Woodworking machines can be powerful and essential tools in any workshop, but they also pose a potential risk if not properly grounded. Grounding woodworking machines is crucial for ensuring both personal safety and the effective functioning of the equipment.
In this article, we will explore the concept of grounding and its significance within the context of woodworking machines. We will delve into the risks associated with using ungrounded machines and why it is essential to address this issue. Additionally, we will provide a comprehensive list of the tools and materials needed to effectively ground woodworking machines.
By following our step-by-step guide on how to ground various types of woodworking machines, including table saws, planers, routers, and more, you’ll be equipped with the knowledge and skills necessary to ensure a safe working environment. We will also discuss common mistakes to avoid when grounding these machines and provide tips for testing and troubleshooting any issues that may arise.
Lastly, we’ll emphasize the importance of regular maintenance checks and additional safety precautions to take alongside grounding.
Join us as we uncover the importance of grounding woodworking machines and learn how it can lead to safer working practices as well as optimal machine performance.
What is grounding
Grounding is a crucial concept in the context of woodworking machines. It involves creating a connection between the electrical circuit of a machine and the ground to ensure safety and effectiveness. In simple terms, grounding provides a pathway for electrical current to flow safely away from the machine and into the ground, preventing potential hazards such as electrical shocks, fires, or damage to the machine.
The significance of grounding woodworking machines cannot be overstated. Without proper grounding, there is an increased risk of electrocution if a fault occurs in the electrical system. Woodworking machines often involve high levels of electricity, which can be hazardous if not properly controlled. Grounding also helps prevent static electricity buildup that could potentially ignite flammable materials or cause sparks.
To effectively ground woodworking machines, it is essential to understand how electricity flows through them. Most woodworking machines have metal components that conduct electricity, which can become energized if there is a fault in the electrical system. By connecting these metal components to an earth ground, any excess current will flow directly into the ground instead of causing harm.
In summary, grounding is vital for both personal safety and optimal performance of woodworking machines. It prevents potential hazards such as electrocution or fires by providing a safe path for electrical current. By understanding the concept and ensuring proper grounding techniques are implemented, woodworkers can create a safe working environment for themselves and others while maximizing the efficiency and longevity of their machines.
Concept | Significance |
---|---|
Prevents electrical shocks | Reduces risk of injury or fatality |
Prevents fires | Protects property and surroundings |
Avoids damage to the machine | Prolongs the lifespan and functionality of the equipment |
Minimizes static electricity buildup | Prevents ignition of flammable substances or sparks |
Understanding the risks of ungrounded machines
Woodworking machines that are not properly grounded pose significant risks to both the operator and the functionality of the machines themselves. Understanding the potential hazards of using ungrounded woodworking machines is essential for ensuring a safe and effective working environment.
- Electrical Shock: One of the most immediate dangers of operating ungrounded woodworking machines is the risk of electrical shock. Without proper grounding, stray currents can build up in the machine’s components, leading to the potential for electric shocks when these components are touched. This poses a serious danger to operators, especially if they are not wearing proper protective gear or working in wet conditions.
- Fire Hazards: Ungrounded woodworking machines have an increased risk of electrical fires due to static electricity buildup and malfunctioning components. When electrical current is not properly controlled and grounded, it can arc or spark, potentially igniting nearby flammable materials such as sawdust or wood shavings. This can quickly escalate into a dangerous situation, endangering the operator, other workers, and property.
- Machine Functionality: In addition to safety concerns, ungrounded woodworking machines may experience reduced performance and functionality. The lack of proper grounding can lead to irregular power supply, voltage fluctuations, or interference with other electrical equipment in the workshop. These issues can result in decreased accuracy, inefficiency in cutting or shaping wood pieces, and overall poor machine maintenance.
To mitigate these risks associated with ungrounded woodworking machines, it is crucial to follow proper grounding procedures outlined by manufacturers and regulations. By dedicating time to ensuring that your machinery is correctly grounded, you will help create a safe working environment that maximizes productivity while minimizing potential hazards.
- Use appropriate grounding rods or conductors specifically designed for woodworking machinery.
- Ensure all wiring connections are secure and tightened properly.
- Regularly inspect all electrical components for signs of wear or damage.
Remember that grounding is not a one-time task; it requires regular maintenance and checks to ensure continued safety. By understanding the risks associated with ungrounded machines, you can prioritize proper grounding practices and create a safer working environment for everyone involved.
Tools and materials needed for grounding
Grounding rods and clamps
To effectively ground woodworking machines, you will need grounding rods and clamps. The grounding rod is typically made of copper or another conductive material and is inserted into the ground outside of your workshop. It provides a connection point for the grounding system. The clamps are used to securely attach the grounding wire to the machine.
Grounding wire
A key component of the grounding system is the grounding wire. It should be made of copper or another highly conductive material to ensure effective grounding. The length of the wire will depend on the distance between your woodworking machines and the grounding rod, so make sure to measure this before purchasing.
Wire connectors
Wire connectors are essential for connecting various components of the grounding system. You will need connectors to attach the grounding wire to both the woodworking machine and the grounding rod. These connectors should be compatible with the type and gauge of wire you are working with.
Electrical tape
Electrical tape is used to secure connections, insulate wires, and provide an extra layer of protection against electrical shocks or short circuits. Make sure to choose electrical tape that is specifically designed for use in high voltage applications and can withstand exposure to dust, heat, and moisture.
Multimeter
A multimeter is a versatile tool that measures various electrical properties such as voltage, current, and resistance. It can be used during testing and troubleshooting stages to ensure that your woodworking machines are properly grounded.
Additional tools
Depending on your specific setup, you may also need additional tools such as pliers, wire cutters/strippers, screwdrivers, wrenches, or drills for securing connections or making adjustments in order to properly ground your woodworking machines.
By ensuring that you have all the necessary tools and materials before starting the grounding process, you can effectively and safely ground your woodworking machines, minimizing the risk of electrical hazards and maximizing their performance.
Step-by-step guide on how to ground woodworking machines
Identify Components
The first step in grounding woodworking machines is to identify the key components that will need to be grounded. This includes the machine itself, as well as any electrical connections or accessories that may be attached. Take note of any metal parts that are in contact with the machine, such as the table or fence on a table saw.
Gather Tools and Materials
Before beginning the grounding process, gather all the necessary tools and materials. Some common items you will need include a grounding rod, copper wire or braided conductor, grounding clamps, screws or bolts, pliers or wire strippers for cutting and stripping wires, and a multimeter for testing conductivity.
Locate Grounding Point
Next, locate the appropriate grounding point for your woodworking machines. This is typically a metal surface or structure that can conduct electricity safely into the ground. Common grounding points include metal water pipes or building steel reinforcement bars. Make sure to choose a location that is stable and securely connected to the ground.
Attach Grounding Wire
Once you have identified the grounding point, attach one end of your copper wire or braided conductor to this location using a grounding clamp or similar connector. Ensure that the connection is tight and secure so that it does not come loose during operation.
Connect Grounding Wire to Machine
Next, connect the other end of the copper wire or braided conductor to a suitable metal part on your woodworking machine. This could be any exposed metal surface that is directly in contact with your hands while operating the machine – such as a metal body panel or frame.
Test Grounding System
After completing these steps, it is important to test your grounding system to ensure its effectiveness. Use a multimeter to measure the resistance between the grounding point and any metal parts of the woodworking machine. Ideally, you should have a low resistance reading, indicating that your grounding system is properly working.
Secure and Inspect
Lastly, secure all connections and inspect your grounding system for any signs of wear or damage. Check that wires are firmly attached and not frayed or exposed. Additionally, regularly inspect your grounding system during routine maintenance to ensure its continued effectiveness.
By following this step-by-step guide, you can effectively ground various types of woodworking machines, such as table saws, planers, routers, and more. Ensuring proper grounding is essential for both personal safety and optimal machine performance.
Common mistakes to avoid
When it comes to grounding woodworking machines, there are a few common mistakes that people often make. Understanding these mistakes and how to avoid them is crucial for maintaining safety and preventing any potential hazards. One common mistake is neglecting to properly inspect the grounding system before using a woodworking machine.
It’s important to ensure that all connections are secure and that there are no loose or damaged wires. Regularly checking the grounding system can help prevent electrical shock hazards.
Another mistake to avoid is using inappropriate or low-quality grounding materials. It’s essential to use materials that are designed specifically for grounding purposes and have the appropriate voltage rating. Using substandard materials may compromise the effectiveness of the grounding system and increase the risk of electrical accidents.
In addition, not following proper installation procedures can also be a significant mistake when grounding woodworking machines. Each machine may have specific instructions for proper grounding, so it’s essential to read the manufacturer’s manual carefully. Failing to follow these instructions can result in an ineffective grounding system and may void warranties.
To prevent these common mistakes when grounding woodworking machines, it is recommended to always conduct regular inspections of the grounding system, ensuring that all components are secure and undamaged. Additionally, invest in quality grounding materials that meet industry standards and have sufficient voltage ratings for the machines being used. Most importantly, closely follow the manufacturer’s instructions when installing or modifying the grounding system for each machine.
By avoiding these common mistakes, woodworkers can ensure a safe working environment when using grounded woodworking machines. Properly functioning grounds are vital in reducing electrical hazards and providing optimal performance from your woodworking equipment.
Testing and troubleshooting
Testing and troubleshooting are crucial steps in ensuring the effectiveness of the grounding system for woodworking machines. By conducting regular tests and addressing any issues that may arise, woodworkers can maintain a safe working environment and prevent potential accidents. This section will provide tips and techniques for testing the grounding system and troubleshooting common problems.
Testing:
- Visual Inspection: Begin by visually inspecting the grounding wiring, connectors, and connections for any signs of damage or loose connections. Ensure that all wires are properly attached and securely connected.
- Multimeter Test: Use a multimeter to measure the resistance between the machine’s metal body and a known ground point. The resistance should be low, ideally less than one ohm.
- Earth Ground Check: To verify if your grounding system is properly connected to earth ground, use an earth ground tester or clamp meter designed specifically for this purpose. Follow the manufacturer’s instructions to perform the test accurately.
Troubleshooting:
- Poor Ground Connection: If you find a high resistance reading during testing or suspect a poor ground connection, start by tightening all connections carefully. Replace any damaged wires, connectors, or grounding rods as necessary.
- Insufficient Grounding: If you are consistently experiencing electrical shocks when using your woodworking machines, it could indicate inadequate grounding. Revisit the grounding process following the step-by-step guide provided earlier in this article.
- Noise Interference: Sometimes, improper grounding can cause noise interference on electronic devices connected to woodworking machines. Investigate any buzzing sounds or flickering lights and address them by improving your grounding setup or implementing additional shielding measures.
Regularly perform these testing procedures to ensure that your grounding system remains effective over time. Remember that safety should always be prioritized when working with woodworking machines, so if you encounter persistent issues with your grounding system or are unsure about how to troubleshoot them effectively, consult a professional electrician.
By following these testing and troubleshooting techniques, woodworkers can identify and address grounding issues promptly, ensuring a safe and efficient working environment. Remember that a well-functioning grounding system is not only essential for personal safety but also for the optimal performance and longevity of woodworking machines.
Maintenance and periodic checks
Regular maintenance and periodic checks of the grounding system are essential to ensure continued safety and efficiency when using woodworking machines. Over time, the grounding system may deteriorate or become compromised, leading to potential safety hazards or reduced effectiveness of the machines. By incorporating regular maintenance and checks into your woodworking routine, you can mitigate these risks and maintain a safe working environment.
One important aspect of maintaining the grounding system is to visually inspect all components regularly. This includes checking the ground wire for any signs of damage or wear, such as frayed wires or loose connections. Additionally, inspect the grounding rod to ensure it is securely grounded in the earth and free from corrosion or other damage. Any damaged components should be repaired or replaced immediately to maintain an effective grounding system.
In addition to visual inspections, it is also crucial to perform periodic tests on the grounding system. One common method is using a multimeter to measure the resistance between electrical equipment and ground.
A low resistance reading indicates a well-grounded machine, while a high resistance reading may indicate a fault in the system that needs further investigation. It is recommended to conduct these tests at regular intervals, such as every six months or annually, depending on the frequency of machine use.
Regular maintenance and checks of the grounding system not only contribute to personal safety but also ensure optimal performance of woodworking machines. A proper grounding system helps prevent static electricity buildup, reduces the risk of electric shock or fire, and improves machine efficiency by providing a stable electrical pathway. By incorporating these maintenance practices into your woodworking routine, you can have peace of mind knowing that you are working with safe and reliable equipment.
Maintenance Tasks | Frequency |
---|---|
Visual inspection of ground wire connections | Monthly |
Visual inspection of grounding rod | Quarterly |
Resistance testing of grounding system | Biannually or annually |
Repair or replacement of damaged components | As needed |
Additional safety precautions
When it comes to working with woodworking machines, grounding is just one aspect of ensuring safety. In addition to grounding, there are several supplementary safety precautions that should be implemented to further protect oneself while operating woodworking machines. These precautions include wearing protective gear and following proper safety protocols.
One of the most crucial safety measures is wearing appropriate protective gear. This includes goggles or a face shield to protect your eyes from flying debris, as well as ear protection to guard against the loud noises produced by power tools. Additionally, wearing gloves can protect your hands from cuts and abrasions, while a dust mask or respirator should be worn to prevent inhalation of sawdust particles.
In addition to protective gear, it is important to follow proper safety protocols when using woodworking machines. Always read and follow the manufacturer’s instructions for each machine, as they contain specific operational guidelines and safety precautions. It is also important to keep the workspace clean and organized, ensuring that there are no tripping hazards or obstructions that could potentially cause accidents.
Furthermore, when using power tools, it is vital to maintain focus and concentration on the task at hand. Avoid distractions such as cell phones or other devices that may divert attention away from safe operation. Remember to never rush through a project and take breaks when needed to avoid fatigue which can lead to accidents.
By implementing these additional safety precautions alongside grounding woodworking machines, you can create a safer working environment for yourself and others. Following proper safety protocols and wearing protective gear will help minimize the risk of injuries while operating woodworking machines and allow you to focus on achieving optimal results in your projects.
Conclusion
In conclusion, grounding woodworking machines is of utmost importance for both personal safety and optimal machine performance. By understanding the concept of grounding and its significance in the context of woodworking machines, you can effectively mitigate potential hazards and ensure a safer working environment.
Throughout this article, we have explored the risks associated with using ungrounded machines and provided a step-by-step guide on how to properly ground various types of woodworking machines. We have also highlighted common mistakes to avoid during the grounding process and discussed testing, troubleshooting, maintenance, and periodic checks to ensure continued safety and efficiency.
However, it is crucial to remember that grounding alone is not sufficient to guarantee complete safety. It is essential to implement additional safety precautions such as wearing protective gear and following proper safety protocols while working with woodworking machines. These supplementary measures will further enhance your overall safety while using these powerful tools.
Frequently Asked Questions
How do you ground machinery?
Grounding machinery is an important safety measure to prevent electrical hazards and ensure the equipment functions properly. To ground machinery, a grounding conductor needs to be connected from the machinery’s metal frame to a grounding electrode, such as a grounding rod or a metal water pipe.
This establishes an electrical connection between the machinery and the ground, allowing any electrical fault or surge to be safely dissipated into the earth. It is crucial to follow local electrical codes and guidelines when grounding machinery to ensure it is done correctly and effectively.
How do you ground a dust collection system?
Grounding a dust collection system is essential for both safety and efficient operation. By properly grounding the system, you can minimize the risk of static discharge, reduce fire hazards, and prevent damage to equipment or personnel. To ground a dust collection system, several steps need to be taken. First, all metal components of the system should be electrically connected using conductive materials like copper wire or metal straps.
Next, these components should be bonded together through direct contact or by using conductive clips or straps to maintain continuity throughout the system. Finally, a grounding electrode should be installed nearby and connected to the metal components of the system using appropriate conductors. This provides a path for static charges to dissipate safely into the ground.
How do you reduce static in dust collection system?
Static in a dust collection system can cause various issues like material buildup, poor filtration efficiency, increased maintenance requirements, and even potential fire hazards. However, there are several ways to reduce static in such systems effectively. Firstly, incorporating anti-static features into the design of equipment can significantly help with static reduction. This includes using anti-static filters, hoses with conductive properties, and installing ionizers in critical areas where static buildup often occurs.
Additionally, ensuring proper airflow velocity within the ductwork can minimize particle friction that leads to static generation. Regular cleaning and maintenance of filters are also crucial for reducing static as clogged filters can exacerbate electrostatic charges within the system. Monitoring humidity levels and maintaining an appropriate moisture balance is another effective way to reduce static in dust collection systems, as higher humidity can mitigate static electricity buildup.
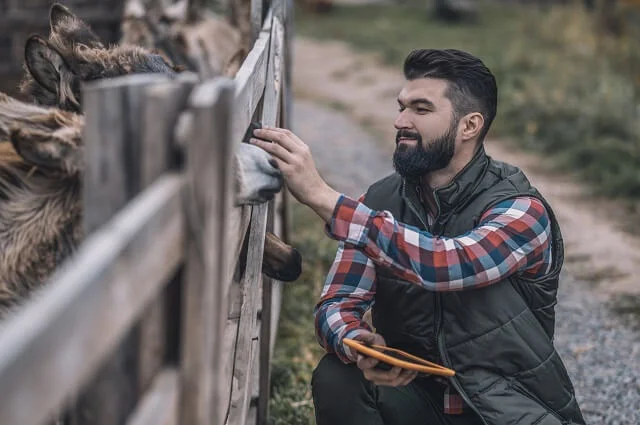
Hi everyone! I’m a woodworker and blogger, and this is my woodworking blog. In my blog, I share tips and tricks for woodworkers of all skill levels, as well as project ideas that you can try yourself.