What type of business is woodworking for OSHA? Woodworking businesses are subject to the regulations and standards set by the Occupational Safety and Health Administration (OSHA).
Understanding OSHA and its relevance to woodworking businesses is crucial for ensuring a safe and compliant work environment. In this article, we will explore the specific OSHA standards and regulations that apply to woodworking businesses, the different types of woodworking businesses and their classification under OSHA, as well as the importance of workplace safety and health requirements in this industry.
When it comes to OSHA standards and regulations for woodworking businesses, there are specific guidelines in place to address the unique hazards associated with this industry. From machine guarding requirements to ventilation standards, OSHA sets forth rules that aim to protect employees from workplace injuries and illnesses. Additionally, different types of woodworking businesses may have varying OSHA classifications based on their operations, which we will delve into further in this article.
Workplace safety and health requirements for woodworking businesses go beyond just following OSHA regulations; they are essential for protecting workers from potential hazards. By understanding common risks in woodworking businesses according to OSHA, employers can take proactive measures to create a safe working environment. This includes providing proper training, implementing safety protocols, and ensuring equipment maintenance to prevent accidents.
OSHA Standards and Regulations for Woodworking Businesses
Woodworking businesses are subject to various standards and regulations set forth by the Occupational Safety and Health Administration (OSHA). These regulations are in place to ensure the safety and health of workers in the woodworking industry. OSHA has specific standards that address the unique hazards present in woodworking, including exposure to wood dust, noise, and machine hazards.
One of the key OSHA regulations that woodworking businesses must comply with is the OSHA Woodworking Machinery Standard (29 CFR 1910.213). This standard outlines requirements for the safe operation of woodworking equipment, including saws, planers, routers, and sanders. It also specifies guarding requirements to protect workers from coming into contact with hazardous machine parts.
In addition to machinery safety standards, OSHA also requires woodworking businesses to address other safety and health concerns such as wood dust exposure. Wood dust can cause respiratory issues and combustible dust explosions if not properly controlled. OSHA’s combustible dust standard (29 CFR 1910.307) applies to woodworking facilities where wood dust is generated during manufacturing processes.
Another important aspect of OSHA regulations for woodworking businesses is the requirement for conducting regular hazard assessments and implementing appropriate control measures. This includes providing personal protective equipment (PPE) such as respirators, hearing protection, and safety goggles to employees who may be exposed to workplace hazards. Compliance with these regulations is crucial for protecting the wellbeing of workers in the woodworking industry.
OSHA Standard | Description |
---|---|
29 CFR 1910.213 | Addresses safe operation of woodworking machinery |
29 CFR 1910.307 | Applies to facilities with combustible wood dust |
Types of Woodworking Businesses and Their OSHA Classification
Woodworking businesses cover a wide range of activities, from small artisanal workshops to large-scale manufacturing plants. Each of these different types of woodworking businesses may fall under different OSHA classifications based on their size and the specific operations they undertake. Here are the main types of woodworking businesses and how they are classified by OSHA:
Types of Woodworking Businesses:
– Artisanal Woodworking Shops: These are small, independent workshops where craftsmen produce handmade furniture, cabinets, and other wood products. They may have only a few employees or be operated solely by the owner.
– Woodworking Manufacturing Plants: These larger facilities mass-produce wood products such as doors, windows, and furniture. They typically employ a larger workforce and may have more complex machinery and equipment.
– Carpentry and Construction Companies: These businesses focus on carpentry work in construction, including framing, cabinetry installation, and finishing work.
OSHA Classification for Woodworking Businesses:
1. Small Artisanal Workshops: These smaller woodworking businesses may fall under the OSHA classification for “low-hazard industries” due to their limited number of employees and lower risk factors compared to larger manufacturing operations.
2. Woodworking Manufacturing Plants: As larger industrial facilities with more machinery and employees, these businesses are likely categorized under OSHA’s “high-hazard industry” classification.
3. Carpentry and Construction Companies: Due to the nature of their work in construction sites with various hazards, these companies also fall under OSHA’s “high-hazard industry” classification.
It is important for woodworking business owners to understand how their operations are classified by OSHA in order to ensure compliance with the respective safety standards and regulations. By knowing their OSHA classification, woodworking businesses can proactively address workplace safety and health requirements while minimizing potential risks for violations and consequences arising from non-compliance with OSHA regulations.
Workplace Safety and Health Requirements for Woodworking Businesses
Understanding OSHA Standards for Woodworking Businesses
Woodworking businesses are subject to specific workplace safety and health requirements outlined by the Occupational Safety and Health Administration (OSHA). It is essential for woodworking businesses to understand the OSHA standards applicable to their operations to ensure compliance and maintain a safe working environment for employees. OSHA standards cover various aspects of woodworking, including equipment safety, ventilation, noise exposure, and handling of hazardous materials.
Equipment Safety and Maintenance
One of the key OSHA standards for woodworking businesses revolves around equipment safety and maintenance. Employers are responsible for ensuring that all machinery and tools are properly maintained, guarded, and used with the appropriate protective equipment. Additionally, regular inspections should be conducted to identify any potential hazards or defects in equipment that could compromise worker safety.
Hazardous Materials Handling
Woodworking businesses often involve the use of hazardous materials such as adhesives, solvents, and finishes. OSHA regulations require employers to implement suitable control measures to minimize employee exposure to these substances. This may include providing training on safe handling practices, ensuring proper storage and labeling of chemicals, and maintaining adequate ventilation systems in areas where hazardous materials are used.
By adhering to these OSHA standards for workplace safety and health requirements, woodworking businesses can protect their employees from potential harm while also avoiding costly penalties for non-compliance with regulations. Understanding the specific guidelines set forth by OSHA is crucial for maintaining a safe work environment within the woodworking industry.
Common Hazards and Risks in Woodworking Businesses According to OSHA
Woodworking businesses, like any other industry, pose unique hazards and risks that need to be carefully managed in order to maintain a safe working environment for employees. According to OSHA, there are several common hazards and risks that woodworking businesses should be aware of and take proactive measures to address. These include:
- Exposure to wood dust: Wood dust can pose serious health risks when inhaled, including respiratory issues and allergic reactions. OSHA requires woodworking businesses to implement dust control measures such as ventilation systems and personal protective equipment to minimize exposure.
- Machinery hazards: Woodworking businesses often use powerful machinery such as saws, planers, and routers which can cause serious injuries if not used properly. OSHA mandates that safety guards are in place, and employees receive proper training on using these machines safely.
- Hearing protection: The noise levels in woodworking shops can exceed safe limits, leading to potential hearing damage for employees. OSHA requires woodworking businesses to provide hearing protection devices such as earplugs or earmuffs, as well as conducting regular noise level monitoring.
Proper understanding and management of these hazards are crucial for woodworking businesses to maintain a safe work environment while complying with OSHA regulations.
Overall Workplace Safety Requirements for Woodworking Businesses
In addition to managing specific hazards, woodworking businesses must also comply with general workplace safety requirements set forth by OSHA. These include:
- Maintaining a clean and organized workspace to prevent slips, trips, and falls
- Providing adequate lighting for visibility
- Performing regular maintenance on equipment to ensure safe functioning
By adhering to these guidelines alongside the specific standards for woodworking industries, companies can ensure the safety and well-being of their workforce while remaining compliant with OSHA regulations.
OSHA Training and Compliance for Woodworking Employees
Required OSHA Training
According to OSHA regulations, woodworking employees need to undergo training on the proper use of equipment, handling of hazardous materials, and recognizing potential workplace hazards. This training should also include education on emergency procedures and first aid.
Compliance Standards
Woodworking employees must comply with OSHA standards by following safety protocols, utilizing personal protective equipment (PPE), and reporting any unsafe conditions or incidents. Compliance with OSHA standards not only ensures the safety of the employees but also prevents potential violations and penalties for the woodworking business.
Continual Education and Awareness
It is crucial for woodworking businesses to continually educate their employees about OSHA regulations through workshops, seminars, and regular safety meetings. Heightened awareness of potential risks in the woodworking environment can help prevent accidents and maintain a safe workplace. By fostering a culture of safety and compliance, woodworking businesses can mitigate the likelihood of OSHA violations.
Overall, it is imperative for woodworking businesses to prioritize OSHA training and compliance for their employees to uphold workplace safety standards. Ensuring that woodworking employees are knowledgeable about OSHA regulations and compliant with safety protocols is essential in preventing hazards and maintaining a secure work environment.
Importance of OSHA Compliance in Woodworking Businesses
Woodworking businesses are subject to specific regulations and standards set by the Occupational Safety and Health Administration (OSHA) to ensure the safety and health of employees. It is important for woodworking businesses to comply with OSHA guidelines to protect workers from potential hazards, minimize workplace accidents, and avoid costly penalties or legal consequences. By adhering to OSHA regulations, woodworking businesses can create a safer working environment and mitigate the risks associated with operating in this industry.
One of the key reasons for OSHA compliance in woodworking businesses is the prevention of work-related injuries and illnesses. Woodworking involves various processes and equipment that can pose significant health and safety risks if not properly managed. Compliance with OSHA standards helps woodworking businesses identify these risks, implement appropriate safety measures, and provide employees with necessary training to prevent accidents and protect their well-being.
In addition, OSHA compliance also enhances the overall reputation and credibility of woodworking businesses. Demonstrating a commitment to workplace safety through adherence to OSHA regulations can have a positive impact on customer confidence, employee morale, and relationships with regulatory authorities. This can ultimately contribute to the long-term success and sustainability of woodworking businesses within the industry.
Reasons for OSHA Compliance | Benefits |
---|---|
Prevention of work-related injuries and illnesses | Safe working environment, reduced healthcare costs |
Enhanced reputation and credibility | Customer confidence, employee morale, business sustainability |
Case Studies of Woodworking Businesses With OSHA Violations and Consequences
Woodworking businesses, like any other industry, are subject to OSHA regulations to ensure the safety and health of their employees. Failure to comply with these regulations can result in serious consequences for the business. One type of woodworking business that has faced OSHA violations and consequences is a small custom furniture shop in Indiana.
In this case, the business was found to have numerous violations, including inadequate machine guarding, lack of respiratory protection for employees, and failure to provide proper training on woodworking machinery. As a result, the business faced significant fines and had to make substantial changes to their operations to come into compliance with OSHA standards.
Another example is a mid-sized cabinet manufacturing company in California that experienced OSHA violations related to hazardous chemical exposure. The company failed to implement an effective hazard communication program and did not properly train employees on how to handle these chemicals safely. This resulted in fines and the requirement to reevaluate their chemical handling processes and improve employee training.
These case studies illustrate the serious implications of failing to comply with OSHA regulations within woodworking businesses. It is clear that OSHA takes workplace safety and health very seriously, and woodworking businesses must prioritize compliance to avoid costly fines and penalties.
Conclusion
In conclusion, OSHA regulations are of utmost importance for woodworking businesses to ensure the safety and health of their employees. Woodworking businesses, whether small-scale or large-scale, must comply with OSHA standards and regulations to create a safe working environment.
The OSHA classification for different types of woodworking businesses will determine the specific requirements they need to meet, such as providing proper ventilation in facilities where wood dust is generated, providing appropriate personal protective equipment, and implementing machine guarding to prevent injuries.
It is crucial for woodworking businesses to prioritize workplace safety and health by adhering to OSHA regulations. This not only ensures the well-being of employees but also helps in preventing costly violations and penalties. By providing OSHA training and compliance programs for their employees, woodworking businesses can minimize risks, hazards, and potential accidents in the workplace. Additionally, maintaining OSHA compliance can improve the reputation of woodworking businesses and build trust with clients and customers who value safety standards.
In summary, woodworking businesses should be fully aware of the OSHA standards pertaining to their industry in order to mitigate risks and ensure a safe working environment. Compliance with OSHA regulations not only protects workers from potential harm but also strengthens the overall operations and reputation of woodworking businesses within the industry.
Frequently Asked Questions
What Type of Business Is OSHA?
OSHA, which stands for Occupational Safety and Health Administration, is a regulatory agency within the United States Department of Labor. It is responsible for establishing and enforcing workplace safety and health regulations to ensure that workers are provided with safe and healthy working conditions.
What Does OSHA Stand for in Woodworking?
In woodworking, OSHA stands for Occupational Safety and Health Administration, just as it does in all other industries. In the woodworking industry, OSHA regulations and standards specifically focus on safeguarding workers from hazards such as sawdust exposure, machine guarding, handling of wood materials, and respiratory protection.
What Industries Fall Under OSHA?
OSHA’s jurisdiction covers a wide range of industries including construction, manufacturing, agriculture, healthcare, maritime operations, and more. Essentially, any business or industry that employs workers within the United States falls under the purview of OSHA regulations. From office environments to heavy industrial settings, OSHA’s regulations are designed to protect workers from a variety of occupational hazards and risks.
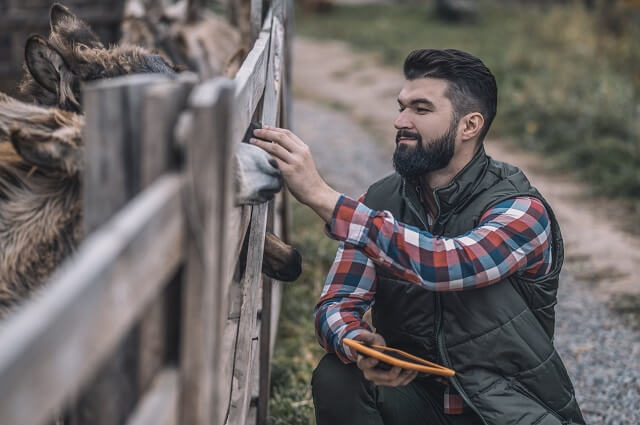
Hi everyone! I’m a woodworker and blogger, and this is my woodworking blog. In my blog, I share tips and tricks for woodworkers of all skill levels, as well as project ideas that you can try yourself.