Woodworking is a craft that has been practiced for centuries, with its roots dating back to ancient civilizations. Throughout history, craftsmen have relied on the use of hand tools to shape and manipulate wood into functional objects and stunning works of art. However, with the advent of power tools in the modern era, the traditional methods and techniques of woodworking have significantly shifted.
In this article, we will embark on a journey through time to explore how craftsmen achieved intricate woodwork before the invention of power tools. We will delve into the historical significance of woodworking and its reliance on hand tools, as well as highlight the curiosity surrounding this age-old craft.
Before power tools became commonplace, woodworkers had to rely on early hand tools to conduct their trade. These primitive tools included hand saws, chisels, planes, and braces. With these basic implements, craftsmen demonstrated exceptional craftsmanship and precision in their work. We will delve into these early hand tools and unravel the skill required to achieve seamless joints and smooth surfaces.
Joinery techniques played a crucial role in woodworking before power tools dominated the industry. Through methods such as dovetailing, mortise and tenon joints, and tongue and groove connections, craftsmen were able to create strong and enduring structures without relying on automated machines. We will examine these joinery techniques in detail, shedding light on the meticulousness needed to achieve such remarkable craftsmanship.
By exploring how woodworkers achieved extraordinary feats before power tools revolutionized their trade, we can gain a deeper appreciation for their skill and ingenuity. Join us as we uncover the secrets behind traditional woodworking methods that are still cherished today for their artistry and timeless beauty.
Early Hand Tools of Woodworking
Before power tools became commonplace in woodworking, craftsmen relied on a variety of hand tools to shape and manipulate wood. These early hand tools served as the foundation for woodworking practices that have endured for centuries. Understanding the primitive tools used by ancient woodworkers provides insight into the craftsmanship and skill required to achieve intricate woodwork.
The use of hand saws, chisels, planes, and braces was central to traditional woodworking. Hand saws were essential for cutting through wood, with different types of saws designed for specific purposes such as crosscutting or ripping. Chisels were used for carving out precise shapes or cutting grooves, while planes were employed to smooth surfaces or create beveled edges. Braces functioned as manual drills, allowing craftsmen to create holes for joinery or other purposes.
Working with these early hand tools required a high level of precision and patience. Craftsmen had to rely entirely on their own skills and expertise to achieve desired results. Carving delicate details or creating seamless joints demanded meticulous attention to detail and a deep understanding of the properties of wood. The mastery of these early hand tools allowed artisans to create beautiful furniture pieces, architectural elements, and decorative objects that have stood the test of time.
While power tools have largely replaced many traditional hand tools in modern woodworking practices, there is still much that can be learned from studying these historic techniques. The craftsmanship and precision achieved with early hand tools remain highly regarded in today’s woodworking community. By appreciating the artistry involved in using these primitive implements, we gain a deeper understanding of the evolution of woodworking and can incorporate aspects of this heritage into our own contemporary projects.
- Hand saws
- Chisels
- Planes
- Braces
Joinery Techniques
In the world of woodworking, joinery refers to the art and skill of creating strong and enduring connections between pieces of wood. Before the advent of power tools, craftsmen relied solely on their mastery of joinery techniques to create solid wooden structures. This section explores the various methods and meticulousness involved in achieving seamless joints by hand.
One of the most well-known and revered joinery techniques is the dovetail joint. This method involves interlocking wedge-shaped tenons with corresponding mortises, creating a connection that is not only strong but also visually appealing. The precision required to create tight-fitting dovetails by hand is truly remarkable, as it demands careful marking, sawing, and chiseling to achieve perfect mating angles.
Another classic joinery technique is the mortise and tenon joint, which has been used for centuries in furniture making and architectural structures. This method involves cutting a rectangular hole (mortise) into one piece of wood and forming a corresponding protrusion (tenon) on another piece of wood to fit snugly within the mortise. The key challenge lies in accurately shaping the tenon and ensuring it fits perfectly into the mortise without any gaps or looseness.
Additionally, tongue and groove joints have long been utilized in woodworking to create flush surfaces between two pieces of wood. This technique involves cutting a groove (slot) into one piece of wood that matches perfectly with a corresponding tongue (protrusion) on another piece of wood. The strength of this joint comes from its interlocking nature, which provides stability even without adhesive or fasteners.
Mastering these traditional joinery techniques requires patience, precision, and a keen eye for detail. Craftsmen would often spend years perfecting their skills in order to create structurally sound connections that could withstand the test of time. Even today, many modern craftsmen choose to learn these traditional techniques and incorporate them into their work as a way to honor the art of woodworking.
Overall, joinery without power tools demonstrates the true essence of craftsmanship in woodworking. The skill required to create seamless connections by hand is something that should not be underestimated or overlooked. In a world driven by advancing technology, it is important to acknowledge and appreciate the artistry and dedication involved in mastering these ancient joinery techniques.
Shaping Wood
In the world of woodworking, shaping wood is an essential aspect of creating beautifully crafted pieces. Before the advent of power tools, hand planes and chisels played a crucial role in achieving smooth and flawlessly curved surfaces. This section will examine the importance of hand planes and chisels in shaping wooden surfaces, analyze the technique and precision needed to create these surfaces, and discuss the versatility and application of different types of planes and chisels in woodworking.
Hand planes are one of the oldest woodworking tools used for shaping wood. They consist of a sharp blade set into a flat base, commonly referred to as a sole. The blade is adjusted using a screw mechanism to control the depth of cut.
By pushing or pulling the plane along the surface of the wood, craftsmen can remove excess material, flatten uneven areas, or create beveled edges. Hand planes come in various sizes and shapes, each designed for different purposes. For example:
- Block planes: These small, compact planes are ideal for fine finishing work and end grain.
- Jack planes: With their longer soles and larger blades, jack planes are versatile tools suitable for general-purpose smoothing tasks.
- Jointer planes: These longer planes excel at flattening long boards or creating precision edges.
Chisels also play a vital role in shaping wood by allowing craftsmen to remove material with precision. They are used for various purposes such as cutting mortises or carving intricate details. Chisels consist of a sharp metal blade with beveled edges that is attached to a handle for easy manipulation. To ensure clean cuts without splintering or tearing the wood fibers, it is essential to use chisels with extremely sharp blades. Different types of chisels include:
- Bench chisels: These general-purpose chisels come in various sizes and are commonly used for many woodworking tasks.
- Mortise chisels: Designed specifically for cutting mortises (rectangular holes), these chisels are thicker and more robust than bench chisels.
- Carving chisels: With their specialized shapes and profiles, carving chisels enable craftsmen to create intricate designs and sculptures.
Using hand planes and chisels requires a high level of skill and precision. Woodworkers must have a deep understanding of wood grain direction, cutting angles, and the properties of different types of wood.
They carefully adjust blade depth, maintain sharp edges on their tools, and rely on their keen senses to guide them as they shape the wood. While power tools have made woodworking more efficient in certain aspects, many artisans still prefer using hand planes and chisels for their ability to provide greater control, produce finer details, and achieve superior craftsmanship.
In the next section, we will explore the world of wood carving and the tools employed by early craftsmen for creating intricate designs.
Carving
Carving is a woodworking technique that allows craftsmen to create intricate and detailed designs on wooden surfaces. Before the advent of power tools, woodcarving was done entirely by hand using a variety of specialized tools. This section will delve into the world of wood carving and explore the tools employed by early craftsmen to achieve their artistic visions.
Unveiling the World of Wood Carving
Wood carving is an art form that dates back thousands of years, with examples found in ancient Egyptian tombs and classical Greek sculptures. Early woodworkers used a range of hand tools to bring their designs to life. Gouges were one of the most essential tools, featuring a curved blade that allowed artisans to remove material efficiently.
Carving knives, with their sharp and pointed blades, were used for more delicate and intricate cuts. Mallets were also commonly employed, providing the necessary force for driving chisels and gouges into the wood.
The Skill and Artistry Involved
Carving intricate designs by hand requires both patience and skill. Craftsmen must envision their design in advance, considering both the overall composition and fine details they wish to incorporate. Each cut made with a carving tool must be deliberate and precise, as any mistake can be difficult or impossible to correct. The depth and angle of each cut are crucial in creating dimensionality within the design.
Wood carving is not merely about removing excess material; it is an art form that involves understanding the grain direction of the wood, highlighting natural patterns and textures, and achieving smooth surfaces. The ability to manipulate light through careful carving adds depth and nuance to finished pieces.
The Revival of Hand-Carved Woodwork
In recent years, there has been a resurgence in interest and appreciation for traditional woodworking techniques, including hand carving. Many artisans are drawn to these methods because they allow for a more intimate and hands-on approach to the craft. Hand-carved woodwork possesses a unique beauty and character that cannot be replicated by power tools.
Moreover, there is an increasing appreciation for the sustainability aspect of traditional woodworking techniques. By relying on hand tools instead of power tools that consume electricity and produce waste, craftsmen can create beautiful pieces while minimizing their impact on the environment.
Artisans specializing in hand carving can be found around the world, creating breathtaking sculptures, intricate furniture details, and decorative elements. Their dedication to preserving these ancient techniques ensures that the art of hand-carved woodwork continues to thrive and inspire new generations of craftsmen.
Finishing Touches
When it comes to achieving a professional finish, hand sanding and polishing techniques play a crucial role in woodworking. While power tools have simplified the process, there is still a place for traditional hand methods that allow for precision and attention to detail.
Describing the hand sanding and polishing techniques
Hand sanding involves the use of sandpaper or abrasive pads to smooth wooden surfaces. It allows woodworkers to refine edges, eliminate imperfections, and prepare the wood for staining or finishing. The key to successful hand sanding lies in choosing the right grit of sandpaper and exerting consistent pressure while moving in the direction of the grain. Coarser grits are used for removing rough marks and scratches, while finer grits are employed for achieving a smooth finish.
Polishing is the next step after sanding that brings out the natural beauty of wood. This can be done by applying different types of compounds such as wax, oil, or varnish with soft cloths or brushes. The goal is to create a shine while providing protection against moisture and wear. Hand polishing allows woodworkers full control over the application process, ensuring an even distribution of polish and highlighting any intricate details.
Exploring the use of different grits of sandpaper and polishing compounds
In woodworking, a range of grits is available, from coarse (40-60) to extra fine (600-1200). Coarse-grit sandpaper removes material quickly but leaves visible scratches on the surface. As you progress towards finer grits, these scratches become less noticeable until they eventually disappear. The final step involves using ultra-fine grits for creating a mirror-like sheen on wood surfaces.
Polishing compounds come in various forms such as pastes or liquids with different levels of abrasiveness. Wax-based polishes provide a natural look and a soft sheen, while oil-based products offer more durability and can enhance the wood’s natural color. Varnishes and shellacs provide a protective layer on wood surfaces and can be applied by hand to achieve excellent results.
Elucidating the level of precision and attention to detail involved in achieving professional finishes
Hand sanding and polishing require patience, skill, and an eye for detail. Woodworkers must maintain consistent pressure while sanding, carefully monitoring the progress to avoid over-sanding or creating uneven surfaces. When it comes to polishing, each stroke must be deliberate and even to ensure an impeccable finish.
Achieving professional finishes through hand techniques takes time and practice. Evenly sanding large areas or intricate details requires a meticulous approach. It is important to remember that rushing through this process can result in subpar results, diminishing the overall quality of the woodworking project.
By employing traditional hand sanding and polishing techniques, woodworkers have greater control over their final product, ensuring that it meets their exact standards. The craftsmanship involved in manually finishing wood surfaces not only enhances its appearance but also preserves the artistry of handcrafted woodwork.
Efficiency and Speed of Hand Tools
In the world of woodworking, power tools have become increasingly prevalent, offering greater convenience and speed in completing various tasks. However, it is a misconception to believe that hand tools are less efficient and slower than their powered counterparts. In fact, hand tools often outperform power tools in certain woodworking tasks due to their simplicity, portability, and quiet operation.
One major advantage of using hand tools is the level of control they offer. By using hand saws, chisels, planes, and other manual instruments, craftsmen can have complete precision over their work. This level of control allows for intricate and detailed woodwork that may not be easily achieved with power tools. For example, delicate carving or joinery work often requires the finesse that only a skilled craftsman can achieve by using hand tools.
Hand tools are also highly portable compared to bulky power tools. In situations where woodworking needs to take place on-site or in a location without electricity access, hand tools are indispensable. Carpenters and woodworkers who specialize in construction or restoration work on historical buildings find that relying on traditional hand tools is essential for adapting to different environments and ensuring quality craftsmanship.
Furthermore, working with hand tools can be quieter than using power tools. This is advantageous in settings where noise pollution should be minimized such as residential areas or shared workshops. The ability to work quietly not only benefits woodworkers but also their fellow craftsmen or neighbors nearby.
Reviving Traditional Woodworking Techniques
In recent years, there has been a noticeable revival in the popularity of traditional woodworking techniques. Despite the convenience and efficiency of power tools, many craftsmen and woodworking enthusiasts have chosen to embrace the old-fashioned methods that were employed before the advent of power tools. This resurgence can be attributed to a variety of factors, including an appreciation for craftsmanship, a desire for sustainability, and a sense of connection to history.
One of the primary reasons behind the revival of traditional woodworking techniques is the appreciation for craftsmanship. In a world where mass-produced items dominate the market, handmade wooden objects stand out as unique and truly one-of-a-kind. The careful attention to detail and the human touch that goes into each piece make them highly valued by discerning consumers who seek authenticity in their surroundings.
Furthermore, there is a growing desire for sustainability among woodworkers. When power tools are used extensively, they consume energy and produce noise and air pollution. The use of hand tools eliminates these negative environmental impacts, making traditional woodworking techniques more eco-friendly. Additionally, hand tools rely on manpower instead of electricity, allowing woodworkers to connect with nature and work at their own pace.
Prominent workshops and individual artisans around the world have embraced traditional hand tools and techniques in order to preserve this rich heritage. These modern practitioners are not only skilled craftspeople but also passionate advocates for the beauty and artistry of handmade wooden objects. They offer classes and workshops where both beginners and experienced woodworkers can learn traditional skills from master craftsmen.
Through reviving traditional woodworking techniques, these artisans hope to inspire others to appreciate the value of handcrafted woodwork and promote its preservation in today’s fast-paced world dominated by technology. By honing their skills with primitive hand tools such as saws, chisels, planes, braces, gouges, carving knives, mallets, sandpaper templates and polishing compounds for finishes they are able to create seamless joints without the help of power tools.
By embracing traditional woodworking methods, craftsman can create meaningful connections to the past and carry forward centuries-old techniques into the future of woodwork.
Traditional Woodworking Techniques | Benefits |
---|---|
Craftsmanship | Unique and one-of-a-kind pieces that stand out in a mass-produced world. |
Sustainability | Eco-friendly practices that eliminate noise and air pollution associated with power tools. |
Preservation of heritage | Maintaining and passing on centuries-old woodworking techniques. |
Conclusion
In conclusion, the journey of woodworking before power tools is a testament to the enduring artistry and craftsmanship of traditional handcrafted woodwork. Through exploring the historical significance of woodworking tools and techniques, we have gained a deeper appreciation for the skill and precision required to achieve intricate woodwork without the aid of modern machinery.
From the early hand tools of woodworking to mastering joinery techniques, shaping wood, carving intricate designs, and applying finishing touches, craftsmen of the past showcased their talent through their meticulous attention to detail. Despite the advancements in technology that have made power tools more efficient and faster, there is still a place for traditional woodworking methods in today’s world.
The revival in popularity of traditional woodworking techniques speaks volumes about our society’s appreciation for craftsmanship and a desire for sustainability. Modern workshops and artisans who specialize in using hand tools showcase the beauty and artistry that can be achieved through these traditional methods.
As we move forward in a technologically advanced world, it is crucial to remember and preserve the art of handcrafted woodwork. By encouraging further exploration and appreciation for traditional woodworking techniques, we can ensure that this timeless craft continues to thrive, providing us with beautifully crafted works of art that will be cherished for generations to come.
Frequently Asked Questions
What did they use before power tools?
Before the invention of power tools, people relied on hand tools to accomplish various tasks. These hand tools were predominantly made of metal or wood and required physical exertion to operate. For shaping and smoothing wood, hand planes and chisels were widely used.
Axes and saws were employed for cutting down trees and working with larger pieces of timber. Additionally, hammers, mallets, and chisels were commonly used for carving intricate designs or details onto wooden surfaces. While these manual tools required substantial effort and time to use effectively, they were the primary means for working with wood before power tools became widely accessible.
How did people drill before power tools?
In the absence of power tools, drilling holes in materials such as wood was achieved through a process known as bow drilling. This technique involved using a bow-shaped apparatus consisting of a string or cord attached to a wooden spindle with a drill bit at the end. To operate this primitive drill, one person would hold the handle while applying downward pressure on the wooden spindle against the material being drilled.
At the same time, another person would rapidly move the bow back and forth, causing the string to rotatthe spindle while maintaining tension on it. This rotational motion generated enough friction between the drill bit and material to gradually create a hole over time.
How was wood cut in ancient times?
Wood was cut in ancient times using an assortment of manual methods that varied depending on cultural practices and available resources. One prevalent method involved using axes to fell trees by repeatedly striking at their base until they toppled over. Afterward, different types of saws were employed to transform fallen trees into smaller pieces suitable for various applications like construction or crafting.
These saws could be reciprocating saws where the blade moved back-and-forth manually or frame saws where multiple craftsmen coordinated their efforts to operate large frame-mounted blades together. Additionally, chisels and adzes played important roles in shaping or sculpting wood by removing excess material through carefully controlled cutting and carving actions. The ancient techniques for cutting wood required immense skill, strength, and patience, reflecting the resourcefulness and craftsmanship of people in earlier times.
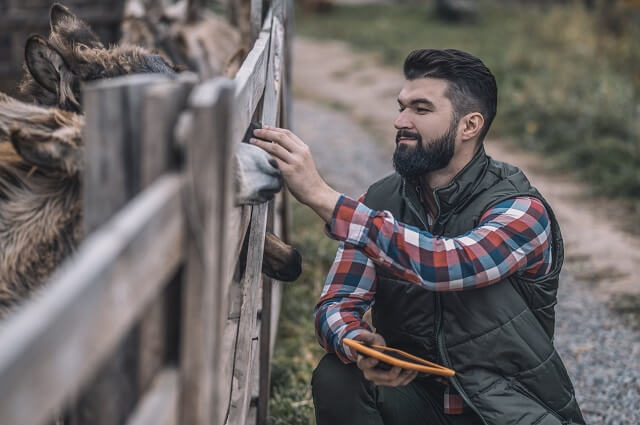
Hi everyone! I’m a woodworker and blogger, and this is my woodworking blog. In my blog, I share tips and tricks for woodworkers of all skill levels, as well as project ideas that you can try yourself.