What is a flute in woodworking, and why is it important to understand this technique? Woodworking is a craft that has been practiced for centuries, requiring skill, precision, and knowledge of various techniques.
One such technique is the creation of flutes, which adds intricacy and detail to wooden surfaces. In this article, we will explore the concept of fluting in woodworking, including its definition, historical significance, tools and materials needed, techniques for creating flutes, practical applications, common mistakes to avoid, and the importance of understanding this technique.
In woodworking, a flute refers to a long, shallow groove or channel that is carved into the surface of wood. Flutes serve both functional and decorative purposes and are commonly found in furniture making and decorative trims. Understanding how to create flutes can greatly enhance the quality and beauty of woodworking projects.
As we delve deeper into this topic, we will also explore the historical significance of fluting in woodworking and how this technique has evolved over time. Additionally, we will discuss the tools and materials needed for creating flutes, as well as the step-by-step process for beginners to master this technique. From practical applications to common mistakes to avoid, our comprehensive guide will provide valuable insights for woodworkers of all levels.
Definition of a Flute
In woodworking, a flute refers to a long, shallow groove or furrow that is usually carved, milled, or routed into the surface of a wooden piece. The purpose of creating flutes in woodworking is primarily decorative, adding visual interest and texture to the wood. Flutes are commonly found on furniture pieces such as table legs, chair backs, and columns, as well as in architectural elements like moldings and trim work.
There are different types of flutes used in woodworking, each serving a specific aesthetic or structural purpose. For example, reeded flutes feature multiple parallel grooves that create a ribbed effect on the wood surface. Spiral flutes, on the other hand, are characterized by a continuous helical groove that runs along the length of the wood. Regardless of the type of flute being utilized, precision and attention to detail are essential in achieving the desired result.
Understanding what a flute is in woodworking is crucial for woodworkers who want to add an extra dimension to their projects. Whether it’s enhancing the appearance of furniture pieces or incorporating decorative elements into interior design elements, mastering the art of fluting can significantly elevate the craftsmanship of woodworking projects.
Types of Flutes | Description |
---|---|
Reeded Flutes | Feature multiple parallel grooves for ribbed effect |
Spiral Flutes | Characterized by continuous helical groove along the wood |
History of Fluting
The history of fluting in woodworking dates back to ancient civilizations such as the Greeks and Romans, who used this technique to enhance the aesthetic appeal of columns and architectural elements. The process of creating flutes involved the use of hand tools such as chisels and gouges to carve out symmetrical grooves along the surface of wood, stone, or metal.
These fluted columns and decorative trims not only showcased the craftsmanship of artisans but also added a sense of grandeur and sophistication to buildings and furniture.
The art of fluting continued to evolve throughout the centuries, with different cultures incorporating their own unique styles and designs. In the 18th century, for example, the neoclassical movement in Europe saw a resurgence of interest in fluting, particularly in furniture making. Craftsmen utilized specialized hand planes and molding cutters to create intricate fluted patterns on tables, chairs, and cabinets, demonstrating a mastery of woodworking skills.
Today, fluting remains a prominent feature in both traditional and contemporary woodworking. Modern advancements in technology have expanded the repertoire of tools available for creating flutes, including routers and CNC machines. Woodworkers can now explore a wide range of creative possibilities when incorporating flutes into their projects, whether it’s adding elegant details to custom cabinetry or crafting personalized heirloom pieces. Understanding the historical significance of fluting helps woodworkers appreciate its enduring appeal and timeless beauty in craftsmanship.
Tools and Materials
Creating flutes in woodworking requires specific tools and materials to achieve the desired results. The most essential tool for creating flutes is a router, which is used to hollow out the wood and create the groove that defines a flute. Additionally, a table saw or bandsaw may be used to cut the initial groove before using the router. Other tools that can be helpful include chisels for refining the flute’s shape and sandpaper for smoothing out any rough edges.
In terms of materials, it is important to select the right type of wood for creating flutes. Hardwoods such as cherry, maple, or oak are ideal for their durability and ability to hold intricate details.
Softwoods such as pine can also be used, but they may be more prone to denting or scratching over time. It’s important to consider the intended use of the flute when selecting materials; for example, furniture pieces may require more durable woods compared to decorative trims.
When creating flutes in woodworking, it is crucial to have a secure work surface and clamps to hold the wood in place during the routing process. Safety equipment such as goggles and hearing protection should also be worn when using power tools. By having the right tools and materials on hand, woodworkers can ensure that they are well-equipped to create precise and beautiful flutes in their woodworking projects.
Techniques for Creating Flutes
When it comes to creating flutes in woodworking, there are several techniques that can be used to achieve the desired results. Here are some step-by-step processes for creating flutes, as well as some tips and tricks for beginners:
1. Planning and Marking: The first step in creating flutes is to carefully plan and mark the location of each flute on the wood surface. This can be done using a ruler, pencil, and marking gauge to ensure that the flutes are evenly spaced and aligned correctly.
2. Cutting the Flutes: Once the markings are in place, the next step is to cut the flutes into the wood using a router or a specialized flute-cutting bit. It’s important to use steady, even pressure when cutting the flutes to ensure a clean and consistent result. Different types of cutting bits can be used depending on the desired shape and depth of the flute.
3. Smoothing and Finishing: After cutting the flutes, it’s important to smooth out any rough edges or imperfections using sandpaper or a file. This will help ensure that the finished flutes have a professional and polished appearance. Additionally, applying a finish such as stain or varnish can enhance the look of the flutes while also protecting the wood.
Tips and Tricks for Beginners:
Remember, creating fluted surfaces in woodworking requires patience, precision, and attention to detail. By following these step-by-step processes and incorporating these tips and tricks into your work, you can achieve beautiful and professional-looking fluted surfaces in your woodworking projects.
Practical Applications
The practical applications of fluting in woodworking are numerous and play a significant role in the creation of various items such as furniture and decorative trims. Understanding how to incorporate flutes into woodworking projects can add an elegant and sophisticated touch to the final product.
Fluted Furniture
Fluted furniture has been a popular choice for centuries, with its distinctive grooved patterns adding character and texture to the piece. Fluted columns, table legs, and cabinet doors are just a few examples of how fluting is incorporated into furniture design. Whether it’s a classic or modern piece, the addition of flutes can elevate the overall aesthetic and provide an interesting focal point.
Decorative Trims
In woodworking, decorative trims often feature fluting as a way to embellish various surfaces. From crown molding to baseboards, fluted trims can be found in many architectural details within homes and buildings. The intricate designs created by flutes enhance the visual appeal of these elements, making them stand out as ornate accents in interior design.
Utilizing Flutes in Custom Projects
Beyond furniture making and trim work, woodworkers also utilize fluting in custom projects such as custom door panels, picture frames, or staircases. By incorporating flutes into these bespoke creations, artisans can transform ordinary pieces into extraordinary works of art that showcase craftsmanship and attention to detail.
Understanding how fluting is used in woodworking opens up endless possibilities for creating visually stunning pieces that add elegance and sophistication to any space. By mastering the techniques for creating flutes and incorporating them into various projects, woodworkers can elevate their craft and produce truly remarkable pieces that showcase the timeless beauty of this age-old technique.
Common Mistakes to Avoid
Improper Measurement and Marking
One common mistake when creating flutes in woodworking is improper measurement and marking. It is crucial to measure and mark the placement of the flutes accurately to ensure that they are evenly spaced and aligned.
Failing to do so can result in uneven or crooked flutes, negatively impacting the overall appearance of the finished piece. To avoid this mistake, it is important to use precise measuring tools such as a ruler or calipers and to double-check all measurements before making any cuts.
Incorrect Depth of Cut
Another potential pitfall when creating flutes in woodworking is making an incorrect depth of cut. Flutes should be cut to a consistent depth to ensure uniformity and visual appeal.
If the depth of cut varies from one flute to another, it can detract from the overall quality of the woodworking project. To avoid this mistake, woodworkers should carefully set their cutting tools, such as a router or plow plane, to the desired depth and make test cuts on scrap material before working on the actual project.
Failure to Secure Workpiece Properly
Failure to secure the workpiece properly can also lead to mistakes when creating flutes in woodworking. Without adequate clamping or securing mechanisms, the workpiece may shift or move during cutting, resulting in uneven or jagged flutes. To avoid this issue, woodworkers should use clamps or bench dogs to firmly hold their workpiece in place during the flute-cutting process. Additionally, using a stable work surface and ensuring that the workpiece is flat and even can help prevent movement during cutting.
By being aware of these common mistakes and taking proactive measures to avoid them, woodworkers can achieve better results when creating flutes in their woodworking projects. These tips can help beginners improve their skills and produce high-quality fluted pieces with precision and consistency.
Conclusion
Understanding what a flute is in woodworking is crucial for anyone interested in mastering the craft. From its historical significance to its practical applications, fluting adds a touch of elegance and sophistication to woodworking projects. By learning about the different types of flutes, tools and materials needed, as well as the techniques for creating them, woodworkers can elevate their skills and create truly stunning pieces.
Fluting has been an integral part of woodworking for centuries, adding both decorative and functional elements to furniture, moldings, and architectural details. By understanding the history of fluting, woodworkers can appreciate its cultural significance and find inspiration for their own creations. Additionally, knowing common mistakes to avoid when creating flutes can save both time and frustration in the workshop.
For those interested in delving deeper into the world of fluting in woodworking, there are plenty of additional resources available. Whether it’s books on traditional woodworking techniques or online tutorials demonstrating advanced flute carving methods, woodworkers have access to a wealth of knowledge at their fingertips. By continuing to learn and master the art of fluting, woodworkers can take their projects to new heights and create masterful pieces that showcase their craftsmanship and attention to detail.
Frequently Asked Questions
What Is Fluting in Woodworking?
Fluting in woodworking refers to the process of creating long, rounded grooves or channels on the surface of wood. This decorative technique is often used to enhance the appearance of furniture, molding, or other wooden objects. Fluting can be done using hand tools like chisels or gouges, as well as with power tools such as routers.
What Is a Flute on a Router Bit?
A flute on a router bit is a long, spiral-shaped groove that runs along the length of the bit. These flutes help to remove wood chips and debris from the cutting area, allowing for smoother and more efficient routing operations.
The number and shape of the flutes on a router bit can vary depending on the specific application or cutting task.
What Is a Flute in Construction?
In construction, a flute typically refers to a shallow trough or channel that is incorporated into a material or structure for functional or decorative purposes. For example, in concrete construction, metal decking may have flutes to improve its load-carrying capacity while also providing space for utilities.
Additionally, in classical architecture, fluted columns are often used as decorative elements in building design. Whether serving an aesthetic or practical function, flutes play a versatile role in construction applications.
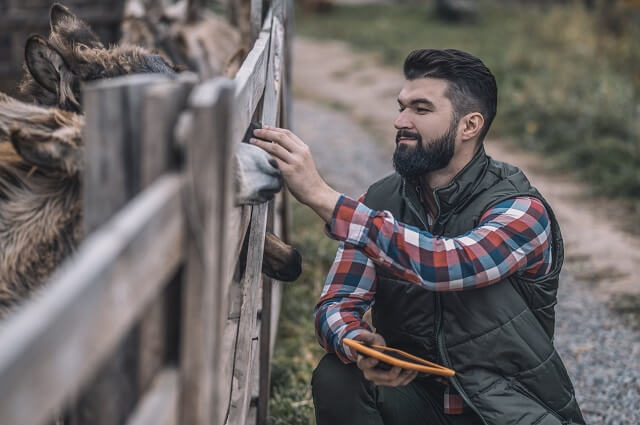
Hi everyone! I’m a woodworker and blogger, and this is my woodworking blog. In my blog, I share tips and tricks for woodworkers of all skill levels, as well as project ideas that you can try yourself.