Woodwork has long been admired for its natural beauty and craftsmanship, but what if there was a way to make it seem invisible? In this article, we will explore the art of concealing woodwork and discover the techniques and tools needed to achieve seamless results. Whether you are a seasoned woodworker or just starting out, mastering these invisible techniques can elevate the aesthetics of your projects to a whole new level.
Understanding the importance of seamlessness is crucial when it comes to woodworking. The goal is to create a finish that appears as if it has no seams or joints at all, giving the illusion that the piece is made from one solid piece of wood. This attention to detail not only enhances the overall appearance of the project but also highlights the skill and precision of the woodworker.
To achieve invisible woodwork, having the right tools and materials is essential. From sandpapers and fillers to stains and varnishes, each element plays a crucial role in creating seamless results. Throughout this article, we will provide a comprehensive guide on these essential tools and materials, helping you choose what works best for your specific project.
Before diving into the techniques and tips, proper preparation of the wood surface is key. We will outline the key steps required for achieving a smooth finish, ensuring that any imperfections are eliminated before moving forward. Additionally, we will delve into expert techniques for filling nail holes and concealing joints – an essential skill in creating invisible woodwork.
Join us on this journey as we explore various methods such as grain matching, concealed joinery techniques, choosing the right wood stain, applying varnishes and sealers – all with one objective in mind: how to make woodwork seems invisible. With our step-by-step instructions and helpful tips, you’ll be well on your way to achieving flawless finishes that leave even seasoned craftsmen amazed.
Understanding the Importance of Seamlessness
Woodwork is not just about building and constructing with wood; it is also an art form that requires attention to detail and a keen eye for aesthetics. One important aspect of mastering the art of woodwork is making it appear seamless and invisible. This section will delve into why achieving seamlessness in woodwork matters, highlighting the benefits and impact it can have on the overall aesthetics of a project.
When woodwork is seamless, it creates a sense of continuity and harmony in a space. Whether you are working on furniture, cabinetry, or architectural elements, having invisible woodwork allows the focus to be on the design and craftsmanship rather than on visible joints, seams, or imperfections. It gives off an impression of quality workmanship and attention to detail, elevating the overall appeal of the piece.
Additionally, making woodwork appear invisible can greatly enhance the visual flow of a room or space. Seamless woodwork facilitates smooth transitions between different components, such as when attaching trim or molding to walls or joining pieces together to create larger structures. By seamlessly blending into its surroundings, woodwork can create an uninterrupted visual experience that adds to the overall aesthetic value of a room.
To achieve this seamless look in woodwork, there are several key factors to consider. The choice of tools and materials plays a crucial role in ensuring precision and accuracy. Selecting high-quality wood with consistent grain patterns is essential for achieving smooth joins and concealed connections. Using proper techniques such as sanding and filling nail holes also contributes to creating invisible woodwork.
Essential Tools and Materials
In order to achieve seamless and invisible woodwork, having the right tools and materials is essential. These items will not only help you achieve a refined finish but will also make the process easier and more efficient. Here is a comprehensive guide to the essential tools and materials needed for creating invisible woodwork:
Sandpaper
Sanding is a crucial step in achieving a smooth finish on your woodwork. Make sure to have different grits of sandpaper ranging from coarse to fine. Coarser sandpaper (around 60-80 grit) is perfect for initial shaping and removing imperfections, while finer sandpaper (around 120-180 grit) will help you achieve a polished and smooth surface.
Wood Filler
To conceal any gaps or holes in your woodwork, it’s important to have a good quality wood filler on hand. Look for a filler that closely matches the color of your wood and dries quickly without shrinking or cracking. Apply the wood filler using a putty knife, ensuring it is leveled with the surrounding surface.
Wood Stain
Choosing the right wood stain plays a vital role in enhancing the natural beauty of your wood while still hiding imperfections. Opt for a stain that closely matches the original color of your wood or one that provides complete coverage if you want to change its appearance entirely.
Sanding Block
A sanding block is an essential tool for achieving even pressure and preventing uneven surfaces when sanding larger areas. It provides stability and makes it easier to maintain consistent pressure throughout the sanding process.
Putty Knife or Scraper
A putty knife or scraper comes in handy when working with excess adhesive, removing old finishes, or scraping off dried wood filler. It allows for precise and controlled application, ensuring smooth and seamless results.
Paintbrushes and Foam Brushes
Having a variety of paintbrushes and foam brushes will give you options when it comes to applying wood stain, varnish, or sealers. Ensure they are clean and dry before use to prevent any unwanted streaks or clumps.
When embarking on your woodworking project, be sure to have these essential tools and materials ready. They will make the process smoother, more efficient, and help you achieve that invisible finish you desire. Remember that investing in quality tools will provide better results in the long run.
Preparing the Wood Surface
To achieve a seamless and invisible woodwork, one of the key steps is to properly prepare the wood surface. Preparing the wood surface is essential for achieving a smooth finish and ensuring that no imperfections show through. By following these key steps, you can create a flawless base that will enhance the overall appearance of your finished project.
Step 1: Cleaning and Sanding
Before starting any woodworking project, it is crucial to clean the wood surface thoroughly. Remove any dust, dirt, or debris using a soft brush or vacuum cleaner. This will ensure that there are no particles trapped in the finish and that you have a clean working environment.
After cleaning, sanding is an essential step in preparing the wood surface. Start with coarser grit sandpaper (around 80 or 100) to remove any roughness or unevenness on the surface. As you progress, switch to finer grit sandpapers (such as 120, 180, or higher) for a smoother finish. Sand in the direction of the grain, applying consistent pressure to avoid creating dips or grooves.
Step 2: Filling Imperfections
During sanding, you may come across small imperfections such as knots, cracks, or holes in the wood. To ensure a flawless surface, it is important to fill these imperfections before moving forward. There are various options for fillers depending on your project and personal preference. Wood putty or epoxy-based fillers are common choices that effectively fill small holes and cracks.
When applying filler, follow the manufacturer’s instructions carefully. Use a putty knife or scraper to apply an even layer of filler over the imperfections while pressing it firmly into place. Allow it to dry completely before sanding again to achieve a smooth finish.
Step 3: Sealing and Priming
After sanding and filling imperfections, it is important to seal the wood surface before applying any finishes or stains. Sealing the wood helps to prevent the absorption of stain or finish unevenly, resulting in a more consistent and smoother appearance.
Apply a wood sealer or primer using a brush, roller, or spray gun, following the manufacturer’s instructions. Make sure to cover all surfaces evenly and allow the sealer or primer to dry completely before proceeding with further steps. This step is crucial for achieving a professional-looking finish.
By properly preparing the wood surface through cleaning, sanding, filling imperfections, and sealing, you are on your way to achieving a smooth finish for your invisible woodwork. These key steps lay the foundation for flawless results and elevate the overall aesthetic of your project. With attention to detail and patience during this preparation phase, your woodwork will seamlessly blend into its surroundings, creating an elegant and refined look.
Mastering the Art of Proper Sanding
Proper sanding is a crucial step in achieving a smooth and seamless finish for your woodwork. It not only helps to remove any imperfections or rough spots in the wood surface but also prepares it for the application of stains or finishes. In this section, we will explore various techniques and tips to help you master the art of proper sanding.
Choosing the Right Sandpaper Grit
One of the key factors in achieving a smooth finish through sanding is using the right grit sandpaper. The grit number indicates the coarseness or fineness of the sandpaper, with lower numbers being coarser and higher numbers being finer. It is important to start with a coarser grit to remove any roughness or unevenness on the wood surface and progressively move towards finer grits for a smoother finish.
Using Proper Sanding Techniques
When sanding, it is important to use consistent pressure and make long, even strokes along the grain of the wood. Avoid applying too much pressure as it can create dents or grooves in the surface. Sanding across the grain should be avoided as it can lead to scratches that are difficult to remove later on.
Additionally, it is recommended to use a sanding block or a piece of scrap wood wrapped in sandpaper for better control and even pressure distribution. This helps to prevent uneven sanding and allows for more precise results.
Checking Progress and Achieving a Uniform Surface
Throughout the sanding process, regularly check your progress by running your hand over the surface to feel for any imperfections or rough areas. If necessary, repeat sanding with finer grits until you achieve a uniformly smooth surface.
It is also important to note that different types of wood might require different approaches when it comes to sanding. Hardwoods like oak may need more aggressive sanding with lower grits initially, while softer woods like pine might require gentler sanding actions.
By mastering these sanding techniques and paying attention to the specific needs of your wood, you can achieve a flawless and seamless finish, making your woodwork seemingly invisible.
Choosing the Right Wood Stain
Wood staining is a crucial step in achieving invisible woodwork. It not only enhances the natural beauty of the wood but also allows you to conceal any imperfections or discolorations. Choosing the right wood stain can make a significant difference in creating a seamless finish. Here are some tips for selecting the perfect stain:
Consider the Type of Wood
Different types of wood absorb stains differently, so it’s important to consider the characteristics of your wood when choosing a stain. Hardwoods like oak, cherry, and mahogany tend to absorb less stain due to their dense nature, while softer woods like pine and cedar absorb more easily. Experimenting with test samples on your specific type of wood can help you determine how much stain will be needed to achieve the desired effect.
Determine the Color Palette
Choose a stain color that complements your overall design aesthetic. Whether you want a warm and rich tone, a cool and modern hue, or a natural and rustic look, there is a wide range of stain colors available to suit every preference. Consider the existing color scheme and decor in your space to ensure that the chosen stain will seamlessly blend in.
Test Samples
Before applying the stain on your entire piece of woodwork, it’s essential to test samples on inconspicuous areas or scrap pieces of wood. This allows you to assess how the stain will react with your specific type of wood and how many coats may be needed to achieve an even finish.
Application Technique
The technique used for applying the stain can significantly impact its appearance. Brushing on a thin layer with long, smooth strokes generally gives an even finish with no visible brush marks. However, wiping on or using foam brushes can provide more control over the application process and help achieve a desired level of transparency.
Choosing the right wood stain is an integral part of creating invisible woodwork. It allows you to enhance the natural beauty of the wood while effectively concealing any flaws or imperfections. Considering the type of wood, determining the color palette, conducting test samples, and applying the stain with care are essential steps towards achieving a seamless finish. With attention to detail and thoughtful selection, you can elevate the aesthetics of your woodwork and create an exquisite, invisible result.
Expert Techniques for Filling Nail Holes and Concealing Joints
When it comes to creating invisible woodwork, one of the most crucial aspects is ensuring that nail holes and joints are flawlessly concealed. The seamless finish achieved through these expert techniques adds to the overall aesthetic appeal of the project. Here, we will explore some tried-and-tested methods for filling nail holes and concealing joints.
- Wood Filler: Wood fillers come in different colors and formulations, making them suitable for various wood types. Select a filler that matches the color and grain of your woodwork for a seamless blend. Using a putty knife or scraper, apply the filler generously over the nail hole or joint, pressing it firmly into place. Allow it to dry completely before sanding it smooth. Remember to remove any excess filler on the surface of the wood.
- Epoxy Putty: Ideal for larger holes or voids, epoxy putty offers excellent durability and strength. It can be molded and shaped to fit precisely into the hole or joint, ensuring a tight seal. Follow the manufacturer’s instructions when mixing and applying epoxy putty to achieve optimal results. Once cured, sand it down gently until it is flush with the surrounding wood.
- Concealing Joints: For seamless connections between pieces of wood such as corners or miters, concealing joints is essential. Apply a thin layer of glue to both surfaces before joining them together. Wipe off any excess glue immediately using a damp cloth or sponge. Once dried, use fine-grit sandpaper to carefully smooth out any visible seams.
By employing these expert techniques for filling nail holes and concealing joints, you can enhance the invisible quality of your woodwork. Remember to take your time during each step ensuring precision and attention to detail. These methods will help you achieve a flawless finish that seamlessly blends in with the surrounding wood, creating a truly professional result.
Invisible Joinery Methods
When it comes to creating invisible woodwork, the methods used for joining pieces together are crucial. By employing invisible joinery methods, you can achieve seamless connections that not only enhance the overall aesthetics but also provide structural integrity. In this section, we will delve into some expert techniques that will help you unlock these seamless connections.
Traditional Methods
One of the tried and true invisible joinery methods is using traditional techniques such as mortise and tenon joints or dovetails. These methods have been used for centuries and have stood the test of time for good reason. The beauty of these joinery methods lies in their ability to create strong connections while remaining virtually invisible to the casual observer.
Mortise and tenon joints involve cutting a slot (the mortise) into one piece of wood and inserting a projecting piece (the tenon) from another piece into that slot. This method allows for a secure connection while keeping any visible signs of joint hidden within the wood itself. Dovetail joints, on the other hand, create interlocking shapes that provide both mechanical strength and visual appeal.
Modern Techniques
With advancements in woodworking technology, there are also modern techniques available that enable even more seamless connections. One such technique is using pocket hole joinery. This involves drilling an angled hole through one piece of wood and connecting it with screws to another piece from behind, leaving no visible fastener on the surface.
Another popular method is using biscuits or dowels to join two pieces together. Biscuits are small wooden discs inserted into slots cut along the edges of two pieces, acting as alignment aids and providing additional strength. Similarly, dowels are wooden rods inserted through corresponding holes in both pieces to create a sturdy bond.
Adhesive Techniques
Besides traditional and modern joinery methods, adhesive techniques play a significant role in creating invisible connections. Woodworkers often use high-quality wood glues or epoxy to bond pieces together. These adhesives not only provide exceptional strength but also have the advantage of being almost invisible once dried and sanded properly. It is crucial to apply the adhesive evenly and remove any excess before joining the pieces, ensuring a clean and seamless connection.
By mastering these invisible joinery methods, you can elevate the quality and aesthetics of your woodwork. Whether using traditional techniques, modern advancements, or adhesive methods, achieving seamless connections will enhance both the visual appeal and structural integrity of your woodworking projects.
The Power of Wood Grain Matching
Wood grain matching is a crucial technique to achieve seamless integration and make woodwork seem invisible. When the grains of two or more pieces of wood align perfectly, it creates a visual continuity that hides any visible joins or seams. This technique not only enhances the aesthetic appeal of the finished woodworking project but also adds a touch of elegance and sophistication.
To effectively match wood grain, it is essential to carefully select and prepare the wood pieces. Start by examining the patterns and characteristics of each piece to find those with similar grain patterns, color tones, and texture. This will help create a cohesive look when the pieces are joined together.
Once you have chosen the appropriate wood pieces, there are a few techniques you can use to ensure a seamless integration:
- Bookmatching: This technique involves cutting adjoining pieces from the same piece of wood, like opening a book. The result is symmetrical mirror images that create an exquisite effect. Bookmatching is especially effective for large surfaces such as tabletops or cabinetry doors.
- Butt Joint Grain Alignment: In projects where two separate pieces need to be joined together at right angles, matching the grains can camouflage the joint line. By aligning the grains correctly during assembly, it becomes difficult to spot where one piece ends and another begins.
- Veneering: Veneer is a thin layer of decorative wood that is applied over other materials like plywood or MDF (medium-density fiberboard). With veneering, it’s possible to achieve consistent grain patterns across larger surfaces or complex shapes.
Proper care should be taken throughout the process to ensure precise grain matching. It may involve rotating and flipping individual boards until they fit seamlessly with their neighboring pieces. Additionally, applying a clear finish can highlight the beauty of matched wood grain while protecting it from wear and tear.
Benefits | Techniques |
---|---|
-Enhances aesthetic appeal | -Bookmatching |
-Creates visual continuity | -Butt Joint Grain Alignment |
-Adds elegance and sophistication | -Veneering |
Finishing Touches
To achieve truly invisible woodwork, the proper use of varnishes and sealers is essential. These finishing touches not only enhance the natural beauty of the wood but also protect it from damage and wear over time. In this section, we will explore how varnishes and sealers play a crucial role in creating seamless and invisible woodwork, and provide tips for achieving the best results.
Varnishes and sealers are applied to wood surfaces to create a protective layer that shields the wood from moisture, dirt, and other external elements. They also add depth, richness, and sheen to the wood’s appearance, enhancing its natural beauty. When properly applied, these finishes can make joints and seams almost invisible, allowing for a seamless integration of different pieces of wood.
One important consideration when choosing varnishes or sealers is their transparency. For invisible woodwork, opt for clear or transparent finishes that allow the natural grain of the wood to show through. Matte or satin finishes are often preferred as they give a more subtle look compared to high-gloss finishes.
Varnish/Sealer Type | Features |
---|---|
Polyurethane Varnish | Durable finish with excellent protection against scratches and stains. |
Lacquer | Fast-drying finish that provides a high-gloss appearance. |
Shellac | Natural finish derived from insect resin; offers good protection but may require periodic upkeep. |
Water-Based Sealers | Environmentally friendly option with low odor and quick drying time. |
In addition to the type of varnish or sealer, proper application is crucial for achieving invisible woodwork. Make sure to carefully follow the manufacturer’s instructions and apply thin, even coats. Sanding between coats can help achieve a smoother finish.
By incorporating varnishes and sealers into your woodworking projects, you can elevate the aesthetics of your work while ensuring its longevity and durability. The right choice of finishes, combined with meticulous application techniques, will help you create seamless and invisible woodwork that will be admired for years to come.
How to Maintain and Preserve Invisible Woodwork
Maintaining and preserving invisible woodwork is crucial to ensure its longevity and durability. Despite the seamless and concealed nature of invisible woodwork, it still requires proper care and attention to keep it looking its best. In this section, we will explore some essential tips for maintaining and preserving invisible woodwork.
One important aspect of maintenance is regular cleaning. Dust, dirt, and grime can accumulate on the surface of the woodwork over time, compromising its appearance. To clean invisible woodwork, use a soft cloth or brush to gently remove any dust or debris. Avoid using abrasive cleaners or harsh chemicals as they can damage the finish of the wood. Instead, opt for a mild soap solution or specialized wood cleaner recommended by the manufacturer.
In addition to cleaning, protecting invisible woodwork from moisture is crucial for its preservation. Wood is prone to swelling and warping when exposed to excessive moisture or fluctuations in humidity levels. To prevent this, ensure that the room where the woodwork is installed has controlled humidity levels. Use a dehumidifier during humid months if necessary. It’s also important to wipe off any spills or moisture promptly to avoid stains or damage.
Furthermore, applying a protective coating such as varnish or sealer can contribute greatly to the preservation of invisible woodwork. These coatings provide an extra layer of protection against stains, scratches, and fading due to UV exposure. Before applying any protective coating, make sure to thoroughly clean and dry the wood surface. Follow the manufacturer’s instructions for application techniques and drying times.
By implementing these maintenance tips regularly, you can ensure that your invisible woodwork remains in excellent condition for years to come. Taking care of your invisible woodwork not only maintains its aesthetic appeal but also prolongs its lifespan, allowing you to enjoy its beauty for generations.
Conclusion
In conclusion, mastering the art of invisible woodwork techniques can truly elevate the aesthetics of your projects. By understanding the importance of seamlessness and following the key steps outlined in this article, you can achieve a smooth finish that appears flawless and seamless. The use of proper tools, materials, and techniques such as sanding, wood staining, filling nail holes, and utilizing invisible joinery methods all contribute to creating a finished product that looks seamless and professional.
One of the essential aspects to consider when aiming for invisible woodwork is grain matching. By selecting wood pieces with similar or complementary grain patterns, you can seamlessly integrate different sections for a cohesive appearance. Additionally, choosing the right varnishes and sealers can enhance the natural beauty of the wood while protecting it from wear and tear over time.
To ensure longevity and durability of your invisible woodwork, it is important to follow proper maintenance and preservation techniques. Regular cleaning, appropriate care techniques, and periodic inspections will help maintain the integrity of your projects for years to come.
Frequently Asked Questions
How do you make wooden seams disappear?
Making wooden seams disappear requires careful attention to detail and precision in woodworking techniques. The first step is ensuring that the wood pieces being joined are cut accurately and have smooth edges. This helps in achieving a tight fit between the pieces, minimizing visible gaps or seams. Next, using wood glue or adhesives specifically designed for woodworking, apply a thin layer to both surfaces being joined and press them firmly together.
It’s important to ensure that excess glue is wiped away before it dries to prevent any unsightly residue. After the glue has dried, sanding the joint area gently with fine-grit sandpaper will help to level and blend the seam further. Finally, finish the wood surface with appropriate staining or painting techniques that match the rest of the piece, effectively camouflaging any remaining minor imperfections.
How do you hide timber joints?
Hiding timber joints can be achieved through various methods depending on the project and desired aesthetic outcome. One common approach is using dowels or biscuits during assembly as they create strong joints while reducing visibility of connection points. These small wooden elements are inserted into pre-cut holes in corresponding positions on both pieces of timber before applying adhesive and joining them together.
Another method involves incorporating decorative features like molding or trim around timber joints to divert attention from the connection itself. By adding these additional embellishments, focus is shifted towards the overall design rather than specific joint areas. Additionally, using wood filler or putty can help conceal small gaps around timber joints by filling them in and creating a seamless appearance when sanded and painted.
How do you fill a gap in a wooden joint?
Filling a gap in a wooden joint entails utilizing suitable materials to bridge and disguise any spaces between connected pieces of wood. Depending on the size of the gap, there are several options available for filling it effectively. For smaller gaps, wood filler or putty can be used by pushing it into the space until it is level with surrounding surfaces, then smoothing out excess material once dry before refinishing.
For larger gaps, inserting wooden shims or wedges into the joint can help close the distance and create a tighter fit. These shims are trimmed or sanded to match the surface level and then secured in place using glue or nails before being finished to blend with the rest of the woodwork. Overall, selecting a filling method that matches the color and grain pattern of the wood will help achieve an inconspicuous result.
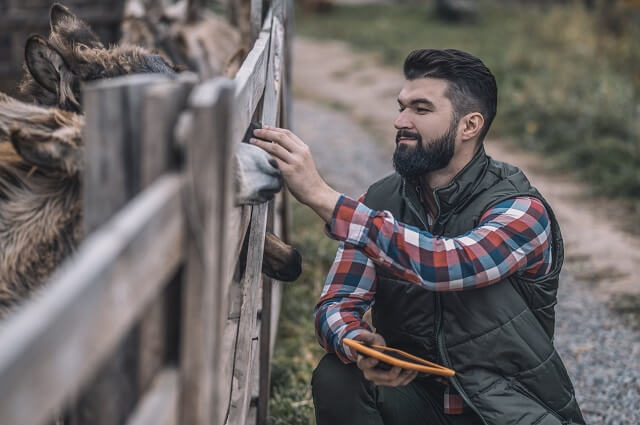
Hi everyone! I’m a woodworker and blogger, and this is my woodworking blog. In my blog, I share tips and tricks for woodworkers of all skill levels, as well as project ideas that you can try yourself.