CNC (Computer Numerical Control) woodworking machines have revolutionized the way woodworkers create intricate and precise designs. Whether you’re a professional carpenter or a passionate hobbyist, building your own CNC woodworking machine can open up endless possibilities for your projects. In this article, we will guide you through the process of constructing your own CNC woodworking machine, from the basic components and functionality to the assembly and testing of the machine.
To get started, it’s important to understand what CNC means and why it is significant in woodworking. CNC refers to the ability of a machine to be controlled by a computer program to carry out specific movements precisely. This level of precision allows woodworkers to produce complex designs, intricate patterns, and consistent cuts that would be challenging or time-consuming to achieve with traditional manual methods.
Before diving into the construction process, we will provide an overview of the essential components and functionality of a CNC woodworking machine. From motors and electronics to control systems and spindles, each part plays a vital role in ensuring smooth operation and accurate results. By understanding these basics, you’ll be well-equipped to choose the right materials and tools for building your own CNC woodworking machine.
Building your own CNC woodworking machine is an exciting journey that requires careful planning and attention to detail. The next sections will delve into choosing the right materials and tools for construction, designing and planning your machine, constructing its frame and structure for stability, installing motors and electronics, building a reliable Z-axis for precision work, configuring software for control, troubleshooting common issues, and ongoing maintenance.
By following this comprehensive guide, you’ll gain valuable knowledge on creating a powerful yet cost-effective DIY CNC woodworking machine that suits your specific needs. So let’s get started on this exciting adventure of empowering yourself as a woodworker with the capabilities of advanced technology.
Choosing the Right Materials and Tools for Building a CNC Woodworking Machine
Building a CNC woodworking machine requires careful consideration of the materials and tools needed to ensure its efficiency and durability. When it comes to selecting the right materials, it is important to prioritize strength, stability, and resistance to wear and tear. Here are some essential materials required for constructing a CNC woodworking machine:
- Frame Materials: The frame is the backbone of your CNC machine, providing support and stability. It is recommended to use a rigid material such as aluminum extrusion or steel square tubing for the frame construction. These materials offer excellent strength-to-weight ratio, ensuring the machine can handle demanding woodworking tasks.
- Working Surface Materials: The working surface or table of the CNC machine should be flat, smooth, and resistant to warping. Good options include MDF (Medium-Density Fiberboard), plywood with laminates, or aluminum plates. Consider adding T-slots on the working surface to accommodate clamps or fixtures for securing your workpieces.
- Linear Motion Components: Selecting high-quality linear motion components such as linear rails, ball screws, and linear bearings is crucial for smooth and accurate movement of your CNC machine. Look for components that are durable, precision-made, and have low friction.
In addition to materials, sourcing high-quality components, motors, and electronics is vital for building an efficient CNC woodworking machine. Here are some key considerations:
- Motors: Stepper motors are commonly used in CNC machines due to their affordability and ability to provide precise control over movement. NEMA 23 or NEMA 34 stepper motors are popular choices for driving different axes of a CNC woodworking machine.
- Electronics: You will need a reliable controller board that communicates with your computer and controls the movements of the machine based on G-code instructions. Additionally, drivers that connect the controller board with the stepper motors are required.
- 3.Tools and Equipment: To assemble your CNC woodworking machine, you will need basic hand tools such as screwdrivers, wrenches, and Allen keys. Power tools like a drill, table saw, and angle grinder might also be necessary depending on your specific design.
By carefully selecting the right materials and sourcing high-quality components and tools, you can significantly improve the performance and longevity of your CNC woodworking machine. Taking the time to research and invest in these essential elements will ensure that your DIY project results in a reliable and efficient machine that can handle various woodworking tasks with precision.
Designing and Planning Your CNC Woodworking Machine
Designing and planning your CNC woodworking machine is a crucial step in the construction process. Before building the machine, it is important to create a blueprint or 3D model that will serve as a guide throughout the construction process. This allows you to visualize the final product and make any necessary adjustments before beginning the actual build.
When designing your CNC woodworking machine, it is essential to identify the dimensions and specifications of each component. This includes determining the size of the frame, the length and width of the working area, as well as other specific measurements such as the clearance for tool movement. Additionally, you need to consider factors such as weight capacity and rigidity to ensure that your machine is strong enough to handle various woodworking tasks.
Another consideration in designing your CNC woodworking machine is assessing the space requirements for installation and operation. You will need to determine where you plan on placing your machine and consider factors such as whether you have enough space for proper ventilation, wiring connections, and easy access for maintenance. It is important to have ample space around the machine so that you can comfortably work on larger wood pieces without obstruction.
By carefully designing and planning your CNC woodworking machine, you can ensure that it meets your specific needs and requirements. Taking the time to create a well-thought-out design will save you time and potential mistakes during construction. With a clear plan in place, you can proceed confidently with constructing your CNC woodworking machine.
Constructing the Frame and Structure of Your CNC Woodworking Machine
Building a sturdy and reliable frame is a crucial step in constructing a CNC woodworking machine. The frame provides the structure and stability necessary for accurate cutting and carving. To construct the frame, follow these step-by-step instructions:
- Determine the size and dimensions of your machine: Before starting the construction process, it’s important to determine the size of your machine based on your woodworking needs and available workspace. Measure the dimensions of each component and plan accordingly.
- Select suitable materials: Choose strong and rigid materials for building the frame, such as aluminum extrusion, steel or hardwood. These materials provide adequate strength while minimizing flexing during operation. Consider the weight of the components when selecting materials.
- Cut and assemble the frame parts: Use a miter saw or a circular saw with appropriate blades to cut the material into required lengths according to your design specifications. Assemble the parts using brackets, corner connectors, or screws, ensuring tight connections for stability.
- Ensure proper alignment: Verify that all angles are 90 degrees using a square tool to ensure proper alignment of the frame. Double-check that all joints are securely fastened to prevent any wobbling or movement during operation.
- Reinforce critical areas: Identify areas that may require additional support for enhanced rigidity and strength, such as corners or joints where vibrations may occur. Reinforce these areas by adding gussets made from metal plates or plywood.
- Check for levelness: Place a level tool across different sections of the frame to ensure it is level on all sides. Adjust as necessary by adding shims or making slight modifications to achieve proper balance.
By following these steps, you can construct a solid and stable frame for your CNC woodworking machine, providing a strong foundation for precise cutting and carving operations.
Materials Needed
- Aluminum extrusion or steel beams.
- Brackets or corner connectors.
- Screws.
- Metal plates or plywood for reinforcement.
- Level tool.
- Miter saw or circular saw.
- Square tool.
Tools Required
- Drill with appropriate drill bits.
- Screwdriver or screw gun.
- Miter saw or circular saw.
- Square tool.
- Level tool.
Installing the Motors, Electronics, and Control System
Installing the Motors and Electronics
When it comes to building a CNC woodworking machine, one of the crucial steps is installing the motors and electronics. The motors are responsible for controlling the movement of the machine, while the electronics ensure that all components work together seamlessly. In this section, we will explore different types of motors suitable for a CNC machine, discuss how to connect and calibrate them, as well as provide guidance on setting up the electronic components for optimal performance.
Exploring Motor Options
Before diving into the installation process, it is important to choose the right motors for your CNC woodworking machine. There are various types of motors to consider, including stepper motors and servo motors. Stepper motors are commonly used in DIY CNC machines due to their affordability and precision. On the other hand, servo motors offer higher power and speed but come at a higher cost.
When selecting motors, it is essential to consider factors such as torque requirements and desired cutting speeds. Be sure to check motor specifications to ensure compatibility with your machine design. Researching online forums or consulting experienced builders can also provide valuable insights into which motor options would work best for your specific woodworking needs.
Connecting Motors and Calibrating Movement
Once you have chosen the appropriate motors for your CNC woodworking machine, it is time to connect them. Referencing your blueprint or 3D model can help guide you in positioning each motor correctly. Securely attach each motor using suitable brackets or mounting solutions provided with or purchased separately from the motor manufacturers.
After connecting each motor, calibration is necessary to ensure accurate movement. This involves configuring settings such as steps per millimeter or inch of travel in both the X and Y axes based on your design specifications. Most modern control systems provide software features that facilitate easy calibration. Following manufacturer instructions or referring to online tutorials can assist you in successfully calibrating your machine’s movement.
Setting Up the Control System and Electronics
In addition to motors, a CNC woodworking machine requires electronic components for proper operation. These include a control system, such as a CNC controller board or computer interface, as well as wiring and power supply units. The control system is responsible for interpreting commands from software and translating them into physical movements by the motors.
Carefully read the instructions provided with your chosen control system to understand how it functions and how to properly connect it to the motors and other electronic components. Most systems require connecting each motor to specific driver boards that receive signals from the controller and send appropriate voltages/currents to manipulate motor movement accurately.
It is crucial to follow safety guidelines provided by the manufacturer when working with electronic components, especially regarding power connections. Take precautions such as wearing insulated gloves, turning off power before making any electrical connections, and double-checking all connections before powering up the machine.
By carefully selecting suitable motors, connecting them correctly, and setting up the control system, you can ensure that your CNC woodworking machine is ready for operation. The next section will focus on building the Z-axis and spindle for precision woodworking.
Building the Z-Axis and Spindle for Precision Woodworking
Building the Z-Axis and Spindle is a crucial step in constructing a CNC woodworking machine that ensures precision and accurate depth control. The Z-Axis refers to the vertical movement of the spindle, which determines how deep the tool cuts into the wood. It is essential to understand the importance of a well-constructed Z-axis for achieving high-quality woodworking results.
To begin building the Z-Axis, it is necessary to select the appropriate components and materials. This includes acquiring stepper motors, lead screws or ball screws, linear bearings, and an anti-backlash nut. These components are responsible for precisely controlling the movement of the spindle along the vertical axis.
The next step involves installing and calibrating the Z-Axis. Careful alignment and adjustment are important to ensure that it moves smoothly and accurately. Proper alignment can be achieved by mounting the linear bearings securely and making sure they are parallel to each other.
Once the linear bearings are installed, attach them to a sturdy frame or gantry structure. It is crucial to ensure that this frame provides stability and rigidity to prevent any unwanted movement during operation. Additionally, integrating additional support elements such as braces or cross supports can further enhance stability.
After securing the Z-Axis mechanism, it is time to focus on selecting an appropriate spindle for woodworking tasks. The spindle is responsible for holding various cutting tools like router bits, end mills, or drills. Consider factors such as power rating, speed range, collet type compatibility, noise levels, and dust collection capabilities when choosing a suitable spindle.
Installing and calibrating the chosen spindle involves attaching it securely to the Z-Axis mechanism. This may require adjusting belt tension or ensuring proper tool holder alignment with respect to your workpiece.
Configuring and Testing the Software for CNC Woodworking Machine Control
Configuring and testing the software for CNC woodworking machine control is a crucial step in the construction process. The software used to control the machine determines its capabilities and functionality, allowing users to design and execute precise woodworking tasks. In this section, we will explore popular software options for controlling a CNC machine, provide installation and configuration instructions, and discuss how to test and troubleshoot the software to ensure proper functionality.
Identifying Popular Software Options
When it comes to controlling a CNC woodworking machine, there are several software options available on the market. One popular choice is Mach3, which offers a user-friendly interface and comprehensive features for 2D and 3D woodworking projects. Another commonly used software is GRBL, which is an open-source option that allows for more customization and flexibility in programming.
Installation and Configuration Instructions
Once you have chosen the software that best suits your needs, the next step is to install it onto your computer or controller. Most CNC software packages come with detailed installation instructions that are specific to each program. Follow these instructions carefully to ensure a successful installation.
After installation, you will need to configure the software to work with your specific machine. This typically involves selecting the appropriate machine type (such as CNC router or milling machine), specifying the dimensions of your work area or table size, setting up motor configurations (step per unit), and defining axis directions.
Testing and Troubleshooting
Once you have configured the software, it is essential to test its functionality before moving forward with your woodworking projects. Test each axis individually by commanding movements using the control panel within the software. Ensure that all movements are accurate and aligned with your commands.
If you encounter any issues during testing, such as incorrect movement or error messages, it is important to troubleshoot these problems promptly. Start by double-checking your configuration settings for accuracy. Verify that your motors are correctly wired and that the connection to the controller is secure. In some cases, you may need to adjust motor settings or fine-tune other configurations within the software.
By configuring and testing the software properly, you can ensure that your CNC woodworking machine operates smoothly and accurately. Taking the time to understand each software’s features and capabilities will also enable you to fully utilize its potential in executing complex woodworking tasks. Remember to consult the user manuals and online resources provided by the software developers for additional guidance and support during this process.
Maintaining and Troubleshooting Your CNC Woodworking Machine
Once you have built your DIY CNC woodworking machine, it is important to properly maintain and troubleshoot it to ensure optimal performance and longevity. Regular maintenance will help prolong the lifespan of your machine, while troubleshooting techniques will help address any mechanical or electrical issues that may arise. Here are some tips to help you with maintaining and troubleshooting your CNC woodworking machine.
Firstly, routine maintenance is crucial for keeping your machine in good condition. Regularly clean the machine to remove dust and debris that can accumulate during use. It is also important to regularly lubricate the moving parts of the machine to ensure smooth operation. Check for any loose screws or bolts and tighten them if necessary. Additionally, regularly inspect the wiring connections and electrical components for any signs of damage or wear.
When it comes to troubleshooting, it is important to first identify the cause of the issue. If you notice any abnormalities in the movement or performance of the machine, start by checking all connections and wiring to ensure they are secure.
If there are issues with specific components such as motors or electronics, refer to the manufacturer’s instructions for troubleshooting guidelines. Additionally, it can be helpful to consult online forums or seek advice from experienced CNC woodworking enthusiasts who may have encountered similar issues.
In some cases, upgrades or improvements may be necessary to enhance the performance of your CNC woodworking machine. This could involve upgrading certain components such as motors or electronics for increased speed and precision. It could also involve adding additional features or functionality based on your specific woodworking needs. When considering upgrades, thoroughly research the compatibility of new components with your existing setup before making any modifications.
By properly maintaining and troubleshooting your DIY CNC woodworking machine, you can enjoy many years of accurate and efficient woodwork projects. Remember to regularly perform routine maintenance tasks, troubleshoot any issues promptly, and consider upgrades or improvements when needed. With a well-maintained machine at your disposal, you can fully explore the limitless possibilities of woodworking and unlock your creative potential.
Conclusion
In conclusion, building your own DIY CNC woodworking machine can be a rewarding and fulfilling project. By following the step-by-step instructions outlined in this guide, you will have a deeper understanding of how a CNC machine works and the skills needed to construct one from scratch.
Having a CNC woodworking machine at your disposal offers numerous benefits. Firstly, it allows for unparalleled precision and accuracy in your woodworking projects. With the ability to program the machine to make intricate cuts and designs, you can achieve professional-level results with ease. This opens up a whole new world of possibilities when it comes to creating custom furniture pieces or intricate wood carvings.
Furthermore, a DIY CNC woodworking machine gives you the freedom to customize it according to your specific needs and preferences. You can choose the materials, components, and software that best suit your workflow and desired outcomes. This flexibility ensures that your machine is not only tailored to meet your current woodworking requirements but also allows for future upgrades or improvements as your skills progress.
Frequently Asked Questions
Is it cheaper to build or buy a CNC machine?
When considering whether it is cheaper to build or buy a CNC machine, several factors come into play. Building a CNC machine from scratch can potentially be cheaper upfront, especially for those who are skilled in building and have access to the necessary tools and materials at lower costs. However, it is important to consider the time and effort required in building a CNC machine, as well as the potential need for troubleshooting and additional expenses that may arise during the process.
On the other hand, buying a pre-built CNC machine may have a higher initial cost, but it often comes with technical support, warranty coverage, and ready-to-use functionality. Ultimately, the decision between building or buying a CNC machine depends on an individual’s specific needs, budget, skill level, and available resources.
Can I make my own CNC?
Yes, it is possible to make your own CNC machine. Many DIY enthusiasts and hobbyists have successfully built their own CNC machines using readily available plans or by customizing existing designs. The level of complexity involved in building your own CNC machine depends on factors such as its size, precision requirements, and intended purpose.
There are various online resources that provide step-by-step guides, tutorials, and forums where individuals can seek advice from others who have already undertaken similar projects. Additionally, having some knowledge of electronics, software programming, mechanics, and woodworking can be advantageous when embarking on this endeavor.
What do I need to build my own CNC?
Building your own CNC machine requires several key components and tools. Firstly, you will need a sturdy frame or structure to house all the moving parts of the machine securely. The choice of material for the frame can range from aluminum extrusions to steel beams depending on desired rigidity and budget considerations. Secondly, you will need motors to control the movement of different axes within the CNC machine. Stepper motors are commonly used due to their precise control capabilities at relatively low costs compared to servo motors.
These motors require drivers that interpret signals from controller boards that direct the motion. Additionally, a spindle or router is necessary to perform cutting or milling tasks. Other essential components include a controller board, power supply, limit switches, wiring, and various nuts and bolts for assembly. Moreover, you will need software to generate the tool paths and G-code instructions that control the movement of your DIY CNC machine. Different software options are available, ranging from free open-source programs to more advanced commercial packages that offer additional features and support.
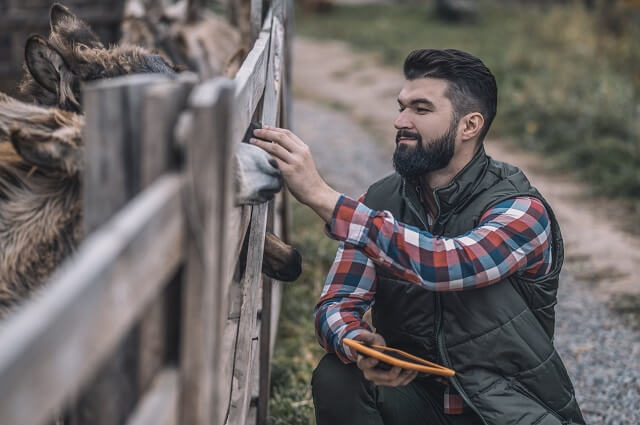
Hi everyone! I’m a woodworker and blogger, and this is my woodworking blog. In my blog, I share tips and tricks for woodworkers of all skill levels, as well as project ideas that you can try yourself.