Woodworking projects require a high level of precision, efficiency, and safety. One tool that can greatly enhance these aspects is a flexible drive shaft. In this article, we will explore the importance of a flexible drive shaft in woodworking and how it can improve your projects.
A flexible drive shaft is a crucial component in many woodworking tasks, allowing for greater maneuverability and accuracy. It serves as a bridge between the motor and the tool, transmitting power from the source to the working end with flexibility and ease. This flexibility enables woodworkers to navigate tight corners, intricate designs, and hard-to-reach areas that would otherwise be challenging or impossible without it.
Not only does a flexible drive shaft enhance precision, but it also improves efficiency in woodworking. By providing a direct connection between the motor and tool with minimal loss of power, it ensures optimal performance and effectiveness. Woodworkers can achieve smoother cuts, faster shaping, and more efficient sanding by using a flexible drive shaft.
Furthermore, safety is paramount in any woodworking endeavor. A flexible drive shaft plays a crucial role in ensuring safe operation. By allowing woodworkers to distance themselves from potentially dangerous machinery components such as spinning motors or sharp cutting tools, it reduces the risk of accidents or injuries. The flexibility of the drive shaft also minimizes vibration transfer from the tool to the operator’s hand, reducing strain and fatigue during prolonged use.
In this article, we will delve into the basics of what a flexible drive shaft is and how it functions in woodworking projects. We will also provide a step-by-step guide on creating your own flexible drive shaft for woodworking purposes.
Additionally, we will discuss important considerations such as material selection, maintenance tips, safety guidelines, and alternative options available for achieving similar results without using a flexible drive shaft. Join us as we explore this indispensable tool for enhancing precision and efficiency in woodworking projects.
Understanding the Basics
A flexible drive shaft is a crucial tool in woodworking that enhances precision, efficiency, and safety in various tasks. In order to fully understand its significance, it is important to define what a flexible drive shaft is and how it functions in woodworking projects.
A flexible drive shaft is a mechanical device used to transmit rotary motion from one end to another in a flexible manner. It consists of a long tube or casing made of high-quality steel or other durable materials. Inside the casing, there are multiple layers of wound wire coils that provide flexibility while maintaining strength and torque transmission.
The purpose of a flexible drive shaft in woodworking is to transfer power from the motor or engine to various cutting tools or attachments. By using this mechanism, woodworkers are able to achieve precise control over their tools, even when working on intricate and delicate designs. The flexibility of the drive shaft allows for greater maneuverability and access to tight spaces, making it an essential tool for shaping, carving, routing, and polishing wood surfaces.
Understanding the composition and construction of a flexible drive shaft can help woodworkers better utilize this tool for their projects. The outer casing is typically made of steel tubing for durability and resistance against bending or torsion. Inside the casing are several layers of tightly coiled wires made from spring steel or stainless steel, which provide the necessary flexibility while ensuring optimum torque transfer.
In addition to the coiled wires, a lubrication system is integrated into the design of a flexible drive shaft. This system serves two purposes: reducing friction between the wires during rotation and providing cooling for the assembly. Proper lubrication helps prolong the life of the drive shaft by minimizing wear and tear on its components.
To create a functional flexible drive shaft for woodworking projects, certain tools and materials are required. A comprehensive list includes:
- High-quality steel tubing for the outer casing.
- Spring steel or stainless steel wire coils.
- Lubrication system components such as oilers and fittings.
- Wire cutters or a wire cutting machine for cutting the coils to the desired length.
- A vise or clamp for securing the casing during assembly.
- Screwdrivers and wrenches for attaching components.
It is important to source these materials from reputable suppliers to ensure their quality and reliability. Woodworking supply stores, hardware stores, or online retailers specializing in tool parts and accessories are effective sources for acquiring these materials.
Tools and Materials Required for Making a Flexible Drive Shaft
To create a flexible drive shaft for woodworking, several tools and materials are required. Having the right equipment and components will ensure that the drive shaft is constructed properly and functions effectively. Here is a comprehensive list of tools and materials necessary for making a flexible drive shaft:
Tools:
- Drill press or lathe: A drill press or lathe is needed to shape the components of the drive shaft accurately.
- Saw: A saw will be used to cut various parts to size.
- File or sandpaper: These tools are essential for smoothing rough edges and ensuring a proper fit.
- Pliers: Pliers will be useful for bending and gripping small parts during assembly.
Materials:
- Flexible metal rod: The main component of a flexible drive shaft is a flexible metal rod, such as steel or brass, that can easily bend without losing its strength.
- Coupling connectors: These connectors are used to attach the flexible rod to other components, such as drill chucks or motor arbors.
- Bearings: Bearings provide support and reduce friction in the drive shaft assembly.
- Sleeves and collars: These components help secure and align different sections of the drive shaft.
It’s important to choose high-quality materials that can withstand the stress and torque involved in woodworking tasks. The flexibility of the metal rod should also be considered, as it should allow for smooth movement without breaking or kinking.
When acquiring these materials, it’s best to visit specialized woodworking supply stores or search online for reputable suppliers that offer high-quality components specifically designed for making flexible drive shafts.
Having all the necessary tools and materials ready before starting the construction process will make it easier to follow along with the step-by-step guide discussed later in this article. It’s also advisable to have spare parts on hand in case any components need replacement during construction or regular maintenance of the drive shaft.
Tools | Materials |
---|---|
Drill press or lathe | Flexible metal rod |
Saw | Coupling connectors |
File or sandpaper | Bearings |
Pliers | Sleeves and collars |
Step-by-Step Guide
Creating your own flexible drive shaft for woodworking can be a rewarding and cost-effective project. With the right tools and materials, you can construct a drive shaft that enhances precision and efficiency in your woodworking tasks. Follow this step-by-step guide to make your very own flexible drive shaft.
Step 1: Gather the Necessary Materials
Before you begin the construction process, make sure you have all the required materials on hand. You will need a flexible outer casing, a solid core wire or cable, coupling attachment adapters, and appropriate adhesive or soldering materials. The specific specifications for these materials depend on the size and complexity of your woodworking projects.
Step 2: Measure and Cut the Flexible Outer Casing
Start by measuring the length of outer casing needed for your flexible drive shaft. Use a sharp utility knife or wire cutters to cut the casing accurately.
Remember to factor in any additional length needed for coupling attachment adapters or other connectors.
Step 3: Prepare the Solid Core Wire or Cable
Next, measure and cut the solid core wire or cable according to the desired length of your drive shaft. Make sure to choose a wire or cable that is strong enough to withstand torque without breaking or bending excessively.
Step 4: Install Coupling Attachment Adapters
Attach coupling attachment adapters to both ends of the solid core wire or cable. These adapters will allow you to connect your drive shaft to power tools such as drills, motors, or rotary tools.
Ensure that they are securely fastened using adhesive suitable for metal-to-metal bonding or soldering if necessary.
Step 5: Insert Core Wire into Outer Casing
Carefully thread the solid core wire into the flexible outer casing until it reaches both ends. Take note not to bend or kink either component during this process.
If needed, apply lubricant to ease insertion.
Step 6: Secure the Drive Shaft Components
Using an appropriate adhesive or soldering technique, secure the drive shaft components together to prevent them from separating during operation. Allow adequate time for the adhesive to cure or the solder to set properly.
Step 7: Test and Adjust
Once your drive shaft is assembled, test it by connecting it to a power tool and observing its performance. Ensure smooth rotation without excessive vibrations or noises.
If adjustments are necessary, you may need to revisit previous steps to ensure proper fitting and attachment of components.
By following this step-by-step guide, you can construct your own flexible drive shaft for woodworking projects. Remember to prioritize safety throughout the construction process, including wearing appropriate protective equipment such as gloves and safety glasses. With your new drive shaft in hand, you can enhance precision and efficiency in your woodworking endeavors.
Tips for Choosing the Right Material for your Flexible Drive Shaft
When it comes to constructing a flexible drive shaft for woodworking, choosing the right material is crucial. The material used will determine the durability, flexibility, and overall performance of the drive shaft. Here are some tips to help you make an informed decision on selecting the most suitable material for your woodworking projects:
- Steel: Steel is a popular choice for flexible drive shafts due to its strength and durability. It can withstand heavy use and provide excellent torque transmission. However, steel can be more rigid compared to other materials, which may limit its flexibility in certain woodworking tasks.
- Nylon: Nylon is a lightweight and flexible material that offers good resistance to wear and tear. It is often used in applications where vibration damping is important. Nylon drive shafts are also known for their excellent electrical insulation properties.
- Fiberglass: Fiberglass drive shafts are lightweight, strong, and resistant to corrosion. They offer good flexibility while maintaining stability during operation. Fiberglass is an ideal choice for woodworking projects that require precision and accuracy.
- Carbon Fiber: Carbon fiber is another lightweight and durable material commonly used in high-performance applications. It provides excellent stiffness while offering superior strength-to-weight ratio. However, carbon fiber drive shafts can be more expensive compared to other materials.
- PVC/Vinyl: PVC or vinyl drive shafts are affordable options that offer decent flexibility and resistance to chemicals and moisture. They may not have the same level of durability as other materials but can still perform well in less demanding woodworking tasks.
It’s essential to consider the specific requirements of your woodworking projects when selecting the material for your flexible drive shaft. Factors such as the type of wood being worked on, the level of precision needed, and the duration of use should all be taken into account.
To ensure you choose the best material, it’s recommended to consult with experts or experienced woodworkers who have used different types of flexible drive shafts before making a decision. They can provide valuable insights and recommendations based on their own experiences.
Remember, the material you choose for your flexible drive shaft will ultimately impact the quality of your woodworking projects. Take the time to research and evaluate different options to make an informed choice that aligns with your specific woodworking needs.
Maintenance and Care of a Flexible Drive Shaft
Proper maintenance and care of a flexible drive shaft is crucial for ensuring its optimal performance and longevity. By following some simple steps, woodworkers can keep their drive shaft in excellent condition, allowing them to continue working with precision and efficiency. This section will provide a guide on how to properly maintain and care for a flexible drive shaft.
Cleaning
Regular cleaning is essential to remove any dirt, debris, or sawdust that may accumulate on the flexible drive shaft. Begin by disconnecting the shaft from the power source or machine it is attached to. Use a soft cloth or brush to gently wipe away any residue on the surface of the shaft. Be sure to clean both the inner and outer parts thoroughly.
Lubrication
To ensure smooth operation and minimize friction, lubricating the flexible drive shaft is necessary. Apply an appropriate lubricant along the length of the shaft, ensuring even coverage. Be cautious not to over-lubricate as excessive grease or oil can attract more debris and cause buildup over time. Check with the manufacturer’s guidelines for specific lubricants recommended for your particular drive shaft.
Storage Techniques
Proper storage of a flexible drive shaft can prevent damage and extend its lifespan. When not in use, it is advisable to store it in a clean and dry environment, away from direct sunlight or extreme temperatures. Coiling the shaft loosely or hanging it vertically can help avoid kinks or bends that may affect its flexibility.
Troubleshooting Tips
In case issues arise with your flexible drive shaft, there are some common troubleshooting steps you can take before seeking professional assistance. If you notice decreased flexibility or stiffness in certain areas of the shaft, try cleaning it thoroughly as mentioned earlier. Lubrication might also help alleviate this problem by reducing friction between internal components. However, if these measures do not resolve the issue, it is advisable to consult a professional for repair or replacement.
By following these maintenance and care guidelines, woodworkers can ensure that their flexible drive shaft remains in excellent working condition. Regular cleaning, proper lubrication, appropriate storage, and troubleshooting as needed will contribute to enhancing the overall performance and longevity of the shaft. By taking these simple steps, woodworkers can continue to rely on their flexible drive shaft for precise and efficient woodworking projects.
Safety Considerations when Using a Flexible Drive Shaft
When working with a flexible drive shaft in woodworking, it is important to prioritize safety to prevent accidents and ensure the well-being of the woodworker. The nature of a flexible drive shaft poses certain risks that need to be taken into consideration. By following safety guidelines and practicing proper usage techniques, woodworkers can work with confidence and minimize the likelihood of injuries or mishaps.
Personal Protective Equipment (PPE)
Before operating a flexible drive shaft, it is essential to wear appropriate personal protective equipment (PPE) to protect oneself from potential hazards. Always wear safety glasses or goggles to shield your eyes from flying debris and particles. Additionally, wearing ear protection such as earmuffs or earplugs is crucial due to the high noise levels generated by the machinery. Finally, don’t forget to wear close-fitting clothing that cannot become entangled in the rotating components of the drive shaft.
Secure Work Area
Creating a secure work area is vital for safe operation. Ensure that your workbench or workspace is clean, organized, and free from any clutter or obstructions that may interfere with the movement of the flexible drive shaft. Make sure there are no loose objects nearby that could potentially get caught in the rotating parts. It is also advisable to have sufficient lighting in your workspace to maintain visibility throughout the woodworking process.
Proper Technique
Adopting proper technique when using a flexible drive shaft can significantly reduce the risk of accidents. Always grip the tool firmly but comfortably while maintaining balance and stability during operation. Avoid placing excessive force on the tool as this may strain the motor or cause vibrations that could compromise precision and control over the woodworking task.
Inspect Regularly
Regular inspections of both the flexible drive shaft and its components are necessary to ensure safe usage. Check for any signs of wear and tear, such as fraying or damage to the drive shaft itself or the connections. If any defects are found, the flexible drive shaft should be promptly repaired or replaced to prevent failure during use.
Proper Storage
When not in use, it is important to store the flexible drive shaft in a safe and secure manner. Consider using a designated storage container or rack specifically designed for holding power tools. This will protect it from accidental damage and reduce the risk of injuries that may occur if it is left exposed and accessible to others.
By following these safety considerations when working with a flexible drive shaft, woodworkers can ensure their own safety and optimize their woodworking experience. It is crucial to always prioritize safety and take necessary precautions before operating any machinery in order to create a safe and productive workspace.
Alternatives to a Flexible Drive Shaft for Woodworking
While a flexible drive shaft is an essential tool in woodworking, there are alternatives available that can achieve similar results. These alternatives provide different options for woodworkers, depending on their specific needs and preferences. It is important to consider these alternatives and understand their strengths and limitations before making a decision.
One alternative to a flexible drive shaft is the use of direct-drive tools. Direct-drive tools, such as routers or drills with long flexible cables, can be used to perform tasks that would typically require a flexible drive shaft. These tools eliminate the need for a separate drive shaft component, as they have built-in flexibility in their design. They offer convenience and versatility, allowing woodworkers to switch between various applications without changing attachments.
Another alternative is the use of flexible extension bits or extensions. These extensions attach directly to power tools like drills or screwdrivers, providing additional length and flexibility. They are particularly useful when working in tight spaces or around obstacles where a rigid tool cannot reach. Flexible extension bits come in various lengths and can be fitted with different types of drill bits or screwdriver heads to suit specific woodworking tasks.
Alternative | Advantages | Limitations |
---|---|---|
Direct-drive tools (e.g., routers, drills with long flexible cables) | – Built-in flexibility
| – Limited length compared to a full-length flexible drive shaft
|
Flexible extension bits/extensions | – Increased reach and flexibility
| – Limited length compared to a full-length flexible drive shaft
|
It is important for woodworkers to assess their specific needs and the requirements of each project when considering alternatives to a flexible drive shaft. While these alternatives offer flexibility and convenience, they may not provide the same level of precision and efficiency as a dedicated flexible drive shaft.
Woodworkers should weigh the advantages and limitations of each alternative in relation to their desired outcome before making a decision. Ultimately, choosing the right tool or method will enhance woodworking precision and efficiency, leading to successful projects.
Conclusion
In conclusion, a flexible drive shaft is a crucial tool for enhancing precision and efficiency in woodworking projects. By understanding the basics of what a flexible drive shaft is and how it is constructed, woodworkers can create their own drive shaft or choose one that suits their specific needs.
Throughout this article, we have discussed the tools and materials required for making a flexible drive shaft, as well as provided a step-by-step guide on its construction. We have also offered tips on choosing the right material for the drive shaft and covered maintenance and care techniques to ensure optimal performance.
Safety considerations when using a flexible drive shaft were also addressed, emphasizing the importance of following proper usage techniques and guidelines to prevent accidents or injuries. Additionally, alternatives to the flexible drive shaft were explored, providing woodworkers with options that may achieve similar results in their woodworking projects.
In summary, incorporating a flexible drive shaft into your woodworking toolkit can greatly enhance precision and efficiency in various tasks. Whether you choose to make your own or acquire one from reputable sources, investing in this tool will undoubtedly benefit your woodworking endeavors.
With proper maintenance and care, coupled with adherence to safety guidelines, you can maximize the longevity and performance of your flexible drive shaft. So go ahead and start utilizing this tool to take your woodworking projects to new heights.
Frequently Asked Questions
How are flexible shafts made?
Flexible shafts are typically constructed by combining multiple layers of metal wires, typically steel or stainless steel, and casing them in a protective outer layer. The metal wires, often referred to as strands, are twisted together to form a flexible core that can transmit rotary motion. This core is then covered with layers of coatings and reinforcement materials to provide durability and flexibility.
The outer layer is usually made of rubber or plastic, which provides insulation and protection against external elements. As a result, flexible shafts exhibit the ability to bend while also transmitting rotational force from one end to the other.
Is a flex shaft the same as a Dremel?
While a flex shaft is commonly associated with the brand Dremel due to its widespread use with Dremel rotary tools, they are not exactly the same thing. A Dremel refers specifically to a brand of rotary tool that can accommodate attachments such as flex shafts, whereas a flex shaft is an accessory that can be used with various brands of rotary tools besides Dremel.
Essentially, a flex shaft is an extension that connects between the motorized part of the rotary tool (handpiece) and the tip where various attachments can be used.
How do you put a flex shaft on a rotary tool?
Attaching a flex shaft on a rotary tool generally involves several steps. First, ensure that your rotary tool has compatible dimensions for connecting the flex shaft attachment. Most common models have removable collets or chuck nuts near the tip where you would typically change attachments. Unscrew or loosen this collet or nut depending on your model’s design specifications but make sure it remains connected enough for stability during attachment.
Insert the end of the flex shaft attachment into this collet or chuck nut firmly until it fits securely into place without any wobbling or unevenness. Finally, tighten back down on the collet or nut to hold the flex shaft in position securely while allowing it to rotate freely when powered on. It’s important to consult your specific rotary tool’s manual for precise instructions as attachment methods may vary between models.
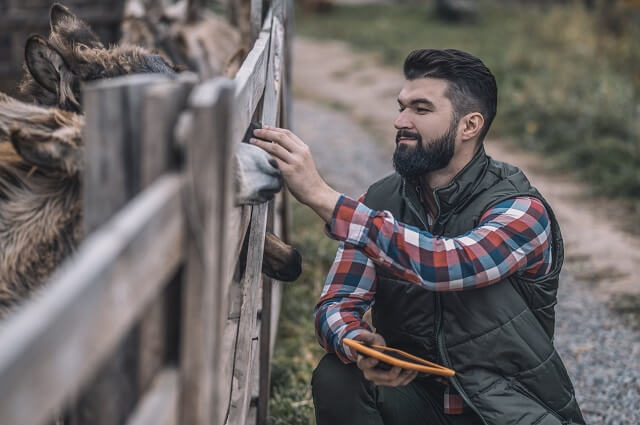
Hi everyone! I’m a woodworker and blogger, and this is my woodworking blog. In my blog, I share tips and tricks for woodworkers of all skill levels, as well as project ideas that you can try yourself.