Woodworking is a craft that requires careful attention to detail and precision. One crucial aspect of woodworking is ensuring that the wood used in projects is properly dried before it is worked on. This article will provide a comprehensive guide on how to dry wet wood for woodworking, covering various methods and techniques to achieve optimal results.
Using wet wood in woodworking projects can have serious consequences. Wet wood can shrink, warp, split, and even become infested with insects or fungus over time. These issues can result in a finished product that is unstable, unreliable, and prone to damage. Therefore, proper drying of wet wood is crucial to ensure the quality and longevity of any woodworking project.
In this article, we will walk you through a step-by-step guide on how to identify wet wood and assess its moisture content. We will also discuss different methods of drying wet wood, including natural air drying techniques and kiln drying. Additionally, we will provide tips for monitoring moisture content during the drying process and preventing common issues such as splitting and warping.
Whether you are a seasoned woodworking professional or just starting out as a hobbyist, understanding the importance of properly drying wet wood is essential for achieving exceptional results in your projects. By following the guidelines outlined in this article, you can ensure that the wood you use in your woodworking endeavors is properly dried and ready for crafting into beautiful pieces of furniture or other works of art.
The Consequences of Using Wet Wood in Woodworking Projects
Using wet wood in woodworking projects can have serious consequences that can compromise the quality and durability of the finished product. Properly drying the wood before using it is crucial to ensure a successful woodworking project. This section will discuss the various consequences of using wet wood and highlight why proper drying is so important.
Risk of Shrinkage and Warping
One of the main consequences of using wet wood in woodworking projects is the risk of shrinkage and warping. Wet wood contains a significant amount of moisture, and as it dries, it undergoes physical changes. The moisture loss causes the wood to shrink unevenly, leading to warping, twisting, and cupping.
This can result in misaligned joints, gaps, or even complete failure of the project. By properly drying the wood, you can minimize these risks and ensure that your finished product remains sturdy and stable over time.
Increased Probability of Splitting or Cracking
Wet wood is more prone to splitting or cracking compared to dry wood. As the moisture evaporates from the wood, it creates internal stresses that can cause the material to split or crack along its grain lines. These defects not only compromise the visual appeal but also weaken the structural integrity of the piece. By thoroughly drying the wood before working with it, you reduce the likelihood of such issues and create a stronger end result.
Potential for Mold Growth
Another consequence of using wet wood is an increased risk of mold growth. Moisture provides an ideal environment for mold spores to thrive and multiply on wooden surfaces, leading to unsightly discoloration, decay, and an unpleasant odor. Furthermore, inhaling mold spores can pose health risks for individuals with respiratory conditions or allergies. Properly drying the wood eliminates excessive moisture content that encourages mold growth, ensuring a healthier working environment and preserving the quality of the wood.
By understanding the consequences of using wet wood in woodworking projects, it becomes clear that proper drying is crucial for achieving successful outcomes. Shrinkage and warping, increased probability of splitting or cracking, and potential mold growth are just a few examples of why woodworkers should prioritize drying their materials. In the next section, we will provide a step-by-step guide on how to identify wet wood and assess its moisture content to determine if it requires drying before use.
Step-by-Step Guide
Step 1: Visual Inspection
The first step in identifying wet wood is to visually inspect the surface of the wood. Look for signs of discoloration, such as dark spots or stains, which indicate moisture absorption. Wet wood may also appear swollen or feel heavier than dry wood. Additionally, check for any visible signs of mold or mildew growth, which can be a clear indication of high moisture content.
Step 2: Use a Moisture Meter
To accurately assess the moisture content of the wood, it is recommended to use a moisture meter. These devices are designed specifically to measure the amount of water present in a material. Simply insert the moisture meter’s probes into the wood and allow it to take a reading. The moisture meter will provide you with a percentage value representing the wood’s moisture content. Generally, for woodworking projects, a moisture content below 8-10% is considered suitable.
Step 3: Perform the Oven-Dry Method (Optional)
If you want to double-check the accuracy of your moisture meter readings or if one is not available, you can perform the oven-dry method. Start by weighing a small sample of freshly cut wood and record its weight as “wet weight”. Then, place the sample in an oven set at approximately 220°F (105°C) for several hours until all moisture has evaporated from the wood.
Once dry, weigh the sample again and record its weight as “dry weight”. Finally, use this formula to calculate the wood’s moisture content:
Moisture Content = ((Wet Weight – Dry Weight) / Dry Weight) x 100%.
By following these steps, you will be able to accurately identify wet wood and determine its precise moisture content before proceeding with any woodworking project.
Step 4: Determining Drying Time
Once you have assessed the moisture content of the wood, it is important to determine how long it will take for the wood to dry. This is crucial in planning your woodworking project timeline.
There are several factors that affect drying time, including the type and thickness of the wood, prevailing environmental conditions, and drying method used. As a general rule of thumb, natural air drying can take several months to a year, while kiln drying can significantly reduce the drying time to just a few weeks.
Step 5: Consider Wood Species
It’s important to note that different wood species have different drying characteristics. Certain hardwoods, like oak or maple, tend to dry more slowly than softwoods like pine or cedar due to their higher density. Understanding the specific properties of the wood species you are working with will help you determine an appropriate drying method and estimate the required drying time more accurately.
By following this step-by-step guide, you will be equipped with the knowledge and skills needed to identify wet wood and assess its moisture content effectively. This information is essential for ensuring proper wood preparation before embarking on any woodworking project.
Preparing Wet Wood for Drying
When working with wet wood for woodworking projects, it is essential to properly prepare the wood before beginning the drying process. This involves removing bark, slabs, and any unnecessary moisture from the wood. By taking these steps, you can ensure that the drying process is more effective and efficient, ultimately resulting in high-quality woodworking materials.
One of the first tasks in preparing wet wood for drying is to remove the bark. Bark on wet wood can trap moisture inside and hinder the drying process. Using a sharp chisel or a drawknife, carefully remove the bark by following the natural grain of the wood. Be cautious not to gouge or damage the underlying wood during this process.
Next, it is important to remove any large slabs or pieces from the wet wood that may impede airflow during drying. These slabs are often thicker and retain more moisture than other parts of the wood. Using a saw or an axe, cut away any excess wood, focusing on removing sections that have a higher moisture content.
To further facilitate drying, it is crucial to eliminate any unnecessary moisture present in the wet wood. One popular method is called “pounding,” where you use a rubber mallet or hammer to gently tap on each surface of the wood. This helps dislodge excessive water droplets and increases airflow within the fibers.
After completing these preparatory steps, your wet wood will be ready for the drying process. Whether you choose natural air drying methods or kiln drying techniques (as outlined in other sections), having properly prepared wet wood allows for more effective and efficient drying, resulting in high-quality woodworking materials for your projects.
Natural Air Drying Methods
When it comes to drying wet wood for woodworking projects, one of the most common and effective methods is natural air drying. This process relies on the power of time and airflow to gradually remove moisture from the wood, resulting in a stable and usable material for your woodworking needs. In this section, we will explore the steps and best practices for harnessing this method.
The first step in natural air drying is to ensure that you have a suitable location. The ideal drying area should be well-ventilated with good air circulation and protection from direct sunlight and rain. A covered or partially shaded area such as a shed or covered patio can work well.
Once you have identified the drying location, it’s important to prepare the wood properly. Start by placing the wet wood on top of wooden stickers or spacers, which allow air to flow around all sides of the wood. Make sure there is enough space between each piece of wood for adequate ventilation.
Throughout the drying process, it’s crucial to monitor the moisture content of the wood regularly using a moisture meter. Check the readings every few days initially and then less frequently as the drying progresses. It’s important to note that different species of wood will require different amounts of time to dry fully.
Patience is key when using natural air drying methods, as it can take several months or even years for larger pieces of wood to reach an acceptable moisture content. However, this method allows for slow and controlled drying, reducing the risk of cracking, warping, and other issues commonly associated with rapid drying methods.
Step | Description |
---|---|
1 | Identify a well-ventilated and protected drying location such as a shed or covered patio. |
2 | Place wet wood on top of wooden stickers/spacers to allow air circulation around all sides of the wood. |
3 | Regularly monitor moisture content using a moisture meter to track drying progress. |
4 | Be patient and allow several months or years for larger pieces of wood to dry fully, reducing the risk of cracking and warping. |
Kiln Drying
Kiln drying is an effective method for drying wet wood quickly and efficiently. This section will discuss the process of kiln drying, including the equipment needed and the benefits it offers for woodworking projects.
Understanding Kiln Drying
Kiln drying involves using controlled heat and humidity to remove moisture from the wood. In a kiln, wood is placed in a chamber where temperature and humidity levels are carefully monitored and adjusted. The heat and airflow within the kiln facilitate the evaporation of moisture from the wood, resulting in faster drying times compared to natural air drying methods.
The Benefits of Kiln Drying
There are several benefits to using kiln drying for wet wood in woodworking projects. Firstly, kiln drying helps to prevent splitting, warping, and other issues that can occur when wood dries unevenly or too quickly. By controlling the environmental conditions during the drying process, kiln drying minimizes these risks and ensures that the wood retains its shape and stability.
Another advantage of kiln drying is that it allows for more precise control over moisture content. This is particularly important for woodworking projects where specific moisture levels are required for optimal results. Kilns can be adjusted to achieve different moisture content targets, making it easier to meet project specifications.
Moreover, kiln-dried wood tends to have increased strength and durability compared to air-dried wood. The controlled environment of a kiln accelerates the release of water from within the wood fibers without causing excessive stress or damage. As a result, kiln-dried wood is less susceptible to decay, insect infestation, and other forms of deterioration.
The Process of Kiln Drying
To begin with, it is essential to properly stack the wet wood inside the kiln to ensure adequate airflow around each piece for even drying. The desired temperature and humidity levels are then set based on the specific wood species and thickness. The kiln is typically heated using gas, electricity, or steam to reach the desired temperature.
Throughout the drying process, it is important to monitor the moisture content of the wood regularly. Moisture meters are commonly used for this purpose, allowing woodworkers to determine whether the wood has reached its target moisture content and is ready for use. Depending on the type of wood and thickness, kiln drying can take anywhere from a few days to several weeks.
The Importance of Monitoring and Measuring Moisture Content during the Drying Process
Wood drying is a critical process in woodworking, as using wet wood can lead to significant problems in woodworking projects. One of the key factors in ensuring proper wood drying is monitoring and measuring the moisture content throughout the process. This section will explore the importance of this step and provide guidance on how to effectively monitor and measure moisture content during the drying process.
Monitoring and measuring moisture content during wood drying is crucial for several reasons. First, it helps determine when the wood has reached its desired moisture level for woodworking. Different types of wood have different ideal moisture levels for specific projects, and by monitoring the moisture content, woodworkers can ensure that their materials are ready for use. This prevents issues such as warping or splitting that can occur if the wood is too wet or too dry.
Second, monitoring moisture content allows woodworkers to prevent over-drying or under-drying. Over-drying can result in brittleness and make the wood prone to cracking or breaking, while under-drying may cause excess moisture to remain in the wood, leading to future problems as it dries further over time.
There are several methods available for monitoring and measuring moisture content during the drying process. One common method is using a moisture meter specifically designed for woodworking purposes. These meters utilize different technologies such as pin-type or pinless sensors to measure the percentage of moisture present in the wood. Another method involves weighing small samples of wood at regular intervals throughout the drying process and comparing their weight loss over time.
By regularly monitoring and measuring moisture content during wood drying, woodworkers can ensure that their materials are properly dried and ready for use in their projects. It allows them to achieve optimal results while minimizing issues such as warping, splitting, or reduced durability caused by improper drying.
Best Practices and Tips for Preventing Splitting, Warping, and other Drying-related Issues
Woodworkers understand that properly drying wet wood is essential to ensure the quality and longevity of their projects. One of the biggest challenges in wood drying is preventing splitting, warping, and other drying-related issues. In this section, we will discuss some best practices and tips to help woodworkers avoid these problems and achieve successful drying results.
- Slow and Controlled Drying: One of the most important rules in wood drying is to go slow. Rapid drying can cause stress within the wood fibers, leading to splitting and warping. It is crucial to allow the moisture within the wood to escape gradually by using proper air circulation and low humidity environments. This slow and controlled approach helps minimize stress on the wood and reduces the risk of common drying issues.
- Proper Stacking Techniques: When stacking wet wood for drying, it is essential to stack it carefully to prevent warping or bending. Ensure that the boards are supported evenly across their entire length with no gaps between them. Place spacers between each layer, allowing for proper airflow between boards, which aids in even moisture removal.
- End Sealing: The ends of freshly cut lumber tend to dry faster than the rest of the piece due to their exposed nature. This uneven drying can lead to end splits or checks. To prevent this, it is recommended to seal the ends of green or wet boards with a commercial end-grain sealer or even wax. This helps slow down moisture loss from the ends, allowing for more even drying throughout.
In addition to these best practices, there are several other tips that can help prevent splitting, warping, and other drying-related issues:
- Avoid direct sunlight or excessive heat exposure during the drying process.
- Use dehumidifiers or fans if necessary to maintain proper humidity levels.
- Regularly monitor moisture content using a moisture meter.
- Rotate or flip boards periodically during drying for more balanced moisture removal.
- Allow sufficient time for wood to acclimate to its new environment before using it in a project.
By following these best practices and tips, woodworkers can greatly reduce the risk of splitting, warping, and other drying-related issues. Properly dried wood will not only result in stable and high-quality projects but also save time and resources in the long run.
Best Practices | Tips |
---|---|
Slow and Controlled Drying | Avoid direct sunlight or excessive heat exposure during drying. |
Proper Stacking Techniques | Use dehumidifiers or fans if necessary to maintain proper humidity levels. |
End Sealing | Regularly monitor moisture content using a moisture meter. |
Alternative Techniques
In addition to natural air drying and kiln drying, there are alternative techniques that can be used to dry wet wood for small-scale woodworking projects. These methods, such as microwave and oven drying, are particularly useful when you need to dry smaller pieces of wood quickly or when you’re working on a project that requires a faster turnaround time.
- Microwave Drying: Using a microwave to dry small pieces of wet wood is a quick and convenient method. Start by cutting the wood into thin slices or small pieces that can fit comfortably inside the microwave. Place the wood on a microwave-safe plate or tray, making sure not to overcrowd it.
Set the microwave to low heat (around 30% power) and set the timer for short intervals, such as 20-30 seconds. After each interval, check the moisture content of the wood using a moisture meter. Repeat the process until the desired moisture level is achieved. - Oven Drying: Another option for small-scale woodworking projects is oven drying. Preheat your oven to about 200°F (93°C). Similar to microwave drying, cut the wet wood into thin slices or small pieces that can easily fit inside your oven without overcrowding it.
Place the wood on a baking sheet lined with parchment paper or aluminum foil. Leave some space between each piece to allow for proper airflow. Insert the baking sheet into the preheated oven and let it dry for a few hours, checking regularly for any signs of overheating or scorching.
It’s important to note that while these alternative techniques can save time in certain situations, they may not be suitable for larger pieces of wood or those with higher moisture content. Additionally, they should always be used with caution as improper use could lead to damage or even fire hazards. It’s recommended to consult expert advice and resources before attempting these methods, especially if you’re a beginner in woodworking.
Case Studies and Success Stories
Woodworking enthusiasts and professionals often face the challenge of working with wet wood. In this section, we will explore real-life case studies and success stories of individuals who have successfully dried wet wood for their woodworking projects. These examples will provide valuable insights into the different techniques and approaches used to achieve optimal results.
Case Study #1: Air Drying
One successful example of drying wet wood is demonstrated by a woodworker named John. He had a large oak log that he wanted to dry for use in a furniture project. Instead of using kiln drying or other artificial methods, John chose to air dry the wood. He prepared the log by removing bark and branches, creating slabs of manageable size.
John then went through the meticulous process of stacking and spacing his oak slabs to allow for proper airflow. He positioned them in a shaded area with good ventilation and protected them from rain using tarpaulins. Over the course of several months, he regularly measured the moisture content using a moisture meter, ensuring it was steadily decreasing.
After about a year, the wood reached an acceptable moisture content level for his woodworking project. John was able to successfully craft a beautiful dining table from his dried oak slabs without experiencing any significant issues such as splitting or warping.
Case Study #2: Kiln Drying
In another case study, we have Jane who needed to dry several pieces of walnut for her woodworking business within a short timeframe. Time constraints meant that air drying was not an option for her project, so she opted for kiln drying instead.
Jane carefully monitored the moisture content throughout the entire kiln drying process. By controlling both temperature and humidity levels within the kiln, Jane was able to accelerate the drying time while still maintaining quality results.
Within just a few weeks, Jane’s walnut pieces were sufficiently dried and ready for her woodworking projects. The controlled environment of the kiln allowed her to achieve a consistent moisture content throughout the wood, minimizing the risk of splitting or warping.
These case studies demonstrate that there are multiple successful approaches to drying wet wood for woodworking projects. Whether it is through natural air drying methods or utilizing kiln drying, proper monitoring and measuring of moisture content are essential. By following best practices and taking necessary precautions, woodworkers can ensure that their dried wood is stable and ready for use in their creations.
Conclusion
Properly drying wet wood is vital for any woodworking project as it significantly affects the final outcome. By following the right methods and techniques, woodworkers can achieve exceptional results while avoiding common issues such as splitting, warping, or decay.
Whether using natural air drying or kiln drying methods, monitoring and measuring the moisture content throughout the process is crucial to ensure the wood reaches its ideal level of dryness. Additionally, implementing best practices and tips can help prevent potential problems that may arise during the drying process.
One of the main reasons why proper wood drying is essential is to avoid potential issues that arise when working with wet wood. Wet wood can lead to structural problems in finished projects such as warping and splitting as it dries over time. This can ultimately compromise the integrity of the piece and reduce its lifespan. By taking the necessary steps to dry wood properly, these issues can be minimized or completely eradicated.
Another significance of proper wood drying lies in achieving optimal strength and stability in woodworking projects. Wet wood lacks rigidity since it contains a high moisture content, which makes it more prone to damage and deformation. By adequately removing excess moisture from the wood, it not only strengthens but also stabilizes it. This ensures that the final product retains its shape and durability over time, making it suitable for various applications such as furniture making or construction.
Additional Resources and Further Reading
In conclusion, proper wood drying is essential for achieving exceptional woodworking results. By understanding the importance of properly drying wet wood and following the step-by-step guide provided in this article, woodworkers can ensure that their projects are successful and long-lasting.
Throughout this article, we have discussed the consequences of using wet wood in woodworking projects and highlighted the methods for identifying wet wood and assessing its moisture content. We have explored natural air drying methods and kiln drying techniques, emphasizing the need to monitor and measure moisture content during the drying process to prevent splitting, warping, and other drying-related issues.
Furthermore, we have delved into alternative techniques such as microwave and oven drying for small-scale woodworking projects. While these methods may be suitable for certain situations, it is crucial to approach them with caution and carefully follow safety guidelines.
To further deepen your knowledge on the subject, there are several additional resources available. Recommended websites, books, and tools can provide valuable information and guidance for drying wet wood in woodworking. Exploring these resources will equip you with a comprehensive understanding of the topic and help you refine your skills as a woodworker.
Frequently Asked Questions
What is the fastest way to dry wet wood?
The fastest way to dry wet wood is by using a kiln or a specialized drying chamber. Kiln drying involves controlling the temperature and humidity levels to expedite the evaporation of moisture from the wood.
This method allows for rapid drying, reducing the overall time required compared to air-drying. However, it is important to note that kiln drying requires specialized equipment and expertise, making it more suitable for commercial woodworking operations rather than small-scale projects.
Can you woodwork with wet wood?
Woodworking with wet wood is generally not recommended. Working with wet wood can present various challenges and risks. Wet wood is typically softer and more prone to warping, splitting, and cracking when cut or shaped.
It may also cause issues with glue adhesion or result in subpar finishing results due to inconsistencies in moisture content. Therefore, it is advisable to wait until the wood has dried adequately before engaging in woodworking activities.
How long does wood take to dry for woodworking?
The time required for wood to dry before it’s suitable for woodworking can vary significantly depending on several factors such as the species of wood, its initial moisture content, environmental conditions, and the desired moisture level for woodworking purposes. As a general guideline, air-drying typically takes around 6 months to a year per inch of thickness, but this can be longer for denser woods or under less favorable conditions.
However, using accelerated methods like kiln drying can significantly reduce this timeframe to a matter of weeks or even days in some cases. Professional moisture meters can help determine whether the wood has reached an appropriate moisture level for woodworking by measuring its internal moisture content accurately.
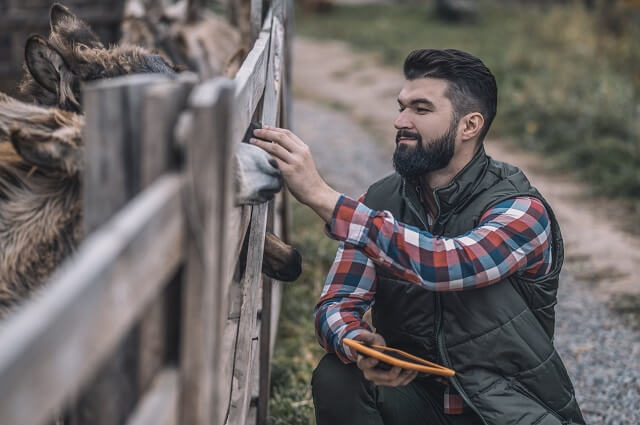
Hi everyone! I’m a woodworker and blogger, and this is my woodworking blog. In my blog, I share tips and tricks for woodworkers of all skill levels, as well as project ideas that you can try yourself.