Introduction
Japanese woodworking joinery is a style of woodworking that involves joining two pieces of wood together for strength and durability, the focus being on aesthetics as opposed to utility. This joinery technique enables wooden structures to be built that are both aesthetically pleasing and strong. As seen in traditional Japanese architecture, carpentry, and furniture production, Japanese joinery is highly regarded for its craftsmanship and attention to detail.
The term “joinery” can be interpreted in different ways by different professions; however, within woodworking it usually refers to wooden components connected using various methods such as nails, screws, or adhesives. In contrast to Western joinery techniques that rely on metal fasteners like nails or screws, traditional Japanese joinery uses specific types of interlocking joints which can include cutting complex shapes into the woodwork in order to fit them together without the use of fastening materials. The advantage of this is that these joints create structural integrity so that even large objects such as furniture or buildings can be constructed without any metal touches. As a result of this careful attention to detail, Japan has been able to preserve some exquisite examples of traditional architecture since the 8th century.
One example of Japanese joinery is called mitokori (三斗栓). This type of joint acts as a corner bridging joint with two angled tenons coming from outside the corner which then combine with two cuts from inside the corner making three parts connect together at a 90 degree angle forming a nice transition between surfaces. Mitokori often features curved lines in the leg-tenon assembly which are decorated further with embellishments like detailed carvings.
Lap joint (押止)is another form of joint used extensively in Japan which involves inserting lap boards into specially designed grooves at right angles so as to increase stability when connecting dissimilar materials or pieces within an assembly. The designs range from simple straight wedges through highly decorative planking patterns known as ubameko (添え子)or gaku haraiko (皿払子). Generally these patterns are further decorated with carving techniques used either directly on the surface or around it for a more elaborate look.
Japanese woodworking joiners also employ many other techniques such as frame and panel door construction which utilizes rabbeted panels housed within adjustable frames filled with shoji paper openings; tsukuri-miteyu joints using dowels cut crosswise along grain laid flat against each other forming stiles; and keyaki muna tsuki joints made up of small wedge shaped pieces fitted into routed pockets creating friction locks so they won’t come apart while still allowing movement without reducing strength over time due to shrinkage or expansion caused by changing weather conditions. Other popular methods include mortise and tenon where one piece slot fits tightly into another; double scarf lap joint consisting multiple wedged strips locking long rectangular members together; dai shachi joi employing mirror sharp curves created by thin reeds inserted tangentially between two mating members held by sliding horizontally inserted keys through aligned enlarged holes called omote-zashi; and japanning where lacquered metal sheets are affixed onto wooden surfaces providing needed protection from harsh elements while adding both beauty and value over other types finishing processes like staining or painting alone.
Japanese Woodworking Joinery has become widely renowned for its unique craftsmanship, beautiful designs and attention to detail that sets it apart from other styles of woodworking in terms of structure and performance abilities. While certainly common in traditional Japanese architecture, carpentry, furniture production, boats building etc., modern day applications have also grown immensely thanks largely due recent advances made among technology ensuring easier preparation steps taken before joining components can take place – making them much faster than would otherwise be possible by keeping traditional hand tools based approach alive yet no longer time consuming as first-time results tend to take lesser amount attempts reach acceptable consistent output quality demands users now expect end product have meet ongoing performance expectations no matter what level design complexity arrives with specific individual projects regardless planned fruition’s particular fitting usage may require once accomplished happy customer reports back notifying job well done proving met requirements desire customer anticipation moves post completion stage response readies hold steady seal approval excellence performed verified shortly after arrival location finishes residing neatly put place ready admire proudly show off allow witness first glance awe wonder admiration accompanies upon reveals task accomplished masterfully let everyone knows create properly mastered skill mastering proficiency process reacquiring acquired skills along development journey helping spread practice word gaining popularity along strive success taken forth adding burst new life creativity innovation mix ever realizing constant perfectible improvement possibility giving enthusiasm keeps burning hot burn longer together heading brighter tomorrow unity solidarity offer assemble solidarity embrace
A Brief History of Japanese Joinery
Japanese woodworking joinery has been practiced for hundreds of years throughout the country’s history. As far back as 6th century CE Japan, records show that complex construction joints were being used to create sacred artifacts such as pagodas and shrines. Throughout the centuries, various temples and castles have been built utilizing a wide variety of joinery techniques. These construction methods eventually evolved into what is known today as “Shokunin Carpentry” or Japanese Woodworking Joinery.
The tools used to create these intricate designs have also changed over time and now include chisels, planes, saws and hammers which are still widely used in traditional Japanese carpentry. In addition to these tools, Japanese joiners use natural adhesives made from tree sap or rice paste which help bind the joints together securely. Furthermore, Japanese joiners typically use “loose-tenon” methodology which involves cutting mortises into thicker joists that are then filled with separate pieces of timber containing T shaped cuts at each end. This allows more flexibility when creating large constructions without having to rely on the strength of one particular joint alone. Finally, traditional wooden pegs called ‘dowels’ may be inserted between the two pieces of wood in order to ensure a strong connection between them.
Today, the craftsmanship behind traditional Japanese woodworking joinery is taught and passed on through apprenticeships which are seen as essential for preserving this hallowed tradition. By learning this skill first hand from experienced woodworkers in Japan, many practitioners both inside and outside the country try their best to preserve the skill and keep it alive for generations to come.
Common Methods of Japanese Joinery
A traditional method of woodworking and carpentry, Japanese joinery is an intricate form of craftsmanship. Multiple techniques are used to build strong joints without the use of nails or screws and can include typical dovetail construction to complex gridlock clamping. Common methods of Japanese joinery include:
Kigumi Joints: One of the oldest types of joinery, kigumi involves cutting a series of interlocking notches along two mitered pieces of wood, allowing them to sit flush with each other when assembled.
Mejiro Joinery: Used especially in furniture making for its simple yet strong design, mejiro interlocks two pieces together at their end grain corner and provides a smooth, tight fit that ensures durability.
Fukugi Joints: Originating from the Okinawan region, fukugi joints involve perpendicular cuts along both pieces which match up perfectly when slotted together creating a tight, secure joint.
Dodai Joinery: Ideal for framing shelving or doorways, dodai joining is one of the more complex forms which utilizes sharp angles but yields great results due to their stability and strength.
Tsukuri Tenons: A fundamental technique for constructing frames and boxes is tsukuri tenon joining whereby interlocking rectangular shaped tenons are ‘trapped’ within a series of slots matching their shape beneath the frame’s exterior surface. This process requires exact precision and accuracy for good alignment behind the proud faces.
Traditional Tools Used In Japanese Joinery
Japanese joinery is a type of traditional woodworking that involves intricate interlocking cuts and joints that create strong and stable furniture. The jointing technique is often used in the construction of temples, shrines, and other structures due to its strength and durability. Japanese joinery has long been used in Japan and throughout Asia, with artisans honing their craft over centuries.
To use Japanese joinery, artisans traditionally utilize several specific tools, including chisels, coping saws, handsaws, planes, gimlets (boring devices), awls (tools for marking or measuring), hammers, drills and squares. Chisels come in various sizes and shapes to accommodate different types of joinery; the most common being rectangular with a curved blade for paring wood quickly. Coping saws are typically U-shaped blades used to cut fine details like curves or circles into wood. These are also known as fret saws since they can be used on curved surfaces as well as flat surfaces with just the same speed and accuracy. Hand saws include dozuki spiral pull saws that are designed for close-quarter cutting of wood grain for finer work such as flush cutting or tight cuts around corners, while larger crosscut saws can be used on thicker pieces of wood. Planes have rounded blades adjusted through a screw mechanism which is then locked into place when the appropriate depth is achieved. Gimlets are small rotary drill bits used mostly for boring but also can be fitted with certain shaped heads to make angled holes instead of circular ones. Awls allow carpenters to mark or measure by punching accurate holes at desired points along a line or piece of lumber. Hammers come in various weights depending on what type of job needs to be done; lighter ones help prevent splitting when pounding in delicate items like tacks whereas heavier ones are necessary for heavier tasks such as joining two large pieces that require extra force for connection security. Drills can be utilized if screws are needed to add extra support when joining two pieces together; the bits themselves coming in many sizes from very small jewelry size up to industrial versions capable drilling deep holes into thick logs for large projects involving multiple timbers joined end-to-end—all made possible through hand-held drills powered by electricity or even cordless rechargeable models providing convenience nearly anywhere without having an outlet nearby. Lastly squares are often seen as indispensable tools due to their usefulness when laying out pieces so that they’ll fit correctly when joined; especially squares with scribes marked onto them allowing measurements or lines drawn onto lumber easily while increasing accuracy during certain time-sensitive jobs—allowing even the most novice carpenter just starting out saving valuable time making the right cuts right away!
Achieving Impressive Visual Effects With Japanese Joinery
Japanese joinery is a centuries-old tradition in woodworking that uses intricate cuts, interlocking pieces and creative assembly techniques to achieve complex shapes without the use of nails or screws. This technique looks fragile but can be incredibly strong and durable—attesting to the skill of Japanese artisans who have crafted this method over time.
Japanese joinery is used to create beautiful, functional objects like furniture and architectural components. The extremely precise and detailed cuts of this technique allow these objects to take on aesthetically pleasing shapes, curves and details that are enhanced by the careful assembly process. While more expensive than other joining methods, it produces an impressive visual effect with clean lines and symmetrical composition. Movement within the structure can also be achieved by thoughtful placement of brackets and pins, creating balance while allowing parts to move freely. In addition, positive energy (or “ki”) is said to flow through the gap in these interconnected components—a concept often incorporated by Japanese designers into their projects for good luck. Japanese joinery is truly an art form: its unparalleled beauty enables craftsmen to bring out the best of each material’s character, producing spectacular results that stand the test of time.
Comparing Japanese Joinery To Other Types of Joinery
Japan has a rich woodworking tradition, and its joinery, known as nakatsugi (なかつぎ) or Japanese joinery is considered to be some of the strongest and most elegant in the world. Japanese joinery is often used when constructing objects such as tea corners (chabudai), tansu cabinets and mizuya kitchen cupboards.
Japanese joinery is unique compared other types of joiners in its robustness and beauty. The majority of joints are made with no nails or screws, relying only on wooden pegs pushed through holes drilled with traditional Japanese tools called oomi (大工). This type of joint offers superior strength between the two pieces without limiting their ability to expand and contract due to temperature or humidity. The use of wood also encourages a tighter seal around each peg making them very difficult to remove or separate once assembled.
The application of these complex designs can also give elements an air of sophistication that cannot be replicated with other forms of joinery. Motifs such as octagons, crosses, butterflies, and even diamonds are often seen within construction pieces to create visual appeal while reinforcing structure at the same time. Used artfully Japanese joinery can add visual interest to any table, room divider, stair system or furniture piece while maintaining structural integrity for a lifetime.
Benefits And Advantages of Japanese Joinery
Japanese woodworking joinery has a long and rich history in Japan. These wood joints have been used for centuries to join together pieces of wood to form structures that are both strong and flexible. A wide range of different joints is used, ranging from simple dowels and half laps to more complex finger joints, mortise and tenon, scarfed-out joints etc. Each joint type has its advantages and benefits which make them a popular choice amongst woodworkers today.
One of the main advantages of Japanese joinery is that it provides flexibility in design while still being extremely strong and stable. Its combination of interlocking components allow craftsmen to create intricate forms that would be difficult or even impossible with other joining techniques. The tight fits between the joint components also provide stability over time as the entire structure tends to become one solid piece when held together properly. This makes Japanese joinery ideal for large projects such as furniture or architectural construction since the components can expand or contract without weakening the structure. Furthermore, Japanese joinery does not require any glue or fastners; instead it relies on friction between the pieces to hold them together which results in a cleaner finished product in comparison to other joining methods.. Additionally, because there is no need for adhesives, nails, screws or bolts this style of joining significantly reduces working time by eliminating many steps in the process.
Incorporating Modern Techniques To Enhance Japanese Joinery Results
Japanese woodworking joinery is renowned for its beauty and strength, using methods that have been in use for centuries. However, nowadays modern techniques are used to make the experience faster, easier and more reliable. For instance, biscuit or dowel jointing in furniture making has become widely utilized with many professional woodworkers. This involves using a power tool to cut shallow grooves into two pieces of material which house biscuits or dowels that allow tight joints to be created quickly.
Hand joinery is still very popular among Japanese workers, though modern techniques have been adapted to suit this traditional style of craftsmanship. For instance, the drawbore joint is a classic example of hand-work combined with modern powered drills. Using a drill bit slightly smaller than the peg that will go through the joint; holes are drilled at an angle just slightly larger to allow for adjustment as it is being tapped into place with a mallet. This creates an incredibly secure connection between materials that can easily adjusted by any adjustments made from pieces being in or out of alignment or through misdrilling holes while drilling them by hand.
Other combinations of traditional and modern practices offer great versatility when woodworking bindings such as mortise and tenon joints, scarf joints and even finger joints which use precision cutting machines to get results far superior than the finest craftsman could get without such powerful tools. By mixing modern technology with tried and true methods lots of time can be saved on labour allowing artisans to focus on design elements not on mundane details associated with any form of joinery needed in woodworking projects.
Tips From Experts For Using Japanese Joinery To Its Full Potential
Japanese joinery is a traditional craft with its own terminology, tools, and techniques. The results of Japanese joinery can be seen in many fine furniture pieces, cabinetry, and even elaborate structures like temples and shrines. Many makers have found success with Japanese joinery when adding detailed design elements to their work that require strong and durable woods to come together without the use of screws or nails.
The precise fit and precision visible in Japanese woodworking joinery is admired around the world. Here are some tips from experts on how to make the most of this ancient technique:
1. Start with the highest quality materials possible – High-quality hardwoods like cherry, walnut, teak, maple and hinoki cypress will yield better results than softer woods. Working with harder woods might seem intimidating at first but it allows for more precise cuts that contribute to the overall strength of your joint when completed.
2. Make sure your tools are sharp – A dull saw or chisel won’t get you very far in completing a cleanly joined joint as slipping off course could damage the piece you’re working on or create an inconsistent cut that won’t properly fit together later on duct joints – Mallets, chisels and hand saws are essential tools for creating traditionally styled joints using ‘deadman’ strength which allows gravity to apply pressure while components remain joined intact without hardware or adhesives
3. Practice makes perfect – Even experienced timber crafters must continually practice these difficult joints until their muscle memory takes over. Skills such as controlling angles while sawing accurate lines take time to master so expect several mock-up pieces before getting it right!
4. Choose appropriate grain direction – Different woodworking joint types require different grain directions; especially important when constructing mitered corners where choosing a perpendicular orientation will produce best results by allowing each half support one another outwards from the corner itself for superior strength.
5. Always use caution – While Japanese joinery relies entirely on friction and tight fits between adjacent parts instead of glue or fasteners it is still possible for those components to become loosened over time especially in heavily used items such as furniture so checking periodically for wear is recommended before any project is considered finished and ready to be used!
Wrapping Up
Japanese Woodworking Joinery is a traditional method of creating structures and furniture out of wood. It is based on the idea of connecting two pieces of wooden material together in such a way that they are strong, yet simple and elegant in appearance. This joinery technique dates back centuries and has been used to build everything from cabinets to public buildings. The most common types of joints used in Japanese Woodworking Joinery are the through-dovetail, mortise-and-tenon, halved joint, half blind dovetails, miter joints and lap joints.
The beauty of Japanese Woodworking Joinery lies in its simplicity; without the need for complicated tools or machines, it allows for delicate yet sturdy designs to be created quickly with few parts. Furthermore, due to the use of natural materials like wood that are sustainably sourced from managed forests, not only will there be no environmental impact but these creations will also last an incredibly long time. As such Japan’s woodworking joinery tradition continues to spread through international markets as more people seek out traditional carpentry methods that can offer both elegance and sustainability.
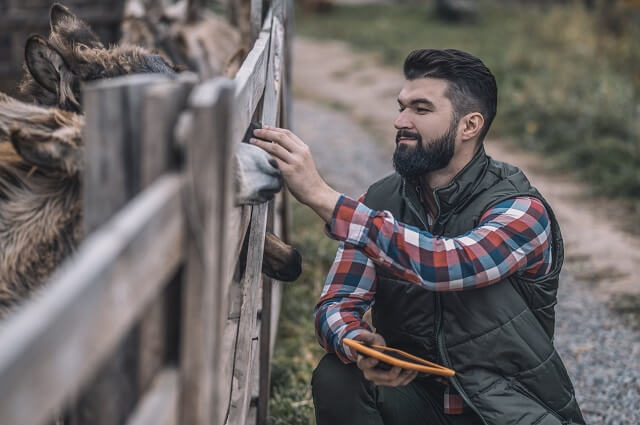
Hi everyone! I’m a woodworker and blogger, and this is my woodworking blog. In my blog, I share tips and tricks for woodworkers of all skill levels, as well as project ideas that you can try yourself.