Are you interested in learning how to use a CNC machine for woodworking? Whether you’re a hobbyist or a professional woodworker, using a CNC machine can revolutionize the way you approach woodworking projects. In this article, we will explore the ins and outs of using a CNC machine for woodworking, from understanding the basics to achieving precision and accuracy in your projects.
CNC (Computer Numerical Control) machines have become increasingly popular in the woodworking industry due to their ability to automate and streamline the woodworking process. By utilizing CNC technology, woodworkers can produce intricate designs, achieve precise cuts, and replicate designs with ease.
In this comprehensive guide, we will cover everything you need to know about using a CNC machine for woodworking. From understanding the basics of a CNC machine to choosing the right one for your projects, setting it up, programming and using software, safety measures and precautions, as well as maintenance and care for long-term success.
Whether you’re new to CNC machines or looking to enhance your skills, this article will provide valuable insights for incorporating this technology into your woodworking ventures.
Understanding the Basics of a CNC Machine
CNC (Computer Numerical Control) machines have revolutionized woodworking by allowing for greater precision, efficiency, and the ability to create intricate designs that would be nearly impossible with traditional methods.
To understand the basics of a CNC machine for woodworking, it’s important to note that these machines are controlled by a computer program, which dictates the movements and actions of the machine. This means that instead of manually operating the machine as with traditional woodworking tools, you input your design into a computer program and the CNC machine follows those instructions to precisely cut, shape, or carve wood.
Here are some key basics to keep in mind when using a CNC machine for woodworking:
- Understanding the different types of CNC machines: There are various types of CNC machines specifically designed for woodworking, including CNC routers, CNC mills, and CNC lathes. Each type has its own strengths and applications in woodworking, so it’s important to choose the right one for your particular project.
- Familiarizing yourself with the components of a CNC machine: A typical CNC machine consists of a cutting tool (such as a router bit or end mill), a workpiece-holding platform (often called a spoilboard), motors and drivetrains for movement along multiple axes (X,Y,Z), and a control panel or computer interface.
- Learning about axis movements: Most CNC machines operate along three primary axes – X, Y, and Z – allowing for movement both horizontally and vertically. Understanding how these movements work is essential in creating accurate and precise designs on your woodwork.
Understanding these core principles is crucial when learning how to use a CNC machine for woodworking. With this knowledge as a foundation, woodworkers can then move on to more advanced techniques and projects while achieving impressive results.
Choosing the Right CNC Machine for Woodworking Projects
When selecting a CNC machine for woodworking, it’s crucial to consider the type of projects you will be working on. Different CNC machines are designed for specific purposes, whether it’s carving intricate designs, cutting complex shapes, or creating large-scale furniture pieces. The two primary types of CNC machines for woodworking are routers and mills. Routers are ideal for cutting and shaping while mills are better suited for precise drilling and cutting.
Another important factor to consider when choosing a CNC machine for woodworking is the size of the workspace or bed. This will determine the maximum dimensions of the wood pieces you can work with. It’s essential to choose a machine that can accommodate the size of your typical woodworking projects to ensure efficiency and precision.
Additionally, the spindle speed and horsepower of the CNC machine are critical considerations. Higher spindle speeds and horsepower allow for faster cutting and carving, making them suitable for larger production runs or more intricate designs. However, it’s important to find a balance between speed and power based on the specific requirements of your woodworking projects.
Consideration | Importance |
---|---|
Type of CNC Machine | Crucial based on project requirements |
Size of Workspace/Bed | Determines maximum wood piece dimensions |
Spindle Speed and Horsepower | Balance between speed and power important |
Setting Up Your CNC Machine for Woodworking
- Leveling the Machine: Ensuring that your CNC machine is properly leveled is imperative for achieving accurate cuts and carvings. Use a leveling tool to make sure that the machine’s bed or work area is perfectly flat, which will prevent any errors during the cutting process.
- Securing Workpieces: Properly securing your workpieces onto the CNC machine’s bed is essential to prevent movement or slippage during operation. Utilize clamps, double-sided tape, or vacuum hold-down systems to secure the wood firmly in place before starting the machining process.
- Tool Changes and Calibration: If your woodworking project requires different cutting tools, it’s essential to have a clear understanding of how to change and calibrate these tools within the CNC machine. Follow the manufacturer’s guidelines for safely swapping out cutting bits and calibrating them for precision cuts.
- Dust Collection System: Woodworking with a CNC machine can produce a significant amount of sawdust and debris. Implementing an efficient dust collection system will not only keep your workspace clean but also maintain the longevity of your CNC machine by preventing sawdust from accumulating within its components.
By following these steps and carefully preparing your CNC machine for woodworking, you can ensure that your projects are executed with precision and efficiency, ultimately leading to successful woodworking outcomes. Understanding how to use a CNC machine for woodworking involves not only operating the equipment but also ensuring that it is set up correctly for optimal performance and safety during use.
Programming and Using CNC Software for Woodworking
Understanding CNC Software
CNC software is an essential component of using a CNC machine for woodworking. This software allows users to create the designs and instructions that the CNC machine will follow to produce the desired woodwork. The most common types of CNC software for woodworking include CAD (computer-aided design) and CAM (computer-aided manufacturing) programs. CAD software is used to create the digital designs, while CAM software is used to generate the toolpaths and machining instructions based on those designs.
Creating Design Files
One of the first steps in using CNC software for woodworking is creating or obtaining design files. These files can be created from scratch using CAD software, or they can be obtained from existing design libraries or marketplaces. Once you have your design files, you can import them into your CNC software to begin programming the toolpaths and machining instructions.
Programming Toolpaths and Machining Instructions
After importing your design files, it’s time to program the toolpaths and machining instructions in your CNC software. This process involves specifying parameters such as cutting depths, feed rates, spindle speeds, and tool changes.
Additionally, you’ll need to define the sequence of operations and consider factors such as grain direction when working with wood. Once the programming is complete, you can simulate the toolpaths in the software to ensure everything looks correct before moving on to actually running the CNC machine.
By understanding how to use a cnc machine for woodworking in terms of programming and using CNC software, woodworkers can effectively translate their designs into precise and accurate finished products. With these essential skills in place, users can take full advantage of a CNC machine’s capabilities for a wide range of woodworking projects.
Safety Measures and Precautions When Using a CNC Machine
Woodworking with a CNC machine can be an incredibly rewarding experience, but it’s important to prioritize safety at all times. When using a CNC machine for woodworking, there are several key safety measures and precautions that should always be followed to prevent accidents and injuries.
First and foremost, it is crucial to wear the appropriate personal protective equipment (PPE) when operating a CNC machine for woodworking. This typically includes safety glasses or goggles to protect your eyes from flying debris, as well as hearing protection to guard against the loud noise produced by the machine. Additionally, wearing gloves can help protect your hands from sharp edges and splinters.
Another important safety measure when using a CNC machine for woodworking is to ensure that the work area is well-ventilated. Woodworking often produces fine dust particles that can pose respiratory risks if inhaled over time. Using a dust collection system or wearing a respirator can help minimize these risks and keep the air in your workspace clean.
In addition to PPE and ventilation, it’s essential to familiarize yourself with the emergency stop procedures for your specific CNC machine. Knowing how to quickly and safely shut down the machine in case of an emergency is critical for preventing accidents. Always take the time to read through the manufacturer’s instructions and guidelines for operating your specific CNC machine safely.
Safety Measure | Description |
---|---|
Personal Protective Equipment | Wearing safety glasses, hearing protection, and gloves to prevent injuries from flying debris or sharp edges. |
Ventilation | Using a dust collection system or wearing a respirator to minimize respiratory risks from fine dust particles produced during woodworking. |
Emergency Stop Procedures | Familiarizing yourself with how to quickly and safely shut down the CNC machine in case of an emergency. |
Tips and Techniques for Achieving Precision and Accuracy With a CNC Machine in Woodworking
Woodworking with a CNC machine requires precision and accuracy to ensure the quality of the final product. By focusing on certain tips and techniques, woodworkers can maximize the potential of their CNC machines for woodworking projects.
Understanding Feed Rates and Speeds
One key aspect of achieving precision with a CNC machine in woodworking is understanding the feed rates and speeds. The feed rate refers to how quickly the cutting tool moves in relation to the material being cut, while speed is the rate at which the cutting tool rotates. Finding the optimal combination of feed rates and speeds for different types of wood can greatly improve the accuracy of cuts and carve details.
Selection of Cutting Tools
Proper selection of cutting tools is essential for achieving precision in woodworking with a CNC machine. Different types of wood require different tools to achieve optimum results. Using sharp, high-quality bits designed for specific tasks can make a significant difference in the outcome of a project. Additionally, understanding the appropriate cutting depths and tool paths for different woodworking tasks is crucial in achieving precision with a CNC machine.
Material Hold-Down Techniques
Another important factor that affects precision when using a CNC machine for woodworking is proper material hold-down techniques. Securely holding down the material being worked on is essential to prevent movement or vibration during cutting, which could result in inaccuracies. Utilizing clamps, vacuum tables, or other hold-down methods can help maintain stability and precision throughout the machining process.
By implementing these tips and techniques, woodworkers can enhance the precision and accuracy when using a CNC machine for woodworking projects. Understanding feed rates and speeds, selecting appropriate cutting tools, and employing proper material hold-down techniques are just some of the crucial factors that contribute to successful outcomes in woodworking with a CNC machine.
Maintenance and Care for Your CNC Machine for Long-Term Woodworking Success
In conclusion, mastering the art of using a CNC machine for woodworking involves understanding its basics, choosing the right machine for your projects, setting it up correctly, programming and using the software, and most importantly, practicing safety measures. However, maintaining and caring for your CNC machine is equally important for long-term woodworking success. Proper maintenance not only ensures the longevity of your machine but also contributes to the quality of your woodworking projects.
One way to maintain a CNC machine for woodworking is to regularly clean and lubricate its components. Dust and debris can accumulate in the machine’s moving parts, affecting its precision and accuracy. Regular cleaning with compressed air and wiping with a soft cloth can help prevent this issue. Additionally, proper lubrication of the moving parts will ensure smooth operation and reduce wear and tear.
Furthermore, scheduling routine maintenance checks is crucial in keeping your CNC machine in top condition. Checking for loose bolts or screws, belt tension, and electrical connections can prevent unexpected breakdowns during woodworking projects. By following these maintenance practices, you can maximize the lifespan of your CNC machine while consistently producing high-quality woodwork pieces.
Frequently Asked Questions
How Hard Is It to Use a Wood CNC Machine?
Using a wood CNC machine may initially seem challenging, especially for those new to woodworking and computerized machinery. However, with the right training, practice, and understanding of the software and tooling, it can become more manageable. It requires a good understanding of the machine’s operations and programming.
What Can a Woodworking CNC Machine Do?
A woodworking CNC machine can do a variety of tasks such as cutting, carving, engraving, and drilling wood materials with precision and accuracy. It enables the production of intricate designs, complex shapes, and repetitive components that would be difficult to achieve manually. This technology allows for an increase in productivity and consistency in woodworking projects.
What Do I Need to Run a CNC Machine?
To run a CNC machine effectively, you will need proper training on its operation, knowledge of CAD/CAM software for programming, safety equipment including eye protection and hearing protection, proper tooling such as router bits or drill bits suitable for woodworking applications, and an understanding of the material being used (in this case wood).
Additionally, having a clean and organized workspace is essential for efficient CNC machine operation.
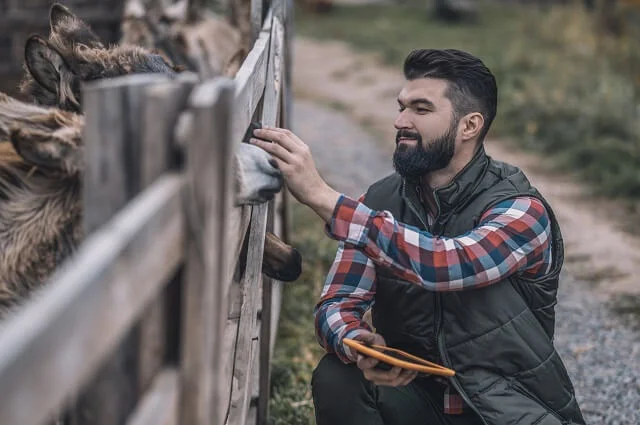
Hi everyone! I’m a woodworker and blogger, and this is my woodworking blog. In my blog, I share tips and tricks for woodworkers of all skill levels, as well as project ideas that you can try yourself.