Woodworking is a beloved DIY hobby that has captured the attention of both novices and experienced craftsmen for generations. The combination of creativity, precision, and the satisfaction of working with one’s hands makes woodworking a rewarding pursuit.
Among the many projects that can be undertaken in this field, making a wooden clock holds a special place. This article will delve into the world of woodworking clocks, exploring their history, materials used, essential tools and techniques required, as well as providing step-by-step instructions for constructing your very own clock.
Woodworking has seen a resurgence in recent years as people seek to reconnect with traditional craftsmanship and embrace the satisfaction of creating something unique. Whether you are an enthusiastic beginner or a seasoned woodworker looking for a new challenge, making a wooden clock is an excellent choice. Not only does it offer an opportunity to hone your skills and learn new techniques, but it also results in a functional piece of art that adds character to any space.
In this comprehensive guide, we will explore various aspects related to woodworking clocks. We’ll start by tracing their origins and evolution throughout history, highlighting iconic designs and famous makers. Next, we will delve into the types of wood commonly used in these clocks and how they impact the final product.
We’ll also cover the essential tools and techniques needed for crafting a woodworking clock, from cutting and shaping to sanding and finishing. So let’s dive into this fascinating world of woodworking clocks and embark on an enriching journey together.
History of Woodworking Clocks
Throughout history, wooden clocks have played a significant role as both functional timepieces and beautiful works of art. The history of woodworking clocks dates back to ancient civilizations, where the first mechanical devices for measuring time were created. Tracing the origins and evolution of wooden clocks offers fascinating insights into the craftsmanship and ingenuity of past generations.
One of the earliest known examples of a wooden clock is the chamber or table clock, which emerged in Europe during the late 13th century. These early clocks were typically made from oak or other readily available woods and featured simple mechanisms that relied on weights or springs to power the movement. As technology advanced, so did clockmaking techniques, leading to innovations such as striking mechanisms that signaled hours and even quarter-hour chimes.
The 17th century marked a period known as the Golden Age of Wooden Clocks, with craftsmanship reaching new heights. This era saw the emergence of renowned clockmakers like Peter Klockentien, who produced intricate wooden timepieces adorned with elaborate carvings and decorations. It was also during this time that English longcase or grandfather clocks gained popularity, featuring impressive wooden cases often made from mahogany or walnut.
Wooden clockmaking continued to evolve throughout the centuries, with various regions developing their unique styles and designs. In America, notable makers such as Eli Terry and Seth Thomas became synonymous with quality craftsmanship and timeless beauty in their creations. The same can be said for Black Forest cuckoo clocks from Germany, which have become iconic symbols of woodworking excellence.
Today, antique wooden clocks are highly sought after by collectors and enthusiasts alike. Their historical significance and skilled craftsmanship make them valuable pieces of art that continue to captivate admirers worldwide. Furthermore, contemporary artisans draw inspiration from these historic designs when creating their own unique woodworking clocks, blending traditional techniques with modern aesthetics.
Time Period | Key Developments | Famous Makers |
---|---|---|
13th Century | Emergence of chamber or table clocks | N/A |
17th Century | Golden Age of Wooden Clocks, invention of striking mechanisms, rise of grandfather clocks | Peter Klockentien, Eli Terry, Seth Thomas |
19th Century-present | Diverse regional styles and designs, development of modern woodworking techniques | N/A |
Types of Wood Used
Woodworking clocks can be crafted from a variety of different types of wood, each with its own unique characteristics and impact on the final product. The choice of wood used in a woodworking clock not only affects its appearance but also its durability, stability, and overall performance. Here are some commonly used types of wood in woodworking clocks:
- Hardwood: Hardwood is a popular choice for woodworking clocks due to its strength and durability. Woods like oak, mahogany, walnut, and cherry are often used for their beautiful grain patterns and ability to take on intricate detailing. Hardwoods provide a solid foundation for the structure of the clock and are known for their longevity.
- Softwood: Softwoods such as pine, cedar, and spruce are also utilized in woodworking clocks. While softer than hardwoods, they offer their own advantages such as being lightweight and easy to work with. Softwoods often give a more rustic or country-style aesthetic to the clock design.
- Exotic Wood: For those looking to create a truly unique woodworking clock, exotic woods can add an extraordinary touch. Woods like ebony, padauk, zebrawood, or purpleheart bring vibrant colors and striking grain patterns that make the clock stand out. However, these types of woods may be more expensive and harder to source.
The choice of wood ultimately depends on personal preference as well as factors such as budget and availability. It is important to consider the characteristics of different types of wood when selecting the material for a woodworking clock project. Each type has its own natural beauty that can enhance the overall design and style of the clock.
When working with wood for a clock project, it is essential to properly prepare and treat the wood before assembling it into the final product. This includes removing any dirt or debris from the surface, sealing or finishing the wood to protect it from moisture damage or warping over time.
Tools and Techniques
Woodworking clocks require a variety of tools and techniques to bring them to life. Whether you are a beginner or an experienced woodworker, having the right tools and knowing the proper techniques is essential for a successful project. Here are some of the essential tools and techniques that you will need for crafting a woodworking clock:
- Cutting: One of the most important aspects of woodworking is cutting the wood accurately. For this, you will need tools such as a table saw, miter saw, or scroll saw. These tools allow you to make precise cuts and achieve the desired dimensions for your clock parts.
- Shaping: Shaping the wooden components of a clock adds character and style to the overall design. Woodworkers often use chisels, rasps, files, and carving knives to shape intricate details on their clocks. It’s important to have good control over these tools to achieve smooth curves and crisp edges.
- Sanding: After cutting and shaping the pieces, sanding is necessary to smoothen any rough edges or surfaces. Sandpaper of varying grits is used in this process, starting with coarse grits for initial sanding and gradually moving towards finer grits for achieving a smooth finish.
- Finishing: The final touch that brings out the natural beauty of wood is the finish applied to it. You can use various finishes like varnish, lacquer, oil, or wax depending on your preferences. Applying a finish not only enhances the appearance but also protects the wood from moisture and wear over time.
In addition to these basic tools and techniques, there are other specialized instruments that may be required depending on your specific design choices. For example, if you plan on incorporating intricate inlays or marquetry into your clock, you would need additional tools such as routers or fret saws.
When starting a woodworking clock project, it is essential to familiarize yourself with these tools and techniques before diving in. Practice on scrap pieces of wood to develop your skills and gain confidence in using the tools effectively.
Design and Assembly
When embarking on a woodworking clock project, the design and assembly phase is where creativity truly comes into play. This is the stage where you can let your imagination run wild and create a clock that reflects your personal style and preferences. However, before diving into the design process, it’s important to consider several key factors that will not only determine the overall look of your clock but also its functionality.
One of the first considerations when planning your woodworking clock design is the size. Think about where you plan on placing the clock – will it be a focal point or more of a subtle addition to your home decor?
Take measurements of the space to ensure that your clock will fit perfectly without overwhelming or appearing too small in relation to its surroundings. Additionally, consider practical aspects such as whether there will be enough space for components like pendulums or other mechanisms.
Style is another crucial factor in designing a woodworking clock. Are you drawn to traditional designs with intricate carvings and ornate details? Or do you prefer a modern minimalist approach with clean lines and simple finishes? Take inspiration from existing clock designs or explore various architectural styles to find what resonates with you. Keeping in mind the overall aesthetic of your home’s interior can also help guide your decision-making process.
Functionality should not be overlooked when designing your woodworking clock. Consider its intended purpose – will it primarily serve as a timekeeping device or do you want additional features like chiming mechanisms or calendar dials? Think about whether you want your clock to have hour and minute hands only or if you’d like it to include second hands as well. These elements can greatly impact both the construction process and final appearance of your woodworking clock.
Once these key factors have been determined, it’s time to take pen to paper (or computer screen) and begin the design process. Sketch out different ideas, explore various shapes and proportions, and experiment with different wood types to achieve the desired effect.
Remember to consider factors such as balance, symmetry, and harmony of the overall design. It can also be helpful to create a prototype or mock-up using cardboard or other inexpensive materials to get a better sense of how your clock will look in three dimensions.
The design phase is an exciting opportunity for both beginners and woodworking enthusiasts to unleash their creativity and create a truly unique woodworking clock. By carefully considering factors such as size, style, and functionality, you can ensure that your final product not only meets your aesthetic preferences but also functions seamlessly as a timekeeping device. Once you have finalized your design, it’s time to move on to the next phase: step-by-step construction.
Step-by-Step Construction
Building a woodworking clock from scratch can be a fulfilling and rewarding project. This section will provide a comprehensive, easy-to-follow guide on the step-by-step construction process, including detailed photographs and instructions.
- Gathering Materials: The first step in building a woodworking clock is gathering all the necessary materials. This includes selecting the type of wood you want to use for the clock’s frame, dial, and pendulum. Additionally, you will need to gather tools such as a saw, chisel, drill press, and sandpaper to shape and assemble the components.
- Crafting the Frame: Begin by cutting the pieces for the clock frame according to your chosen design and dimensions. Use a saw to carefully cut out each piece, ensuring clean and precise edges. Next, use a chisel to remove any excess material or create intricate details on the frame. Sand down each piece to achieve a smooth surface.
- Constructing the Dial: Measure and cut out the dial from a contrasting wood species that complements your chosen frame wood. Use a drilling press to create holes for the hour marks and hands in the appropriate positions on the dial surface.
- Assembling Mechanism Components: Follow the instructions provided with your clock mechanism kit to properly install it onto the backside of your clock frame. Attach all necessary gears, hands, weights, and pendulum according to manufacturer guidelines.
- Finishing Touches: Apply a finish of your choice to protect and enhance the beauty of your wooden clock. Popular finishes for woodworking clocks include varnish or wax that highlight the natural color and grain patterns of the wood.
- Mounting and Displaying: Once your woodworking clock construction is complete, it’s time to mount it securely onto either a wall or place it on an appropriate stand for display purposes.
By following these step-by-step instructions accompanied by detailed photographs of each stage in construction, even beginners can successfully build their own woodworking clock and enjoy the satisfying experience of creating a functional and beautiful timepiece.
Tips and Troubleshooting
Choosing the Right Wood
When it comes to woodworking clocks, selecting the right type of wood is crucial for both aesthetics and functionality. Different woods have distinct characteristics that can affect the appearance, durability, and overall performance of the clock. For beginners, it is recommended to start with softer woods such as pine or poplar, which are easier to work with due to their lower density and less hardness. These types of wood are also more forgiving when mistakes occur during shaping or carving.
However, if you are looking for a more decorative and elegant clock, hardwoods like oak, cherry, or walnut are excellent choices. Hardwoods provide a beautiful natural grain pattern and have greater resistance to wear and tear over time. Keep in mind that each wood species has unique properties, so it’s essential to consider factors such as stability, color variations, and availability before making your selection.
Dealing with Joinery Challenges
Joinery refers to how different pieces of wood are connected together in a woodworking project. Building a wooden clock often involves intricate joinery techniques like dovetail joints or mortise and tenon joints. These joints can be challenging for beginners due to their precision requirements and complexity.
To overcome these challenges, take the time to practice on scrap pieces of wood before attempting them on your clock project. It’s also helpful to use clamps or specialized jigs to ensure accurate alignment during assembly. Additionally, using high-quality glues specifically formulated for woodworking will provide stronger bond strength and reduce the risk of joints failing over time.
Addressing Common Issues
While working on a woodworking clock project, it’s not uncommon to encounter certain issues that may require troubleshooting. One common problem is warping or twisting in the wood caused by changes in humidity or improper storage methods. To minimize this issue, make sure to acclimate your wood properly before starting your project by storing it in the same environment where your clock will be displayed.
Another common issue is tear-out, which occurs when the wood fibers splinter or break unevenly during cutting or shaping. To prevent tear-out, ensure that your cutting tools are sharp and properly maintained. Take precautionary measures such as using a backing board or making shallow cuts to minimize the risk of tear-out. If tear-out does occur, applying wood fillers or sanding down the affected area can help restore a smooth surface.
By being aware of these common issues and having strategies to address them, you can avoid frustration and successfully navigate through any challenges that may arise during your woodworking clock project. Remember, patience and attention to detail are key in producing a beautiful and functional timepiece.
Finishing and Maintenance
Importance of Proper Finishing Techniques
After the construction and assembly of a woodworking clock, one crucial step remains to truly showcase its beauty and ensure its longevity: proper finishing techniques. The finish applied to a clock not only enhances its appearance but also protects the wood from damage caused by moisture, sunlight, and regular wear and tear.
There are several options for finishing a woodworking clock, including varnishes, oils, waxes, and lacquers. Each type of finish has its own unique characteristics and application methods. Varnishes, for example, provide a durable protective layer that can withstand daily use. Oils deeply penetrate the wood fibers to enhance its natural beauty while providing some level of protection. Waxes offer a softer sheen and can be buffed to achieve a rich, lustrous finish.
Before applying any finish, it is important to properly prepare the surface by sanding it smooth and removing any dust or debris. Applying multiple thin coats of finish is usually recommended rather than one heavy coat as it allows for better absorption into the wood and minimizes the risk of drips or uneven coverage. It is also essential to follow the manufacturer’s instructions regarding drying times between coats.
Maintenance Tips for Woodworking Clocks
To keep your woodworking clock in pristine condition, regular maintenance is key. Here are some tips to help you maintain its beauty and functionality:
- Dusting: Regularly dust your clock with a soft, lint-free cloth or feather duster to remove any accumulated dust or dirt.
- Avoid Direct Sunlight: Exposure to direct sunlight can cause the wood to fade over time. Keep your clock away from windows or use curtains or blinds to protect it from harsh UV rays.
- Temperature and Humidity Control: Extreme temperature fluctuations and high humidity levels can lead to warping or cracking of the wood. Place your clock in a controlled environment to minimize these risks.
- Handle with Care: When moving or handling your clock, always take care to lift it properly and avoid excessive force or pressure.
- Regular Cleaning: Occasionally clean your clock with a mild wood cleaner or a mixture of water and gentle soap. Avoid using harsh chemicals or abrasive cleaners that can damage the finish.
By following these maintenance tips, you can ensure that your woodworking clock retains its beauty and functionality for years to come. Regular care and attention will help preserve the unique craftsmanship and make it a cherished piece in your home or office.
Showcase of Inspirational Woodworking Clocks
In conclusion, the showcase of inspirational woodworking clocks serves as both a testament to the artistry and skill of talented artisans and a source of inspiration for beginners and enthusiasts alike. Throughout history, wooden clocks have provided a canvas for creativity and innovation, with each clock reflecting the unique style and vision of its maker.
The gallery presented in this article showcases a diverse range of stunning and innovative designs that demonstrate the endless possibilities within the realm of woodworking clocks.
By exploring this gallery, readers can gain insights into various techniques, styles, and materials used in woodworking clockmaking. The featured clocks highlight the craftsmanship involved in creating intricate details, such as ornate carvings or complex mechanisms. They also showcase different wood types and finishes utilized to achieve specific aesthetic effects or to enhance durability.
Beyond serving as visual inspiration, these showcased clocks can also provide practical ideas for readers’ own projects. Whether it’s borrowing a particular design element or adapting a unique construction technique, the gallery serves as a springboard for creativity and encourages readers to push their boundaries.
Ultimately, the goal is not only to create functional timepieces but also to express one’s personal style through woodworking. With determination, patience, and attention to detail, anyone can embark on their own journey in crafting a woodworking clock that will become both an heirloom piece and a source of personal pride. So why not take inspiration from these showcased works and let your imagination run wild as you embark on your own woodworking clock project?
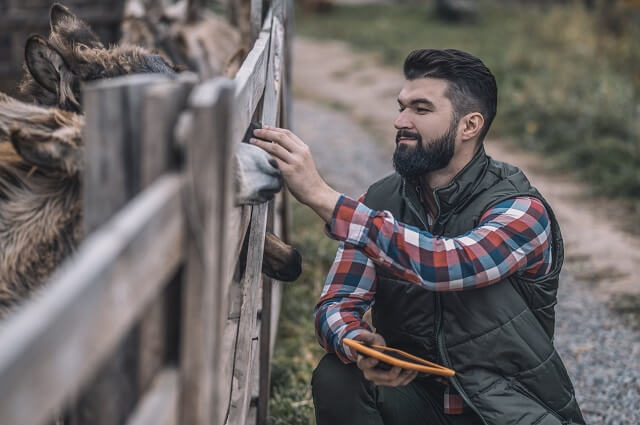
Hi everyone! I’m a woodworker and blogger, and this is my woodworking blog. In my blog, I share tips and tricks for woodworkers of all skill levels, as well as project ideas that you can try yourself.