Introduction to OSHA Woodworking Standards
OSHA woodworking standards are guidelines and regulations from the Occupational Safety and Health Administration that help ensure safe working conditions in woodworking shops. These standards protect workers from potential hazards, such as saws, sharp tools, flying debris, chemical fumes, and falling objects. They also reduce the risk of work-related injuries and illnesses by setting limits for specific noise levels and equipment operation. OSHA woodworking standards are intended to help businesses comply with safety requirements and maintain a safe working environment, while also preserving the quality of their finished products. In particular, these standards address topics such as machine guard construction, personal protective equipment use, and fire protection plans. Proper adherence to these standards can provide a safe work environment for workers while minimizing the likelihood of costly fines or litigation associated with workplace accidents. Above all else, these regulations ensure that employers take all necessary steps to ensure their employees’ safety in the workplace.
Overview of OSHAs Basic Woodworking Standards
OSHA’s general woodworking standards ensure that employees are provided with a safe and healthy work environment. These include protecting workers from the various hazards present in these environments, such as exposure to airborne particles, noise, heat, dust and smoke, improving visibility and proper ventilation of the space. Furthermore, requirements exist on how to store materials properly, how to maintain machines in good condition, and maintaining all electrical parts of the machines in a secure manner. Additionally, fall protection is required if platforms or steps are used for any type of task in elevated areas above ground level.
Other requirements include taking proactive measures for accident prevention by providing safety training and instruction for all tools used by employees. This also includes regular testing of machinery to make sure it is up-to-date with its safety features. Proper time management of employees’ working hours is also expected by OSHA; overtime must be avoided as much as possible to prevent fatigue or employee exhaustion leading to mistakes on the job. Finally, personal protective equipment should be worn where appropriate”such as safety goggles when operating power saws and gloves when handling sharp objects or other hazardous materials.
Specific OSHA Regulations for Woodworking
The Occupational Safety and Health Administration (OSHA) requires employers to provide a safe work environment for all employees. This includes specific regulations designed to protect woodworkers from hazards in the workplace. These regulations apply to any type of business that makes, uses, repairs, stores or handles wooden products, including sawmills, cabinet and furniture makers, boat builders and more.
OSHA regulations for woodworking require certain protections for workers who use machinery such as saws and routers. All machines must have proper guards installed on them to protect operators’ hands. Computerized numerical control machines must also be guarded to prevent the machine from making contact with workers while it is running. In addition, shields must be mounted around any power-driven blades or rollers that are exposed on any machine.
OSHA also requires employers of woodworking businesses to ensure protective clothing is worn by employees when using power tools or operating machinery. This includes eye protection when operating large equipment such as drill presses or planers. Hearing protection is also recommended if loud noise levels exceed 85 decibels in a work area as well as respirators to protect against dust particles in the air when working with sawdust-producing machines such as sanders.
Finally emergency procedures should be established and posted clearly in the workplace for all employees regarding emergency scenarios such as fires, chemical spillages and hazardous material impacts on the environment. Emergency personnel contacts should be provided along with designated escape routes and performance goals for emergency personnel arrival times such as fire suppression response teams etc…
How to Implement and Maintain OSHA Woodworking Standards
The Occupational Safety and Health Administration (OSHA) is committed to keeping workplace environments safe, and their woodworking standards are an important part of this effort. It’s the responsibility of employers to implement and maintain OSHA woodworking standards in their workplace. To do this effectively, employers should follow a few key steps:
1. Identifying Hazards: First, assess the workplace and identify potential hazards that could result in injury or health risks. Look out for potential slip-and-fall hazards, tripping risks, airborne dust contamination, and hazardous objects that can cause cuts or puncture wounds.
2. Risk Assessment: Once the potential risks have been identified, it’s important to assess each risk to determine the likelihood that employees may be exposed to them. For example, if there is a risk of airborne dust contamination it’s important to assess how often workers will likely be exposed to this hazard based on their job roles and tasks.
3. Creating Protocols: Next, employers should create protocols for addressing these risks accordingly. For example, mitigation tactics such as creating designated pathways to reduce trip or fall hazards or providing dust masks for workers in areas with heightened dust levels can be effective at minimizing safety concerns associated with those hazards.
4. Training Employees: Finally, employees should receive training on proper safety protocol within the workplace environment so they know what actions they should take when exposed to any identified risks or in general while completing tasks related ot woodworkinhg activities within the workplace. This type of training not only helps employees stay safe but also ultimately creates a safer working environment overall by reducing these hazardous situations altogether!
Reasons to Comply with Woodworking Standards
Complying with Osha’s woodworking standards offers an array of benefits to businesses and the individuals who work with the material. Employee safety is one major benefit of following the regulations, as it keeps workers safe from hazardous materials and creates a more secure environment for them to perform their duties. Increased productivity is also likely due to fewer incidents that result from employees not being familiar with proper safety protocols. And from a legal standpoint, compliant companies are far less likely to be held liable for damage sustained in the workplace that results from incorrect use of woodworking tools or the presence of hazardous materials such as saw dust. Compliance also demonstrates an organization’s commitment to ethical business practices and can help attract better talent, especially younger and more technically proficient people who may be aware of OSHA regulations. All in all, there are numerous reasons why compliance with OSHA regulations is beneficial in terms of safety, productivity, and legal protection.
Potential Hazards of Non-Compliance
Financial penalties: When the Occupational Safety and Health Administration (OSHA) finds that your business is in violation of OSHA Woodworking Standards, you may be subject to serious financial penalties. Depending on the severity of the violation and how long it has been left unchecked, these fines can range from hundreds to thousands of dollars for every infraction. In some cases, especially with severe and/or repeat violations, criminal penalties may also apply.
Employee safety risks: Non-compliance with OSHA Woodworking Standards puts your employees at risk for potential accidents or injuries in the workplace. Woodworking machinery can be highly dangerous when not maintained properly or used incorrectly, so it is important that these standards are followed closely to protect your staff.
Reduced reputation: Not only is failing to meet OSHA Woodworking Standards costly financially and potentially hazardous, but it can also damage your business’s reputation. Clients and customers expect businesses they work with to operate according to industry regulations, and not meeting those standards reflects poorly on their judgement. Failing to comply with safety regulations can result in losing current clients as well as deterring new ones from working with you.
Resources for Woodworking Professionals
The Occupational Safety and Health Administration (OSHA) sets the standards for woodworking industry safety. OSHA Woodworking Standards provide employers and employees with guidelines to ensure workplace safety in a variety of situations. It covers topics related to hazardous chemicals, fire safety, personal protective equipment (PPE), machine guarding, ergonomics and noise.
More specifically, these standards help protect workers from hazardous dust particles, airborne gases, vapors and mist resulting from the use of various chemicals during finish or paint stripping. Additionally, staff must be trained on using materials safely as well as proper disposal practices for hazardous material waste. All machines must be guarded to prevent loose clothes or hair becoming entangled in moving parts or contact electrical hazards such as shock or spark produced from tools such as grinders or saws. Proper ventilation systems must also be installed to improve air quality and evacuate dangerous heat vapor out of working areas. Furthermore, workers need appropriate PPE that meets the standards set by OSHA including gloves, coveralls and masks with particulate filters depending on the task being performed. Last but not least employers need to monitor noise levels within their premises and institute control measures if sound output is excessive according to OSHA guidelines.
Professionals involved in woodworking can benefit greatly from resources available concerning OSHA woodworking standards; these include relevant publications such as books on OSHA Publications 29 CFR 1900-1910 Regulation Series https://www.osha.gov/pls/oshaweb/owadisp.show_document?p_table=STANDARDS&p_id=10051as well as federal government contacts who can assist with inquiries; furthermore there are numerous Industry Trade Organizations that offer useful information about this topic such as Safe Woodworking http://safewoodworkingtipsandtoolsguide.com/.
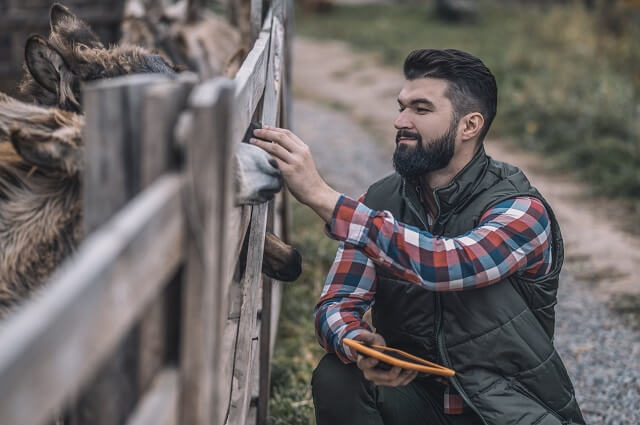
Hi everyone! I’m a woodworker and blogger, and this is my woodworking blog. In my blog, I share tips and tricks for woodworkers of all skill levels, as well as project ideas that you can try yourself.