What is a chamfer in woodworking? When it comes to woodworking, the concept of chamfering is an important technique that can make a significant impact on the overall aesthetics and functionality of a piece. In this article, we will delve into the world of chamfering, exploring its history, different types and styles, tools needed, step-by-step guide, expert tips, applications in woodworking projects, and common mistakes to avoid.
Chamfering has been used in woodworking for centuries and has become a popular technique due to its ability to add visual interest and create smooth edges. Understanding the concept of chamfering and its importance in woodworking is essential for woodworkers of all levels.
In this section, we will provide an overview of chamfering and why it is such a fundamental aspect of woodworking. We will also explore the historical significance of chamfering and how it has evolved over time. Additionally, we will discuss the various types and styles of chamfers used in woodworking and their respective techniques. Join us as we uncover the intricacies of chamfering and its role in creating beautifully crafted wood pieces.
The History of Chamfering
One of the earliest known examples of chamfering can be traced back to ancient Egyptian woodworking, where it was used to decorate furniture and architectural elements such as columns and beams. The Greeks and Romans also utilized chamfering in their woodworking, particularly in the construction of intricate furniture pieces and intricate joinery. The technique continued to evolve over the centuries, with different cultures developing their own unique styles and methods of chamfering.
In medieval Europe, chamfering became a popular technique in carpentry and joinery, particularly in the construction of timber-framed buildings and furniture. The use of chamfers not only added visual interest to wooden structures but also served practical purposes such as easing sharp edges for safety and creating strong joints. Today, chamfering remains a fundamental skill in woodworking, used in both traditional handcrafted pieces and modern industrial manufacturing processes.
Chamfer History | Description |
---|---|
Ancient Egypt | Chamfering used for decorating furniture and architectural elements. |
Greek and Roman | Utilized chamfering in intricate furniture pieces and joinery. |
Medieval Europe | Chamfers became popular in carpentry, joinery, and timber-framed buildings. |
Types of Chamfers
Chamfering is an important woodworking technique that creates a beveled edge on a workpiece, providing both aesthetic and structural benefits. There are several types of chamfers that woodworkers use to achieve different effects in their projects. Understanding the different styles and techniques of chamfering can help you choose the best approach for your woodworking needs.
Here are some common types of chamfers used in woodworking:
- Straight Chamfer: This is the most basic type of chamfer, created by cutting a straight bevel along the edge of the workpiece. It is commonly used to remove sharp edges and add visual interest to furniture and decorative pieces.
- 45-Degree Chamfer: As the name suggests, this chamfer is cut at a 45-degree angle to the edge of the workpiece. It is often used for decorative purposes, such as creating a finished look on table legs or picture frames.
- Curved Chamfer: This chamfer features a curved bevel instead of a straight line, adding a softer, more refined look to the edge of the workpiece. It requires more precise cutting and shaping but can result in beautiful, unique designs.
Each type of chamfer has its own set of considerations and techniques for achieving clean and precise results. Woodworkers often experiment with different styles to find the perfect look for their projects.
In addition to these basic types, woodworkers may also create custom chamfers using specialized tools such as routers and hand planes. These tools allow for greater creativity and precision in chamfer design, opening up endless possibilities for incorporating chamfers into woodworking projects.
Tools and Equipment Needed for Chamfering
Chamfering in woodworking requires a few specific tools and equipment to achieve clean and precise results. The process of chamfering involves creating a beveled edge on a workpiece, and the right tools can make all the difference in achieving the desired outcome. Here is a detailed look at the tools needed for chamfering and their uses:
- Block Plane: A block plane is an essential tool for chamfering as it allows woodworkers to create smooth and consistent beveled edges. It is lightweight and easy to maneuver, making it ideal for chamfering tasks.
- Chamfer Router Bit: For those using a router, a chamfer router bit is an excellent tool for creating precise and uniform beveled edges. These bits come in various angles, allowing woodworkers to achieve different chamfer depths.
- Chisel: A sharp chisel is necessary for refining and smoothing out the chamfered edge. It can also be used to remove any excess material or refine the angle of the chamfer.
- Measuring Tools: Accurate measurements are crucial for achieving consistent chamfers. A combination square or measuring tape can help ensure that the chamfers are uniform across the workpiece.
In addition to these primary tools, there are other accessories that can aid in achieving clean and precise chamfers, such as sandpaper for smoothing out rough edges, clamps for securing the workpiece, and safety equipment such as goggles and ear protection.
Understanding how to use these tools effectively is essential for successful chamfering in woodworking.
Woodworkers should always pay attention to safety guidelines when using these tools and equipment, including wearing appropriate safety gear and following manufacturer’s instructions for tool usage. By having the right tools on hand and using them with care, woodworkers can achieve professional-looking chamfers in their woodworking projects.
Overall, having a good understanding of what is a chamfer in woodworking helps in choosing the correct tools required for successful outcomes.
Step-by-Step Guide to Chamfering
Chamfering is a woodworking technique that involves creating a beveled edge or a furrow along the corner of a wooden piece. It serves both decorative and functional purposes, adding visual interest to the edges of furniture, cabinetry, and other wooden objects, as well as providing a more comfortable and safe feel to the edges.
In this section, we will delve into a step-by-step guide to chamfering, providing an in-depth walkthrough of the process of creating chamfers in woodworking.
Choosing the Right Tools and Materials
Before starting the chamfering process, it’s essential to gather the necessary tools and materials. The primary tool for creating chamfers is a chamfer plane or a block plane with an adjustable mouth. Additionally, you will need marking tools such as a pencil or marking gauge, as well as clamps to secure your workpiece while chamfering. Depending on your project, you may also require sandpaper or files for refining the edges after chamfering.
Marking and Shaping
Once you have gathered your tools and materials, start by marking the area where you want to create the chamfer using a pencil or marking gauge. Next, set your chamfer plane to the desired angle – commonly 45 degrees – and begin shaping the edge of your workpiece by making light passes with the plane. It’s crucial to maintain consistent pressure and keep checking your progress to ensure an even and symmetrical result.
Refining and Finishing
After shaping the initial bevel with your chamfer plane, refine the edge further using sandpaper or files for a smoother finish. Pay attention to details such as removing any splinters or rough spots left from planing. Once satisfied with the smoothness of your chamfered edge, apply any desired finish like stain or varnish before incorporating it into your woodworking project.
By following this step-by-step guide to chamfering, you can achieve clean, precise, and visually appealing beveled edges on your woodworking projects while enhancing their overall aesthetic appeal and functionality. Now that you know how to create chamfers in woodworking, you can incorporate this versatile technique into various projects for professional-looking results.
Tips and Tricks for Successful Chamfering
Choosing the Right Angle
When it comes to chamfering in woodworking, the angle at which the cut is made plays a crucial role in achieving clean and precise chamfers. The most common angles for chamfers are 45 degrees and 30 degrees, each providing a different look to the finished piece.
It’s important to consider the type of wood being used and the overall design of the project when deciding on the angle for the chamfer. Experimenting with scrap pieces of wood can help determine which angle works best for a particular project.
Using Sharp Tools
One of the key factors in achieving clean chamfers is using sharp tools. Dull blades or bits can result in tear-out and uneven cuts, leading to a less professional finish. It’s essential to regularly sharpen cutting tools such as chisels, planes, or router bits before starting a chamfering project. Additionally, using high-quality cutting tools can make a significant difference in achieving clean and precise chamfers.
Securing the Workpiece
To avoid any mishaps during chamfering, securing the workpiece is crucial for safety and precision. Clamping down the wood securely prevents it from moving or vibrating during the cutting process, resulting in cleaner cuts and reducing the risk of accidents. Whether using hand tools or power tools for chamfering, ensuring that the workpiece is firmly secured will contribute to achieving clean and precise chamfers in woodworking.
By following these tips and tricks from experts in woodworking, individuals can enhance their skills and achieve professional-looking chamfers in their projects. Understanding how to choose the right angle, using sharp tools, and securing the workpiece are essential elements for successful chamfering. Practicing these techniques will lead to improved craftsmanship and high-quality finishes in woodworking projects.
Applications of Chamfering in Woodworking
Chamfering is a technique used in woodworking to create beveled edges or angles along the corners of a piece of wood. This process not only adds decorative details to the wood but also serves practical purposes such as preventing splintering and providing a finished look to projects. Understanding the applications of chamfering in woodworking is crucial for any woodworker looking to incorporate this technique into their projects.
One common application of chamfering in woodworking is creating smooth and rounded edges on furniture pieces such as tables, chairs, and cabinets. By adding chamfers to the edges of these items, woodworkers can enhance the overall aesthetic appeal while also making the furniture more comfortable and safe for everyday use. Additionally, chamfering can be used to add visual interest to moldings, door frames, and windowsills, bringing a touch of elegance to interior design elements.
In addition to its decorative uses, chamfering also offers functional benefits in woodworking projects. For example, chamfered edges on cutting boards or kitchen countertops can prevent sharp corners from chipping or splintering over time.
Similarly, chamfers are often added to the underside of tabletops or shelving units to create a smoother transition between surfaces and reduce the risk of snagging or catching on clothing or other objects. This combination of both aesthetic enhancement and practical utility makes chamfering an essential technique for woodworkers across various project types.
Applications | Benefits |
---|---|
Creating smooth and rounded edges on furniture pieces | Enhanced aesthetic appeal & improved comfort |
Add visual interest to moldings, door frames, and windowsills | Elegance in interior design elements |
Preventing sharp corners from chipping on cutting boards or countertops | Improved safety & durability |
Common Mistakes to Avoid in Chamfering
In conclusion, chamfering is a crucial technique in woodworking that adds both aesthetic appeal and functionality to the finished piece. Understanding the history of chamfering and the different types and styles available can help woodworkers make informed decisions about which method will best suit their projects.
Additionally, having the right tools and equipment for chamfering is essential for achieving clean and precise results. Following a step-by-step guide to chamfering and implementing expert tips can help woodworkers avoid common mistakes and create professional-quality chamfers.
Chamfering has been used in woodworking for centuries, and its applications are varied, making it a versatile technique for creating beveled edges on furniture, cabinets, picture frames, and more. The benefits of chamfering include improved safety by removing sharp edges, enhancing the visual appeal of the piece, and creating smooth transitions between surfaces. By understanding how to avoid common mistakes in chamfering, woodworkers can achieve a high level of craftsmanship in their woodworking projects.
It is important for woodworkers to remember that achieving successful chamfers takes practice and patience. By learning from experienced craftsmen and understanding how to use different tools to create various chamfer styles, woodworkers can avoid pitfalls such as tear-out or inconsistent angles. With dedication and attention to detail, anyone can master the art of chamfering in woodworking.
Frequently Asked Questions
What Is the Purpose of Chamfering?
The purpose of chamfering is to create a beveled edge or furrow at the intersection of two surfaces, often to prevent sharp edges, make assembly easier, or improve the aesthetic appeal of an object.
What Does a Chamfer Cut Look Like?
A chamfer cut looks like a sloped or angled surface that replaces a sharp 90-degree edge. It can be seen on the edges of wooden furniture, metal parts, or even on the corners of architectural structures.
What Is the Purpose of the Chamfer Feature?
The purpose of the chamfer feature is to remove sharp edges and corners, making objects safer to handle and reducing the risk of injury. Additionally, it can also improve the overall appearance and symmetry of an object by creating a more polished look.
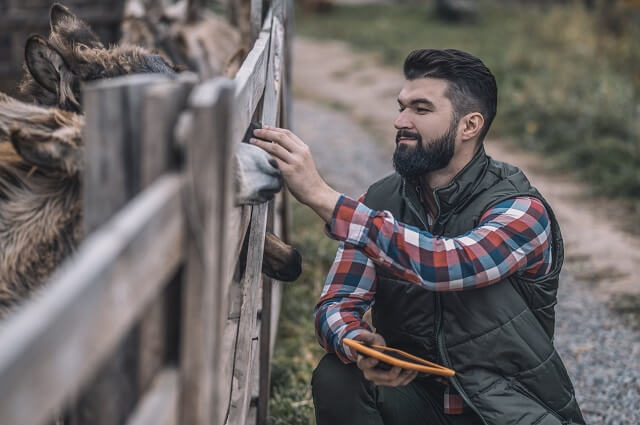
Hi everyone! I’m a woodworker and blogger, and this is my woodworking blog. In my blog, I share tips and tricks for woodworkers of all skill levels, as well as project ideas that you can try yourself.