Introduction to Woodworking CNC Software
Woodworking CNC software is computer-aided design (CAD) and computer-aided manufacturing (CAM) software that helps mill, router, lathe and other machines cut out parts from wood, metals and other materials. The software generally starts with design patterns which can be created manually or with specialized tools to manipulate images and 3D models. These designs are then converted into instructions for CNC machines which tell the machine where to move, what machining tool to use, how much material to take away and more.
The first woodworking CNC machines used mainly 2D drilling technologies while modern day machines have evolved to commonly use advanced 3D routing technology. Wood cutting CNC routers have capabilities such as pocketing, inlaying and sculpting complex shapes which is intended to maximize surface detail of finished product as well as reduce scrap material costs. They can also produce elaborate designs at speeds faster than manual operations while also improving accuracy.
Software advancements have been crucial in securing the widespread adoption of CNC machine tools by increasing their capabilities end efficiency. To further improve productivity and output quality, CAD/CAM systems are integrated into the popular operating systems on the market today such as Windows or Linux allowing the user to sketch out a desired shape quickly on their 3D screen and making it ready for programming. This allows for faster processing times with minimal setup fees for each part made resulting in quicker response times to new orders from customers as well as shorter production lead times for a job’s completion.
Common Woodworking Projects That Use CNC Software
1. Cabinet Doors: Cabinet doors can be made using woodworking CNC software, which is far easier and more accurate than handcutting them with jigs and traditional tools. A template drawing can be programmed into the CNC software and the required pieces cut quickly, accurately, and to precisely follow the desired design.
2. Carving Designs: Intricate carving designs often require a high level of accuracy, making CNC software an invaluable tool for their production. Patterns or shapes can be programmed into the software to create carved scrollwork, appliqué designs, or detailed trim work on crown molding.
3. Shelves: CNC routing can also be used to easily produce custom-made shelving components such as direct mounting shelves for use in closets or kitchen cupboards. Shelf brackets can also be cut with precise angles and cutouts for objects like toys or vases that fit onto standard shelves yet have their own unique slots or mounts for securing into place quickly and easily.
4. Furniture: Coffee tables, chairs and other furniture elements are easy to make with the help of woodworking CNC software since the computer controls it all from start to finish instead of having to create each piece manually by hand using power tools such as jigsaws or routers.
5. Signs: Wooden signs are often ornate after they are designed on paper as well as when they are finally cut out of wood on a specific table saw setup; however, this process is extremely time-consuming without professional assistance from machines such as these equipped with woodworking cnc software programs any shape imaginable that could potentially adorn a sign project can be produced in minutes rather than hours!
Choosing the Right CNC Software for Your Needs
CNC (Computer Numerical Control) software is now essential to any woodworking shop. In order to maximize efficiency and accuracy, it’s important to choose the right CNC software for your needs. The different types of CNC software provide functionality and features that are unique to specific applications.
STEPPER MOTION SOFTWARE: This type of software is generally used in 3-axis stepper motor systems and can be programmed with G-codes or proprietary languages written for each machine model. It allows for complex movements with simple commands and special features like look-ahead control, which reduces latency by predicting and reacting to the next command sent by the controller before it has been completed, allowing for higher speed machining with smoother operation.
SERVO MOTION SOFTWARE: This type of software is usually used in larger machines that use expensive servo motors for motion control, providing greater precision than its counterpart. It also allows user variables and macros to simplify complicated operations like tool length compensation as well as output various electrical signals from the controller unit.
OTHER SOFTWARE OPTIONS: Depending on the complexity of your project you may also want to consider CAD/CAM software that helps you create virtual models of the object you’re creating before plotting them out on real materials; computer-aided design (CAD); electronic document management systems that allow you store all your production designs in one central location; post processors, which help translate instructions produced by a CAD system into instructions compatible with a particular CNC machine; simulation softward which lets you test out your designs on a two dimensional scale at no cost before committing to physical production runs; offline programming options that enable CNC operators program components without directly accessing their computers; editing functions that manipulate existing CNC programs quickly and accurately; debugging capabilities that detect errors in processes before they happen; and last but not least networking features between multiple machinery so you can monitor activity remotely from another location or device.
Common Challenges Encountered When Using Woodworking CNC Software
1. Inaccurate results ” Improperly setting up the tool path, improper parameters, and faulty machines can lead to inaccurate results. To prevent this from happening, make sure to properly calculate speeds and feeds for the machine, the tooling and material combination.
2. Machines going out of sync with the program ” It’s important to check the program following any changes to ensure that all axes are in sync and that there is no backlash or overtravel. Make sure all safety devices and homing routines are in place as well.
3. Failure to account for overall dimensions ” Not accounting for stock or part dimensions when programming can cause woodworking CNC machines to produce off-sized parts leading to errors later down the line. This mistake can be avoided by using CAD software such as Fusion 360 when creating a tool path, as it automatically compensates for material thickness along with other factors.
4. Poor programming of pockets/holes ” Making sure all pockets/holes are programmed on individually rather than grouping them together will result in much cleaner and more accurate outcomes. Additionally, double checking lead-in/out positions before producing a part can save time from having to fix issues further down the line caused by areas cutting slightly off center from requested positions.
Tips and Tricks to Achieve Optimal Results with CNC Software
1. Make sure to familiarize yourself with your CNC software and its hardware capabilities before beginning a project. This is especially important for experienced woodworkers so they know which features will best help their individual projects.
2. Utilize preset programs that have been proven to be successful and efficient. Networking with local professionals who use the same type of software can help you identify these programs and save time on programming yourself.
3. Keep organized while designing, cutting and milling parts on your machine as opposed to attempting to create all the parts at once, as this will lead to errors due to clashing objects in one layer of material or another.
4. Set up parameters such as speed, cut depth and dwell to ensure your design meets the lumber’s specifications and that you get the results you want from your project; it may take testing a few times before perfecting these settings if cutting different types of lumber with different specs.
5. It’s helpful to double-check CAD drawings against the real world by taking measurements and adjusting accordingly; this ensures each component fits perfectly in place every time and also negates any errors resulting from inaccuracies during measurement phase of design process for example during inputting many dimensions quite close together when accurately capturing an object’s shape or size .
6. Always test a portion of your program before committing it completely – running only a portion of code on the machine can prevent costly overruns or mistakes that would otherwise arise if the entire program ran without first verifying correct operation of just a portion of it.
7. Take regular breaks throughout each project as eyes become tired after extended periods of looking at computer screens ” this also helps refocus mind while steps are playing out in CNC process allowing users work smarter not harder !
Conclusion
Overall, CNC software is an invaluable tool for woodworking projects. It can help increase productivity while reducing wasted materials and time spent on manual processes. Additionally, CNC software streamlines the entire woodworking process, giving the user easy accessibility to all their design specifications and allowing them to make adjustments as needed. Additionally, it helps in providing accurate cutting and measuring of parts using precise algorithms. Furthermore, CNC Software can also help users create unique designs that can be altered quickly with a single click of a mouse without having to start from scratch or remake any parts after making changes. Finally, it helps save costs because of its higher accuracy compared to conventional milling or sawing methods. In conclusion, CNCsoftware is highly beneficial for professionals in the field of woodworking and should be taken into serious consideration when it comes time to purchase new equipment for projects.
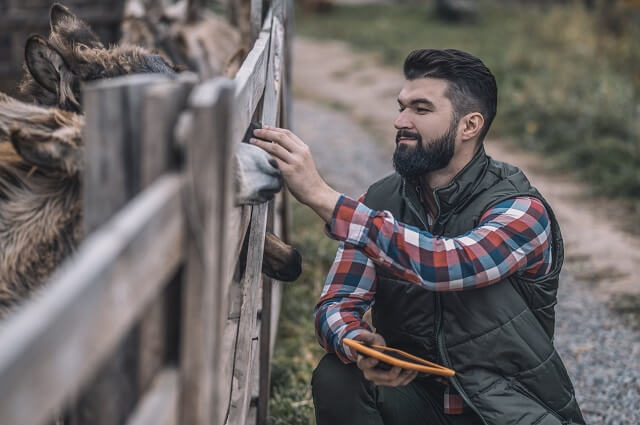
Hi everyone! I’m a woodworker and blogger, and this is my woodworking blog. In my blog, I share tips and tricks for woodworkers of all skill levels, as well as project ideas that you can try yourself.