Introduction to Custom Woodworking Machines
Custom woodworking machines are specially designed pieces of machinery that allow users to produce unique and intricate products from wood. They are often able to manipulate the materials in ways that would not be achievable with the use of standard power tools or by hand alone. The level of accuracy, repeatability, and control provided by custom woodworking machines makes them incredibly beneficial for a variety of projects.
These machines are typically found in specialized workshops due to their high cost compared to traditional tools. They also require extensive knowledge and understanding in order to be used correctly and safely. Some of the most common uses for custom woodworking machines include creating curves, carving decorative details, making precise cuts, separating joints, planes, saws, routers and drills.
Regardless of the type or complexity of project undertaken with a custom woodworking machine, all can benefit from their use as they provide complete control over every step of creation while speeding up production processes significantly.
Different Types of Custom Woodworking Machines
Woodworking machines have become increasingly popular in the capital-intensive and skill-based craftsmanship sector. With the right devices and tools, one can easily create furniture pieces, cabinetry, doors, frames, countertops and flooring. As many custom woodworking projects are highly specific to a consumer’s needs and desires, customized woodworking machines offer manufacturers a level of precision that is unmatched by other types of production machines.
Examples of different types of custom woodworking machines include: routers, lathes, jointers, mills and band saws. Routers are power tools used to shape the outside or interior surface of an object. Lathes operate with a tool mounted onto its headstock to shape stock that is held in place by its tailstock. Jointers involve running boards through cutters which flatten them for joining purposes; these are used for large panels such as table tops. Mills involve large cutting heads which move up and down at various angle to cut grooves or other shapes out of materials such as plastic or aluminium. Band saws consist of two rotating wheels connected by a steel band which moves reciprocally back and forth from wheel to wheel; this enables curved cuts in woods that would otherwise be impossible with straight blades tools.
The size and capability of customized woodworking machines vary drastically depending upon what is needed for each individual project. For instance, some high speed industrial robots may be able to create complex cabinets with due speed while others may take much longer in order to complete such tasks as drilling or routing intricate details on an object. It is also important to consider how compatible these devices are when using modern CNC technologies like CAD/CAM software programs; if they do not support the latest versions then they may require extra programming in order to ensure they accurately track every movement made by their operators within millimeters or even microns without error.
Advantages of Custom Woodworking Machines
Custom woodworking machines can be a great advantage to businesses in the woodworking industry. They allow businesses to increase their production speed and efficiency, which can result in greater profits and improved customer satisfaction. Custom woodworking machines also allow for the creation of custom designs, rather than relying on existing templates or machinery for production. These custom designed products can provide a unique look and style that will stand out from other companies who are using pre-fabricated machinery.
Additionally, having access to custom woodworking machines allows businesses to better troubleshoot any issue that may arise during their production process, as each machine can be tailored to fit a particular operation or environment. The flexibility and freedom provided by custom machines also makes it easier for a business to experiment with different techniques and materials to produce a higher quality product, often leading to greater innovation within the industry.
How to Select a Custom Woodworking Machine
When selecting a custom woodworking machine there are many factors to consider. The most important of these is the budget: be sure to determine the amount of money you are willing to spend on the machine. Size is another important factor; this will help you determine what type of woodworking machine is best suited for the job. Increased power and enhanced features could provide greater capabilities, but also cost more money.
Other factors to consider when selecting a custom woodworking machine include ease of use and durability. Be sure to read reviews from other users who have already tested out the particular machine, as this could give insight into how easy it is to set up and use as well as its overall quality. Additionally, additional features might make a big difference when it comes to taking on large scale projects or making intricate designs, so research should be done thoroughly before deciding on a machine.
Finally, it’s important to look into any servicing requirements prior to purchasing a custom woodworking machine. Consult with the manufacturer or sales representative about service contracts available for purchase that cover any necessary repairs or parts replacement, which could save you time and money down the line if your machine ever breaks down or malfunctions in any way.
How to Properly Operate Custom Woodworking Machines
Step-by-Step Operation of Custom Woodworking Machines:
1. Before starting the machine, make sure all safety guards are in place and all parts are functioning properly.
2. Familiarize yourself with the machine’s user manual to identify any necessary adjustments before starting it up.
3. Wear personal protective equipment such as gloves,Safety glasses, and a dust mask when operating the machine to prevent any particles from coming in contact with your skin or eyes.
4. Turn on the power switch and wait for the motor to reach full speed before introducing material into its feed rollers, if applicable.
5. Introduce wood pieces that meet your specific project requirements into the machine’s cutting path. Make sure to place them so that their grain direction follows the intended cutting pattern for most efficient results.
6. If you are making a repetitive cut, adjust the cutting depths appropriate for each pass according to your desired results or the project requirements configured in the user manual of the machine respectively.
7. Monitor long feeding pieces closely as they go through to ensure accuracy and avoid kickbacks caused by overfeeding or irregular surfaces presented by longer boards which might cause malfunctioning during operation and unnecessary damages caused by abnormally high stress levels placed on them during passing through saw blades or other cutters being used in accordance with your machining needs at this stage of production run cycle common cuts made using custom woodworking machines include straight-line ripping, crosscutting, rabbeting and grooving Cuts can be made against straight edges — against fences bolted onto moving tables powered by motors configured accordingly—and bullnose bits can be deployed where appropriate for decorative profiles requiring finer tolerances performance outputs and accurate specs which might not always be achieved when dealing with very hard woods that surpass regular tensile strength of lumber used day to day hence impeding making more detailed cuts while dealing with these types of materials either manually deployed routers or CNC machines should be considered sensible alternatives particularly under extreme conditions beyond limits handled efficiently regarding output per hour production cycles commonly required when creating prototypes destined for mass market something like cabinet doors could easily require multi-pass precision operation involving four stages – grooving panels first then deep rabbit cutting , shaping door frames afterwards followed by mortising hinges respective holes precisely sited around components later checking for quality control finally before considering products ready and sent out
How to Troubleshoot and Repair Custom Woodworking Machines
One of the most common problems people experience when using custom woodworking machines is that their machines are not correctly aligned. This can be caused by improper assembly, loose hardware, or wear and tear over time. To address this issue, perform a visual inspection of all mechanical parts to ensure they are properly seated and tightened, as well as regularly inspect the machine for signs of wear. If necessary, use a level and ruler to re-align any necessary components that may have shifted over time or through normal wear and tear.
Another frequent problem with custom woodworking machines is inadequate lubrication or the wrong type of oil being used. To prevent this from occurring, always reference your machine’s user manual to make sure you are using the correct type of lubricant or oil for proper performance. Additionally, regular maintenance checks should be performed to make sure all moving parts are properly oiled.
Finally, custom woodworking machines sometimes experience motor malfunction. This issue can be caused by a number of issues like faulty wiring or worn out motors due to overuse. To combat this issue, use a multimeter to test for issues in electrical wiring within the machine itself and replace any frayed wires that may have been damaged by age or wear and tear. If there’s no fault found in your wiring then it’s likely time for replacing your motor entirely since it has reached its end-of-life stage.
Tips for Maintaining Custom Woodworking Machines
Custom woodworking machines are designed to last, but as with any device, proper maintenance will help ensure machine longevity and optimal performance. Here are some tips for keeping your custom woodworking machine running smoothly.
1. Clean your machine regularly. Remove all sawdust, dirt, and debris— particularly from moving parts and controls— using a soft cloth and a vacuum cleaner with an attachment that is specifically designed for cleaning machines.
2. Lubricate components on the machine after each use; this should include the pulleys on belt-driven machines, bases and guideways that panels slide along, and cutting tools (if they’re powered by an electromechanical motor). Regularly inspect components to identify wear spots that need lubrication or require replacement.
3. Store your custom woodworking machine in a climate-controlled area, away from moisture and dust which can cause damage over time. Direct sunlight should be avoided too since it could impact the temperature of the machinery over time – battery-powered motors can be especially sensitive to extreme temperatures changes.
4. Replace dust bags when recommended to prevent particles from entering the system, which can lead to build up in sensitive areas and impede performance or cause damage over time if left unchecked.
5. Maintain a regular service schedule; depending on how often you use your custom woodworking machine, you may want to enlist a professional to give it a thorough examination once ayear or every six months – depending on frequency of usage-to identify small potential problems or worn out parts before they become bigger health risks for your workers or costly repairs down the line for you.,
Conclusion
Custom woodworking machines have become increasingly important for those who want to produce custom furniture, cabinetry, and other wooden products. These tools are often used in cabinet-making shops, as well as many large industrial settings. The use of these machines also makes it easier for small businesses to create unique pieces of art. They can cut through materials much faster than manual hand tools, making production much more efficient. Custom woodworking machines enable makers to easily create complex shapes and textures, which can make all the difference in the finished product. Additionally, these machines provide precision and repeatability that is often hard to match manually.
In conclusion, custom woodworking machines offer a variety of advantages to both makers and industry professionals alike – they are fast, reliable, and precise. With these tools at their disposal, shop owners and makers alike can produce beautiful and intricate works crafted with precision – all while saving time and energy.
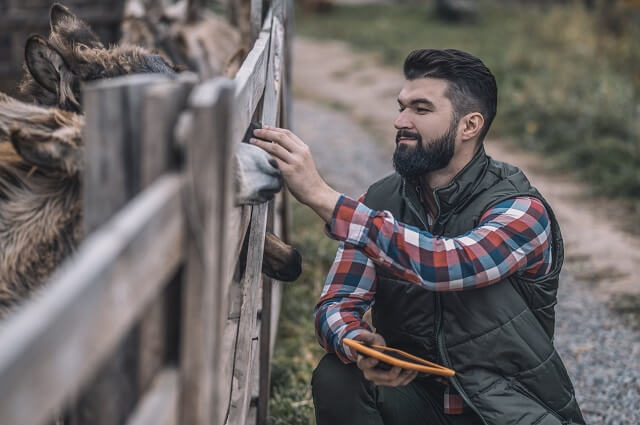
Hi everyone! I’m a woodworker and blogger, and this is my woodworking blog. In my blog, I share tips and tricks for woodworkers of all skill levels, as well as project ideas that you can try yourself.