Woodworking has long been a beloved craft, with artisans showcasing their skill and creativity through the creation of intricate wooden masterpieces. However, as technology continues to advance, traditional woodworking methods are being complemented – and even replaced – by innovative solutions. Enter the woodworking CNC machine.
In recent years, CNC (Computer Numerical Control) machines have gained immense popularity in the woodworking industry, revolutionizing the way wooden objects are designed and produced. These machines offer remarkable precision, speed, and versatility, allowing hobbyists and professionals alike to bring their creations to life with incredible accuracy.
The appeal of a woodworking CNC machine goes beyond its industrial applications; it extends into the realm of home workshops as well. Having a CNC machine at home means limitless possibilities for creating custom furniture, intricate wood carvings, and personalized decor pieces. Whether you aspire to explore your artistic side or enhance your craftsmanship skills, building a woodworking CNC machine opens up a whole new world of opportunities.
This article will serve as your comprehensive guide on how to make a woodworking CNC machine from scratch.
We will delve into the basics of CNC woodworking machines, provide step-by-step instructions on gathering tools and materials, guide you through designing the frame and axis system, help you select the right control system and spindle motor setup, teach you software configuration and testing techniques, emphasize safety precautions and maintenance practices, and even point you towards resources for expanding your CNC woodworking skills.
So let’s embark on this exciting journey together.
Understanding the Basics of CNC Woodworking
CNC machines, or Computer Numerical Control machines, have become an increasingly popular tool in the woodworking industry. These machines utilize computer programming to automate and control the movements of cutting tools, allowing for precision and efficiency in woodwork projects. Whether you are a hobbyist or a professional, having a woodworking CNC machine in your workshop can greatly enhance your capabilities and productivity.
At its core, a CNC machine is essentially a router with computer control. It takes digital instructions from design software and converts them into physical movement of cutting tools on the workpiece. This automation allows for precise and repetitive cuts, intricate designs, and complex shapes that would be difficult to achieve by hand.
There are different types of woodworking CNC machines available in the market, each suited for various applications and budgets. One common type is a gantry-style machine with a fixed table and moving gantry that houses the cutting tools. This type of machine is typically used for larger projects as it offers stability and can handle heavy workpieces.
Another type is the benchtop or desktop CNC machine which is more compact and portable. It operates on a smaller scale but still offers precision cutting abilities suitable for intricate designs on smaller pieces of wood. These machines are often less expensive than their larger counterparts and can be a good option for hobbyists or those with limited space.
In addition to size and portability considerations, there are other factors to consider when choosing a woodworking CNC machine such as spindle power (to determine cutting speed), axis travel (to determine maximum working area), controller interface (to ensure compatibility with design software), and overall build quality.
Woodworking CNC Machine Type | Description |
---|---|
Gantry-Style Machine | A larger machine with a fixed table and moving gantry; suitable for larger projects and heavy workpieces. |
Benchtop/Desktop CNC Machine | A more compact and portable machine; suitable for smaller projects and limited space. |
Gathering the Necessary Tools and Materials
To build a woodworking CNC machine, you will need a variety of tools and materials. This comprehensive list includes both essential components that are necessary for the basic functioning of the machine, as well as optional components that can enhance its capabilities. It is important to gather all the necessary items before starting the construction process to ensure smooth progress.
Tools:
- Screwdrivers and Allen wrenches: These tools will be needed for assembling various components of the CNC machine.
- Soldering iron and solder: Used for soldering electrical connections during the installation process.
- Wire cutters and strippers: Essential for cutting and stripping wires to the required size during wiring.
- Drill and drill bits: Needed for creating holes in the frame or other parts where necessary.
- Clamps or vices: Useful for holding pieces securely while making adjustments or assembling parts.
- Measuring tools: A tape measure, ruler, or calipers will be required to ensure accurate measurements throughout the construction process.
Materials:
- Aluminum extrusions or steel tubing: These will form the framework of your CNC machine and provide stability.
- Stepper motors: The choice of motors may vary depending on your specific requirements, but NEMA 23 stepper motors are commonly used in woodworking CNC machines.
- Linear motion components: Linear guides, lead screws, bearings, pulleys, belts, nuts, and couplers are necessary to create smooth movement along each axis (X-axis, Y-axis, Z-axis).
- Controller board with appropriate software compatibility: Choose a controller board that suits your needs and is compatible with your chosen software for controlling the machine’s movements.
- Power supply unit (PSU): A PSU provides power to different components of your CNC machine such as motors, controller boards, and sensors.
- Wiring harnesses: Various cables are required to connect different electrical components together.
Optional Components:
- Limit switches: These switches are used to define the limits of travel for each axis, ensuring the machine does not exceed its intended range.
- Spindle and router: Depending on your woodworking needs, you can choose a suitable spindle or router for cutting and shaping wood. The power and speed capabilities of the spindle should align with the requirements of your projects.
- Dust collection system: A dust collection system is recommended to keep your workspace clean by removing sawdust and debris generated during CNC machining.
Before starting the construction process, it is important to thoroughly research and identify all the necessary tools and materials required for building your CNC machine. This will ensure that you have everything you need on hand, saving time and avoiding delays during the construction process. Additionally, having a comprehensive list helps in budgeting for any optional components or specialty items that you may want to include in your woodworking CNC machine.
Designing the Machine’s Framework
Choosing the Right Materials
When designing the framework for your woodworking CNC machine, it’s crucial to start with the right materials. The frame should be sturdy enough to provide stability and support for the machine’s components while also being lightweight and portable. One commonly used material is aluminum extrusion, which is durable, lightweight, and easily customizable.
Another option is steel tubing, which offers excellent rigidity but may increase the overall weight of the machine. Consider your specific needs and preferences when selecting the material for your CNC machine’s frame.
Taking Measurements and Planning
Before you begin constructing the frame, take accurate measurements of your components and plan accordingly. Determine the ideal size of your machine based on factors such as the maximum workpiece size you’ll be working with and the available space in your workshop. Consider any potential limitations or restrictions you may have to ensure that your finished CNC machine fits comfortably in its designated location.
Once you have determined the dimensions of your frame, sketch out a detailed plan or use CAD software to create a 2D or 3D model. This step will help you visualize how all the components will fit together and allow you to identify any potential issues or adjustments that need to be made before construction begins.
Constructing the Frame
Now that you have chosen your materials and planned out your design, it’s time to start building the frame for your woodworking CNC machine. Begin by cutting or shaping the individual pieces according to your measurements and design specifications. Use precision tools such as mitre saws or tube cutters to ensure accurate cuts.
Next, assemble the frame by joining the pieces together using techniques such as welding, bolting, or screwing. Make sure to maintain proper alignment throughout this process to ensure a stable and square structure.
Consider incorporating additional supports or braces at strategic points of stress to reinforce stability. This could include cross beams or diagonal bracing. It is important to maintain the overall balance and weight distribution of the machine.
Once the frame is fully constructed, double-check for any loose or weak connections and make any necessary adjustments. Lastly, take the time to sand or polish down any rough edges or surfaces to ensure a professional finish.
Designing and constructing the framework of your woodworking CNC machine requires careful planning, accurate measurements, and precise construction techniques. By following these step-by-step instructions, you can create a sturdy yet portable frame that will provide a solid foundation for all the other components of your CNC machine.
Selecting and Installing the Control System
The control system is a crucial component of a woodworking CNC machine as it determines its functionality, precision, and ease of use. When selecting a control system for your DIY CNC machine, there are several factors to consider such as compatibility with your operating system, availability of software support, and budget constraints. Here is a step-by-step guide on how to choose the right control system for your woodworking CNC machine and install it successfully:
- Research and compare different control systems: Start by researching different control systems available in the market. Look for renowned CNC manufacturers that offer reliable products with good customer reviews. Compare features like compatibility with popular CAD/CAM software, ease of use, warranty, and technical support.
- Consider your requirements: Determine your specific needs regarding CNC woodworking projects. Are you planning to work on intricate designs or large-scale projects? Do you need advanced features like automatic tool changers or multi-axis capabilities? Consider these requirements when selecting a control system.
- Check compatibility: Ensure that the control system you choose is compatible with the operating system of your computer or laptop. Some systems are designed specifically for Windows-based machines while others are compatible with Mac or Linux systems.
- Software availability: Check if the control system comes with its own software or if it is compatible with widely used CAD/CAM software like Fusion 360, Vectric Aspire, or VCarve Pro. Having software support can enhance your woodworking capabilities and streamline your design process.
- Budget considerations: Set a budget for your control system and stick to it. Remember that more advanced features often come at a higher cost. Determine which features are essential for your woodworking projects and prioritize those within your budget limits.
- Installation process: Once you have selected a suitable control system, follow the manufacturer’s instructions for installation. This will typically involve wiring the control system to the CNC machine and connecting it to your computer. Make sure to carefully follow the provided guidelines to avoid any electrical or connectivity issues.
- Programming and setup: After installing the control system, you will need to program it according to your specific woodworking projects. This may involve configuring motor settings, defining tool paths, and setting up workpiece coordinates. Consult the user manual or seek online tutorials for guidance on programming your control system effectively.
By selecting and installing the right control system for your woodworking CNC machine, you’ll be able to achieve precise and reliable results in your projects. Properly wiring and programming the control system ensures smooth communication between your computer and CNC machine, enabling you to bring your designs to life with accuracy and efficiency.
Building the Axis System
Choosing the Right Components for the Axis System
When building a woodworking CNC machine, one of the most crucial aspects is constructing a reliable and accurate axis system. This system consists of three main components: the X-axis, Y-axis, and Z-axis. To ensure proper alignment and smooth movement, it is important to choose the right components for each axis.
For the X-axis, which controls the movement from left to right, linear guides or linear rails are commonly used due to their precision and stability. These guides support the motion of the gantry as it moves across the work area. It is essential to select guides that are compatible with your machine’s dimensions and weight requirements.
The Y-axis handles front-to-back movements and requires a robust linear motion system as well. Often, ball screws or rack and pinion drives are utilized in this axis for their ability to provide consistent and accurate positioning. Consider factors such as speed, precision, and load capacity when selecting components for this axis.
The Z-axis controls vertical movements, such as adjusting the cutting depth or tool height. Here, lead screws or ball screws combined with a stepper motor or servo motor are typically used for precise control. Pay attention to the weight capacity and rigidity of these components to prevent any deflection or inaccuracies during operation.
Ensuring Alignment and Smooth Movement
Once you have selected the appropriate components for each axis, it is crucial to ensure proper alignment and smooth movement for optimal machine performance.
To achieve proper alignment, make sure that all axes are perpendicular to each other using measurement tools like squares or spirit levels. This ensures that your machine moves accurately in all directions.
Additionally, ensure that all components are securely fastened together using brackets or mounting plates to maintain stability during operation. Loose connections can adversely affect both alignment and movement.
To achieve smooth movement along each axis, lubricate any linear rails or leadscrews with high-quality lubricants specifically designed for CNC machines. This reduces friction and promotes fluid motion, preventing binding or jerky movements.
Testing and Adjusting the Axis System
Once the axis system is constructed, it is crucial to thoroughly test and adjust its performance before moving forward. Start by manually moving each axis through its entire range of motion to ensure smooth movement without any binding or excessive play.
After the initial mechanical testing, connect the axis motors to the control system and perform some test runs using simple commands. Verify that each axis moves accurately according to the commands given by the control software.
It may be necessary to fine-tune parameters such as steps per unit, acceleration, and velocity within your control software to achieve accurate movement. Consult your controller manufacturer’s documentation for detailed instructions on adjusting these settings.
Regularly check and re-adjust the axis components as needed to maintain optimal performance over time. Additionally, regularly clean and lubricate all moving parts of the axis system to prevent wear and ensure longevity.
By following these in-depth instructions for constructing the axis system, woodworkers can ensure proper alignment and smooth movement of their CNC machines, enabling precise cuts and intricate designs.
Implementing the Spindle and Motor
When it comes to selecting the spindle and motor for your woodworking CNC machine, there are a few factors you need to consider. The spindle is responsible for rotating the cutting tool, while the motor provides the power necessary to drive the spindle. These components play a crucial role in determining the speed, performance, and precision of your machine.
There are several types of spindles available for woodworking CNC machines, including air-cooled spindles, water-cooled spindles, and even high-frequency spindles. Air-cooled spindles are typically more affordable and easier to maintain but may not be as powerful as other options.
Water-cooled spindles provide better cooling capabilities, ensuring that the spindle doesn’t overheat during longer cutting sessions. High-frequency spindles are known for their high-speed capabilities and are often used in professional settings where precision is essential.
Similarly, there are different types of motors compatible with CNC machines, such as stepper motors and servo motors. Stepper motors are popular choices due to their affordability and simplicity. They work by dividing a full rotation into several smaller steps, allowing precise control over positioning. On the other hand, servo motors offer higher torque at higher speeds, making them ideal for applications that require faster movement.
When selecting both the spindle and motor for your woodworking CNC machine, it’s vital to ensure compatibility with your specific machine design and intended use. Consider factors such as power requirements, torque capabilities, speed range, noise level, and precision needed for your projects.
Once you’ve selected the appropriate components for your CNC machine, it’s time to install them correctly. This process involves mounting the spindle onto the machine’s framework securely and connecting it to the motor using proper wiring techniques. It’s crucial to follow the manufacturer’s instructions and guidelines during the installation process to ensure optimal performance and safety.
Overall, implementing the spindle and motor for your woodworking CNC machine requires careful consideration of the specific requirements of your projects and understanding the capabilities of different components. By selecting the right components and installing them correctly, you can achieve efficient and precise cutting results with your CNC machine.
Configuring and Testing the Machine
Setting Up the Software
Once the woodworking CNC machine is built, the next step is to configure the software and settings. Start by installing the appropriate software on your computer, which typically includes a control program that communicates with the machine and a design software for creating or importing designs. Some popular control programs for CNC woodworking include Mach3, GRBL, and LinuxCNC.
After installing the software, it is important to set up the parameters and preferences to ensure accurate performance. This includes configuring the motor drivers, adjusting step per unit settings based on the machine’s mechanical specifications, and setting up homing and limits switches. Check the documentation of your specific software for detailed instructions on how to configure these settings properly.
Calibrating the Machine
Before starting any cutting operations on your CNC machine, it is crucial to calibrate it properly. Calibration ensures that the machine moves accurately according to its programmed coordinates, resulting in precise cuts and carvings. Begin by checking if each axis moves smoothly from end to end without any binding or skipping steps.
Next, measure the actual movement of each axis using a precision ruler or dial indicator. Compare these measurements with your software’s settings for steps per millimeter or inch. Make necessary adjustments in your software’s configuration until the measured movement matches with what is expected from your design.
Test Cuts and Tool Paths
After configuring and calibrating your CNC woodworking machine, it is time to perform test cuts and tool paths to ensure its accuracy and flawless performance. Use a scrap piece of wood or material similar to what you plan on working with to run various test cuts using different toolpaths.
Start with simple shapes like squares or circles before moving on to more complex designs. Pay attention to details like corners being perfectly square, smooth curves without any jagged edges, and consistent depths in carving or engraving operations. Adjust the feed rate, spindle speed, and depth of cut as needed to achieve optimal results.
Regularly inspect the tooling and replace any dull or damaged bits to maintain the quality of the cuts. Keep in mind that different types of wood may require different settings, so it is important to experiment with various materials and configurations to find the best combination for each project.
By following these steps in configuring and testing your woodworking CNC machine, you can ensure precise and accurate performance for all your future projects. Proper calibration and testing are essential for achieving high-quality cuts and carvings while minimizing material waste.
Safety Precautions and Maintenance
CNC woodworking machines offer a range of capabilities and benefits, but it is essential to prioritize safety when using these powerful tools. Implementing proper safety precautions can protect both the user and the machine itself. Additionally, regular maintenance ensures that the CNC machine operates at its optimal level and extends its lifespan. This section will highlight the importance of safety measures while providing valuable tips for maintenance and troubleshooting common issues.
Safety Precautions:
- Personal Protective Equipment (PPE): Always wear appropriate PPE such as safety glasses, hearing protection, and protective gloves. This will protect against potential hazards like flying debris or loud noise generated during the cutting process.
- Machine Placement: Ensure that your CNC woodworking machine is placed on a stable surface, free from any obstructions or tripping hazards. The work area should be well-lit, allowing for clear visibility of both the machine and the workpiece.
- Emergency Stop Button: Familiarize yourself with the location of the emergency stop button on your CNC machine. It is vital to react swiftly in case of any unexpected situations or emergencies.
- Dust Collection System: Woodworking generates a significant amount of dust, which can pose health risks and impair machine performance over time. Invest in a reliable dust collection system to maintain a clean and safe working environment.
Maintenance and Troubleshooting Tips:
- Regular Cleaning: Routinely clean all components of your CNC machine, including the frame, axis system, spindles, and motors. Remove dust, debris, and accumulated sawdust to prevent clogs or damage.
- Lubrication: Keep moving parts well-lubricated to reduce friction and ensure smooth operation. Refer to your machine’s manual for specific lubrication requirements.
- Calibration Checks: Periodically check and recalibrate your CNC machine to maintain accuracy in cutting dimensions and movements.
- Software Updates: Stay up-to-date with software updates provided by the manufacturer. These updates often include bug fixes and performance improvements.
- Troubleshooting Common Issues: Be familiar with common problems encountered with CNC woodworking machines, such as tool chatter, misalignment, or motor malfunctions. Research troubleshooting techniques and consult resources to efficiently resolve these issues.
By prioritizing safety precautions and regularly maintaining your woodworking CNC machine, you can ensure a safe working environment and prolong the lifespan of your equipment. Additionally, promptly addressing any issues that arise will help to minimize downtime and maximize productivity. Remember that safety and maintenance go hand-in-hand when it comes to owning and operating a woodworking CNC machine.
Expanding Your CNC Woodworking Skills
Once you have successfully built your woodworking CNC machine and familiarized yourself with its basic operations, it is time to take your skills to the next level. There are numerous ways to expand your CNC woodworking skills and explore the full potential of this versatile machine. In this section, we will discuss some additional resources and ideas that can help you enhance your CNC woodworking abilities.
One way to broaden your knowledge in CNC woodworking is by utilizing specialized software. While most CNC machines come with basic software for creating designs and generating toolpaths, there are more advanced programs available that offer a wide range of features and capabilities. These specialized software packages allow you to create intricate designs, simulate the cutting process, and optimize toolpaths for better efficiency.
Some popular options include Vectric Aspire, ArtCAM, and Fusion 360. Investing time in learning these programs can significantly enhance your ability to create complex projects with precision.
Experimenting with different materials is another great way to expand your CNC woodworking skills. While wood may be the primary material used in most projects, there are various other materials that can be successfully machined with a woodworking CNC machine.
You can try working with materials such as plastics, acrylics, foam, or even metals like aluminum or brass. Each material has its own unique properties and challenges when it comes to machining, so be sure to do some research on best practices before starting a project.
Lastly, exploring advanced techniques in CNC woodworking opens up a world of possibilities for creating intricate and unique projects. By delving into topics such as 3D carving, multi-axis machining, or parametric design, you can push the boundaries of what is possible with your woodworking CNC machine.
There are many online tutorials and forums dedicated to these advanced techniques, where you can learn from experienced users and exchange ideas with fellow enthusiasts. Don’t be afraid to challenge yourself and try new things – the more you experiment and explore, the more skilled you will become in CNC woodworking.
By utilizing specialized software, experimenting with different materials, and exploring advanced techniques, you can greatly expand your CNC woodworking skills beyond the basics. Embracing these resources and ideas will not only allow you to create more complex and intricate projects but also foster your creativity and innovation in this exciting field. So go ahead and continue honing your skills – the possibilities are endless.
Conclusion
In conclusion, building a woodworking CNC machine can be a rewarding and beneficial endeavor for both hobbyists and professionals alike. Throughout this guide, we have explored the step-by-step process of constructing your own CNC machine, from understanding the basics to selecting the right components and configuring the software.
By following these instructions and investing time and effort into this project, you will not only gain a valuable tool for your woodworking projects but also expand your skills in CNC woodworking.
One of the main benefits of having a woodworking CNC machine is its precision and efficiency. With this machine, you can create intricate designs and complex cuts with ease. The accuracy of the machine ensures that each piece is consistent, which is especially important for professional woodworkers who need high-quality results.
Additionally, utilizing a CNC machine saves both time and effort compared to traditional methods. It automates many of the manual processes involved in woodworking, allowing you to focus on other aspects of your craft or take on more projects.
Furthermore, building a DIY CNC machine offers flexibility and customization options. By designing the frame, selecting control systems, constructing axis systems, and choosing spindles and motors based on your specific needs, you can create a machine that perfectly fits your woodworking requirements. This level of personalization enhances both the functionality and overall enjoyment in using your CNC machine.
As you embark on your CNC woodworking journey, it is crucial to prioritize safety precautions while operating your machine. Always wear appropriate protective gear such as goggles or gloves when working with power tools or operating the CNC machine. Regular maintenance is also essential to keep your equipment running smoothly and prevent any potential issues from arising.
Frequently Asked Questions
Is it cheaper to build or buy a CNC machine?
The cost of building or buying a CNC machine can vary depending on several factors. Generally, building your own CNC machine can be cheaper if you have the necessary skills, resources, and access to affordable components. By sourcing and assembling the parts yourself, you have more control over the quality and price points.
Additionally, you can customize the machine to meet your specific requirements and potentially save money on features you don’t need. However, building a CNC machine requires time, knowledge, and expertise in mechanical engineering and electronics. If you lack these skills or prefer a ready-to-use solution, buying a CNC machine from a manufacturer might be more suitable albeit potentially more expensive.
Can I make my own CNC?
Yes, it is possible to make your own CNC machine if you have the necessary expertise and resources. Building your own CNC typically involves designing and constructing the frame, sourcing and assembling electronics like motors and drivers, as well as implementing control software. You would need proficiency in mechanical engineering, electrical systems, computer programming, and possibly other related disciplines.
There are various plans available online with detailed instructions for DIY CNC builds using commonly available materials like aluminum extrusions or plywood. By making your own CNC machine, you have the freedom to create a custom design that suits your needs precisely.
Can I build my own CNC router?
Building your own CNC router is certainly possible with the right skills and resources at hand. While similar to building a general-purpose CNC machine in terms of technical requirements, constructing a router-specific one entails focusing on aspects such as spindle mountings, bed size optimization for cutting sheet goods efficiently (e.g., wood or acrylic), dust collection systems integration for cleanliness during operation, among others.
As with any DIY project involving specialized machinery like routers or mills — safety precautions should always be followed closely throughout— including proper guarding mechanisms to protect against potential accidents or injuries associated with rotating bits or high-frequency spindles. Whether it’s designing from scratch or utilizing existing plans in conjunction with off-the-shelf components, building your own CNC router can offer customization options that align with your specific woodworking or fabrication needs.
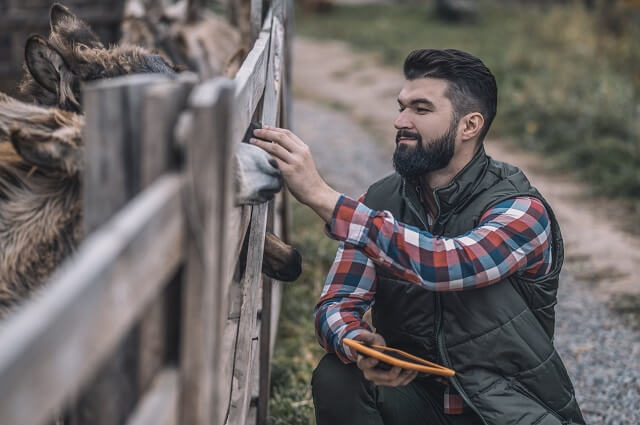
Hi everyone! I’m a woodworker and blogger, and this is my woodworking blog. In my blog, I share tips and tricks for woodworkers of all skill levels, as well as project ideas that you can try yourself.