Introduction to Woodworking Epoxy Inlay
Woodworking epoxy inlay is an art form that has been practiced for centuries, with records dating as far back as 4000 BC in ancient Egypt. The craft typically involves skillfully cutting or carving shapes into wood, then filling or inlaying the shape with a colored epoxy resin or veneer to create a beautiful piece of artwork. Artists use this technique to create decorative patterns, intricate designs and detailed color schemes within their work. It can also be used to repair cracked, damaged pieces of wood while still keeping the structure and integrity of the original piece intact. Although woodworking epoxy inlays have been consistently practiced throughout history, it wasn’t until the late 1800s when tools and machinery were introduced that advanced techniques could be developed and perfected. Today, this technique is used by professional furniture makers, sculptors, carpenters and even hobbyists for small projects. Woodworking epoxy inlay is an exciting way to create unique pieces and introduce color into otherwise plain surfaces.
Overview of the Techniques Used to Create Woodworking Epoxy Inlays
Woodworking epoxy inlays use two parts of an epoxy resin system to create decorative shapes and designs within a surface. The two components, a base and a hardener, must be combined precisely at the correct ratio in order to achieve the desired result. Types of epoxy available to create these effects include low viscosity, medium viscosity and high viscosity resins with various curing speeds for different applications.
Jointing techniques used in woodworking epoxy inlays may consist of hand carving or routing of the wood with specified router bits before the design is sealed with liquid or paste epoxies. Additionally, CNC machinery can be utilized to accurately cut intricate patterns into the wood prior to adding epoxy filler or tinted colorants to enhance the design overall.
The method used most commonly when working with clear epoxies is to apply multiple pours until the desired height has been reached, allowing each successive layer to properly cure before application of the next layer. With pre-mixed tints and colors placed within one pouring session, it is important that all materials have been completely soluble before mixing them together for application. Pressure pot vacuum systems are utilized when doing large areas or complex filling requirements. This ensures that all air bubbles contained within are forced out by vibration on a specified frequency setting ensuring even cures and complete coverage throughout entire areas without any pinholing or loss of clarity or strength characteristics within the finished product.
Safety Tips for Working with Woodworking Epoxy Inlays
When working with woodworking epoxy inlay, it is important to practice safety precautions to ensure proper use of the product and avoid any potential hazards. Here are some suggested safety tips that should be followed when handling and storing epoxy inlays:
1. Always wear protective eyewear and gloves when working with epoxy, as the chemicals can be hazardous if they come into contact with your skin or eyes.
2. Store epoxy in a cool, dry location away from direct sunlight or extreme temperatures. This will help extend its shelf life.
3. Be sure to keep all unused epoxy containers tightly sealed at all times, go prevent any moisture from entering them and partially curing the resin.
4. When mixing different components of an epoxy mixture, be sure to follow the instructions carefully to ensure proper chemical balance and ratio for complete adhesion when setting up an inlay layer.
5. Immediately clean up any spills or excess material using an appropriate solvent before letting it harden on the workspace surface or surrounding areas like carpets, countertops etc., where it might become difficult to remove later on.
6. Dispose of used containers responsibly once you are finished working with them, preferably through designated recycling centers or appropriately marked trash cans to protect the environment and your local community’s health from exposure to harmful chemicals contained within leftover resin residue present inside these containers.
Examples of Different Woodworking Epoxy Inlay Projects
Creating a woodworking epoxy inlay is a beautiful and intricate process that can be used to create unique designs and patterns. The process begins with the use of a template, which can either be made by hand or pre-made, to cut the wooden material into the desired shape. Once the template has been cut, the epoxy resin is mixed together with natural materials such as crushed shells, sand, glitter, or stones to fill the area that has been created. After allowing time for this layer to dry and set it’s time to add in color – if desired – using a liquid pigment within an additional layer of curing agent.
Finally, after all these components have had their chance to cure and set you are presented with what looks like gems or glass embedded inside your wooden design! Diagram 1 below shows the basic steps involved in creating an epoxy inlay.
Diagram 1: Steps Involved In Creating a Woodworking Epoxy Inlay
1. Mark Layout: Mark layout of your design on wood surface
2. Cut Template: Cut template for desired shape according to marked layout
3. Fill With Natural Materials: Fill cutout with chosen natural materials such as crushed shells, sand etc
4. Add Pigment (optional): Mix liquid pigment with additional layer of curing agent and pour over natural materials
5 .Allow Time To Cure: Allow enough time for entire layers to properly cure/set
6 .Reveal Design: Remove cured material from wood surface to reveal exquisite jewelry-like design
Tips for Finishing Woodworking Epoxy Inlays
Polishing and buffing your epoxy inlay to a smooth finish is a great way to make it stand out. The most important thing to remember when attempting this is to start with a coarse sandpaper, such as 100 grit, to remove any bumps or imperfections in the surface of the epoxy. Then work your way up through 120 and 180 grit paper, followed by 220 and 320. Once you achieve an even surface, begin polishing with 400-800 dustran paper. Lastly, take care not to skip the buffing stage; apply automotive wax or metal polish generously with a clean cloth and let it sit for 2 minutes before buffing off. This will help seal and protect your epoxy inlay from future deterioration or wear.
Benefits of Using Woodworking Epoxy Inlays
Woodworking epoxy inlays are a great way to strengthen weak wood joints and overall reinforce a project. Epoxy creates an extremely strong bond and gives professional results with minimal effort compared to traditional joint glues or nails. When epoxy is applied between two pieces of wood, it significantly increases the strength of the connection points. This helps ensure that structural elements remain secure when projects such as furniture hold more weight than expected. In addition, epoxy can be mixed with various colors, additives or textures to enhance the aesthetic look of your piece. In general, epoxy strongly binds surfaces together to increase structural compatibility and make it easier to create efficient designs that stand the test of time.
Common Problems with Woodworking Epoxy Inlays
If the epoxy is applied unevenly, you should immediately smooth it out with a cloth. Alternatively, apply a thin layer of hot glue over the uneven area and allow it to cool before trying to even it out using sandpaper.
If areas become too hot when working with the epoxy, use a cold washcloth along the edges to keep them cool. Additionally, you can place a damp towel around the area and let it evaporate slowly to cool down the epoxy. Finally, moving quickly with the application of heat is always important for keeping temperatures in check.
Conclusions
There are a few types of epoxy suitable for woodworking and inlay projects, each with its own strengths. Polyester based epoxies (sometimes called Phenolic resins) are the most economical, but require more preparation and tend to bubble. They also can be harder to sand down due to their hardness and their yellowing over time. On the other hand, two-part amine adducts produce crystal clear epoxies with less difficulty in application and sanding, but they can also be more costly. Vinyl esters are also an option to consider as they offer even more clarity than amines and have excellent vibration resistance, however they may still require more time-consuming surface preparation pre-application.
Overall one must assess the types of epoxy to determine which will give them the most advantageous results depending on their project needs. For example, for intricate wooden inlay applications that do not need extreme clarity or end use strength, Polyester resins may be preferred due to cost savings from higher labor efficiency considerations; if a jewelry box is being built where extreme clarity matters vinyl ester may be preferred. Ultimately the type of epoxy used should match the end user’s needs while factoring in their budget constraints as well as labor demands after all factors have been considered.
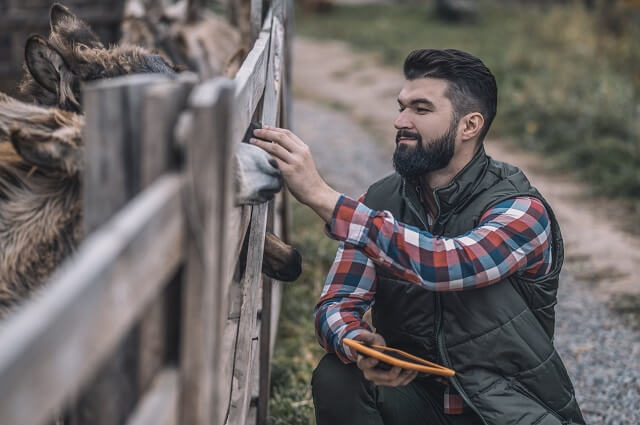
Hi everyone! I’m a woodworker and blogger, and this is my woodworking blog. In my blog, I share tips and tricks for woodworkers of all skill levels, as well as project ideas that you can try yourself.