If you’re looking to enhance your woodworking skills and add versatility to your projects, learning how to run a woodworking shaper is essential. This powerful tool allows you to shape and mold wood with precision and efficiency, opening up a world of possibilities for creating intricate designs and custom profiles. In this article, we’ll dive into the basics of a woodworking shaper and explore its definition, purpose, and the benefits it offers.
A woodworking shaper is a stationary power tool commonly used in woodworking shops. It consists of a spindle that holds interchangeable cutters or router bits, allowing you to shape the edges, moldings, and profiles of wooden boards. The primary purpose of a woodworking shaper is to create smooth, precise cuts and shapes in wood, providing an alternative to other tools like routers or table saws.
One of the primary benefits of using a woodworking shaper is its versatility. With the right cutter and shaper head combination, you can achieve countless profiles and decorative designs on your wooden pieces. Whether you’re looking to create simple chamfers or intricate raised panels, the woodworking shaper provides the control and accuracy required for professional-level results.
However, it’s important to note that operating a woodworking shaper involves some level of skill and understanding. Improper use can not only lead to subpar results but also pose safety risks. Therefore, taking the time to learn how to run a woodworking shaper correctly is crucial for both achieving outstanding outcomes in your projects and ensuring your own well-being.
In the following sections of this article, we will delve into various aspects related to running a woodworking shaper effectively. We will cover safety precautions necessary for protecting yourself and others around you while using this powerful tool. Additionally, we will discuss familiarizing yourself with different parts and components of the woodworking shaper before handling it professionally.
Stay tuned as we equip you with practical knowledge on selecting appropriate cutters and setting up your woodworking shaper to maximize its performance. We will guide you through operating the woodworking shaper step-by-step and provide maintenance tips for prolonging the lifespan of your machine. Lastly, we will also offer advanced techniques and advice to help you unleash your creativity with this remarkable tool.
Are you ready to embark on a woodworking shaper journey? Let’s dive in and explore the wonders of this powerful tool.
Safety Precautions
When it comes to operating a woodworking shaper, safety should always be the top priority. By following essential safety precautions, you can protect yourself and others in your workshop from potential accidents. This section will outline the necessary safety equipment and attire, as well as precautions for handling and operating a woodworking shaper to ensure a safe working environment.
First and foremost, it is crucial to wear the appropriate safety equipment when working with a woodworking shaper. This includes protective eyewear, such as safety glasses or goggles, to shield your eyes from flying wood chips or debris. Additionally, wearing hearing protection, such as earplugs or earmuffs, is recommended due to the high noise levels generated by the shaper.
In addition to personal protective equipment, there are several precautions you should take when handling and operating a woodworking shaper. Always familiarize yourself with the machine’s manual and understand how each component works before starting any task. Keep your hands away from cutting areas at all times and use push sticks or pads when feeding materials into the machine.
To ensure a safe working environment for operating a woodworking shaper, it is important to keep your workspace clean and clutter-free. This reduces the risk of tripping over objects or having tools interfere with the operation of the machine. It is also essential to have adequate lighting in your workspace so that you can clearly see what you are doing.
Overall, prioritizing safety is key when using a woodworking shaper. By wearing the necessary protective equipment, following proper handling procedures, and maintaining a safe working environment, you can minimize the risk of accidents and create a safer woodworking experience for yourself and everyone around you.
Essential Safety Equipment | Precautions for Handling | Maintaining Safe Environment |
---|---|---|
– Safety glasses or goggles | – Familiarize yourself with the machine’s manual | – Keep workspace clean and clutter-free |
– Hearing protection (earplugs or earmuffs) | – Keep hands away from cutting areas | – Ensure adequate lighting in workspace |
Familiarizing Yourself with the Woodworking Shaper
A woodworking shaper is a versatile power tool used in woodworking to shape, cut, and mold wood materials. Before operating a woodworking shaper, it is essential to familiarize yourself with its different parts and components. This section will provide you with a detailed explanation of the various elements of a woodworking shaper, including their functions and roles.
One of the main parts of a woodworking shaper is the motor, which provides the power needed to operate the machine. The motor is connected to the cutter head or spindle, which spins at high speeds to shape the wood. The spindle can hold different types of cutters, such as molding heads or router bits, depending on the desired woodworking application.
Another important component of a woodworking shaper is the fence. The fence acts as a guide for the wood material, allowing for precise and accurate shaping. It can be adjusted both vertically and horizontally to accommodate different wood thicknesses and shapes.
Additionally, a woodworking shaper typically has infeed and outfeed tables. These tables provide support for longer pieces of wood during operation and ensure smooth material feed through the machine. They can be adjusted for height and alignment to enhance stability and accuracy while working with the shaper.
It is crucial to understand each part’s role within the woodworking shaper to operate it effectively and make necessary adjustments when required. By becoming familiar with these components, you can troubleshoot common issues that may arise during operation and achieve optimal results in your woodworking projects.
Component | Function |
---|---|
Motor | Provides power for operating the machine |
Cutter Head/Spindle | Rotates at high speeds with various cutters for shaping wood |
Fence | Acts as a guide for precise shaping of wood |
Infeed and Outfeed Tables | Provides support and smooth material feed during operation |
Selecting the Right Cutter and Shaper Head for Your Needs
When it comes to operating a woodworking shaper, selecting the right cutter and shaper head is crucial for achieving the desired results. The cutter and shaper head determine the type of cuts and profiles you can create, so it’s important to consider your specific needs before making a choice.
- Overview of different cutter types and purposes:
- Factors to consider when choosing the appropriate cutter:
- Matching the shaper head with the desired woodworking application:
There are various types of cutters available for woodworking shapers, each designed for specific purposes. Some common examples include straight cutters, tongue and groove cutters, raised panel cutters, and profile cutters. Straight cutters are versatile and can be used for simple straight cuts or rabbets.
Tongue and groove cutters are ideal for creating joints in flooring or paneling. Raised panel cutters are used for making decorative raised panels in doors or cabinet doors. Profile cutters come in a wide range of shapes and sizes to create intricate moldings.
Several factors should be taken into account when selecting a cutter for your woodworking shaper. First, consider the type of material you will be working with – whether it’s solid wood, plywood, or MDF – as different materials may require different types of cutters. Second, think about the desired profile or shape you want to achieve.
Some projects may call for simple cuts, while others may require more complex profiles. Additionally, take into consideration the size of your project and the power of your shaper. Larger projects may require larger diameter cutters while smaller projects may need smaller ones.
In addition to choosing the right cutter, it’s important to ensure that your selected cutter can be properly mounted on your woodworking shaper’s shaper head. Shaper heads typically come in different sizes to accommodate various types of cutters. It’s important to match the size of the shaper head to the size of your chosen cutter.
This will ensure that the cutter is securely mounted and properly aligned, allowing for accurate and safe operation. Be sure to consult your woodworking shaper’s manual or manufacturer guidelines for compatibility information.
By carefully selecting the right cutter and shaper head for your needs, you can maximize the capabilities of your woodworking shaper and achieve the desired results in your projects. Remember to consider factors such as cutter type, material compatibility, desired profile or shape, project size, and shaper head compatibility when making your choices. With proper selection, you can embark on your woodworking journey with confidence and create beautiful woodwork with precision and ease.
Setting Up Your Woodworking Shaper for Optimal Performance
When it comes to running a woodworking shaper, setting up the machine correctly is crucial for achieving optimal performance. This section will guide you through the important steps of setting up your woodworking shaper to ensure smooth and accurate operation.
Properly mounting the woodworking shaper on a stable surface
Before you begin using your woodworking shaper, it’s essential to mount it securely on a stable surface. This will provide stability and prevent any unwanted movement during operation. Choose a sturdy workbench or table that can handle the weight of the shaper and ensure that it is level. Use mounting bolts or clamps to secure the machine in place, ensuring that it does not wobble or shift during use.
Adjusting the cutter height and fence to suit your project requirements
Once your woodworking shaper is properly mounted, adjust the cutter height and fence according to your project requirements. The cutter height determines how much material will be removed from your workpiece, while the fence controls the direction of the cut. Refer to your specific woodworking shaper’s manual for instructions on adjusting these settings.
To adjust the cutter height, start by turning off the machine and unplugging it for safety. Raise or lower the cutter head using the appropriate adjustment mechanism until it reaches your desired height. Make sure to lock it securely in place before proceeding.
The fence should also be adjusted based on your desired cut. It should be parallel to the spindle axis and held securely in place. Ensure that it is at an appropriate distance from the cutter edge for proper support while feeding material through.
Aligning the infeed and outfeed tables for smooth material feed
In addition to adjusting the cutter height and fence, aligning the infeed and outfeed tables is crucial for achieving smooth material feed through your woodworking shaper. The infeed table is where you place your workpiece to be fed into the machine, while the outfeed table provides support for the material as it exits.
To align these tables, turn off and unplug the shaper. Adjust both tables so that they are level with each other and parallel to the cutter head. This will ensure that your material moves through smoothly without any snags or misalignment.
Taking the time to properly set up your woodworking shaper will greatly contribute to its performance. By mounting it securely, adjusting the cutter height and fence, and aligning the infeed and outfeed tables, you will be well on your way to achieving optimal results with your woodworking projects.
Operating the Woodworking Shaper
Once you have familiarized yourself with the woodworking shaper and have set it up for optimal performance, you are ready to start operating it. This step-by-step guide will walk you through the process of using the woodworking shaper effectively and safely.
- Start-up procedure and powering on the shaper: Before turning on the woodworking shaper, ensure that all safety precautions are in place. Make sure that the machine is securely mounted on a stable surface and that all safety guards are in position. Once everything is in order, power on the shaper by flipping the switch or pressing the start button.
- Feeding the material into the shaper with precision and control: Always maintain a firm grip on your workpiece when feeding it into the woodworking shaper. Start with lighter cuts and gradually increase pressure as you become more comfortable with operating the machine. Keep in mind that pushing too hard or using excessive force can lead to kickback or damage your workpiece.
- Techniques for achieving different woodworking profiles and cuts: The beauty of a woodworking shaper lies in its ability to create various profiles and cuts. To achieve different profiles, adjust the height and angle of your cutter accordingly. When making straight cuts or grooves, use a fence as a guide to ensure accuracy and consistency throughout your project.
Remember to always keep your fingers away from moving parts, especially when adjusting settings or changing cutters. Stay focused, follow proper techniques, and take your time to achieve precise results.
Operating a woodworking shaper can be incredibly satisfying but also requires practice, patience, and attention to detail. By following this step-by-step guide, you will be well-equipped to embark on various woodworking projects with confidence.
Next comes maintaining and caring for your woodworking shaper to ensure its longevity and continued performance excellence.
Maintaining and Caring for Your Woodworking Shaper
Caring for your woodworking shaper is essential to ensure its longevity and optimal performance. Regular maintenance and proper care will not only extend the lifespan of your machine but also enhance its efficiency in producing high-quality woodworking projects. In this section, we will discuss key aspects of maintaining and caring for your woodworking shaper.
- Regular cleaning and lubrication: Like any other power tool, a woodworking shaper requires regular cleaning and lubrication to prevent build-up of dust, debris, or wood chips that can affect its performance. After each use, make sure to clean the machine thoroughly using a brush or air compressor to remove any lingering particles. Additionally, lubricate the moving parts such as the spindle, bearings, and fence with appropriate lubricants to ensure smooth operation.
- Checking and replacing worn-out parts: Over time, certain components of your woodworking shaper may become worn out due to extensive use or general wear and tear. It is important to regularly inspect these parts for any signs of damage or deterioration.
This includes checking the belts, pulleys, cutting heads, spindles, and blades. If any part appears damaged or excessively worn down, it is recommended to promptly replace it with new ones to maintain the performance and safety of your shaper. - Troubleshooting common operational problems: Despite regular maintenance efforts, you might encounter some operational issues with your woodworking shaper. It is crucial to familiarize yourself with common problems that may arise during operation and learn how to troubleshoot them effectively. This includes issues such as poor material feeding, inaccurate cuts/profiles, excessive vibration/noise levels, or difficulties in adjusting settings. Consult the manufacturer’s manual or seek guidance from experienced woodworkers to address these issues promptly.
By implementing these maintenance practices and caring for your woodworking shaper properly, you can ensure its continued reliability and functionality in creating exceptional woodworking projects. Remember that a well-maintained machine not only guarantees a safer working environment but also enables you to achieve excellent results consistently.
Advanced Techniques and Tips for Mastering the Woodworking Shaper
Creating Decorative Woodworking Profiles
One of the most exciting aspects of using a woodworking shaper is the ability to create decorative profiles on your wood pieces. With precision and flair, you can elevate your woodworking projects to a whole new level. To master this advanced technique, it is essential to understand the different types of profiles and the techniques required to achieve them.
There are countless decorative profiles that you can create with a woodworking shaper, such as ogee, cove, bead, and many more. Each profile requires a specific cutter and setup on the shaper. It is crucial to choose a cutter that matches your desired profile and ensure that it is securely mounted on the shaper head.
To achieve precise and clean profiles, it is important to have complete control over the feeding process. Ensure that your material is securely held in place before feeding it into the shaper. Properly adjust the fence and cutter height to match your desired profile depth and width. It is also recommended to work with smaller, manageable sections of wood at first until you become comfortable with creating different profiles.
Practice makes perfect when it comes to mastering decorative woodworking profiles with a shaper. Start by creating simple shapes and gradually progress towards more complex profiles. Experimentation is key in discovering unique combinations and designs that showcase your creativity as a woodworker.
Utilizing Jigs and Fixtures
Jigs and fixtures are invaluable tools for achieving complex shaping tasks with utmost precision on a woodworking shaper. These custom-made devices help hold your workpiece securely in place, allowing consistent repeatability while shaping multiple pieces.
One common type of jig used with a woodworking shaper is a coping sled. This sled holds irregular-shaped pieces or smaller parts securely to ensure their safe passage through the cutter head. Coping sleds are particularly useful when creating intricate moldings or joints that require precise shaping.
Another useful fixture is a featherboard. These devices are secured to the shaper’s fence or the table and apply pressure against the workpiece, keeping it firmly in position during the shaping process. Featherboards are especially helpful when cutting against the grain or when shaping narrow stock.
When utilizing jigs and fixtures with a woodworking shaper, it is crucial to follow proper setup procedures and safety guidelines. Ensure that all attachments are securely fastened and that they do not interfere with the movement of your workpiece through the cutter head. Regularly inspect your jigs and fixtures for any signs of wear or damage, as they need to be in good condition to provide reliable support.
Recommended Resources and Workshops
While this section provides an overview of advanced techniques and tips for mastering the woodworking shaper, there are many resources available that can further enhance your skills. Books, online tutorials, and workshops offer valuable insights from experienced woodworkers who have honed their craft with shapers.
Reading books written by experts can give you a comprehensive understanding of different profiles, techniques, and applications. Look for books that specifically focus on shaping with a woodworking shaper, providing step-by-step instructions along with visual aids to help you grasp concepts more easily.
Online tutorials, videos, and forums also offer a wealth of information on advanced shaping techniques. Many experienced woodworkers share their knowledge through detailed videos that walk you through various shaping processes. Participating in online forums allows you to connect with fellow woodworkers who can provide advice based on their firsthand experiences.
Attending workshops or classes conducted by expert woodworkers is an excellent way to learn advanced shaper techniques directly from professionals. These hands-on learning opportunities allow you to observe demonstrations, ask questions, and practice under guidance until you feel confident enough to apply these techniques independently.
By continuously seeking out additional resources and participating in workshops or classes, you can take your woodworking shaper skills to new heights. Remember that mastering advanced techniques with a woodworking shaper takes time and practice, so be patient and persistent in your pursuit of excellence.
Conclusion
In conclusion, mastering the art of woodworking shaper operation opens up a world of possibilities for woodworkers. Throughout this article, we have explored the basics of a woodworking shaper, discussed safety precautions, familiarized ourselves with the different parts and components, and learned how to select the right cutter and shaper head for our needs.
We have also covered setting up the shaper for optimal performance, provided a step-by-step guide on operating the shaper, and highlighted the importance of maintaining and caring for it.
Now that you have acquired knowledge and understanding of woodworking shapers, it is time to put what you have learned into practice. Embrace this art form and let your creativity flow as you explore the endless possibilities that this tool offers. Remember to always prioritize safety by wearing essential protective equipment and taking necessary precautions.
As you gain more experience with the woodworking shaper, do not hesitate to dive into advanced techniques that allow you to create decorative woodworking profiles with precision and flair. Utilize jigs and fixtures to take on complex shaping tasks that expand your skill set even further.
To continue honing your skills in operating a woodworking shaper, consider seeking out recommended resources or attending workshops where you can learn from experienced woodworkers. By continuing to learn and grow, you can truly excel in this craft.
Frequently Asked Questions
How should a board be fed through the shaper?
When feeding a board through a shaper, it is important to follow certain guidelines for safety and efficiency. First, ensure that the board is clean and free of any debris or loose knots that may cause it to kickback during operation. The board should be flat and straight to prevent any uneven shaping. Next, choose the appropriate cutter for the desired shaping task and secure it in the shaper’s spindle.
Adjust the fence or guides to maintain a consistent distance between the cutter and the edge of the board throughout the process. Start feeding the board slowly and steadily into the rotating cutter, always keeping firm control of it from both sides. This helps ensure an even cut without putting excessive strain on the machine or risking injury.
What can I do with a wood shaper?
A wood shaper is a versatile tool that can be used for various woodworking tasks. One of its primary functions is shaping edges of boards, creating decorative profiles such as beading or fillets. Shapers can also produce grooves, dadoes, slots, rabbets, and other custom cuts on wood surfaces through different cutter configurations.
With their adjustable speed control, they allow you to work with different types of wood at various cutting depths. Beyond shaping wood pieces individually, shapers can also handle more complex operations like making raised panels or creating moldings by using specialized jigs or heads designed specifically for these purposes.
Is A shaper better than a router?
Whether a wood shaper or a router is better depends on the specific task at hand and personal preferences. Shapers are generally preferred for larger-scale projects due to their robustness and ability to handle larger stock sizes effectively. They have more power than routers and can typically accommodate heavier duty cutters for shaping thicker materials without strain – which makes them popular in professional woodworking settings like joineries or cabinet shops where efficiency matters most.
On the other hand, routers are more compact and handheld tools that offer excellent versatility in terms of portability and flexibility in handling smaller scale projects or jobs that require more intricate and detailed work. Routers are also commonly used for tasks such as edge routing, dado cutting, template routing, and creating joinery. Overall, both tools have their own strengths and applications, so determining which one is better ultimately depends on the specific woodworking needs and preferences of the user.
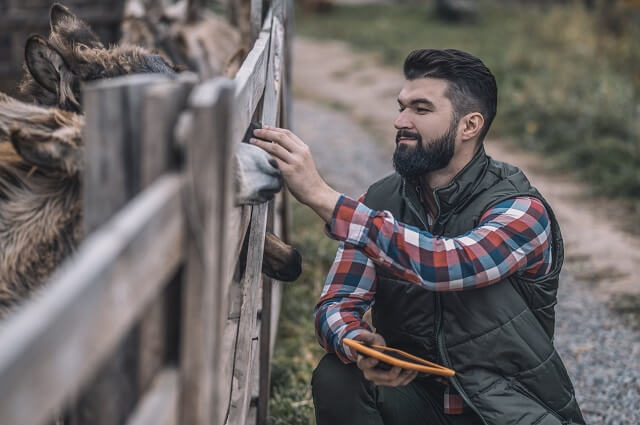
Hi everyone! I’m a woodworker and blogger, and this is my woodworking blog. In my blog, I share tips and tricks for woodworkers of all skill levels, as well as project ideas that you can try yourself.