Introduction to Chest Woodworking
Woodworking is a wonderful and versatile craft to pursue. Chest woodworking specifically can open up a wide and exciting range of tools, techniques, and possibilities for beautiful storage pieces or signs of your skill within the home. The experience of woodworking can provide you with a great creative outlet to make objects by hand that have their own unique story and purpose.
When pursuing chest woodworking projects, you will learn about specific tools and techniques pertaining to carpentry, such as basic joinery techniques like cutting dovetails or mortise & tenon joints. You will also practice sanding and finish techniques such as staining, varnishing or lacquering in order to bring out the natural beauty of the wood used in your project.
One popular example of chest woodworking involves creating an heirloom blanket box ” a type of chest used for storing blankets/linens that has kept its traditional aesthetic over centuries while also expressing individual style with its materials and construction details. Additionally, tackling a small outdoor storage chest helps build understanding of case construction while also being put to use almost immediately after completion. These two examples demonstrate how rewarding it can be to design thoughtful pieces that combine utility with beauty, turning everyday objects into something extra special.
Getting Started with Chest Woodworking
Woodworking is a very rewarding art form, and building a chest can be among the most fulfilling project of any woodworker. The right tools, materials, and having a basic understanding of woodworking terms can help you produce an unbeatable chest that you’ll be proud of.
Picking the right woodworking project is all about finding something that suits your level of expertise and knowledge. For those just starting out, a basic toolbox or blanket chest may be the perfect starter project. Tools such as chisels, saws, planes, hammers and braces are needed to complete this type of box and should all be considered when shopping for supplies. It’s also important to select only the highest quality lumber for optimal performance; avoid checking boards (which contain small cracks) at all costs as they are prone to splintering with use.
For more experienced projects, a joinery-based piece like a settee or chair may be more suitable since it requires more precision cuts and measurements. This type of furniture usually involves complicated joinery techniques such as mortise-and-tenon or dovetail joints which will require quality saw blades and other specialized tools in order to complete correctly.
Regardless of which type of chest woodworking project you choose, it’s always advisable to have an understanding of some common woodworking terms before getting started; this ensures one can properly read plans and follow instructions while being able to comprehend what they’re doing along the way. Below is a brief overview some commonly used terms:
• Rip ” Cutting parallel to the grain in order to reduce material length
• Crosscut – Cutting perpendicular (90 degree angle) to grain in order reduce material width
• Dado – A groove cut into the material created by multiple passes with a circular saw blade
• Dovetail ” A skilled technique used for joining two pieces together primarily used in cabinetry applications
• Rough Cut ” Where secondary actions such as smoothing don’t need prior trimming
Step-By-Step Guide to Building a Chest
Building a chest can provide a rewarding challenge for both amateur and seasoned woodworker alike. Before one begins, it is essential to take the time to plan and accurately measure the design, as well as select the materials that best suit your project needs. Once all of this planning is taken care of, follow these steps to have your chest in no time:
1. Cut out pieces to be assembled with a saw or jigsaw. Measure twice and cut once!
2. Assemble the headboard by fastening two vertical posts together using mortise and tenon construction or pocket hole screws, connecting them at the top with a crosspiece.
3. Construct bottom rail supports underneath headboard and secure with glue or nails.
4. Make sure your portioned compartments are square”this will help with installation of cleats later on!
5. Cut partitions using your saw or jigsaw to fit into place in between the upright posts and attach securely with glue or nails if desired.
6. Install cleats onto sides of chest for drawer runners. Attach preferred type of drawer pulls for each drawer unit (bail pulls work best due to their sturdy construction).
7 . Finish off by applying desired protective finish such as lacquer, varnish, shellac, or paint””allowing adequate drying time between coats per manufacturer specifications!
8 . Celebrate your success in creating a beautiful piece of furniture from scratch!
By taking these steps through the process it does not need to be overly complicated; however, make sure to use extra precaution when dealing with sharp tools such as power saws and jigsaws so as not too injure yourself while building your masterpiece! It is also recommended that you look up video tutorials related specifically to any part of the build which may give added clarity on how things go together along every step of the way””keeping in mind that every project is different which means yours may require alternative methods than presented here depending on intricate details implemented early on in Preliminary Planning Stage! In addition to watching videos, ensure all power tools are connected properly and always wear appropriate safety equipment when operating machinery””being totally aware of what’s going around you at all times!
Finishing Your Chest Woodwork
Sanding
Start off by sanding the rough edges of your chest using a medium grit sandpaper. Move up to a higher grit like 400 to make sure the surface is as smooth as possible. You can use either an electric sander or do it by hand. Make sure you go in the same direction with each pass until all of the rough areas are gone.
Staining
Select the desired color of your stain and test it on a scrap piece of wood before applying it to your chest. Be careful when adding more layers to achieve a darker finish, as too many applications may result in an uneven surface. Make sure to give your chest ample time to dry between coats of stain. If you’re using an oil-based product, remember that they usually take longer than water-based stains.
Finishing Up
Once you’ve achieved the desired color and level of protection with your staining process, you can finish off by applying a top coat such as polyurethane, lacquer or varnish. Depending on what sort of look you’re going for, you can opt for either a glossy or matte finish. When applying sealants always move in the same direction over your wood with each pass and keep an eye out for any blotchy spots that require another layer of polyurethane or lacquer for even coverage!
Preserving & Protecting Your Work
To keep your chest looking like new throughout its lifetime, apply a coat of wax every couple months to refresh and further protect its surface from day-to-day wear and tear. Additionally ” if periodically used near direct sources of heat ” be mindful that seasonal cracking is normal due to fluctuations in humidity levels inside and outside during certain times; however, this can create uneven surfaces if left unattended so be sure check it regularly to ensure everything looks good! Finally ” while sometimes unavoidable – try your best not to place wet items directly onto your work surface as this could lead to discoloration or warping if left untouched for too long which affects how water permeates into unfinished wood causing damage overtime – moisturize thoroughly instead!
Creative Ideas for Chest Woodworking
A chest woodworking project can be as unique and creative as you’d like! Consider using different types of woods, from upcycled materials to hardwood, to create an eye-catching design. If you’re looking to make a statement, try detailed patterns such as fret work or inlays for the panels of the chest. Alternatively, use a variety of stains and paint combinations to add attractive color accents.
For added embellishments, think about carving and etching designs directly into the wood or adding detailing with rope molding, scrolls, and corbels. An interior design element could include nesting drawers or additional storage solutions with fold-out compartments.
Finally, don’t forget that knobs and handles are the perfect finishing touch for a custom chest combination. Choose complementary pulls that fit your style from wooden handles to steel hardware. With so many options available across hardware stores and online retailers today, it’s easy to find a look that fits your project’s theme be it classic farmhouse, modern industrial or traditional colonial style.
Safety Tips for Chest Woodworkers
Working with wood can be a great and rewarding experience, but it is important to keep safety in mind when woodworking. Before beginning any project involving woods, it is important to observe some basic safety measures.
1. Wear protective clothing and eye protection. Long pants and sleeves will help protect your skin from sharp edges and splinters, while safety glasses or goggles will protect your eyes from any flying dust or debris. When working with power tools, hearing protection should also be considered.
2. Keep your workspace clean and safe by keeping it free of clutter and properly storing tools away when not in use. This will not only help prevent accidents but will make it easier to locate items quickly when working on projects that require multiple tools.
3. Understand the capabilities of each tool before using them, as well as their limitations so they do not cause injury if they are used incorrectly or beyond their ability level. Ask questions before starting a new project if there is something you don’t understand.
4. Know what types of saws, blades, chisels and other tools appropriate for each type of wood you are working on and practice proper technique before attempting a complex task such as mortise-and-tenon joinery or carving turnings on a lathe.
5. Keep all saw blades sharp professionally sharpened so they cut cleanly instead of forcing the user to use extra pressure which can lead to kickback or breaks that cause injury
6. Make sure saws are properly guarded at all times with no missing parts or screws! And always unplug power tools when switching saw blades/bits etc..
7. Secure large pieces with clamps or other methods to prevent them from slipping while cutting them with a blade/bit
Fix any electrical issues immediately instead of risking an electrical shock due to faulty wiring!
Additional Resources for Woodworking Enthusiasts
Woodworking enthusiasts can explore a wide variety of resources to hone their craft, whether it’s for hobbies such as building furniture or a career-focused education in carpentry. Here are some links and suggested avenues to get you started:
1. Popular Woodworking Magazine – This magazine is a great resource which offers tips, product reviews, and guidance on everything from basic woodworking to advanced designs. It also offers access to an online community of fellow woodworkers.
2. Online Tutorials – There are countless online tutorials that dive into specific projects or techniques like making cutouts, learning specialized joinery techniques or training with power tools. A quick web search should yield numerous results offering a range of information surrounding specific topics.
3. Woodturning Clubs – Local woodturning clubs often provide educational meetings and classes about different turning techniques and offer advice for those beginning the craft. Understanding the fundamentals of lathe operation, cutting edge geometry and sharpening are integral aspects every beginner should be familiar with before picking up a piece of wood.
4. Public Libraries, Museums & Craft Stores – Libraries often have books about the history and science behind the craft, with helpful articles about all facets of woodwork from planers to dovetail joints; museums may have exhibits showing various tools used through time; and craft stores may offer classes that introduce essential equipment and techniques while also providing light courses in design aesthetics, art styles or professional care practices when finished pieces need display or loyal maintenance.
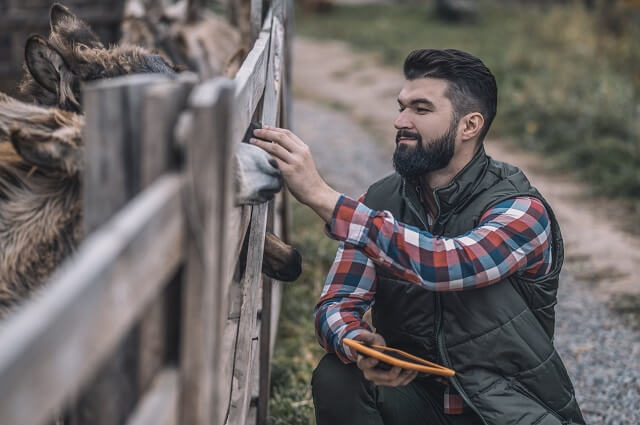
Hi everyone! I’m a woodworker and blogger, and this is my woodworking blog. In my blog, I share tips and tricks for woodworkers of all skill levels, as well as project ideas that you can try yourself.