Woodworking is a crucial aspect of various industrial operations, encompassing the creation, design, and production of wood-based products and materials. The equipment and tools utilized in woodworking facilitate the shaping, carving, and assembly of wood to meet specific industrial needs. In this article, we will delve into the requirements for industrial spaces that can accommodate woodworking activities.
Woodworking involves the use of various tools such as saws, routers, planers, and sanders to transform raw wood into finished products. Such activities require suitable industrial spaces equipped with the necessary layout, ventilation systems, and power sources to ensure efficient operations. Understanding these requirements is essential when considering industrial spaces for woodworking activities.
When looking for an industrial space suitable for woodworking, one must take into account the size and layout requirements for accommodating machinery and work areas. Additionally, proper ventilation and dust collection systems are imperative to maintain air quality and ensure safety within the workspace. Furthermore, a sufficient electrical capacity is needed to power woodworking machinery effectively.
It is important to recognize the crucial role that woodworking plays in diverse industrial settings. Whether in manufacturing facilities or warehouse spaces, finding an industrial space conducive to woodworking requires careful consideration of various factors such as zoning regulations, amenities available, location considerations, budgeting costs, as well as finding the right property through real estate agents or specialists in industrial properties.
Industrial Space Requirements for Woodworking
When it comes to setting up a woodworking operation in an industrial space, there are several important requirements to consider. These requirements include the size and layout of the space, ventilation and dust collection needs, as well as electrical and power requirements for woodworking machinery. Below are some essential factors to take into account:
- Size and Layout Requirements: Woodworking typically requires ample space for workstations, storage of raw materials and finished products, as well as maneuvering room for large machinery. A spacious layout with designated work areas is essential to ensure efficient and safe woodworking operations.
- Ventilation and Dust Collection Needs: Woodworking activities generate a significant amount of sawdust and wood particles, which can pose health hazards if not properly managed. Industrial spaces used for woodworking must have adequate ventilation systems and dust collection equipment in place to maintain air quality and protect workers from respiratory issues.
- Electrical and Power Requirements: Woodworking machinery such as table saws, planers, sanders, and routers require substantial electrical power to operate effectively. Therefore, industrial spaces intended for woodworking must have the necessary electrical infrastructure to support the simultaneous use of multiple woodworking machines.
Considering these requirements is crucial when searching for suitable industrial spaces that can accommodate woodworking activities. Without meeting these basic needs, it may be challenging to establish a functional woodworking operation within an industrial setting.
Zoning and Regulatory Considerations
When considering industrial spaces for woodworking, it is crucial to understand the zoning laws and regulations that govern such activities. Zoning laws dictate the types of activities that are allowed in specific areas, and woodworking may be subject to certain restrictions or special permits. It’s important to research local zoning regulations to ensure that the chosen industrial space is zoned appropriately for woodworking activities.
In addition to zoning considerations, environmental regulations and permits may also apply to woodworking in industrial spaces. Woodworking can produce dust, emissions, and waste that must comply with environmental standards. Obtaining the necessary permits and adhering to environmental regulations are essential for operating a woodworking business in an industrial setting.
Furthermore, safety and health regulations for woodworking in industrial spaces must be carefully observed. Occupational safety guidelines, fire codes, and building regulations may have specific requirements for woodworking operations. It is vital to ensure compliance with these regulations to create a safe working environment for employees and protect against potential liabilities.
Zoning Considerations | Regulatory Permits |
---|---|
Check local zoning laws | Obtain necessary environmental permits |
Understand zoning restrictions | Adhere to environmental standards |
Ensure proper zoning for woodworking activities | Compliance with regulatory requirements |
Types of Industrial Spaces Suitable for Woodworking
Woodworking requires a specific type of industrial space that can accommodate the equipment, tools, and processes involved in this craft. When considering the suitable types of industrial spaces for woodworking, it is essential to look for features that can support efficient operations and ensure the safety of workers. Here are some types of industrial spaces that are well-suited for woodworking:
- Warehouse spaces with high ceilings and open floor plans: Warehouses provide ample space for woodworking activities and allow for the movement of large pieces of lumber and finished products. The high ceilings are ideal for using tall machinery and storing materials vertically. Open floor plans also facilitate workflow and allow for the organization of workstations.
- Manufacturing facilities with designated work areas: Manufacturing facilities often have designated areas for different types of production processes, making it easier to set up woodworking stations without disrupting other operations. These facilities may also have specialized infrastructure, such as power outlets and dust collection systems, to support woodworking activities.
- Industrial parks with shared woodworking amenities: Some industrial parks offer shared amenities specifically tailored to support woodworking activities. These may include communal dust collection systems, tool libraries, or designated woodworking zones within the park.
When considering industrial spaces for woodworking it’s important to consider factors such as ventilation systems, layout requirements and local zoning laws and regulations. Each type of facility comes with its own set of benefits and considerations, so it is important to evaluate each option carefully before making a decision.
Ultimately, the type of industrial space suitable for woodworking will depend on the specific needs of a woodworker or woodworking business. Whether looking at warehouse spaces with high ceilings or evaluating options within an industrial park with shared amenities, it’s crucial to consider factors such as layout requirements, power needs ventilation etc.
Amenities and Features to Look for in Industrial Spaces
When looking for industrial spaces suitable for woodworking, there are certain amenities and features that can enhance the functionality and efficiency of the woodworking activities. These amenities play a crucial role in ensuring that the industrial space can meet the specific needs of woodworking operations.
Loading Bays and Easy Access for Material Delivery
Industrial spaces designed for woodworking should have adequate loading bays and easy access for material delivery. This allows for seamless transportation of raw materials, lumber, and other supplies needed for woodworking projects. Proximity to major transportation routes such as highways or ports can also make material delivery more convenient.
Office Space for Administrative Work and Planning
In addition to the actual workspace for woodworking activities, having dedicated office space within the industrial facility is important. This area can be used for administrative work, project planning, design consultations, client meetings, and other non-production related tasks. Having an integrated office space within the industrial facility fosters better communication and coordination between different aspects of the woodworking operation.
Built-in Storage for Lumber and Finished Products
Adequate storage space is essential in an industrial facility where woodworking activities take place. Specifically, having built-in storage areas for lumber, wood scraps, finished products, and other woodworking materials helps to keep the workspace organized and efficient. Proper storage also contributes to workplace safety by minimizing clutter and potential hazards.
In summary, when searching for industrial spaces suitable for woodworking, it’s important to consider amenities such as loading bays, office space, and built-in storage to support a smooth workflow in the facility. These features contribute to the overall functionality of the industrial space and can significantly impact the effectiveness of woodworking operations.
Location Considerations for Woodworking Industrial Spaces
When considering industrial spaces for woodworking, location is a crucial factor that can impact the success of your operations. Whether you are a small woodworking shop or a large-scale manufacturing facility, the location of your industrial space can significantly influence your access to suppliers, customers, and the local woodworking community. Proximity to these key elements can streamline production processes and contribute to overall business efficiency.
Proximity to Suppliers and Customers
One important consideration when choosing an industrial space for woodworking is its proximity to lumber suppliers, hardware stores, and other essential materials. Being close to these suppliers can reduce transportation costs and lead times for obtaining necessary items for your woodworking projects. Additionally, being located near potential customers or distributors can enhance the efficiency of product delivery and foster stronger relationships within the industry.
Accessibility for Transportation and Shipping
Another important aspect of location considerations for woodworking industrial spaces is accessibility for transportation and shipping. The ease of transporting raw materials in and finished products out of your facility is essential for maintaining smooth operations. Consider factors such as proximity to major highways, access to loading docks, and the availability of trucking services when evaluating potential locations for your woodworking business.
Understanding the Local Woodworking Industry and Community
Finally, when selecting an industrial space for woodworking, it’s crucial to understand the local woodworking industry and community in the area. Being part of a vibrant woodworking ecosystem with access to skilled labor, specialized services, and networking opportunities can be advantageous for businesses in this sector. Researching the presence of other woodworking businesses, trade associations, and support organizations in a given location can provide valuable insights into whether it’s a suitable environment for your woodworking operations.
Considering these location considerations when searching for industrial spaces can help ensure that you find a suitable environment that supports the needs of your woodworking business. By prioritizing proximity to suppliers and customers, accessibility for transportation and shipping, as well as understanding the local woodworking industry community; you can set your business up for success in its chosen location.
Budgeting and Cost Considerations
Industrial woodworking spaces come with their own set of budgeting and cost considerations that must be taken into account. When considering what type of industrial space can accept woodworking, it’s important to factor in the various expenses involved in setting up and operating a woodworking facility.
First and foremost, one of the major cost considerations is the rent or lease prices for industrial spaces. The size and location of the space will greatly impact these costs, as larger spaces and those in high-demand areas may command higher prices. It’s crucial to carefully analyze the budget to ensure that the chosen industrial space for woodworking is financially viable.
In addition to rent or lease prices, potential tenants must also factor in utility costs for running woodworking machinery. Woodworking equipment often requires significant electrical power to operate, which can contribute to higher utility bills. It is important to assess these costs and budget accordingly to avoid any financial strain on the woodworking operation.
Furthermore, when exploring different options for industrial spaces suitable for woodworking, potential cost savings should be considered. Shared woodworking spaces or co-working facilities may offer more affordable alternatives compared to standalone industrial properties. Evaluating these cost-saving opportunities can help in making a financially sound decision when selecting an industrial space for woodworking activities.
Considering all of these budgeting and cost considerations is essential when searching for the right industrial space for woodworking. By carefully strategizing and planning for expenses related to rent or lease prices, utility costs, and potential cost-saving opportunities, businesses can make informed decisions that align with their financial goals while still meeting all their woodworking needs.
Finding the Right Industrial Space for Woodworking
In conclusion, finding the right industrial space for woodworking requires a comprehensive understanding of the specific needs and requirements of this type of activity. Woodworking in industrial spaces entails the use of various equipment and tools, and it plays a crucial role in many manufacturing processes. As such, the industrial space must meet certain criteria to accommodate woodworking activities effectively.
When considering the types of industrial spaces suitable for woodworking, it is important to prioritize features such as high ceilings, open floor plans, and designated work areas. Additionally, amenities like loading bays for material delivery, office space for administrative work, and built-in storage for lumber and finished products are essential for a functional woodworking space. Industrial parks with shared woodworking amenities may also present an attractive option for businesses looking to minimize costs while still accessing necessary facilities.
Furthermore, potential woodworkers must be mindful of budgeting and cost considerations when seeking industrial spaces. Rent and lease prices should be weighed against utility costs for running woodworking machinery as well as any potential cost savings associated with shared woodworking spaces or co-working facilities.
Engaging with a real estate agent or industrial property specialist can help in finding the most suitable space, touring potential options, and negotiating favorable lease terms for woodworking activities. Ultimately, by being thorough in their search process and considering all relevant factors, businesses can find the right industrial space that meets their specific needs for woodworking.
Frequently Asked Questions
Can I Run a Woodworking Business From My Garage?
Running a woodworking business from your garage is definitely possible as long as you have enough space, proper tools, and ventilation. However, it’s crucial to check local regulations and obtain any necessary permits to operate the business legally.
Can I Run a Woodworking Business From Home?
Yes, it is possible to run a woodworking business from home, especially if you have a dedicated workspace like a garage or a small workshop. With the right tools and equipment, you can produce quality wood products and manage your business operations from the comfort of your home.
Do Woodworkers Make Good Money?
Woodworkers have the potential to make good money, especially if they are skilled and produce high-quality products. The income level can vary depending on factors such as expertise, craftsmanship, market demand, and the ability to effectively market and sell their products. With dedication and hard work, woodworkers can certainly earn a decent income.
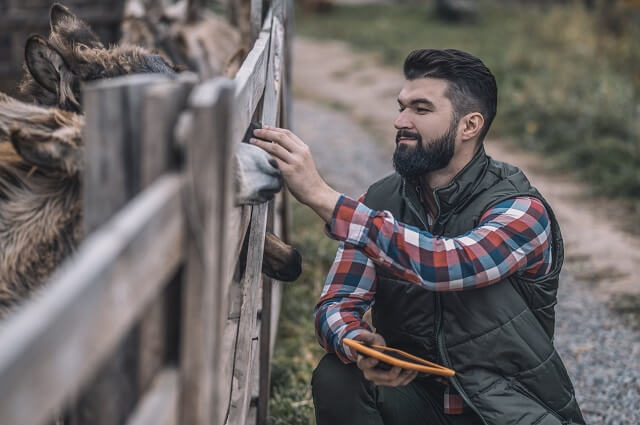
Hi everyone! I’m a woodworker and blogger, and this is my woodworking blog. In my blog, I share tips and tricks for woodworkers of all skill levels, as well as project ideas that you can try yourself.