Japanese woodworking is a great way to get into the craft of woodworking. The techniques used in Japanese woodworking are different than what you may be used to, but they are worth learning. Here are a few of the basics you will need to know:
The first thing you need to know is the difference between hard and soft woods. Hard woods are stronger and more durable than soft woods. Soft woods are easier to work with, but they are not as strong or durable.
The next thing you need to know is the difference between a straight edge and a chisel. A straight edge is used to create a straight line, while a chisel is used to create a curved line.
The final thing you need to know is the difference between a coping saw and a hand saw. A coping saw is used to cut curves, while a hand saw is used to cut straight lines.
Once you know these basics, you can start learning the techniques used in Japanese woodworking. One of the most important techniques is the use of a chisel. Chisels are used to create curved lines, and they can be used to create a variety of different shapes.
Another important technique is the use of a coping saw. Coping saws are used to cut curves, and they can be used to create a variety of different shapes.
Finally, you will need to learn how to use a hand saw. Hand saws are used to cut straight lines, and they are a great way to get started in Japanese woodworking.
Where To Buy Hardwood For Woodworking
There are a few things to consider when looking for hardwood for woodworking. The most important factors are the hardness and durability of the wood. Other factors to consider are the color and grain of the wood.
The hardness of a wood is measured by its Janka hardness rating. The higher the rating, the harder the wood. The Janka hardness rating of red oak is 1,220. The Janka hardness rating of white oak is 1,360. The Janka hardness rating of maple is 1,450. The Janka hardness rating of hickory is 2,000. The Janka hardness rating of walnut is 1,300.
The durability of a wood is measured by its resistance to wear and tear. The higher the rating, the more durable the wood. The wear resistance of red oak is 9. The wear resistance of white oak is 11. The wear resistance of maple is 12. The wear resistance of hickory is 18. The wear resistance of walnut is 13.
The color and grain of a wood can be important factors to consider when choosing a hardwood for woodworking. The color of a wood can be affected by the type of tree it comes from, the age of the tree, and the type of finish that is applied. The grain of a wood can be affected by the type of tree it comes from, the age of the tree, and the type of finish that is applied.
Some hardwoods are available in a variety of different colors and grains. Other hardwoods are only available in one color or one grain.
The best way to choose a hardwood for woodworking is to consider the hardness, durability, color, and grain of the wood.
When To Change Router Speed Woodworking
routers are a common tool in many workshops. There are a variety of different routers on the market, with different speeds and features. If you have a router and you’re not sure what speed to use, there are a few things you can consider.
Router speed is measured in revolutions per minute, or RPM. The higher the RPM, the faster the router will spin. Most routers have a range of speeds, usually between 10,000 and 25,000 RPM.
Router speed is important because it determines the size of the cut you can make. The higher the speed, the smaller the cut you can make. For example, if you’re making a rabbet cut, you’ll need to use a slower speed so that the router can cut all the way through the wood. If you’re using a higher speed, the router will just burn the wood.
The same is true for other types of cuts. If you’re using a higher speed, you’ll need to use a smaller bit to avoid burning the wood.
There are a few things to keep in mind when choosing a router speed. First, you need to consider the type of wood you’re using. Harder woods, like oak, require a slower speed than softer woods, like pine.
You also need to consider the size of the cut you’re making. The smaller the cut, the slower the speed you’ll need.
Finally, you need to consider the type of bit you’re using. A smaller bit requires a slower speed than a larger bit.
So, what speed should you use? The best way to find out is to experiment. Try a few different speeds and see which one works best for the type of cut you’re making.
Japanese Woodworking Joints Pdf
There are a variety of Japanese woodworking joints pdf, each with its own benefits and drawbacks. The most common joints are the butt joint, the miter joint, the dovetail joint, the rabbet joint, and the mortise and tenon joint.
The butt joint is the simplest joint to make, and it’s also the weakest. The two pieces of wood are simply butted together. The miter joint is similar to the butt joint, but the two pieces of wood are cut at a 45-degree angle and then glued and clamped together. The dovetail joint is a strong and attractive joint that is often used in furnituremaking. The two pieces of wood are cut at a 45-degree angle and then glued and clamped together. The rabbet joint is a simple joint in which one piece of wood is cut rabbeted, or notched, to fit snugly into another piece of wood. The mortise and tenon joint is one of the strongest joints and is often used in furnituremaking and in carpentry. The mortise is a hole in one piece of wood that the tenon, or projection, on the other piece of wood fits into.
Picture Frame Sled Fine Woodworking
We all know that a picture is worth a thousand words, but what about a picture frame? The right frame can add elegance and style to any photograph, painting or other work of art. But how do you go about choosing the right frame? And once you’ve chosen the frame, how do you go about attaching it to the artwork?
In this article, we’ll explore the process of choosing and framing a work of art. We’ll start by discussing the different types of frames available, and then we’ll move on to the process of attaching the frame to the artwork.
When choosing a frame, there are a few factors to consider. The first is the size of the frame. The frame should be large enough to frame the artwork, but not so large that it overwhelms the artwork. The second factor to consider is the style of the frame. The frame should match the style of the artwork, and it should also match the style of the room in which the artwork will be displayed.
The third factor to consider is the color of the frame. The frame should contrast with the color of the artwork, but it should also match the color of the room in which the artwork will be displayed. The fourth factor to consider is the type of frame. There are three main types of frames: wood frames, metal frames, and plastic frames.
Each type of frame has its own advantages and disadvantages. Wood frames are the most traditional type of frame, and they come in a variety of styles and colors. Metal frames are more contemporary than wood frames, and they come in a variety of shapes and sizes. Plastic frames are the most affordable type of frame, and they come in a variety of colors and styles.
Once you’ve chosen a frame, the next step is to attach it to the artwork. The most common way to do this is to use a picture frame sled. A picture frame sled is a tool that allows you to attach the frame to the artwork without damaging the artwork.
To use a picture frame sled, you first need to attach the frame to the sled. Then you need to attach the sled to the artwork. Finally, you need to tighten the screws to secure the frame to the artwork.
If you’re not using a picture frame sled, you can attach the frame to the artwork using a number of different methods. The most common method is to use nails or screws. You can also use a glue gun to attach the frame to the artwork.
Once the frame is attached to the artwork, the next step is to add the glass. The glass should be placed in the frame so that it covers the artwork and the frame. Then you need to attach the back of the frame to the glass.
The final step is to attach the hanger to the frame. The hanger should be attached to the back of the frame so that the frame can be hung on a wall.
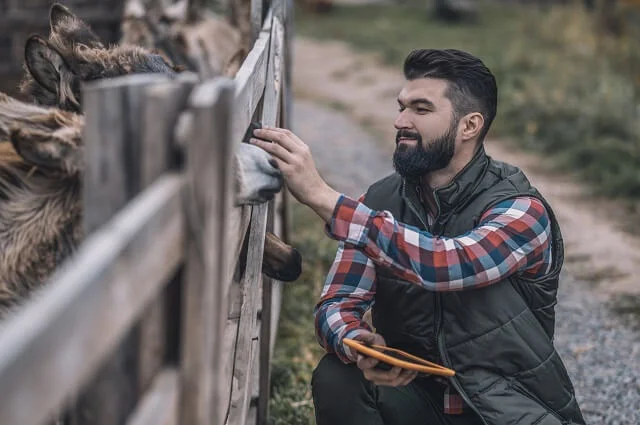
Hi everyone! I’m a woodworker and blogger, and this is my woodworking blog. In my blog, I share tips and tricks for woodworkers of all skill levels, as well as project ideas that you can try yourself.