There are a few different types of woodworking machines that can make clapboards, but the most common type is a shaper. A shaper is a machine that cuts profiles into the edge of a piece of wood. There are a few different types of shapers, but the most common type is a vertical shaper. A vertical shaper has a vertical cutting head that moves up and down. This type of shaper is the best type for making clapboards because the vertical cutting head ensures that the clapboards are cut evenly and with a consistent profile.
What Is Coping In Woodworking
?
Coping is a joinery technique where two pieces of wood are joined together at an angle. The technique is often used in making moldings, where two pieces of wood are joined together to form a corner. The coping saw is a tool often used in this type of joinery.
Coping is a very old joinery technique. The first moldings were probably made by copying the shapes of things that were found in nature. Over time, the technique has been refined and it is now possible to make very intricate shapes with it.
There are several ways to cope a joint. One way is to use a coping saw. The coping saw is a small, handheld saw with a thin blade that is curved. It is used to cut small, intricate shapes in wood.
Another way to cope a joint is to use a chisel. A chisel is a tool that is used to cut wood. It has a sharp blade that is attached to a handle. Chisels are often used to carve wood.
A third way to cope a joint is to use a router. A router is a tool that is used to carve wood. It has a sharp blade that is attached to a motor. Routers are often used to create intricate shapes in wood.
The Big Book Of Weekend Woodworking
Woodworking is a popular hobby enjoyed by many people. It is a great way to relax and get away from the stresses of everyday life. Woodworking can also be a great way to spend time with family and friends. When you’re woodworking, you can create all sorts of things, from small projects, like birdhouses and napkin holders, to larger projects, like tables and chairs.
If you’re new to woodworking, or if you’re looking for a new project to try, why not try building a bookcase? Bookcases are a great way to show off your woodworking skills, and they can also be a great addition to any room in your home. In this article, we’ll show you how to build a bookcase that’s both sturdy and stylish.
The first step in building a bookcase is to gather the materials you’ll need. For this project, you’ll need a piece of plywood, a sheet of MDF, a few pieces of lumber, a drill, a jigsaw, a saw, and some screws. You’ll also need some wood glue, a hammer, a screwdriver, and a tape measure.
Once you have all of the materials, you’ll need to measure and cut the plywood and the MDF. The plywood will be the back and bottom of the bookcase, and the MDF will be the front. The plywood should be cut to the same size as the MDF.
Next, you’ll need to cut the lumber. The lumber will be used to create the frame of the bookcase. The frame should be cut to the same size as the plywood and the MDF.
Once the lumber is cut, you can start assembling the bookcase. Start by gluing and screwing the frame together. Once the frame is assembled, you can attach the plywood and the MDF to the frame. Be sure to use plenty of wood glue and screws to ensure that the bookcase is sturdy.
Once the bookcase is assembled, you can start decorating it. You can paint it, or you can cover it with a piece of fabric. You can also add some decorative trim, or you can add some shelves.
If you’re looking for a new project to try, why not try building a bookcase? Bookcases are a great way to show off your woodworking skills, and they can also be a great addition to any room in your home. In this article, we’ll show you how to build a bookcase that’s both sturdy and stylish.
Woodworking Logo Template
This woodworking logo template is perfect for any business or individual that works with wood. The simple, clean design is perfect for a modern look, and the wood grain texture gives it a touch of authenticity. The template is easy to edit and customize, and it’s available in vector format for high quality printing.
How To Sharpen A Woodworking Knife On A Whetstone
The first step in sharpening a woodworking knife is to find a suitable whetstone. The whetstone should be at least as long as the blade to be sharpened, and it should be flat and smooth.
The next step is to soak the whetstone in water for at least 10 minutes.
Once the whetstone is wet, the knife should be placed on the stone at a 10-degree angle. The knife should be moved from the heel to the point, and then back to the heel. This should be repeated 10 times.
The knife should then be moved to a 20-degree angle, and the process repeated 10 times.
The knife should then be moved to a 30-degree angle, and the process repeated 10 times.
The knife should then be moved to a 40-degree angle, and the process repeated 10 times.
The knife should then be moved to a 50-degree angle, and the process repeated 10 times.
The knife should then be moved to a 60-degree angle, and the process repeated 10 times.
The knife should then be moved to a 70-degree angle, and the process repeated 10 times.
The knife should then be moved to a 80-degree angle, and the process repeated 10 times.
The knife should then be moved to a 90-degree angle, and the process repeated 10 times.
The knife should then be moved back to the 10-degree angle, and the process repeated 10 times.
The knife should then be moved to the 20-degree angle, and the process repeated 10 times.
The knife should then be moved to the 30-degree angle, and the process repeated 10 times.
The knife should then be moved to the 40-degree angle, and the process repeated 10 times.
The knife should then be moved to the 50-degree angle, and the process repeated 10 times.
The knife should then be moved to the 60-degree angle, and the process repeated 10 times.
The knife should then be moved to the 70-degree angle, and the process repeated 10 times.
The knife should then be moved to the 80-degree angle, and the process repeated 10 times.
The knife should then be moved to the 90-degree angle, and the process repeated 10 times.
After the knife has been sharpened at all of the angles, it should be honed on a leather strop.
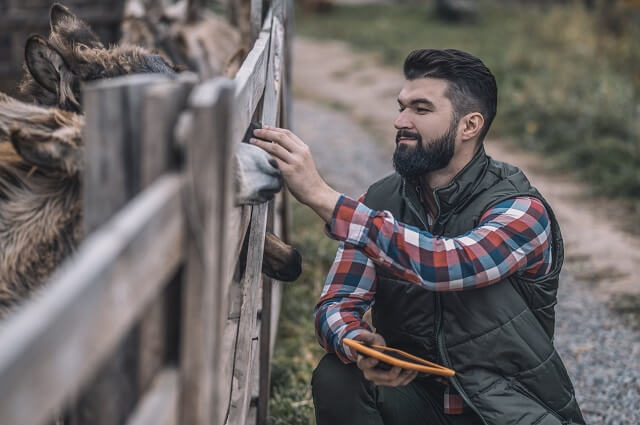
Hi everyone! I’m a woodworker and blogger, and this is my woodworking blog. In my blog, I share tips and tricks for woodworkers of all skill levels, as well as project ideas that you can try yourself.