Woodworking is a craft that requires precision and attention to detail, especially when it comes to copying curved surfaces. Whether you are a seasoned woodworker or just starting out, knowing how to accurately copy these shapes is essential for achieving seamless craftsmanship in your projects. This article will guide you through the process of copying curved surfaces for woodworking and provide helpful tips and techniques to enhance your skills.
One of the major benefits of copying curved surfaces in woodworking is the ability to enhance precision. By accurately tracing and transferring these shapes, you can ensure that your workpiece maintains its desired form throughout the entire project. This is particularly important when working on intricate designs or furniture pieces that require flawless curves. Additionally, copying curved surfaces allows you to achieve seamless craftsmanship, resulting in a finished product that looks professional and visually appealing.
To successfully copy curved surfaces, it is important to have the right tools and materials. In this article, we will provide a comprehensive list of the necessary tools along with detailed explanations of their purpose. From templates and French curves to flexible rulers, each tool plays a crucial role in helping you accurately replicate curves onto your workpiece. It’s essential to understand how each tool works and when it should be used in order to achieve the best results.
In the next sections, we will delve into step-by-step instructions on different techniques for tracing and transferring curved surfaces. Whether it’s using templates or utilizing advanced measuring tools like 3D scanning technology, we will discuss various methods that cater to different project complexities and personal preferences. We will also provide expert advice and insights on common challenges faced during the copying process, along with troubleshooting tips to help you overcome these hurdles.
By mastering the art of copying curved surfaces in woodworking, you can elevate your skills as a woodworker and create stunning projects with professional results every time. So let’s dive into this guide and explore the world of accurately replicating those beautiful curves onto your workpieces.
The benefits of copying curved surfaces for woodworking projects
Woodworking is a craft that requires precision and attention to detail. When it comes to working with curved surfaces, accurately copying the shape becomes even more important. This section will delve into the benefits of copying curved surfaces for woodworking projects, focusing on how it enhances precision and achieves seamless craftsmanship.
Enhancing Precision
One of the primary benefits of accurately copying curved surfaces in woodworking is that it enhances precision. Whether you are creating intricate moldings, shaping furniture components, or crafting decorative pieces, replicating curves with exactness ensures that the end result meets your design specifications.
Copying curved surfaces allows woodworkers to maintain consistency throughout a project and achieve precise fits when joining different elements together. By carefully tracing and transferring the desired curve onto another piece of wood, craftsmen can ensure that all components align seamlessly during assembly. This level of precision not only improves the overall aesthetics but also contributes to the structural integrity of the finished piece.
Achieving Seamless Craftsmanship
Another significant benefit of copying curved surfaces in woodworking is achieving seamless craftsmanship. Whether you are building a chair, table, or any other piece with curved elements, accurate replication ensures that each part looks coherent and harmonious.
When curves are flawlessly copied from one surface to another, it eliminates any visible discrepancies between various parts of a project. Seamless transitions between curves create a sense of continuity and flow within the design and contribute to a polished final result that exudes quality craftsmanship.
Moreover, copying curved surfaces enables woodworkers to replicate traditional designs with historical value or recreate specific styles prevalent in certain periods. For those working on restoration projects or aiming for authentic reproductions, accurate replication allows them to capture the essence of original designs and recreate their beauty faithfully.
Tools and materials required for copying curved surfaces
Copying curved surfaces in woodworking requires specific tools and materials to achieve precise results. Here is a comprehensive list of the essential items you will need, along with a detailed explanation of each tool’s purpose:
- Templates: Templates are pre-cut shapes made from durable materials such as plywood or acrylic. They are used to trace the desired curve onto the workpiece. Templates come in various sizes and shapes, allowing you to replicate curves accurately. They are especially useful when copying repetitive curves.
- French Curves: French curves are flexible drafting tools with smooth, irregularly shaped edges. They are commonly used in woodworking to trace or draw freehand curves. French curves come in different sizes, providing versatility for copying various curve profiles.
- Flexible rulers: Flexible rulers, also known as contour gauges or profile gauges, are made of flexible metal or plastic strips that can be molded to match the curvature of the surface being copied. By pressing the ruler against the curved surface, you can create an exact replica on your workpiece.
- Compass: A compass is a device consisting of two arms joined by a pivot point and a needle at one arm’s end. It is commonly used for drawing circles but can also be used for tracing curves on woodworking projects.
- Calipers: Calipers are measuring instruments with adjustable jaws used for taking precise measurements of distances between two points or diameters of cylindrical objects. When copying curved surfaces, calipers help measure key points on the original surface and transfer them accurately to the workpiece.
- Pencil or marker: A pencil or marker is essential for transferring the traced lines from templates, French curves, flexible rulers, or calipers onto the workpiece.
- Sandpaper: After transferring the shape onto your workpiece, sandpaper is needed to refine and smooth out any rough edges or imperfections. It helps achieve a seamless finish on the copied curved surface.
- Safety equipment: Always ensure you have proper safety equipment, such as safety glasses and hearing protection, when working with tools and machinery in woodworking.
Using the right set of tools and materials is crucial for accurately copying curved surfaces in woodworking projects. Each tool serves a specific purpose, allowing you to replicate curves with precision and achieve seamless craftsmanship. Now that we have covered the necessary tools and materials needed, let’s move on to the next section – Preparing the workpiece.
Preparing the workpiece
Preparing the workpiece is a crucial step in ensuring a smooth and successful copying process for curved surfaces in woodworking. By taking the time to properly prepare the workpiece, woodworkers can minimize errors and achieve more accurate results. In this section, we will explore the necessary steps to follow when preparing the workpiece for copying curved surfaces.
Cleaning and smoothing the surface
Before starting the copying process, it is important to ensure that the surface of the workpiece is clean and smooth. Any imperfections or debris on the surface can affect the accuracy of the tracing or transferring. To clean the surface, use a soft cloth or brush to remove any dust or particles.
If there are any rough areas or bumps on the surface, use sandpaper to smooth them out. It is important to pay attention to detail during this step as even small irregularities can impact the final result.
Securing the workpiece
To effectively trace or transfer a curved surface, it is essential to secure the workpiece in place. This prevents any movement or shifting that could lead to inaccuracies during the copying process. One common method for securing a workpiece is using clamps.
Place clamps strategically around the perimeter of the workpiece to hold it firmly in place on your workstation. Make sure that it is secured tightly but be careful not to apply too much pressure that may damage or warp the wood.
Marking reference points
When copying curved surfaces, marking reference points on both the original piece and the workpiece can help with alignment and accuracy during tracing or transferring. These reference points act as guides for positioning and maintaining symmetry between both objects. Use a pencil or marker to mark these reference points on both surfaces, making sure they are easily visible but won’t interfere with the tracing process later on.
By following these necessary steps when preparing your workpiece, you can ensure a smoother and more successful copying process for curved surfaces. Taking the time to properly clean and secure the workpiece, as well as marking reference points, will help you achieve more accurate results in your woodworking projects.
Techniques for tracing and transferring a curved surface
Using Templates
One of the most common and straightforward methods for tracing and transferring a curved surface in woodworking is by using templates. Templates are pre-cut or pre-shaped materials that are designed to match the desired curve. They can be made from various materials such as cardboard, plywood, or even plastic.
To use a template, start by creating a rough outline of the desired shape on your workpiece. Then, take your template and place it on top of the outline, making sure it aligns perfectly. Use clamps or weights to secure the template in place if necessary.
With a pencil or marker, trace along the edges of the template onto your workpiece. Once you have traced your desired curve, remove the template and you will be left with an accurate representation of the curved surface.
Using French Curves
Another effective method for tracing and transferring curved surfaces in woodworking is by using French curves. French curves are flexible drafting tools that come in various shapes and sizes, allowing for greater versatility when copying different curves.
To use a French curve, start by placing it on your workpiece where you want to transfer the curved surface. Adjust its position until you find a curve that closely matches what you are trying to copy. Once you have found the right curve, hold the French curve firmly against the workpiece while carefully tracing along its edge with a pencil or marker. Continue tracing along different parts of the French curve to capture different sections of the curved surface.
Using Flexible Rulers
Flexible rulers are another handy tool for tracing and transferring curved surfaces in woodworking. These rulers are typically made from thin metal or plastic that can be bent easily without breaking.
To use a flexible ruler, align one end along one edge of your curved surface while holding it firmly against the workpiece. Slowly bend and manipulate the ruler to follow along with each unique curve. As you bend the ruler, trace along its edge with a pencil or marker to transfer the shape onto your workpiece. Continue this process until you have captured the entire curved surface.
By using templates, French curves, or flexible rulers, woodworkers can accurately and precisely copy curved surfaces for their projects. These methods provide step-by-step instructions that are easy to follow and can be adapted based on the complexity of the curve and personal preferences. Mastering these techniques will allow woodworkers to achieve seamless craftsmanship and elevate the overall quality of their woodworking projects.
Choosing the right method for copying curved surfaces
Woodworking projects often require copying curved surfaces in order to achieve precise and seamless craftsmanship. With a variety of techniques available, it is important to choose the right method based on the project’s complexity and personal preferences. Evaluating different techniques will ensure that woodworkers are able to accurately duplicate curves and create their desired outcome.
One method for copying curved surfaces is using templates. Templates are pre-made patterns or shapes that can be traced onto the workpiece. These templates can be made from various materials such as plastic or cardboard. They are especially useful for duplicating curves that have consistent radii, such as circles or symmetrical shapes.
Another technique for copying curved surfaces is utilizing French curves. French curves are flexible templates made from plastic or metal that have a variety of different curved edges. By selecting the curve that closely matches the desired shape, woodworkers can easily trace the curve onto their workpiece for accurate duplication.
Flexible rulers are also an option for tracing and transferring curved surfaces. These rulers can be bent into various shapes and allow woodworkers to trace irregular or freeform curves. This technique is particularly useful when dealing with complex or organic shapes that cannot be replicated with standardized templates.
By evaluating the complexity of a woodworking project and considering personal preferences, woodworkers can choose the most suitable method for copying curved surfaces. Whether using templates, French curves, or flexible rulers, each technique offers its own advantages and allows for accurate duplication of curves.
Technique | Description |
---|---|
Templates | Pre-made patterns or shapes used for tracing onto the workpiece. |
French Curves | Flexible templates made of plastic or metal with various curved edges. |
Flexible Rulers | Rulers that can be bent into various shapes for tracing irregular or freeform curves. |
Tips and tricks for achieving accuracy
When it comes to copying curved surfaces in woodworking, achieving accuracy is crucial to ensure a seamless final result. However, there are often challenges that woodworkers encounter in this process. Thankfully, there are expert tips and tricks that can help overcome these challenges and achieve the desired level of accuracy.
One common challenge when copying curved surfaces is maintaining a consistent contour throughout the entire process. This can be particularly difficult when dealing with complex curves or irregular shapes. To overcome this, experts recommend breaking down the curve into smaller sections and working on each section separately.
By focusing on individual sections, woodworkers can pay close attention to detail and ensure that each part accurately reflects the original shape. Additionally, using clamps or jigs to hold the workpiece securely in place can also help maintain consistency during tracing or transferring.
Another challenge woodworkers face when copying curved surfaces is ensuring accurate measurements. This is especially important if the copied curve needs to fit precisely with other parts of a project or if multiple copies need to be made. To address this, experts suggest using precise measuring tools such as calipers or digital angle finders. These tools allow for precise measurements of curves’ angles and dimensions, ensuring an accurate copy every time.
Expert Advice | Insights |
---|---|
Breaking down the curve into smaller sections | This allows for better attention to detail and ensures accurate replication. |
Using clamps or jigs | Holding the workpiece securely helps maintain consistency during tracing or transferring. |
Using precise measuring tools | Tools like calipers and digital angle finders ensure accurate measurements of angles and dimensions. |
By following these expert tips and taking advantage of reliable measuring tools, woodworkers can overcome common challenges faced when copying curved surfaces. This will result in greater accuracy, allowing for a more seamless and professional-looking final product. As with any woodworking skill, practice is key to mastering the art of copying curved surfaces, and incorporating these tips into your workflow will contribute to continuous improvement in achieving precise copies.
Advanced techniques for complex curved surfaces
Advanced techniques can be employed to accurately copy complex curved surfaces in woodworking projects. These methods utilize advanced measuring tools or 3D scanning technology, allowing for a higher level of precision and efficiency. By exploring these innovative approaches, woodworkers can achieve seamless craftsmanship even with intricate and challenging curved surfaces.
One advanced technique for copying complex curved surfaces is the use of advanced measuring tools. These tools include precision calipers, contour gauges, and flexible metal rules with graduated markings. Precision calipers allow woodworkers to measure the dimensions and curves of a surface accurately. Contour gauges are instrumental in replicating irregular shapes by creating a template that matches the surface contour. Flexible metal rules with graduated markings are ideal for measuring shapes where straight edges alternate with curves.
Another cutting-edge method for copying complex curved surfaces involves utilizing 3D scanning technology. This technique offers an incredibly accurate way to capture every detail and dimension of a curved surface.
Using a 3D scanner, woodworkers can create a digital replica of the surface, which can then be transferred to CAD software or used as a reference for measurements. The digital model obtained from the 3D scan can be manipulated and modified before being implemented into the woodworking project, ensuring precise replication.
These advanced techniques provide woodworkers with powerful tools to tackle even the most intricate curved surfaces. By incorporating precision calipers, contour gauges, flexible metal rules, or 3D scanning technology into their workflow, craftsmen can achieve superior accuracy and efficiency in their woodworking projects.
Troubleshooting and common mistakes to avoid
Woodworking projects that involve copying curved surfaces can be challenging, but with the right knowledge and techniques, it is possible to achieve precise results. However, there are potential pitfalls and common mistakes that often arise during the copying process. Identifying these issues and knowing how to avoid them is crucial for ensuring a smooth and successful project.
One common mistake when copying curved surfaces is not taking accurate measurements. It is important to measure the original curve carefully and precisely before transferring it onto the workpiece. Using a flexible ruler or a measuring tape can help ensure accurate measurements. Additionally, it is crucial to double-check and re-measure multiple times to avoid any discrepancies.
Another pitfall to watch out for is using improper tracing materials. When transferring the curve onto the workpiece, it’s essential to use appropriate tools that can create sharp and clean lines. Poorly chosen tools can result in inaccurate or distorted curves. Pencils are generally recommended due to their versatility and ability to create precise lines. It is also important to maintain consistent pressure while tracing to avoid inconsistencies in the curve.
One of the most significant challenges when copying curved surfaces is achieving symmetry. Sometimes, even with careful measurements and tracing, discrepancies can occur between the original curve and its copied version. To address this issue, a helpful tip is to divide the curve into smaller segments and trace each segment separately. This technique allows for better control over each section and minimizes errors in overall symmetry.
Showcasing successful woodworking projects using copied curved surfaces
Woodworking is a craft that often relies on the ability to accurately reproduce curved surfaces. Whether you are creating a piece of furniture, a decorative object, or any other woodworking project, being able to copy curved surfaces with precision is essential. Not only does it ensure that the final piece looks seamless and professional, but it also enhances the overall aesthetic appeal.
When it comes to showcasing successful woodworking projects using copied curved surfaces, there are numerous examples that highlight the transformative power of accurate copying. One such example is the creation of a beautifully carved wooden chair. By accurately copying the curves of the human body, such as the contours of the back and seat, a chair can be crafted to provide optimal comfort and support while also exuding elegance and style.
Another inspiring example is in the realm of sculptural woodworking. Many woodworkers use curved surfaces to create intricate carvings and sculptures that capture movement and grace. The ability to accurately copy existing curved surfaces allows these artists to recreate these mesmerizing forms in wood, resulting in stunning works of art that captivate viewers.
In addition to furniture and sculptures, accurate copying of curved surfaces can also be seen in functional objects like bowls or vases. These items often feature gracefully shaped exteriors that require precision in order to maintain their aesthetic appeal. By meticulously copying these curved surfaces during the woodworking process, craftsmen can ensure that every curve flows harmoniously and that the finished product is visually pleasing from every angle.
Accurate copying of curved surfaces elevates woodworking projects from mere functionality to true craftsmanship. It allows artisans to not only create pieces that are structurally sound but also visually appealing. By mastering this skill, woodworking enthusiasts can take their creations to new heights, transforming raw materials into beautiful works of art that inspire and delight all who see them.
Conclusion
In conclusion, mastering the art of copying curved surfaces in woodworking is crucial for achieving professional results every time. The ability to accurately replicate curves is essential for enhancing precision and achieving seamless craftsmanship in woodworking projects. By properly understanding the techniques, tools, and materials required for copying curved surfaces, woodworkers can elevate the final aesthetic appeal of their pieces.
Throughout this article, we have explored various methods for tracing and transferring curved surfaces, such as using templates, French curves, or flexible rulers. We have also discussed the importance of choosing the right method based on the complexity of the project and personal preferences. Additionally, expert advice and insights have been shared to help woodworkers overcome common challenges and achieve accuracy when copying curved surfaces.
Furthermore, we have delved into advanced techniques like using advanced measuring tools or 3D scanning technology for more complex curved surfaces. These innovative methods can provide even greater accuracy and efficiency in the copying process.
Frequently Asked Questions
How do you make a curved wood surface?
Creating a curved wood surface involves several steps and techniques. One common method is to use a technique called steam bending, which involves heating the wood to make it pliable and then bending it into the desired shape. This process requires a steam box or a steam generator to heat the wood and soften its fibers.
Once the wood is pliable, it is carefully bent into shape and secured until it cools and retains its curved form. Another approach is using laminated or thin strips of wood that are glued together in layers with alternating grain directions, creating strength and flexibility that can be shaped into curves. This technique is often used for making curved furniture components or decorative wooden elements.
How do I create a curved surface template?
Creating a curved surface template requires precise measurements and attention to detail. The first step is to determine the exact curve you want to create by using drafting tools like a compass or flexible curve ruler. Then, transfer this shape onto a rigid material such as plywood or MDF board that can serve as your template.
Carefully trace the curve onto the material, ensuring accuracy throughout the process. Once you have created the outline of the curve, cut along this line using appropriate tools such as jigsaws or scroll saws, ensuring smooth edges. By creating a well-crafted curved surface template, you can replicate the desired curve accurately and repeatedly.
How do you scribe a curved surface?
Scribing a curved surface involves transferring an irregular shape onto another material for fitting purposes, typically seen when installing countertops, cabinetry, or even scribing baseboards against uneven walls. To scribe a curved surface, start by placing cardboard or foam against the wall (or reference piece) where you need to match the curve of your workpiece or object being installed against it. Then, press firmly against the backside of the cardboard at various points along its length while moving it across your workpiece’s edge with controlled pressure – this will cause an impression of any irregularities on your material.
With these marks as a guide, use a coping saw or a jigsaw to cut along the scribed line, allowing your workpiece to fit snugly against the curved surface. Scribing is an effective method for achieving precise fits on irregular shapes and ensuring a professional finish in many woodworking and installation projects.
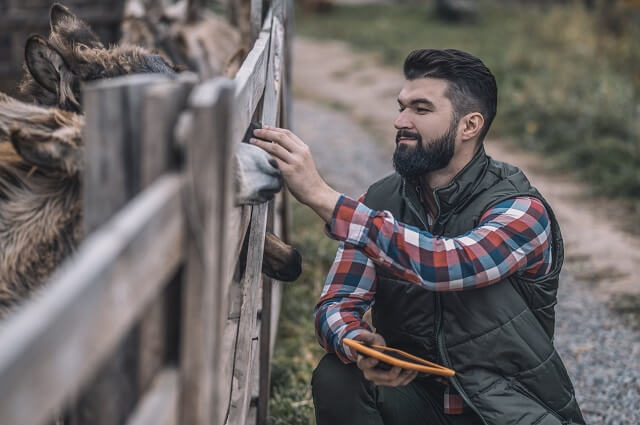
Hi everyone! I’m a woodworker and blogger, and this is my woodworking blog. In my blog, I share tips and tricks for woodworkers of all skill levels, as well as project ideas that you can try yourself.