Woodworking ERP systems have revolutionized the way woodworking businesses operate, streamlining processes, maximizing efficiency, and improving overall business performance. In today’s competitive market, investing in a reliable woodworking ERP system has become essential for companies looking to stay ahead of the curve. This article delves into the world of woodworking ERP, exploring its importance in the industry, common challenges faced by businesses, key features to consider when selecting a system, and real-life case studies of successful implementations.
In the fast-paced world of woodworking, having a robust ERP system can make all the difference. From automating tasks to optimizing production schedules and managing inventory effectively, woodworking ERP solutions are designed to address the unique needs of this specialized industry. For woodworking businesses looking to enhance their operations and gain a competitive edge, finding the right ERP provider is key.
As we delve deeper into this topic, we will explore the significance of ERP in the woodworking industry, shedding light on the benefits it offers and how it can transform business practices. By examining real-world examples of companies that have successfully implemented ERP systems and sharing insights on choosing the right provider, readers will gain valuable knowledge on navigating their own woodworking ERP journey.
Importance of ERP in the Woodworking Industry
Streamlining Operations
In the woodworking industry, efficiency is key to success. Implementing a Woodworking ERP system can help businesses streamline and automate their operations, from inventory management to production scheduling. By centralizing all data and processes in one integrated platform, woodworking companies can eliminate manual tasks, reduce errors, and improve overall productivity. With real-time insights into every aspect of the business, decision-makers can make informed choices that drive growth and profitability.
Enhancing Communication and Collaboration
Effective communication and collaboration are essential for any woodworking business to thrive. A Woodworking ERP system enables employees across various departments to access the same up-to-date information, fostering better coordination and teamwork. From sales teams having visibility into production schedules to warehouse staff knowing inventory levels in real-time, ERP software breaks down silos and promotes a more cohesive work environment. This enhanced communication ultimately results in faster decision-making processes and improved customer satisfaction.
Improving Data Accuracy and Reporting
Inaccurate data can lead to costly mistakes in the woodworking industry. With a Woodworking ERP system in place, businesses can ensure data integrity by eliminating manual entry errors and ensuring consistency across all processes.
This reliable data serves as a foundation for generating accurate reports that provide valuable insights for strategic planning and forecasting. Whether analyzing material costs or tracking project timelines, ERP software empowers woodworking companies with the information needed to make sound business decisions based on facts rather than guesswork.
Common Challenges Faced by Woodworking Businesses
Woodworking businesses face a myriad of challenges in their day-to-day operations, which can impact their overall efficiency and profitability. One common challenge is the lack of integration and organization in managing different aspects of the business, such as inventory, production, sales, and finances.
Without a streamlined system in place, businesses may struggle with tracking orders, managing resources effectively, and meeting customer demand on time. This can lead to delays in production, errors in order fulfillment, and ultimately dissatisfied customers.
Another significant challenge for woodworking businesses is the manual processes involved in various operations. From tracking inventory levels to generating reports for decision-making, relying on manual input can be time-consuming and prone to errors. This inefficiency not only affects productivity but also hinders the ability to make informed business decisions based on accurate data. Without real-time visibility into key metrics and performance indicators, woodworking businesses may find it challenging to stay competitive in the industry.
Moreover, compliance with regulations and standards specific to the woodworking industry poses a major challenge for businesses. From ensuring product quality and safety to adhering to environmental regulations, woodworking companies need to navigate a complex landscape of requirements. Failing to meet these standards can result in costly penalties, damaged reputation, or even legal consequences. Implementing a robust woodworking ERP system can help address these challenges by providing automated processes, real-time insights, and tools for compliance management.
Challenge | Impact |
---|---|
Lack of integration and organization | Delays in production, errors in order fulfillment, dissatisfied customers |
Manual processes | Time-consuming tasks, errors in data input, hindrance to informed decision-making |
Compliance with regulations | Penalties for non-compliance, damaged reputation, legal consequences |
Features to Look for in a Woodworking ERP System
Woodworking ERP systems are specifically designed to cater to the unique needs of businesses in the woodworking industry. When looking for the right ERP system for your woodworking business, there are several key features that you should consider to ensure that it meets your requirements.
One important feature to look for is customizable workflows and processes. Woodworking companies often have specific workflows that are unique to their operations, so having the ability to customize these within the ERP system is crucial for smooth integration.
Another essential feature to consider in a woodworking ERP system is inventory management capabilities. Proper inventory management is vital in the woodworking industry to ensure that materials are always available when needed and to minimize waste. An ERP system with robust inventory tracking functionalities can help optimize material procurement, reduce stockouts, and improve overall efficiency in production processes.
Additionally, a woodworking ERP system should have strong project management tools. Woodworking projects can be complex and multi-faceted, requiring careful planning and coordination of resources. Having project management features within the ERP system can help streamline project execution, track progress, allocate resources effectively, and ensure timely delivery of projects.
Overall, when selecting a woodworking ERP system for your business, it is important to focus on features such as customizable workflows, robust inventory management capabilities, and comprehensive project management tools to enhance operational efficiency and productivity.
Features | Description |
---|---|
Customizable Workflows | Allows customization of workflows to fit unique operations. |
Inventory Management | Helps optimize material procurement and reduce stockouts. |
Project Management Tools | Aids in streamlining project execution and resource allocation. |
Case Studies of Woodworking Companies Implementing ERP
Woodworking companies around the world are increasingly recognizing the benefits of implementing an ERP system in their operations. These systems are designed to streamline processes, improve efficiency, and provide valuable data insights for decision-making. Below are a few case studies of woodworking companies that have successfully implemented ERP solutions:
- Company A: Company A, a furniture manufacturer based in the United States, was facing challenges with inventory management and production scheduling. By implementing a woodworking ERP system, they were able to track inventory levels in real-time, automate reorder processes, and optimize production schedules. As a result, Company A saw a significant improvement in their operational efficiency and product quality.
- Company B: Company B, a cabinet maker located in Canada, struggled with accurate cost tracking and project management. After adopting a woodworking ERP solution, they were able to monitor project costs more effectively, allocate resources efficiently, and deliver projects on time and within budget. The visibility provided by the ERP system allowed Company B to make data-driven decisions that ultimately led to increased profitability.
- Company C: Company C, a woodworking shop in Europe specializing in custom woodworking projects, found it challenging to manage complex orders and track customer preferences. With the help of an ERP system tailored for woodworking businesses, they were able to centralize customer information, develop customized products more efficiently, and enhance customer satisfaction through timely deliveries. The implementation of ERP transformed Company C’s business processes and positioned them for growth in the competitive woodworking market.
These case studies highlight how woodworking ERP systems can address specific challenges faced by businesses in the industry and drive positive outcomes. By leveraging the right technology solutions tailored for their unique needs, woodworking companies can achieve sustainable growth and success in today’s competitive market landscape.
Benefits of Implementing an ERP System in Woodworking
Implementing an ERP system in a woodworking business can bring about numerous benefits that can streamline operations, improve efficiency, and ultimately lead to increased profitability. Here are some key advantages of incorporating an ERP system in the woodworking industry:
- Enhanced Inventory Management: An ERP system can help woodworking businesses accurately track inventory levels, reduce waste, and optimize stocking levels. This can result in cost savings and improved productivity.
- Improved Production Planning: With real-time data insights provided by an ERP system, woodworking companies can better plan production schedules, allocate resources effectively, and ensure on-time delivery of projects.
- Streamlined Communication: By centralizing all information in one platform, an ERP system enables seamless communication among different departments within a woodworking business. This leads to better collaboration and coordination across the organization.
Furthermore, the implementation of a woodworking ERP solution can also help in standardizing processes, reducing errors, and providing visibility into key metrics for informed decision-making. By leveraging technology to automate tasks and streamline workflows, woodworking businesses can stay competitive in a fast-paced industry landscape while meeting customer demands efficiently.
Implementation Process of ERP in Woodworking Businesses
Planning and Preparation
Before implementing an ERP system in a woodworking business, it is essential to have a well-thought-out plan in place. This includes defining the specific goals and objectives of the ERP implementation, selecting a suitable ERP provider that caters to the unique needs of the woodworking industry, and ensuring that key stakeholders are on board with the implementation process.
It is also crucial to conduct a thorough analysis of the current business processes and identify areas that can be improved with the use of an ERP system.
Data Migration and System Integration
One of the key challenges in implementing an ERP system in woodworking businesses is migrating data from existing systems to the new ERP platform. This process requires careful planning and execution to ensure that all data is transferred accurately and securely. Additionally, integrating the ERP system with other software applications used within the business, such as CAD/CAM software for design purposes, is essential for seamless operation.
Training and Change Management
Implementing an ERP system involves significant changes in workflow processes and employee roles within a woodworking business. Therefore, providing comprehensive training programs for employees on how to use the new system effectively is crucial for successful implementation. Additionally, effective change management strategies should be put in place to help employees adapt to the new technology and embrace its benefits. Communication with employees throughout the implementation process is key to managing any resistance or concerns that may arise.
Tips for Choosing the Right Woodworking ERP Provider
When selecting a woodworking ERP provider for your business, it is crucial to consider several factors to ensure that you choose the right fit for your specific needs. One of the essential things to look for in a woodworking ERP provider is industry experience. It is important to select a provider that understands the unique requirements and challenges of the woodworking industry, as this can greatly impact the successful implementation and functionality of the ERP system.
Another key factor to consider when choosing a woodworking ERP provider is the scalability and flexibility of their system. As your business grows and evolves, your ERP system needs to be able to adapt and grow with you.
Look for a provider that offers customizable solutions that can be tailored to suit your business needs both now and in the future. Additionally, ensure that the ERP system is user-friendly and offers comprehensive training and support to help your team effectively utilize the system.
Furthermore, it is essential to assess the integration capabilities of a woodworking ERP provider. A good ERP system should be able to seamlessly integrate with other software applications that you use in your business, such as accounting software or inventory management systems.
This integration ensures efficient data flow across all facets of your business operations, leading to improved productivity and decision-making processes. By carefully evaluating these factors when choosing a woodworking ERP provider, you can set your business up for success in streamlining operations, increasing efficiency, and ultimately boosting profitability.
Conclusion
In conclusion, the future of ERP in the woodworking industry looks promising as more and more businesses are realizing the benefits of implementing such systems. The efficiency, organization, and streamlined processes that ERP brings to woodworking companies can significantly improve their overall operations and profitability. As technology continues to advance, the integration of ERP software tailored specifically for the woodworking sector will only become more sophisticated and user-friendly.
One of the key takeaways from this discussion is the importance of selecting a woodworking ERP provider that understands the unique needs and challenges of this industry. Businesses should look for features such as inventory management, production scheduling, cost tracking, and customizable reporting tools. By choosing a comprehensive ERP system that caters to these specific requirements, woodworking companies can optimize their workflows and achieve greater success in a competitive market.
Overall, the implementation of an ERP system in woodworking businesses has proven to be a game-changer in terms of improving productivity, reducing costs, and enhancing overall performance. As more companies share their success stories through case studies showcasing the positive impact of ERP integration, it is evident that this technology is here to stay in the woodworking industry.
Embracing these advancements and staying updated on the latest trends in woodworking ERP will undoubtedly be crucial for businesses looking to thrive in today’s fast-paced market environment.
Frequently Asked Questions
What Does ERP Stand for in Sage?
In Sage, ERP stands for Enterprise Resource Planning. This software helps businesses manage important aspects like financials, human resources, and supply chain management in an integrated system.
Does IKEA Use ERP?
Yes, IKEA does use ERP systems. By implementing ERP software, IKEA can streamline its operations by integrating various functions such as manufacturing, distribution, and sales into one cohesive system.
What Does the ERP Tool Stand For?
ERP stands for Enterprise Resource Planning tool. This tool is designed to help organizations streamline their business processes by integrating various functions like finance, HR, inventory management, and customer service into a unified system.
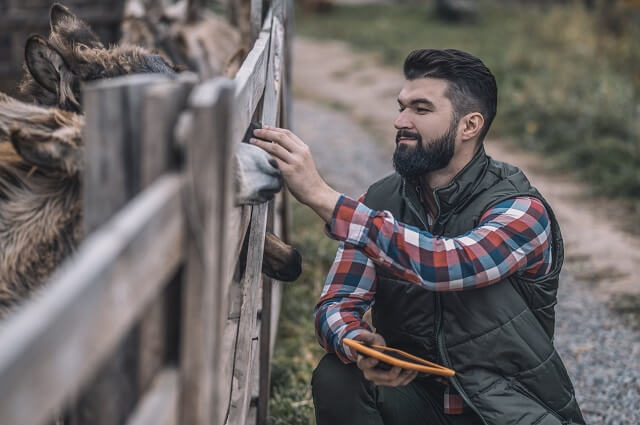
Hi everyone! I’m a woodworker and blogger, and this is my woodworking blog. In my blog, I share tips and tricks for woodworkers of all skill levels, as well as project ideas that you can try yourself.