Woodworking projects require careful planning and accurate estimations to ensure a successful outcome. Whether you are a professional woodworker or an enthusiast tackling a DIY project, understanding how to estimate the materials, labor, and timeline involved is essential for effective project management. In this article, we will explore the steps involved in estimating woodworking projects and provide valuable insights on how to achieve accurate estimations.
Accurate estimations play a significant role in woodworking projects for several reasons. Firstly, they help you determine the amount of materials needed, such as wood, nails, screws, or other hardware. By accurately calculating these quantities, you can ensure that you have enough supplies on hand without overbuying or running out mid-project.
Additionally, precise estimations allow you to determine the appropriate labor cost associated with each woodworking task. This helps you allocate resources effectively and ensures that your estimates align with your budget constraints. Furthermore, accurate estimations enable you to present transparent cost breakdowns to clients when working on commissioned projects.
In this article’s subsequent sections, we will dive deeper into the estimation process for woodworking projects. We will discuss techniques to identify project requirements, gather measurements and specifications accurately, calculate materials quantities precisely, determine labor costs effectively, factor in additional expenses and contingencies appropriately, estimate project timelines realistically, and present your estimates professionally.
By mastering the art of estimating woodworking projects accurately, you can enhance your planning and execution skills while avoiding costly mistakes or delays. Whether it is a small-scale craft or a large-scale construction endeavor; having a solid foundation in estimation techniques can significantly contribute to the success of your woodworking projects. So let’s begin our exploration of this essential skill and discover how to estimate woodworking projects like a pro.
Identifying and analyzing project requirements
Before beginning any woodworking project, it is crucial to identify and analyze the project requirements. This step involves breaking down the project scope, determining the materials needed, and understanding the desired outcome. By carefully considering these factors, woodworkers can ensure accurate estimations for their projects.
To start, it is important to clearly define the project scope. This includes determining the size and complexity of the project, as well as any specific features or designs that need to be incorporated. Breaking down the scope into smaller tasks or components can make it easier to estimate both material quantities and labor costs.
Next, it is essential to determine the materials needed for the project. This includes considering the type of wood required, as well as any additional materials such as nails, screws, or glue. Creating a detailed list of all necessary materials will help in calculating quantities accurately later on.
Additionally, understanding the desired outcome of the woodworking project is crucial in estimating its cost and duration. This involves discussing with clients or stakeholders about their expectations for aesthetics, functionality, and overall quality. Taking note of these specifications will assist in making more precise estimations when calculating labor costs and timelines.
In summary, identifying and analyzing project requirements is an essential step in estimating woodworking projects accurately. By breaking down the project scope into smaller tasks, determining material needs, and understanding desired outcomes thoroughly, woodworkers are better equipped to create more accurate estimates for their projects’ costs and timelines.
- Create a detailed breakdown of the project scope to determine its size and complexity.
- Make a comprehensive list of all materials required for the woodworking project.
- Discuss with clients or stakeholders about their expectations for aesthetics, functionality, and overall quality of the desired outcome.
Gathering measurements and specifications
To ensure a successful woodworking project, gathering accurate measurements and specifications is crucial. This section will explore various methods that can be used to obtain precise measurements and gather vital specifications for the woodworking project.
One of the most basic and widely used methods for measuring in woodworking is using a tape measure. A good quality tape measure with clear markings is essential for obtaining accurate measurements. It is important to measure each component of the project individually, accounting for any overlapping or additional materials that may affect the final dimensions.
In addition to tape measures, there are other specialized measuring tools that can be utilized depending on the complexity of the project. These include calipers, digital angle finders, and squares. Calipers are particularly useful when precise measurements of thickness or depth are required, while digital angle finders help ensure the correct angles are achieved in joinery work.
When it comes to gathering specifications, careful examination and note-taking play a significant role. Take thorough notes of any specific requirements provided by the client or outlined in the project plans. Specifications may include wood species preferences, finish types, hardware requirements, or even design details such as curved edges or decorative elements.
Moreover, visual representation can be invaluable in conveying specifications accurately. Sketches or drawings can help solidify design ideas and provide a clearer understanding of how different components will come together in the final product. Additionally, photographs or existing examples can be referenced to ensure accuracy in replicating certain features.
By employing these methods and techniques to gather measurements and specifications, woodworkers can lay a strong foundation for their projects. Accurate information ensures precision during construction and avoids costly mistakes down the line. With precise measurements and comprehensive specifications at hand, woodworkers can move on to calculating materials quantities with confidence.
Calculating materials quantities
One of the crucial steps in estimating woodworking projects is calculating the quantities of materials needed for the project. The accurate determination of the required amount of wood, nails, screws, or other materials is essential to ensure a smooth and efficient construction process. By understanding the techniques involved in this calculation, woodworkers can avoid wastage and unnecessary expenses.
To begin calculating materials quantities, it is important to have a detailed understanding of the project specifications. This includes analyzing the project scope, reviewing the design plans, and identifying any specific requirements. It is also essential to consider factors such as wood grain direction, joinery methods, and material thickness to accurately determine the quantities needed.
Once the project requirements are clear, precise measurements are crucial. Accurate measurements help prevent overestimating or underestimating material quantities. Various tools can be used to gather these measurements such as tape measures, rulers, or calipers depending on the precision required for the project. Additionally, it is important to account for any cuts or waste that may occur during construction when determining material quantities.
After gathering all necessary measurements and specifications, calculations can be made to determine the required amount of wood and other materials. These calculations will depend on factors such as dimensions of individual pieces, desired spacing between them, and any additional components needed for assembly. It is advisable to calculate material quantities based on worst-case scenarios or potential mistakes to account for contingencies.
Materials | Quantity |
---|---|
Wood | 500 board feet |
Nails | 500 pieces |
Screws | 200 pieces |
Other materials (e.g., glue, sandpaper) | Varies depending on project requirements |
Determining labor costs
Determining labor costs is a crucial aspect of estimating woodworking projects. It involves estimating the amount of time and effort required for different woodworking tasks and assigning an appropriate labor cost. By accurately assessing the labor costs, woodworkers can ensure that they are pricing their projects effectively, covering their expenses, and maximizing their profits.
When estimating labor costs for woodworking projects, it is important to consider various factors. First, one should determine the tasks involved in the project and break them down into smaller components. This allows for a more accurate assessment of the time and effort required for each task. For example, if a project involves building a wooden cabinet, tasks such as measuring and cutting wood, assembling pieces, sanding, staining or painting, and installing hardware need to be considered.
Once the tasks have been identified, it is essential to estimate the time required for each task based on previous experience or industry standards. This estimation should account for any complexity involved in the process as well as potential learning curves for new techniques or designs. Additionally, considering the skill level of the workers involved can help in determining the amount of time needed.
After determining the estimated time required for each task, an appropriate labor cost can be assigned. This labor cost may vary depending on location, skill level of workers, market demand, and other factors specific to individual businesses. It is important to factor in overhead costs such as salaries or wages for workers, insurance, and other expenses associated with running a woodworking business.
Factor | Description |
---|---|
Task Complexity | The level of difficulty associated with each woodworking task. |
Experience Level | The skill level and experience of the workers performing the tasks. |
Location | The geographical location where the woodworking project is taking place. |
Labor Market Demand | The supply and demand dynamics of the labor market in the area. |
Overhead Costs | Expenses associated with running a woodworking business such as salaries, insurance, etc. |
By considering these factors and accurately estimating labor costs for each task, woodworkers can ensure that their pricing is in line with the effort involved and their business remains sustainable. It is important to regularly review and update labor cost estimates as factors such as market conditions and worker skill levels may change over time. With accurate labor cost estimation, woodworkers can effectively plan their projects, provide fair prices to clients, and achieve success in their woodworking endeavors.
Factoring in additional costs
Equipment Rental
When estimating woodworking projects, it is crucial to consider any equipment rental costs that may be necessary. Depending on the scope of the project, you may need specialized tools or machinery that you don’t currently own.
Research the rental rates for the specific equipment you require and factor this into your estimate. It’s important to note that these costs can vary depending on the duration of the rental, so accurately estimating the project timeline will also help determine the duration for which equipment needs to be rented.
Finishing Materials
Another expense that should be accounted for in the estimation is finishing materials. Woodworking projects often require paint, stain, varnish, or other types of finishes to enhance and protect the final product. Consider the cost of these materials when determining your overall estimate. Additionally, take into account any specialized brushes, applicators or tools that may be needed for applying these finishes.
Transportation
Transportation costs are often overlooked but can have a significant impact on project expenses. If you need to transport large quantities of wood or other materials to your workshop or job site, be sure to include transportation costs in your estimate. This can include fuel expenses if you’re using your own vehicle as well as any fees for renting a truck or trailer for larger loads.
Potential Unforeseen Circumstances
It’s crucial to allocate a portion of your estimate to cover potential unforeseen circumstances. No matter how well you plan, there can always be unexpected challenges or obstacles during a woodworking project.
These could range from discovering hidden damage in existing structures that needs repair, changes in client requirements midway through the project, or even weather delays that impact progress. By setting aside some contingency funding within your estimate, you’ll ensure that you have a buffer in case additional expenses arise during the course of your project.
By factoring in these additional costs, you can create a more comprehensive and accurate estimate for your woodworking projects. Taking into account equipment rental, finishing materials, transportation, and potential unforeseen circumstances will help ensure that your estimate is realistic and allows for unexpected expenses. This thorough approach to estimation will not only benefit you as the woodworker but also provide transparency to your clients and contribute to successful project planning and execution.
Estimating the project timeline
Evaluating project complexity
One of the key factors to consider when estimating the project timeline for a woodworking project is the complexity of the work involved. Different projects will have varying degrees of difficulty, which can impact how long it takes to complete.
Factors that contribute to complexity include the intricacy of the design, the number of pieces to be produced, and any unique or custom features required. It’s important to carefully evaluate these factors in order to provide an accurate estimate of the project timeline.
Assessing available workforce
The availability and size of your workforce will also play a significant role in determining the project timeline. If you have a small team or limited resources, it may take longer to complete the woodworking project compared to having a larger team.
Consider factors such as skill level, experience, and availability of your workers when estimating how long each task will take. Additionally, take into account other commitments or potential conflicts that could affect their ability to dedicate time solely to the project.
Accounting for potential delays
It’s crucial to anticipate potential delays in any woodworking project estimation. Delays can occur due to various reasons such as material shortages, unexpected equipment malfunctions, or changes in client requirements.
By considering these possibilities upfront and factoring them into your estimation, you can create a more realistic timeline that accounts for potential setbacks. It’s always beneficial to build some buffer time into your estimate so that if unforeseen delays do arise, you have some flexibility without compromising on quality.
By evaluating project complexity, assessing available manpower, and accounting for potential delays, you can provide guidance on how to accurately estimate the duration of a woodworking project. Understanding these factors allows for better planning and execution and helps ensure successful completion within the estimated timeframe.
Adjusting for contingencies
Adjusting for contingencies is a crucial step in estimating woodworking projects. No matter how well you plan and prepare, it’s inevitable that unexpected obstacles and challenges will arise during the course of a project. These may include unforeseen material shortages, machinery breakdowns, or even changes in design specifications. It is important to allocate a contingency factor in your estimation to ensure that you have enough resources to handle these unforeseen circumstances.
When determining the amount to set aside for contingencies, it’s best to err on the side of caution. Typically, experts recommend allocating between 5% to 10% of the total project cost for contingencies. This percentage should be adjusted depending on the complexity and scale of the project – larger and more complex projects may require a higher contingency factor.
One approach to determining an appropriate contingency factor is by drawing from past experiences. Reflect on previous woodworking projects and identify any common challenges or issues that arose, as well as their associated costs. This will give you a good starting point when estimating contingencies for future projects.
It’s also important to communicate with the client about the need for a contingency factor in your estimate. Explain why it is necessary and how it will help mitigate risks and ensure project success. By being transparent about potential challenges from the beginning, you can establish trust with your clients and manage their expectations more effectively.
Including a contingency factor in your estimation is not just about being prepared for unexpected costs; it’s also about demonstrating professionalism and establishing yourself as a reliable woodworking professional who thoroughly plans for all possibilities. By accounting for contingencies in your estimation process, you will be better equipped to handle any challenges that come your way during the woodworking project, ultimately ensuring its successful completion.
Presenting the estimate to clients
Once you have completed the estimation for your woodworking project, it is essential to effectively present the estimate to your clients. This step is crucial as it sets the tone for your client’s understanding of the project and ensures a transparent and clear agreement between both parties. Here are some tips on how to effectively communicate the estimate to your client.
Firstly, provide a breakdown of costs in your estimate. Break down all the expenses involved in the project, including materials, labor, equipment rental, finishing materials, and any additional costs. This breakdown allows clients to understand where their money is being allocated and enables them to make informed decisions about any adjustments or alternatives they may want to consider. Providing a transparent cost breakdown builds trust and credibility with your client.
In addition to costs, include a timeline in your estimate. Outline specific milestones and deadlines for different phases of the woodworking project. This helps manage client expectations regarding the duration of the project and allows them to plan accordingly. Be sure to account for potential delays or unforeseen circumstances in your timeline estimation so that clients are aware of possible changes that may occur throughout the project.
Lastly, be prepared to provide any necessary clarifications about the estimate. Clients may have questions or concerns about certain aspects of the estimation, such as specific materials being used or labor costs for different tasks. Be open and responsive to their inquiries, providing detailed explanations when needed. Clear communication ensures that both you and your client are on the same page and reduces misunderstandings down the line.
Conclusion
In conclusion, accurate estimations are crucial in woodworking projects for several reasons. Firstly, a well-calculated estimate helps ensure that the project stays within budget and avoids any financial surprises or setbacks. It allows both the woodworker and the client to have a clear understanding of the costs involved and prevents any misunderstandings or disputes that may arise later on.
Secondly, accurate estimations help in effective project planning by providing a roadmap of the materials needed, labor costs, and project timeline. This allows for better resource allocation, scheduling, and coordination of tasks, resulting in a smoother workflow and increased overall efficiency.
Throughout this article, we have discussed various strategies to estimate woodworking projects accurately. From breaking down project requirements and gathering measurements to calculating material quantities and determining labor costs, each step is essential for an accurate estimation. We have also emphasized the importance of factoring in additional costs such as equipment rental, finishing materials, transportation, and contingencies to avoid unexpected expenses.
By applying these strategies discussed here, woodworkers can ensure successful project planning and execution. It is important to remember that accurate estimations not only benefit the woodworker but also instill confidence in clients who will appreciate transparency and proficiency. Therefore, when presenting estimates to clients, it is vital to provide a breakdown of costs along with a timeline and any necessary clarifications to establish trust and foster effective communication.
Frequently Asked Questions
How do you calculate woodworking project?
Calculating a woodworking project involves several important steps. Firstly, you need to determine the cost of materials required for the project, including lumber, hardware, and any other necessary components. This can be estimated by researching the prices at local suppliers or online retailers. Additionally, consider any expendable items like sandpaper or finishes that will be used during the process.
Next, calculate the overhead costs such as rent for your workspace, electricity bills, tool maintenance expenses, and any other business-related costs. It’s crucial to factor in the time it takes to complete the project by estimating labor hours required and multiplying it by an appropriate hourly rate. Finally, consider adding a markup percentage as profit to ensure a reasonable return on your efforts.
How much should a woodworker charge per hour?
Determining how much a woodworker should charge per hour can depend on various factors such as skill level, experience, location, market demand, and overhead costs. It’s essential to consider both direct costs (materials and labor) and indirect costs (rental fees, utilities) associated with running a woodworking business when determining an hourly rate.
Researching what other woodworkers charge in your area can provide insight into competitive pricing while ensuring fair compensation for your time and expertise is also important.
What should my profit margin be for woodworking?
Deciding on an appropriate profit margin for woodworking is subjective and can vary depending on individual circumstances. Profit margins are typically expressed as percentages and represent the amount of profit earned compared to total revenue generated from sales. In woodworking or any business venture, determining a profit margin involves considering various elements such as material costs, labor expenses (including wages), overhead costs (including rent and utilities), taxes payable on profits, desired personal income or salary as well as market competition and demand for your products or services.
A common guideline for establishing a profit margin is aiming for around 10-15% net profit after taking into account all relevant expenses. However, ultimately setting a suitable profit margin requires thorough analysis of both costs and market dynamics to ensure profitability while remaining competitive.
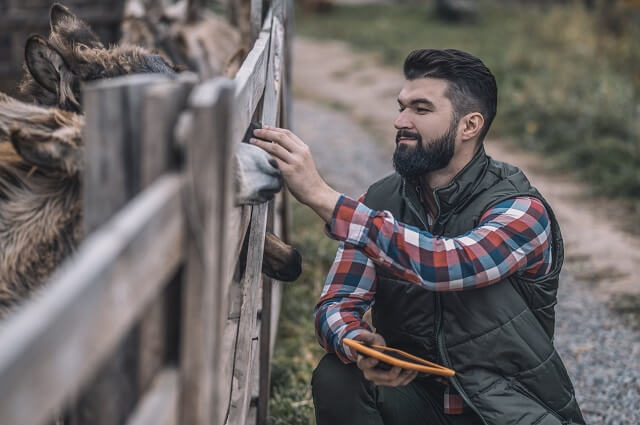
Hi everyone! I’m a woodworker and blogger, and this is my woodworking blog. In my blog, I share tips and tricks for woodworkers of all skill levels, as well as project ideas that you can try yourself.