The 1920s marked a period of significant change and innovation in the woodworking industry. Woodwork, whether it be furniture, architectural elements, or decorative pieces, played a central role in the design and craftsmanship of the era. In this article, we will delve into the techniques and processes used by woodworkers during the 1920s, shedding light on how most woodwork was finished during this time.
During the 1920s, craftsmanship and attention to detail were highly valued in the woodworking industry. Skilled artisans dedicated themselves to creating high-quality woodwork that showcased both beauty and functionality. Traditional hand-finishing methods were prevalent during this period, with woodworkers relying on age-old techniques to achieve desired finishes.
Woodwork in the 1920s was often protected and enhanced through the use of varnishes and lacquers. These coatings not only safeguarded the wood from damage but also brought out its natural beauty, adding depth and luster to the finished pieces. Additionally, industrialization had a significant impact on wood finishing during this time, leading to the adoption of machine-finishing processes that revolutionized production methods.
The Rise of Craftsmanship
The 1920s saw a resurgence in craftsmanship and woodworking, with an emphasis on hand-crafted pieces that displayed intricate designs and attention to detail. This era marked a shift from mass-produced items to unique, artisanal creations, highlighting the importance of skilled woodworkers and their contributions to the field. The focus on craftsmanship during this time was a response to the industrialization of previous decades, as people sought authenticity and artistry in the products they consumed.
Woodworking became a revered skill during the 1920s, with artisans taking pride in their ability to hand-finish wood using traditional methods. These techniques often involved the use of hand planes, chisels, scrapers, and sandpaper to achieve a smooth and polished surface. The meticulous nature of these processes ensured that each piece of woodwork was distinctive and showcased the dedication of the craftsman.
One of the most widely-used traditional finishing methods for woodwork in the 1920s was hand-rubbed oil finishes. This technique involved applying multiple coats of oil to the wood, allowing it to penetrate the grain and enhance its natural beauty.
Additionally, wax finishes were also popular during this time, providing a soft luster and protective layer over the wood. These labor-intensive methods exemplified the commitment of craftsmen to producing high-quality woodwork that would stand the test of time.
Wood Finishing Method | Characteristics |
---|---|
Hand-Rubbed Oil Finishes | Enhances natural beauty; labor-intensive application process |
Wax Finishes | Provides soft luster; offers protection for the wood |
Traditional Hand-Finishing Methods
Woodworking in the 1920s was characterized by a strong emphasis on traditional hand-finishing methods, which contributed to the high level of craftsmanship seen during this era. Woodworkers of the time took great pride in their skills and utilized various techniques to achieve impeccable finishes on their creations.
Hand-Sanding and Planing
One of the most common traditional hand-finishing methods used in the 1920s was hand-sanding and planing. Woodworkers would meticulously sand down surfaces using different grits of sandpaper to achieve a smooth and polished finish. Additionally, hand planing was utilized to create flat, even surfaces on wood pieces, allowing for intricate detailing and joinery.
French Polishing
Another popular technique employed by woodworkers in the 1920s was French polishing, which involved applying multiple thin coats of shellac using a pad made of wadding or cloth. This method created a lustrous finish that enhanced the natural beauty of the wood while providing protection against wear and tear.
Staining and Waxing
In addition to sanding and French polishing, staining and waxing were also common methods used to finish woodwork in the 1920s. Woodworkers would apply various types of stains to enhance the color of the wood, followed by waxing to bring out its natural sheen and provide a layer of protection.
Overall, traditional hand-finishing methods played a crucial role in shaping woodworking practices in the 1920s, resulting in beautifully finished pieces that showcased meticulous craftsmanship. These techniques continue to inspire modern woodworkers seeking to replicate the timeless elegance of vintage woodworking styles.
The Use of Varnishes and Lacquers
Woodwork in the 1920s was often finished with varnishes and lacquers, which served to protect and enhance the natural beauty of the wood. During this time, these types of finishes were commonly used to provide a durable and glossy surface to furniture, cabinetry, and other wooden items. The application of varnishes and lacquers was an important aspect of woodworking in the 1920s, contributing to the overall aesthetic appeal and longevity of the finished pieces.
Traditional Application Techniques
In the 1920s, woodworkers applied varnishes and lacquers using traditional hand-finishing methods. This involved skillfully brushing or spraying on the finish in multiple thin coats to achieve a smooth and lustrous appearance. The meticulous application process required attention to detail and precision, underscoring the craftsmanship that was characteristic of this era.
Protective Qualities
Varnishes and lacquers were favored for their protective qualities, as they formed a strong barrier against moisture, heat, and everyday wear and tear. This made them ideal for use on wooden furniture and fixtures that were subject to frequent use. Additionally, these finishes provided a high level of resistance to scratches and abrasions, prolonging the life of woodwork in homes and commercial settings.
Enhancing Natural Beauty
Beyond their protective properties, varnishes and lacquers were valued for their ability to enhance the natural beauty of wood. These finishes could enrich the grain patterns of different wood species, bringing out their unique colors and textures. In turn, this added depth and visual interest to furniture and architectural elements, aligning with the artistic sensibilities of the 1920s.
Machine-Finishing Processes
During the 1920s, industrialization had a significant impact on wood finishing processes, leading to the rise of machine-finishing methods. This period marked a shift from traditional hand-finishing techniques to more efficient and standardized processes. Woodworking industries began to embrace mechanized methods for applying finishes, resulting in increased productivity and consistency in the quality of finished woodwork.
One of the key advancements in machine-finishing processes during the 1920s was the introduction of spray guns for applying varnishes and lacquers. This innovation allowed for a more uniform application of finishes, reducing wastage and improving the overall efficiency of the process. The use of spray guns also facilitated the application of thinner coats, resulting in faster drying times and a smoother finish on wood surfaces.
Another notable development in machine-finishing processes was the introduction of sanding machines. These machines were instrumental in achieving a smooth, even surface on wooden components before applying finishes. By automating the sanding process, woodworkers were able to eliminate inconsistencies and imperfections, resulting in a higher quality finished product.
One cannot underestimate how much most woodwork was finished in the 1920s through mechanical means rather than by hand. The increased adoption of mechanical processes for wood finishing not only transformed the woodworking industry during that era but also paved the way for modern manufacturing practices that continue to shape woodworking techniques today.
Popular Wood Finishes of the Era
During the 1920s, wood finishing was a crucial component of creating furniture, cabinetry, and architectural details. The most popular wood finishes of the era included shellac, varnish, and lacquer. These finishes not only enhanced the natural beauty of the wood but also provided protection against wear and tear.
Shellac was one of the most widely used wood finishes in the 1920s. It was derived from a resin secreted by the lac bug and was dissolved in alcohol to create a solution that could be applied to wooden surfaces. Shellac provided a shiny finish that highlighted the grain of the wood, making it a desirable choice for furniture and decorative pieces.
Another common finish during this time period was varnish. Varnish was typically made from a blend of oil, resin, and solvents, creating a durable coating that offered excellent protection against moisture, heat, and scratches. It was often used on floors and other high-traffic surfaces due to its resilience.
Lacquer also gained popularity as a wood finish in the 1920s. This fast-drying finish offered a glossy sheen and could be tinted to create vibrant colors. Its quick drying time made it an attractive option for mass production processes.
As industrialization advanced during this era, machine-finishing processes became more prevalent. While traditional hand-finishing methods were still employed to some extent, machines allowed for greater efficiency in applying wood finishes on a larger scale.
Wood Finishes | Description |
---|---|
Shellac | Derived from resin secreted by lac bugs; provided shiny finish that highlighted grains of wood |
Varnish | Made from oil, resin, and solvents; offered durable protection against moisture, heat, and scratches |
Lacquer | Fast-drying finish with glossy sheen; could be tinted for vibrant colors |
The Influence of Art Deco and Art Nouveau Styles on Wood Finishing
The 1920s marked the rise of two significant artistic movements, Art Deco and Art Nouveau, that had a profound impact on wood finishing techniques during this period. These influential styles embraced a combination of traditional craftsmanship and modern industrial processes, resulting in unique and innovative approaches to woodwork. Both Art Deco and Art Nouveau utilized intricate designs, geometric patterns, and organic forms, influencing the aesthetics of wood finishing in the 1920s.
One of the key characteristics of Art Deco style was its emphasis on luxury, glamour, and opulence. This translated into wood finishing techniques that incorporated rich lacquers, glossy varnishes, and metallic accents to create a sense of elegance and sophistication. In contrast, Art Nouveau favored natural materials and organic motifs, leading to wood finishes that highlighted the beauty of wood grain through hand-crafted techniques such as marquetry and inlay.
Art Deco and Art Nouveau styles also brought a renewed focus on decorative elements in woodwork, with ornate carvings, intricate details, and stylized embellishments becoming defining features of furniture and architectural elements during this time. These artistic trends not only influenced how wood was finished but also contributed to the overall design aesthetic of interior spaces in the 1920s.
In summary, the influence of Art Deco and Art Nouveau styles on wood finishing in the 1920s resulted in a harmonious blend of traditional craftsmanship and modern design sensibilities. The legacy of these artistic trends can still be seen today in contemporary woodworking practices that continue to draw inspiration from the innovative approaches to wood finishing developed during this iconic era.
Legacy and Impact
In conclusion, the woodworking techniques of the 1920s left a lasting legacy on the craft and continue to influence wood finishing methods today. The rise of craftsmanship during this era emphasized the importance of traditional hand-finishing methods, which were used by woodworkers to achieve exquisite results. Varnishes and lacquers played a crucial role in protecting and enhancing woodwork in the 1920s, showcasing the attention to detail and dedication to quality that defined the period.
The impact of industrialization on wood finishing processes in the 1920s cannot be understated. Machine-finishing techniques became more prevalent during this time, revolutionizing mass production and leading to new possibilities for achieving consistent and efficient results. Despite this shift towards mechanization, traditional hand-finishing methods remained highly valued for their ability to produce exceptional craftsmanship.
The influence of Art Deco and Art Nouveau styles also left a significant mark on wood finishing in the 1920s, shaping the artistic trends that defined the era. The timeless elegance and sophistication of these styles continue to inspire contemporary wood finishing techniques, demonstrating how the legacy of 1920s woodworking continues to resonate with modern craftsmen and designers.
As we reflect on the lasting influence of 1920s wood finishing techniques, it is clear that their relevance remains strong today, serving as a testament to the enduring artistry and innovation of this pivotal period in woodworking history.
Frequently Asked Questions
How Were Old Wood Floors Finished?
Old wood floors were finished using a variety of methods, including wax, shellac, and varnish. Wax was applied and buffed to create a glossy finish, while shellac provided a durable and glossy surface. Varnish, on the other hand, offered protection and enhancement to the natural beauty of the wood.
What Type of Wood Flooring Was Used in the 1920s?
In the 1920s, many homes used oak wood flooring due to its durability and availability. Oak was especially popular for its strength and resistance to wear and tear, making it a common choice for that time period.
How Did They Stain Wood in the Old Days?
In the old days, wood staining was often done using natural pigments extracted from plants or minerals. These pigments were mixed with various binders such as oil or resin to create a stain that would be applied to the wood’s surface. This method allowed for customization of colors and tones depending on the specific materials used.
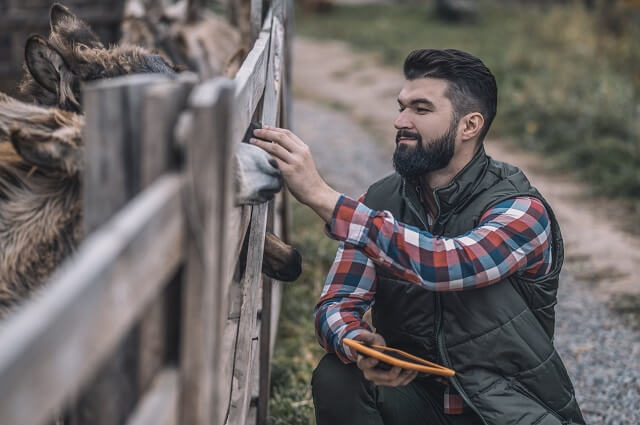
Hi everyone! I’m a woodworker and blogger, and this is my woodworking blog. In my blog, I share tips and tricks for woodworkers of all skill levels, as well as project ideas that you can try yourself.