Are you wondering how to repair old woodworking machines? Woodworking machines play a crucial role in the creation of finely crafted wood products, but over time, they can become worn and damaged. Repairing old woodworking machines can be a challenging task, requiring careful assessment, sourcing replacement parts, and knowledge of proper maintenance and repair techniques.
However, the effort is ultimately worth it as it can save money and preserve valuable machinery. In this article, we will discuss the importance of woodworking machines, the challenges of repairing old machines, and why it’s worth the effort to restore them to optimal working condition.
Woodworking machines are essential tools for creating precision woodwork and furniture. However, as these machines age, they may develop mechanical issues or require electrical repairs.
Repairing old woodworking machines presents challenges such as identifying and locating replacement parts for outdated models, addressing electrical wiring concerns, and restoring the surface of the machinery to extend its lifespan. Despite these hurdles, investing time and effort into repairing old woodworking machines can yield significant rewards by preserving valuable equipment with historical or sentimental value.
By learning how to assess damage effectively, source replacement parts resourcefully, maintain machinery properly, and troubleshoot mechanical and electrical issues skillfully-woodworkers can extend the life of their invaluable assets for years to come. In addition to saving money on costly replacements or repairs by professionals, gaining experience in repairing old woodworking machines brings a sense of satisfaction in reviving antique or beloved equipment.
Whether for personal use or professional endeavors-repairing old woodworking machines is a worthy investment that enhances craftsmanship while preserving tradition.
Assessing the Damage
When it comes to repairing old woodworking machines, the first step is to assess the extent of the damage. This will help you determine the necessary repairs and decide if it’s worth investing in restoration. Here are a few key steps to effectively evaluate the condition of your old woodworking machines:
1. Visual Inspection: Carefully examine every part of the machine for signs of wear, rust, or damage. Look for broken or missing components, as well as any areas that may need cleaning or lubrication.
2. Functional Test: Power up the machine and run it through some test operations to see if all its functions are working properly. This will help you identify any mechanical issues that need to be addressed.
3. Measure and Document: Take accurate measurements and document any abnormalities, including irregular movements, unusual sounds, or vibrations during operation. This information will be useful when troubleshooting and planning repairs.
To properly assess the condition of old woodworking machines, it’s important to have a few essential tools on hand. These tools can help you accurately inspect and diagnose potential issues with your machinery:
– Flashlight: Use a bright flashlight to illuminate hard-to-reach areas inside the machine and look for hidden damages.
– Tape Measure: Take precise measurements of various components to ensure they are within acceptable tolerances.
– Screwdrivers and Wrenches: These basic hand tools are necessary for disassembling parts of the machine for closer inspection.
– Multimeter: A multimeter is essential for checking electrical components and wiring for continuity, voltage, and resistance.
By following these assessment techniques and having the right tools at your disposal, you can effectively evaluate the condition of old woodworking machines before proceeding with repairs.
Once you’ve assessed the damage and identified what needs repair on your old woodworking machine, you may need replacement parts to complete the restoration process. Finding suitable replacement parts for older machinery can be challenging but not impossible.
– Original Manufacturer: Contacting the original manufacturer is always a good starting point when searching for authentic replacement parts.
– Online Marketplaces: Websites such as eBay or specialized forums dedicated to vintage machinery could have sellers offering used or new-old-stock parts.
– Local Metalworking Shops: Establishments that specialize in machining metal parts could replicate specific pieces that are no longer available in stores.
These are just some options available towards finding replacement parts – understanding where to look reduces stress in repairing old woodworking machines so they can be fully restored back into working conditions once again.
Finding Replacement Parts
Where to Look
When it comes to finding replacement parts for older woodworking machines, the first place to start is with the manufacturer or authorized dealers. They may have original parts or suitable replacements that are compatible with your machine. If the manufacturer is no longer in business or does not carry replacement parts for older models, there are other avenues to explore. Online marketplaces, woodworking forums, and classified ads can be valuable resources for sourcing hard-to-find parts.
What to Consider When Purchasing
Before purchasing replacement parts for old woodworking machines, it’s important to carefully evaluate the quality and compatibility of the parts. Look for genuine OEM (original equipment manufacturer) parts whenever possible to ensure proper fit and function. If OEM parts are unavailable, consider aftermarket alternatives from reputable suppliers. Be mindful of any modifications needed to retrofit new parts onto old machines, as these may require additional expertise and resources.
Potential Challenges
One of the biggest challenges in sourcing replacement parts for old woodworking machines is availability. Some components may be rare or obsolete, making them difficult and costly to obtain. Another challenge is ensuring that the replacement part matches the specifications of the original part, especially in terms of size, material, and functionality. In some cases, custom fabrication or refurbishment may be necessary to address these challenges.
With careful research and persistence, it is possible to find suitable replacement parts for older woodworking machines. By considering these tips and being resourceful when searching for parts, woodworkers can restore their vintage equipment to full working order and extend their lifespan for years to come.
Cleaning and Maintenance
Old woodworking machines require regular cleaning and maintenance to prevent further damage and ensure optimal performance. Neglecting these tasks can lead to malfunctions, decreased efficiency, and even safety hazards. In this section, we will provide a step-by-step guide on how to properly clean and maintain old woodworking machines.
The first step in cleaning and maintaining old woodworking machines is to thoroughly inspect the equipment for any signs of wear, damage, or buildup. This includes checking for rust, dust, debris, and other contaminants that may have accumulated over time. Once the inspection is complete, it’s important to gather the necessary tools and supplies for cleaning, which may include lubricants, solvents, brushes, rags, and protective gear.
Next, begin by meticulously removing any dust and debris from all parts of the machine using a soft brush or compressed air. Be careful not to damage any delicate components during this process. Then, use the appropriate solvents or lubricants to clean and protect metal surfaces from rust or corrosion. It’s crucial to follow manufacturer recommendations when selecting cleaning products to avoid causing harm to the machinery.
After the external surfaces are cleaned and protected, it is equally important to check internal components such as gears, bearings, belts, and moving parts for proper lubrication. Ensure that all mechanisms are well-oiled according to manufacturer specifications. Additionally, inspect electrical components for any signs of wear or damage that may compromise safety.
Table 1: Cleaning Supplies
Supplies | Usage |
---|---|
Soft brush | For removing dust without damaging delicate parts. |
Lubricants/Solvents | To clean metal surfaces and protect them from corrosion. |
Rags | To wipe off excess solvents or lubricants. |
Repairing Mechanical Issues
Old woodworking machines often suffer from various mechanical issues such as jammed gears, motor problems, and worn-out bearings. Knowing how to identify and fix these problems is essential for anyone looking to restore old machinery to optimal working condition. Here are some techniques for troubleshooting and repairing mechanical issues commonly found in old woodworking machines.
One of the first steps in addressing mechanical issues with old woodworking machines is to thoroughly clean and lubricate all moving parts. Over time, dirt, dust, and debris can accumulate in the gears, bearings, and other mechanical components, leading to jamming and decreased performance. By carefully cleaning these parts and applying the appropriate lubrication, many mechanical issues can be resolved.
In cases where cleaning and lubrication are not enough to resolve the problem, it may be necessary to disassemble the affected components for further inspection. This process requires careful attention to detail and an understanding of how the machine’s various parts work together. It’s important to document each step of disassembly to ensure that the machine can be reassembled correctly once repairs are complete.
Another common issue in old woodworking machines is motor problems. This can range from simple wiring issues to more complex motor malfunctions. Careful inspection of the motor’s wiring and connections is crucial when addressing electrical problems. In some cases, it may be necessary to replace damaged wiring or faulty components within the motor itself.
While repairing mechanical issues in old woodworking machines can be challenging, it is a rewarding endeavor that allows woodworkers to bring valuable machinery back to life. By following these techniques for troubleshooting and fixing mechanical problems, enthusiasts can enjoy using their restored equipment for years to come.
Technique | Description |
---|---|
Cleaning and Lubricating Moving Parts | Thoroughly clean gears, bearings, and other moving parts before applying appropriate lubrication. |
Disassembly for Inspection | Document each step of disassembly process; inspect parts carefully for damage or wear. |
Motor Troubleshooting | Carefully inspect motor wiring; replace damaged wiring or faulty components when necessary. |
Electrical Repairs
Old woodworking machines, especially those that are decades old, often require electrical repairs due to outdated wiring and electrical components. Taking on the project of repairing the electrical components of these machines can be daunting, but with the right knowledge and safety precautions, it can be done effectively.
When approaching electrical repairs on old woodworking machines, it’s crucial to start with safety in mind. Here are some important safety precautions to take when working with old wiring and electrical components:
- Always wear protective gear such as gloves and safety goggles
- Make sure the machine is unplugged from any power source before starting any repairs
- Use a voltage tester to ensure there is no electricity running through the machine before touching any wires or components
- If you’re unsure about your ability to handle electrical repairs, seek help from a professional electrician
Once you have taken the necessary safety precautions, troubleshooting common electrical problems on old woodworking machines involves identifying issues such as frayed wires, corroded connectors, or damaged switches. Properly diagnosing the problem is crucial before attempting to repair or rewire anything.
When it comes to rewiring old woodworking machines, it’s essential to follow proper guidelines and techniques. Here are some tips for safely rewiring old machinery:
- Consult the original manufacturer’s manual for wiring diagrams and guidelines
- Use high-quality replacement wires and components that meet modern safety standards
- Label all wires and connectors during disassembly to ensure correct reassembly
- Double-check all connections and wiring before powering up the machine again
By taking these safety precautions and following best practices for troubleshooting and rewiring old woodworking machines, enthusiasts can breathe new life into their vintage machinery while ensuring safe operation. Remember that when in doubt, seeking assistance from a professional electrician is always a viable option.
Restoring the Surface
Cleaning the Surface
Before beginning any refinishing or restoration work on old woodworking machines, it’s essential to thoroughly clean the surfaces. Use a mild solvent or detergent to remove grease, dirt, and other residues that have accumulated over the years. For stubborn grime or rust, a fine steel wool or sandpaper may be necessary to gently scrub away the buildup.
Repairing Damage
Once the surface has been cleaned, assess for any damage such as scratches, dents, or rust spots. Depending on the severity of the damage, these issues may need to be addressed before proceeding with refinishing. Minor scratches can often be buffed out with automotive polishing compounds, while deeper scratches may require filler material to even out the surface. Rust spots can be removed using a rust converter product before sanding and painting.
Refinishing Techniques
After cleaning and repairing any damage, consider which refinishing techniques will best suit your woodworking machine. This could involve repainting metal surfaces with durable enamel paint for a fresh look or applying a protective coating such as wax or oil to wooden surfaces. Properly sealing and protecting the surface from moisture and dust will help maintain its appearance and functionality for years to come.
By following these strategies for refinishing and restoring the surface of old woodworking machines, enthusiasts can revitalize their equipment’s appearance while safeguarding it against further deterioration. With care and attention to detail in this process, individuals can enjoy their restored machinery for many more years of woodworking projects.
Safety and Testing
When it comes to repairing old woodworking machines, safety is paramount. Before even attempting to repair an old woodworking machine, it’s important to ensure that the machine is safe to work on and use. This section will cover best practices for ensuring the safety and functionality of repaired woodworking machines, as well as guidelines on how to properly test the machines before use.
One of the first steps in ensuring the safety of a repaired woodworking machine is to thoroughly inspect all components for any signs of damage or wear. This includes checking for frayed wiring, loose bolts or screws, and damaged or worn-out parts. It’s essential to address any safety concerns before moving forward with any repairs.
After making necessary repairs and replacements, testing the functionality of the woodworking machine is crucial. Start by running the machine at a lower speed or with minimal pressure to assess its performance. Listen for any unusual noises or vibrations, which could indicate underlying issues that need further attention. Additionally, check that all safety features such as emergency stops and blade guards are functioning properly.
Finally, it’s important to conduct a thorough test run of the woodworking machine under normal operating conditions before putting it back into regular use. This will help ensure that all repairs have been successful and that the machine is safe for use. Taking these precautions can help prevent accidents and injuries when using old woodworking machines that have been repaired.
Overall, following best practices for safety and testing when repairing old woodworking machines can help ensure that they are not only functional but also safe to use for their intended purpose. Whether it’s a table saw, jointer, planer, or band saw, taking the time to properly test and ensure the safety of repaired woodworking machines is crucial for both personal safety and optimal performance.
Conclusion
In conclusion, repairing old woodworking machines can be a challenging yet rewarding endeavor. Assessing the damage, finding replacement parts, cleaning and maintenance, repairing mechanical and electrical issues, restoring the surface, ensuring safety and functionality are crucial steps in the repair process. By taking on this challenge, woodworkers not only save money but also gain valuable knowledge and experience in understanding and maintaining their machinery.
It’s important to remember that with the right tools, resources, and guidance, anyone can learn how to repair old woodworking machines. There are numerous online forums, communities, and workshops dedicated to sharing expertise and providing support for individuals undertaking these restoration projects. Whether it’s troubleshooting a motor issue or rewiring old electrical components safely, there is a wealth of information available to help woodworkers throughout their repair journey.
Ultimately, taking on the challenge of repairing old woodworking machines is a labor of love that can breathe new life into vintage equipment while cultivating valuable skills. With dedication and patience, anyone can revive these timeless machines and carry on the tradition of craftsmanship for future generations. So roll up your sleeves, gather your tools, and embark on the journey of bringing old woodworking machines back to their former glory.
Frequently Asked Questions
What Should You Avoid When Working With Woodworking Machines?
When working with woodworking machines, it is crucial to avoid wearing loose clothing or jewelry that could get caught in the moving parts of the machines. Additionally, it’s important to never bypass or remove safety guards or devices installed on the machines for protection.
How Can You Maintain Woodwork Machines?
Maintaining woodwork machines involves regular cleaning to remove sawdust, dirt, and debris that can interfere with their proper functioning. Routine inspection for any signs of wear and tear, lubrication of moving parts, and following the manufacturer’s recommended maintenance schedule are all essential for keeping woodwork machines in good working condition.
What Machine Is Used to Smooth Pieces of Wood Before You Begin Working on Them?
The machine used to smooth pieces of wood before beginning work on them is called a planer. Planers are designed to shave off thin layers of wood from the surface in order to create a flat, smooth finish. This initial step helps ensure that the wood is prepared for more precise woodworking techniques.
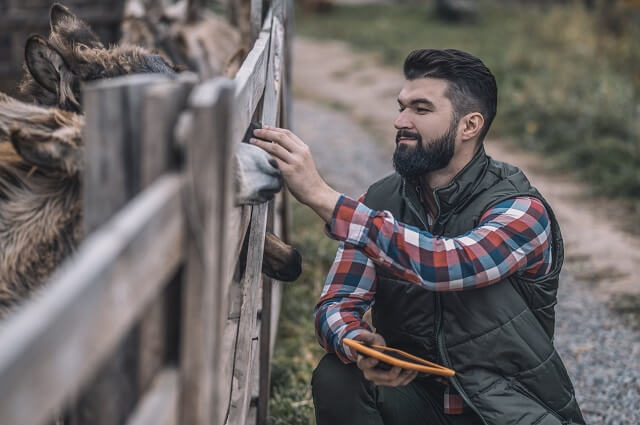
Hi everyone! I’m a woodworker and blogger, and this is my woodworking blog. In my blog, I share tips and tricks for woodworkers of all skill levels, as well as project ideas that you can try yourself.