Introduction
Sashimono woodwork joints are a specialized craft in woodworking that uses only wooden joints and pins (dowels) to assemble pieces without any nails or other mechanical fasteners. As one of the oldest traditional Japanese carpentry techniques, sashimono uses several types of interlocking joints as well as special peg joinery which is designed to give furniture greater strength and stability. These time-honored joints have a neat appearance and result in seamless construction with no exposed screws or nails.
The key components of this ancient craft are the mortise and tenon joint variations, specialty angles, pins, wedges, and dovetails, all of which combine to form the fundamental framework for building complex pieces of furniture. The creation of sashimono utilizes skills handed down through generations”with each piece crafted by an expert carpenter who takes years to perfect their craftsmanship. Among the self-developed joint structure designs available for use, the craftsman can actually customize a particular piece’s trajectory more fluently than with nails or glue. In practice, this technique produces pieces that are often much more durable than modern built furniture due to its ability to absorb shocks more easily.,
As a result of its relative rarity compared to today’s methods, sashimono woodwork joints tend to be sought after for their unique qualities in restoration projects as well as for fine art projects using rare woods with intricate grain patterns. Its traditional beauty adds a memorable touch to any space adorned with it, making it perfect for high-end residential builds or elite designs destined for museums and galleries around the world.
Origins and Historical Significance of Sashimono Woodwork Joints
Sashimono woodwork joints have origins that date back to early Japanese feudal times (around the 17th century) when their use was first documented. During this time, they were widely used by carpenters to construct furniture and other wooden structures. Sashimono is seen as a symbol of craftsmanship, and a display of elite carpentry skills.
Today, sashimono woodwork joints are still widely used as a decorative technique in Japanese style architecture due to its ability to give strength and stability to the structure, while also looking aesthetically pleasing. The details that sashimono adds can be seen featured in traditional temples, shrines, pavilions and more throughout Japan. Especially around Kyoto, where interlocking wooden details are an intricate part of the traditional layout.
A few centuries ago, pieces featuring these intricately crafted joinery designs were historically sometimes presented by shogunates as gifts or homage from one dignitary society to another. That factor has greatly added to the cultural significance of sashimono woodwork joint designs making them more iconic over time.
Benefits of Sashimono Woodwork Joints
Sashimono woodwork joints offer a range of benefits to those looking to create beautiful wooden furniture. They are not only aesthetically pleasing but they also provide great stability and strength to the piece due to their interlocking design. Additionally, they are incredibly easy to assemble as the parts simply slide into place which makes them ideal for beginners and experts alike. Another advantage is that they use little or no nails which can save time when constructing furniture and help ensure a clean look. Finally, sashimono joint designs can help provide an extra touch of sophistication to any room by adding a unique visual element.
Different Techniques used in Sashimono Woodwork Joints
Sashimono woodwork joints are a traditional form of joinery used in Japanese carpentry. These types of joints are most often used to make furniture, buildings, and objects by interlocking different pieces of wood without the use nails or screws. The techniques employed in sashimono woodwork require skillful craftsmanship and produce clean lines and strong joints.
Common techniques used in sashimono woodwork include dovetailing, half-blind dovetailing, dadoing, concealed mortise and tenon, bridle, miter, dovetail miter, coped miter, finger, box or corbel jointing. The dovetailing technique involves using angled cuts to create an interlocking joint between two boards while half-blind dovetailing is almost similar but it is done on just one side of the joint. Dadoes are a trench cut along the length of a board that will fit another board into it; while the mortise and tenon joint is made out of a meeting of two tongues and grooves respectively from two joining boards that fit each other securely with glue or pins. Bridles also involve two parts meeting together but this technique uses an opening cut into one part that fits over the edge of the other part to produce a neat corner piece. Miters use an angled cut for two pieces making an ’L’ shaped corner which must be held together with screws or adhesive; dovetail miters include adding separate triangular pieces at the bottom to give extra strength to the joint; coping miters involve cutting away one surface in order for the board with bevels to fit flush together. Finger joints also have angled cuts connecting several boards along their length while boxes or corbels require a piece resting on top using support flanges or wedges typically used as decorative elements on furniture.
Advantages of using Sashimono Woodwork Joints
Sashimono woodwork joints offer many advantages in the construction of cabinetry and furniture. They are well known for their strength, rigidity, and precision, making them an ideal choice for joinery. Furthermore, sashimono joints are very durable since they are made from solid wood that has been expertly cut and shaped. This means that your furniture will last longer over time compared to other jointery designs. Additionally, sashimono woodwork joints provide a seamless look to any piece of furniture as the two pieces slot together perfectly with no visible screws or nails required. Finally, due to their intricate design, these joints make an excellent decorative element in home decor.
Common Mistakes when Creating Sashimono Woodwork Joints
One common mistake when creating sashimono woodwork joints is that the cuts and angles are not precise enough. As this type of woodworking demands precision, any inaccuracies in the angles or cut lines can significantly affect the final result of the joint. Another common mistake is to use woods of different density; if there is a large difference in hardness or elasticity between two pieces of wood, it could lead to structural instability in the finished joint. Lastly, when constructing sashimono woodwork joints including dovetails and box joints, it is essential to make sure that each cut line and corner are exactly aligned before assembly; any incorrect alignment can cause issues with the fit as well as stressing out and weakening joinery parts over time.
Tips for Crafting a High-Quality Sashimono Woodwork Joint
When crafting a high-quality sashimono woodwork joint, it is important to pay close attention to the details and use precise methods for joining the two pieces of wood together. Before starting, a thorough understanding of the tools and techniques needed is necessary in order to achieve precise results.
First, select quality tools specifically designed for this type of joinery. It is important that they are sharpened properly and checked before each use to ensure accuracy. Choose woods with straight grain and minimal knots, as these will provide superior strength when cut precisely. To create each joint, begin by marking out the exact placement of each piece and drilling pilot holes at intersecting points; this will allow for better alignment when joining the components.
Next, carefully cut a ‘groove’ into both pieces that correspond with one another forming an interlocked ‘finger’ shape that nests the two components together; be sure to leave adequate room for expansion during seasonal changes in humidity so as not to disrupt their fitment. Once completed, hammer or press in a dowel pin at the point of intersection which provides extra strength and prevents movement from external forces. Finally, apply high-grade glue around joints to secure connection between woods for maximum longevity.
Examples of Famous Sashimono Woodwork Joints
Sashimono woodwork joints are traditional woodworking joints originating in Japan. These intricate details provide strength to wooden structures while adding a unique, decorative aesthetic. Examples of famous sashimono woodwork joints include the dovetail joint, which is used to join perpendicular pieces of wood, and the mortise and tenon joint, which involves inserting one piece into another for a strong interlocking connection. Another type of sashimono joint is the half-blind dovetail, where one side of each dovetail corner remains hidden so only a single side appears on the finished product. Finally, the mizumokuri joint uses decorative pegs to join two intersecting beams at their intersections, offering stability to both pieces of wood. All these types of joints use sophisticated techniques and craftsmanship that have been perfected over hundreds of years in Japan.
Conclusion
Sashimono Woodwork Joints offer a wide array of advantages that make them an attractive choice for woodworking projects. They provide strength and stability, with intricate craftsmanship, when used properly. They are relatively easy to assemble and create due to their user-friendly designs, allowing woodworkers to build projects with confidence. They offer greater design flexibility compared to conventional joints which result in improved aesthetics and reduce the need for specialized tools or materials. Finally, Sashimono Woodwork Joints use fewer parts than traditional joints, simplifying the construction process and helping to reduce costs. Overall, they provide excellent utility while increasing the durability and aesthetic appeal of any woodworking project.
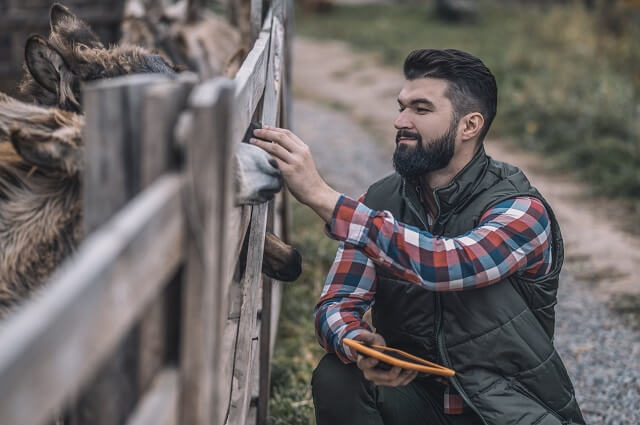
Hi everyone! I’m a woodworker and blogger, and this is my woodworking blog. In my blog, I share tips and tricks for woodworkers of all skill levels, as well as project ideas that you can try yourself.