use out of their woodworking machines and produces high-quality results for any given project.
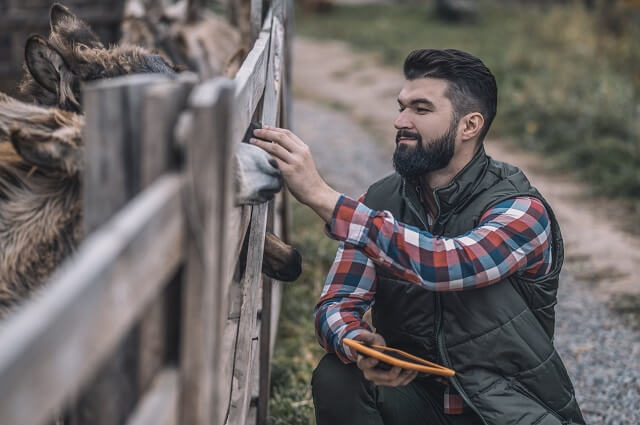
Hi everyone! I’m a woodworker and blogger, and this is my woodworking blog. In my blog, I share tips and tricks for woodworkers of all skill levels, as well as project ideas that you can try yourself.